Co to jest Kaizen? Kaizen (z jap. zmiana na lepsze) to filozofia zorientowana na ciągłe doskonalenie. W praktyce Kaizen niesie za sobą pewne fundamentalne zasady, takie jak: praca zespołowa, nastawienie na usuwanie źródła problemów, posługiwanie się faktami i danymi czy zaangażowanie każdego pracownika. Kaizen to sposób myślenia o doskonaleniu procesów, gdzie największy nacisk kładzie się na pobudzanie kreatywności wśród wszystkich pracowników w firmie. Kaizen powszechnie kojarzony jest z drobnymi pomysłami pracowników (Kaiezn procesu), jednak w Kaizen jest również furtka na duże pomysły doskonalące firmę (Kaizen przepływu). W modelu Kaizen dominują jednak drobne usprawnienia będące częścią właśnie Kaizen procesu. Jest to zupełnie inna koncepcja niż w podejściu do doskonalenia w modelu tradycyjnym, który opiera się na dużych projektach reorganizacyjnych. W takiej sytuacji czas pomiędzy powstaniem koncepcji a realizacją projektu jest bardzo długi (rys.1).
Rys.1. Doskonalenie pracy wg modelu Kaizen i modelu tradycyjnego
Źródło: Misiurek B., 2016, Standardized Work with TWI: Eliminating Human Errors in Production and Service Processes, Productivity Press, New York
W modelu tradycyjnym tworzy się grupy projektowe i poświęca się dużo czasu na analizę. Wymagane jest również, przy każdym projekcie, zaangażowanie szeregu działów, takich jak: służby BHP, dział finansowy, dział jakości itd. Realizacja wniosków reorganizacyjnych jest zdecydowanie lepsza, niż w ogóle brak podejmowania inicjatyw doskonalących. To pewne! Problemem jest to, że działań reorganizacyjnych ze względu na czas i koszty może być maksymalnie kilka w roku. Czasami zdarzają się sytuacje, gdzie zostaje przeprowadzona pełna analiza przedwdrożeniowa, a projekt reorganizacyjny upada ze względu na zmianę np. budżetu. Drobne usprawnienia, będące częścią modelu Kaizen, mają to do siebie, że są odporne na takie sytuacje. Głównie ze względu na krótki okres wdrożenia. Dzięki temu takich usprawnień mogą być tysiące! Zawsze kiedy zapytasz: Co to jest Kaizen? Pomyśl o efekcie skali przy powstawaniu małych pomysłów.
Kaizen a procesy autonomicznej konserwacji AM
Autonomiczna konserwacja (ang. Autonomous Maintenance, AM) to podstawowa metoda wchodząca w skład systemu TPM (ang. Total Productive Maintenance). Celem procesów AM jest angażowanie operatorów w działania obsługowe na maszynach. Jest to o tyle istotne, gdyż operatorzy są najbliżej maszyn i są w stanie bardzo szybko zareagować na ich potencjalne problemy. Całą umiejętnością jest zidentyfikowanie tych problemów (usterek) zanim przerodzą się one w awarie. AM służy temu, aby nauczyć operatorów świadomie przeglądać i czyścić maszyny. Powszechnie przyjmuje się, że wdrażanie procesu AM na wybranym stanowisku składa się z 7 kroków (Nakajima, 1988):
- Gruntowne czyszczenie i sprawdzanie maszyny.
- Oznaczanie i eliminacja źródeł zabrudzeń.
- Ułatwianie dostępu do czyszczenia i inspekcji maszyn.
- Określenie standardów czyszczenia i konserwowania.
- Poprawa ogólnych umiejętności inspekcyjnych u operatorów.
- Autonomiczna inspekcja maszyn.
- Proces ciągłego doskonalenia.
