Standaryzacja pracy w TPM często kojarzona jest z tematem autonomicznej konwersacji (AM, ang. Autonomous Maintenance) – jednym z głównych filarów koncepcji TPM (ang. Total Productive Maintenance). TPM zorientowany jest na eliminację 6 wielkich strat w wykorzystaniu maszyn i urządzeń. Do tych 6 strat należą:
- Przestoje z powodu awarii – nagłe awarie maszyn lub urządzeń, które powodują całkowite zatrzymanie produkcji.
- Ustawienia, regulacje i przezbrojenia – czas stracony na zmianę konfiguracji maszyny lub linii produkcyjnej, na przykład przy zmianie wykonywanego zadania lub wymianie narzędzi.
- Mikroprzestoje – krótkotrwałe zatrzymania produkcji, które nie są związane z awariami, ale z problemami takimi jak zacięcia materiału, błędy sensorów, itp.
- Praca maszyny z obniżoną prędkością – praca maszyny z prędkością niższą niż jej maksymalna zdolność produkcyjna, co może być spowodowane przez złe ustawienia, zużycie techniczne lub inne problemy operacyjne.
- Defekty produkcyjne – straty wynikające z produkcji wadliwych części, które wymagają poprawek lub przetworzenia, oraz odpadów, które nie mogą być już użyte.
- Straty związane z procesem rozruchu maszyny – straty produkcyjne występujące w czasie rozruchu maszyny, zanim osiągnie ona stabilną i optymalną wydajność.
Standaryzacja pracy w TPM AM powiązana jest z angażowaniem operatorów obsługujących pracę maszyn w identyfikację objawów złego funkcjonowania maszyn, zanim przerodzą się one w finalne problemy. TPM AM to nic innego jak standaryzacja procesów obsługowych maszyn. Standardowo operator maszyny szkolony jest z tego jak użytkować maszynę, tzn. produkować na niej produkty. Niech przykładem będzie praca na prasie. Operator szkolony jest z tego, w jaki sposób robić załadunek i rozładunek prasy, tak aby ją użytkować przy możliwie największej efektywności. Niemniej, wiele organizacji idzie o krok dalej i poza standaryzacją procesów użytkowych, skupiają się na standaryzacji procesów obsługowych. Do nich można zaliczyć takie operacje, jak: sprawdzenie poziomu oleju, dokręcenie luźnych śrub, czy kontrolowanie parametrów pracy maszyny. Często działania TPM AM nazywane są w przemyśle jako CILT (ang. Cleaning, Inspection, Lubrication, and Tightening), czyli Czyszczenie, Inspekcja, Smarowanie i Dokręcanie.
Operator techniczny a Operator maszyny
Najlepsze firmy produkcyjne nie boją się inwestować w rozwój swoich operatorów maszyn często nazywając ich operatorami technicznymi. Jest to pojęcie, które z początku może niczym nie różnić się od pojęcia operatora maszyny, ale przyglądając się bliżej zakresowi obowiązków, można zobaczyć, że ten dla operatora technicznego jest bardziej rozbudowany. Operator techniczny w ramach swoich obowiązków ma przypisane zadania, które wchodzą w skład CILT. Operator techniczny nie tylko użytkuje maszynę, ale również ją obsługuje. Poniżej przedstawiliśmy w jaki sposób realizowanie zadań CILT wpływa na identyfikację problemów z pracą maszyny:
- Czyszczenie (C) – regularne i systematyczne czyszczenie maszyn jest kluczowe, aby utrzymać ich sprawność i wydajność. Czyszczenie nie tylko zapobiega gromadzeniu się zanieczyszczeń, które mogą wpływać na działanie maszyny, ale także pozwala pracownikom zauważyć wszelkie potencjalne problemy, takie jak przecieki, pęknięcia lub inne uszkodzenia, które mogą być mniej widoczne, gdy maszyna jest brudna.