Pierwsze sześć kroków wdrażania AM związanych jest z szeroko rozumianą stabilizacją procesów (kroki: 1,2,3), dokumentowaniem pracy (krok: 4), szkoleniem operatorów (krok: 5) oraz utrzymywanie systemu (krok: 6). Ostatni krok przy wdrażaniu procesu AM to ciągłe doskonalenie (krok: 7), które ściśle związane jest z podejściem Kaizen. Dlaczego istotne jest doskonalenie działań wchodzących w skład procesu AM? Ponieważ w większości są one realizowane podczas postoju maszyny, a skrócenie czasu ich wykonywania będzie miało olbrzymi wpływ na poprawę dostępności maszyn. Innym powodem, dla którego doskonali się działania w zakresie AM, jest ułatwienie pracy dla operatorów. Działania AM są wykonywane często – najczęściej raz na zmianę. Im te działania są prostsze, tym mniejsza jest szansa na pomyłki podczas ich realizacji. Jedną z głównych zasad przy doskonaleniu procesów wg Kaizen jest praca na udokumentowanych procesach – krok 4 w we wdrażaniu AM.
Dokumentowanie procesów AM w TPM
Obecnie jednym z najczęstszych podejść stosowanych przy tworzeniu standardów AM jest wykorzystanie programu Training Within Industry (ang. Szkolenia w przemyśle, TWI). Program ten powstał podczas II Wojny Światowej, a jego głównym celem było wyćwiczenie u przełożonych umiejętności szkolenia pracowników, doskonalenia metod pracy i budowania relacji w zespole. W programie TWI tworzy się instrukcje pracy, które zbudowane są z trzech elementów (Liker, Maier, 2007): głównych kroków, wskazówek i przyczyn występowania wskazówek (rys. 2).
Rys. 2. Podział pracy stosowany na instrukcji pracy wg programu TWI
Źródło: Misiurek B., 2016, Standardized Work with TWI: Eliminating Human Errors in Production and Service Processes, Productivity Press, New York
Główne kroki opisują metodę pracy (co robisz). Wskazówki i przyczyny występowania wskazówek opisują sposób pracy (jak to robisz i dlaczego to robisz tak, a nie inaczej). Ten podział pracy jest szczególnie ważny w działaniach AM, gdzie od operatora nie wymaga się tylko i wyłącznie postępowania wg standardu (kroki i wskazówki), ale również istotne jest, aby świadomie reagował na dostrzeżone problemy (znajomość przyczyn i skutków). Dlatego tak istotne jest przy tworzeniu standardów AM określenie przyczyn występowania wskazówek, bo to przyczyny uczą operatorów świadomości. W Tabeli 1 przedstawiono fragment przykładowego standardu AM zapisanego na podziale pracy wg programu TWI.
Tabela 1. Fragment standardu działań AM opisanego z wykorzystaniem programu TWI.
Główne kroki (co?) | Wskazówki (jak?) | Przyczyny (dlaczego?) |
1.Wyczyść pojemnik na odpady | 1.Odkręć 10 śrub | 1.Jest to potrzebne, aby dostać się do środka maszyny. Pleksa jest zamocowana na 10 śrubach, które musisz wykręcić. |
2.Za pomocą zmiotki | 2.W ten sposób wyczyścisz pojemnik. Rękami będzie to trudne. | |
2. Sprawdź zakres ciśnienia | 1. Zakres poprawny pomiędzy: 0 – 2,5 bara | 1.Wzrost ciśnienia w instalacji może też być spowodowany uszkodzeniem np. wężownicy, płaszcza czy wymiennika. Należy poinformować o tym służby utrzymania ruchu. |
3.Kontroluj wagę | 1.Wynik pomiaru (max 5 kg) | 1. W przypadku większej masy może dojść do uszkodzenia podstawy zbiornika. Musisz cały czas kontrolować wynik pomiaru i mieć pewność, że nie przekracza 5 kg. |
Każda wskazówka to potencjalne miejsce pomyłki człowieka wykonywującego działania AM. Zasada jest jedna: im mniej wskazówek w pracy, tym praca jest łatwiejsza – jest mniej szans na pomyłkę. Dlatego w procesie doskonalenia pracy wg filozofii Kaizen kluczowa jest eliminacja wskazówek poprzez działania doskonalące, a jeżeli to nie możliwe, to próba ułatwienia ich wykonywania.