- Inspekcja (I)- regularne inspekcje pozwalają na wczesne identyfikowanie problemów i nieregularności w działaniu maszyn. Pracownicy są szkoleni, aby zwracać uwagę na wszelkie anomalie w działaniu sprzętu, co umożliwia szybką reakcję zanim problemy przerodzą się w poważne awarie.
- Smarowanie (L) – właściwe smarowanie jest niezbędne dla zapewnienia płynnej pracy ruchomych części maszyny. Nieodpowiednie lub niewystarczające smarowanie może prowadzić do przyspieszonego zużycia i awarii.
- Dokręcanie (T) – systematyczne sprawdzanie i dokręcanie luźnych elementów zapewniają, że wszystkie komponenty maszyny są odpowiednio zabezpieczone i działają zgodnie z wymaganiami. To zapobiega wibracjom, które mogą prowadzić do uszkodzeń i awarii.
Standaryzacja pracy w TPM lekarstwem na eliminację 6 wielkich strat
Rozwijanie operatorów maszyn w kierunku operatorów technicznych daje olbrzymi potencjał do poprawy efektywności wykorzystania maszyn (wskaźnik OEE). Firmy, które mniej świadomie podchodzą do TPM, zazwyczaj łączą wskaźnik OEE z problemami technicznymi maszyn. Spoglądając na składowe wskaźnika OEE, widzimy, że zbudowany on jest z 3 elementów: dostępność, wykorzystanie i jakość. OEE liczony jest jako iloczyn tych 3 elementów. Dostępność ściśle powiązana jest ilością przestojów maszyny i jej przezbrojeniami. Dostępność maszyny spada, kiedy maszyna nie produkuje. Wykorzystanie maszyn natomiast wiąże się z ilością mikroprzestojów oraz tym, czy maszyna pracuje na maksymalnej swojej prędkości. Jakość pracy maszyny odnosi się do ilości produkowanej przez nią braków oraz strat podczas rozruchu.
Już na pierwszy rzut oka widać, ze wskaźnik OEE pozwala skategoryzować 6 wielkich strat w pracy maszyny. W Tabeli 1 przedstawiliśmy w jaki sposób te 6 wielkich strat może być minimalizowane przez działania TPM AM, które obejmują aktywności związane z CILT.
Tab. 1. Wpływ TPM AM na eliminację 6 wielkich strat w pracy maszyny
Wielka strata w pracy maszyny | Jak TPM AM pomaga wyeliminować tą stratę |
Przestoje z powodu awarii | Poprzez regularne czyszczenie, smarowanie i podstawową konserwację, operatorzy mogą wcześniej identyfikować i adresować potencjalne problemy zanim przeistoczą się w poważne awarie. Dzięki temu, maszyny działają bardziej niezawodnie, co zmniejsza ryzyko nieoczekiwanych przestojów. |
Ustawienia, regulacje i przezbrojenia | Operatorzy stają się bardziej zaznajomieni z maszynami, na których pracują, dzięki czemu mogą szybciej i skuteczniej przeprowadzać niezbędne ustawienia oraz regulacje. Znajomość specyfikacji i optymalnych ustawień maszyn pozwala na redukcję czasu potrzebnego na zmiany produkcyjne. |
Mikroprzestoje | Autonomiczna Konserwacja zwiększa umiejętność operatorów do szybkiego reagowania na drobne nieprawidłowości i zacięcia. Regularne inspekcje i konserwacja sprzętu mogą zapobiegać wielu przestojom, które mogłyby inaczej przerodzić się w poważniejsze problemy. |
Praca maszyny z obniżoną prędkością | Dzięki ciągłej uwadze na stan maszyny, operatorzy są w stanie utrzymać maszyny w optymalnym stanie technicznym, co pozwala na działanie z maksymalną przepustowością i efektywnością. Regularna konserwacja zapewnia, że maszyny pracują z przewidzianą prędkością, minimalizując straty związane z obniżoną wydajnością. |
Defekty w produkcji i scrap | Autonomiczna Konserwacja uczy operatorów, jak utrzymać maszyny w takim stanie, aby produkować wyroby najwyższej jakości. Poprzez minimalizację wad produkcyjnych i potrzeby przetwarzania, można znacznie obniżyć koszty i zwiększyć ogólną wydajność linii produkcyjnej. |
Straty związane z procesem uruchamiania | Znajomość maszyny i jej regularna konserwacja skraca czas potrzebny na osiągnięcie pełnej operacyjności po rozruchu. Operatorzy, którzy są dobrze zaznajomieni z każdą częścią swojej maszyny, mogą szybciej osiągnąć optymalny poziom produkcji po przestojach czy zmianach w konfiguracji. |
Inwestycja w rozwój operatorów, ich transformację z operatorów maszyn do operatorów technicznych, przyczynia się do redukcji 6 wielkich strat w pracy maszyny, a tym samym poprawy wskaźnika OEE. Zatem skoro to tak oczywiste, dlaczego tak nie wiele firm oddaje w ręce operatorów realizacje działań związanych z TPM AM?
Standaryzacja pracy w TPM AM – problemy
Jak wspomnieliśmy wyżej, TPM AM to nic innego jak standaryzacja procesów obsługowych maszyn. Wyzwania przy wdrażaniu TPM AM sprowadzają się do 3 głównych typów problemów:
- Problem procesowy związany ze źle ustalonymi metodami pracy w zakresie realizacji działań CILT. Należy tutaj zaliczyć takie problemy jak brak zarządzania wizualnego, trudny dostęp do maszyny, brak narzędzi do realizacji działań TPM AM, czy źle wyliczony czas na takie działania.
- Problem ludzki związany brakiem wiedzy przez operatora jak należy wykonywać działania obsługowe na maszynie. Ten problem stanowi wyzwanie organizacyjne dla firmy, ponieważ wdrożenia operatora maszyny do realizacji działań obsługowych wymaga czasu i szkoleń. Często ten czas nie jest odpowiednio zaplanowany, a w takiej sytuacji działania TPM AM w firmie pozostają działaniami wyłącznie na papierze.
- Problem ludzki związany z brakiem chęci realizowana działań TPM AM. Ten problem może wystąpić, kiedy mamy dobrze zdefiniowane metody i poprawnie przeszkolonych operatorów, ale mimo wszystko operatorzy nie chcą realizować takich działań. Np. uważają, że nie jest to ich zakres obowiązków.
W naszym odczuciu, te 3 problemy stanowią główne ograniczenia przed wdrożeniem standaryzacji działań obsługowych maszyn (TPM AM wraz z procesem CILT). Z drugiej strony wiemy, że istnieją gotowe rozwiązania, które te problemy mogą wyeliminować. Te rozwiązania są częścią programu TWI (ang. Training Within Industry).
Program TWI – rozwiązanie pomagające wdrożyć TPM AM
Program TWI to koncepcja, która została opracowana w Stanach Zjednoczonych podczas II wojny światowej w celu wspierania przemysłu wojennego przez szybkie szkolenie pracowników w efektywnych metodach pracy. Program składa się z serii metod szkoleniowych, które mają na celu poprawę efektywności, jakości oraz relacji pracowniczych poprzez lepsze zarządzanie, szkolenie i umiejętności instruktażowe liderów na różnych poziomach organizacyjnych. Program TWI nie jest wyłącznie skierowany do produkcji, ale również do działań powiązanych z utrzymaniem ruchu maszyn. Program TWI wspiera wdrażanie standaryzacji pracy.
Moduły programu TWI
Podstawowe moduły TWI to
- Instruowanie Pracowników (TWI JI, ang. Job Instructions), które uczy przełożonych, jak efektywnie szkolić pracowników w wykonywaniu zadań;
- Metody Pracy (TWI JM, ang. Job Methods), które skupiają się na poprawie metod pracy w celu zwiększenia produktywności;
- Relacje z Pracownikami (TWI JR, ang. Job Relations), które uczą liderów, jak budować dobre relacje z pracownikami, rozwiązywać konflikty i motywować zespoły.