Wróćmy jeszcze do tematu dokumentowania. Z pewnością każdy praktyk zgodzi się, że dobry standard AM powinien zawierać zdjęcia i obrazki. Dlaczego? Ludzie wzrokowo przyswajają do 83% informacji. Podział pracy przedstawiony na Rysunku 2 jest podstawą pod tworzenie wizualizowanych instrukcji pracy. Wówczas na zdjęciach przedstawia się wskazówki (jak wykonać dany główny krok). Zdjęcia powinny obrazować sposób wykonywania pracy, a nie jej efekt (główne kroki) – to bardzo ważna zasada przy tworzeniu standardów.
5W1H – podejście do doskonalenia pracy w oparciu o filozofię Kaizen
Podejście do usprawniania pracy małymi kroczkami (pierwowzór dla Kaizen) powstało w USA również w ramach programu TWI, a dokładniej metody TWI Metody Pracy (TWI MP). Metoda ta, zamiast zachęcać do dużych radykalnych zmian w celu osiągnięcia pożądanych celów, skłaniała osoby ją stosujące do drobnych usprawnień. Takich, które można byłoby wdrożyć najlepiej tego samego dnia. Było to związane z brakiem czasu i środków podczas II wojny światowej na dokonywanie dużych i innowacyjnych zmian przy produkcji sprzętu wojennego. Istotne było rozwijanie się przy użyciu istniejącej siły roboczej i technologii. Skuteczność metody TWI MP była efektem zastosowanego podejścia 5W1H, które wymuszało doskonalenie pracy w sposób ustrukturyzowany z wykorzystaniem kolejnych 6 pytań:
- WHY is it necessary? (pol. Dlaczego jest to potrzebne)
- WHAT is its purpose? (pol. Jaki jest cel? / Po co?)
- WHERE should it be done? (pol. Gdzie to powinno być wykonane?)
- WHEN should it be done? (pol. Kiedy to powinno być wykonane?)
- WHO is best qualified to do it? (pol. Kto powinien to wykonać?)
- HOW is the best way to do it? (pol. Jak to wykonać lepiej?)
Nazwa podejścia 5W1H wywodzi się od użytych liter przy kolejno zadawanych 6 pytaniach w języku angielskim. Podejście to zostało w pełni przyjęte przez Toyotę wchodząc w skład systemu produkcyjnego Toyoty (ang. Toyota Production System) jako główna metoda budująca podejście Kaizen. Zadawanie wspomnianych pytań ma na celu uzyskanie jak największej liczby pomysłów na doskonalenie sposobu wykonywania pracy. Ważne jest, aby nie odrzucać jakiegokolwiek pomysłu, nawet jeśli na samym początku wydawać się może nierealnym do wdrożenia.
Ostatnie pytanie doskonalące: Jak to lepiej wykonać? (ang. How?) nie ma celu uzyskania lepszej sekwencji pracy. Zostało ono zastosowane po to, aby uzyskać jak najwięcej pomysłów związanych z uproszczeniem i ułatwieniem pracy człowieka, szczególnie w zakresie bezpieczeństwa i ergonomii pracy. Stąd podejście 5W1H stanowiące podstawę modelu Kaizen należy traktować jako usprawnienie w dwóch obszarach:
- Metoda – poprzez ustalenie, czy dana wskazówka jest naprawdę potrzebna oraz określenie najlepszej sekwencji pracy (pytania z grupy 5W).
- Człowiek – poprzez uproszczenie pracy operatora w obszarach bezpieczeństwa oraz ergonomii pracy (pytanie z grupy 1H).
Zadawanie pytań dokładnie w takiej kolejności działa jak stymulator burzy mózgów. Jednak w odróżnieniu od burzy mózgów, 5W1H doskonale sprawdza się nawet podczas indywidualnej analizy pracy, ponieważ wymaga zastanowienia się nad każdą ze wskazówek pracy z osobna.
Pytanie pierwsze z podejścia 5W1H: Dlaczego jest to potrzebne? (ang. Why?) jest pytaniem o przyczynę występowania wskazówki. Zostało to pytania zadane przy tworzeniu standardu AM (Tabela 1). Odpowiedź na to pytanie to przyczyna występowania danej wskazówki.
Przy doskonaleniu metod pracy wg filozofii Kaizen istotne jest eliminowanie wskazówek, a jeżeli nie ma takiej możliwości, to ułatwianie ich wykonywania. Dzięki temu zmniejszy się szansa wystąpienia błędu człowieka. W Tabeli 2 zaprezentowano analizę doskonalącą wg podejścia 5W1H dla standardu AM zapisanego w Tabeli 1. Opracowana metoda doskonalenia wykonywanych wskazówek w pracy jest autorską metodą zespołu LeanTrix i nosi nazwę Poka Yoke Generator Sheet (Misiurek, 2016).
Tabela 2. Analiza doskonaląca z wykorzystaniem podejścia 5W1H i podziału pracy na główne kroki, wskazówki i przyczyny – Poka Yoke Generator Sheet
Główny krok | Wskazówka | Przyczyny (dlaczego?) | Co jest celem? | Gdzie? | Kiedy? | Kto? | Jak? | Pomysły | |
1.Wyczyść pojemnik na odpady | 1.Odkręć 10 śrub | 1.Jest to potrzebne, aby dostać się do środka maszyny. Pleksa jest zamocowana na 10 śrubach, które musisz wykręcić. | X | Można podzielić pleksę na dwie części i wtsawić zawias. Wówczas wystarczy odkręcić tylko 4 śruby i otworzyć połowe pleksy. Dzięki temu skróci się czas odkręcania. | |||||
2.Za pomocą zmiotki | 2.W ten sposób wyczyścisz pojemnik. Rękami będzie to trudne. | X | Można użyć odkurzacz, który ułatwi wyczyszczenie pojemnika. | ||||||
2. Sprawdź zakres ciśnienia | 1.Zakres pomiędzy 0-2,5 bara | 1.Wzrost ciśnienia w instalacji może też być spowodowany uszkodzeniem np. wężownicy, płaszcza czy wymiennika. Należy poinformować o tym służby utrzymania ruchu. | X | Łatwiej będzie jeżeli podany zakres oznaczy się kolorem zielonym. | |||||
3.Kontroluj wagę | 1.Wynik pomiaru (max 5 kg) | 1. W przypadku większej masy może dojść do uszkodzenia podstawy zbiornika. Musisz cały czas kontrolować wynik pomiaru i mieć pewność, że nie przekracza 5 kg. | X | Nie będzie potrzeby kontrolowania wyniku pomiaru, jeżeli zainstalowany zostanie czujnik wagi informujący operatora o tym, że zbliża się do wagi 5 kg. Czujnik ustawiony na 4,5 kg. W momencie przekroczenia 4,5 kg zapali się kontrolka i sygnał dźwiękowy – Andon. |
W ramach analizy doskonalącej powstały pomysły usprawniające pracę. Dla przykładu pojawił się pomysł, aby przeciąć pleksę w połowie i zakonotować zawias (1.główny krok, 1.wskazówka) (Rysunek 3). Dzięki temu w krótszym czasie będzie można dostać się do środka maszyny w celu jej wyczyszczenia. W tym konkretnym pomyśle czas odkręcania pleksy został zredukowany z 2 minut do 50 sekund. W ramach analizy doskonalącej powstały inne pomysły jak np. mocowanie pleksy za pomocą śrub motylkowych. Dział BHP jednak odrzucił ten pomysł argumentując to tym, że do maszyny dostęp może być tylko z wykorzystaniem narzędzi. Pomysł z przecięciem pleksy spełniał te wymogi.
Rys. 3. Pomysł doskonalący z przecięciem pleksy
Źródło: Wolak M., Kotlarski B., Maczuga M., 2014, 5S Fundamentem Trwałego Systemu TPM, Prezentacja na XIV Konferencji Lean Management, Wrocław
Innym pomysłem podczas doskonalenia tego procesu było oznaczenie poprawnych zakresów ciśnienia kolorem zielonym (2. główny krok, 1. wskazówka). Rozwiązanie to zaprezentowano na rysunku 4. Dzięki temu rozwiązaniu operator nie będzie musiał zapamiętywać odpowiedniego zakresu (0-2,5 bara). Praca będzie dla niego łatwiejsza.