Program TWI odniósł znaczący sukces w czasie wojny, a jego wpływ trwa do dziś, będąc wciąż stosowanym na szeroką skalę w przemyśle na całym świecie, przyczyniając się do podnoszenia standardów pracy i zwiększania efektywności operacyjnej.
Spoglądając na najważniejsze problemy, jakie występują przy wdrażaniu standaryzacji działań TPM AM, nietrudno wyciągnąć wniosek, że to właśnie program TWI – jako holistyczne podejście do rozwoju kompetencji przełożonych – ma olbrzymi wpływ na eliminację tych problemów. W tabeli 2 przedstawiliśmy jak problemy przy wdrażaniu standaryzacji działań TPM AM mogą być wyeliminowane przez metody z programu TWI.
Tab. 2. Eliminacja problemów związanych z wdrażaniem standaryzacji pracy w TPM AM w oparciu o metody programu TWI
Standaryzacja pracy w TPM AM – problemy wdrożeniowe | Metody z Programu TWI |
Problem procesowy związany ze źle ustalonymi metodami pracy w zakresie realizacji działań CILT. | TWI JM pomaga identyfikować i eliminować nieefektywne metody pracy poprzez nauczanie liderów, jak analizować zadania, rozkładać je na części składowe i usprawniać każdy krok. Dzięki temu, działania CILT mogą być optymalizowane, co prowadzi do zwiększenia wydajności i skuteczniejszego wykonywania konserwacji. |
Problem ludzki związany brakiem wiedzy przez operatora jak należy wykonywać działania obsługowe na maszynie. | TWI JI skupia się na przekazywaniu wiedzy i umiejętności w sposób strukturalny i spójny, co pozwala operatorom dokładnie zrozumieć, jak powinni wykonywać działania obsługowe na maszynie. Poprzez standardowy proces instruktażu, JI zapewnia, że wszyscy operatorzy są odpowiednio przeszkoleni, co minimalizuje ludzkie błędy wynikające z braku wiedzy. |
Problem ludzki związany z brakiem chęci realizowana działań TPM AM. | TWI JR koncentruje się na rozwijaniu umiejętności interpersonalnych liderów, aby mogli oni budować lepsze relacje z pracownikami. Stosując metody TWI JR, liderzy uczą się, jak odpowiednio motywować pracowników i budować zaangażowanie, co jest kluczowe w przypadku braku chęci do realizacji działań TPM AM. Dzięki TWI JR, można zidentyfikować i rozwiązać problemy związane z postawami i motywacją pracowników, zachęcając ich do aktywnego uczestnictwa w działaniach utrzymania autonomicznego. |
Program TWI wydaje się stanowić odpowiedź na wyzwania przy wdrażaniu standaryzacji pracy w TPM AM wraz z aktywnościami CILT. W ramach serii artykułów, przedstawimy dokładnie 3 metody z zakresu programu TWI w kontekście ich użycia, aby standaryzacja pracy w TPM AM mogła być wdrożona.
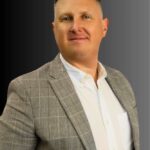
Jestem popularyzatorem Lean Management oraz programu Training Within Industry. Jestem praktykiem. Współtworzę wiele startupów. Od 2015 roku jestem CEO w Leantrix - czołowej firmie z zakresu konsultingu Lean w Polsce, która począwszy od 2024 roku organizuje jedną z największych konferencji poświęconych szczupłemu zarządzaniu w Polsce - Lean TWI Summit. Od 2019 roku jestem CEO w firmie Do Lean IT OU zarejestrowanej w Estonii, która tworzy software etwi.io używany przez kilkadziesiąt firm produkcyjnych i usługowych w Europie i USA.