Rys. 4. Przykład rozwiązania dotyczącego wykorzystania sterownika wizualnego
Źródło: Misiurek B., 2016, Standardized Work with TWI: Eliminating Human Errors in Production and Service Processes, Productivity Press, New York
Opisane pomysły dają duże korzyści, a z drugiej strony praktyczne nie wymagają wysiłku wdrożeniowego. To cała esencja filozofii Kaizen – prostota. W Tabeli 3 zaprezentowano fragment nowego standardu AM po przeprowadzeniu działań doskonalących z wykorzystaniem podejścia 5W1H.
Tabela 3. Fragment usprawnionego standardu działań AM rozpisany na podziale pracy wg programu TWI.
Główne kroki | Wskazówki | Przyczyny |
1.Wyczyść pojemnik na odpady | 1.Odkręć 4 śruby | 1.Jest to potrzebne, aby dostać się do środka maszyny. Odkręcając 4 śruby będziesz mógł otworzyć pleksę dzięki zawiasom. |
2.Odkurzacem | 2.W ten sposób łatwiej wyczyścisz pojemnik. | |
2. Sprawdź zakres ciśnienia | 1. Zakres zielony | 1.Wzrost ciśnienia w instalacji może też być spowodowany uszkodzeniem, np. wężownicy, płaszcza czy wymiennika. Należy poinformować o tym służby utrzymania ruchu. |
3.Kontroluj wagę |
W przedstawionym standardzie AM w Tabeli 3, trzeci główny krok został bez żadnej wskazówki dzięki rozwiązani Andon, który powiadamia operatora o przekroczeniu wagi. Operator nie musi zerkać na wynik pomiaru.
Podsumowanie
Doskonalenie działań AM wg filozofii Kaizen to bardzo skuteczne podejście, aby zwiększać dostępność maszyn poprzez redukcję czasu ich czyszczenia i konserwacji. To również podstawa pod ułatwianie pracy dla operatorów co przekłada się na mniejszą liczbę pomyłek oraz skrócenie czasu instruktażu stanowiskowego (mniej wskazówek do przekazania uczniowi). Ważne jest, aby pamiętać o tym, że filozofia Kaizen jest skuteczna głównie wtedy, kiedy zostanie opracowany standard pracy, który zostanie poddany doskonaleniu. To jedna z ważniejszych zasad filozofii Kaizen. Przedstawiony w artykule podział pracy na główne kroki, wskazówki i przyczyny jest pomocny nie tylko po to, aby doskonalić pracę z wykorzystaniem narzędzia Poka Yoke Generator Sheet. To również podstawa pod szkolenie operatorów z działań AM z wykorzystaniem metody TWI Instruowanie Pracowników (ang. TWI Job Instruction).
Literatura
- Liker J., Meier D., 2007, Toyota Talent: Developing Your People the Toyota Way, McGraw-Hill Education; 1 edition
- Misiurek B., 2016, Standardized Work with TWI: Eliminating Human Errors in Production and Service Processes, Productivity Press, New York
- Nakajima S., 1988, Introduction to TPM: Total Productive Maintenance, Productivity Press, New York
- Wolak M., Kotlarski B., Maczuga M., 2014, 5S Fundamentem Trwałego Systemu TPM, Prezentacja firmy LG Display na XIV Konferencji Lean Management, Wrocław
Autor: dr inż. Bartosz Misiurek, CEO LeanTrix
Artykuł opublikowany w czasopiśmie Szef UR.
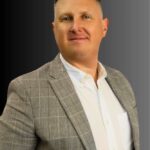
Jestem popularyzatorem Lean Management oraz programu Training Within Industry. Jestem praktykiem. Współtworzę wiele startupów. Od 2015 roku jestem CEO w Leantrix - czołowej firmie z zakresu konsultingu Lean w Polsce, która począwszy od 2024 roku organizuje jedną z największych konferencji poświęconych szczupłemu zarządzaniu w Polsce - Lean TWI Summit. Od 2019 roku jestem CEO w firmie Do Lean IT OU zarejestrowanej w Estonii, która tworzy software etwi.io używany przez kilkadziesiąt firm produkcyjnych i usługowych w Europie i USA.