Narzędzie jakim jest 5S, jest znane niemalże wszystkim, którzy związani są na co dzień z produkcją czy też utrzymaniem ruchu. Wiele osób potrafi wymienić wszystkie kroki tej metody. Większość osób z kadry zarządzającej twierdzi, że rozumie idee. Nic w tym niezwykłego, ponieważ 5S jest logiczną metodą mającą na celu utrzymywanie stanowiska pracy zwiększając, bezpieczeństwo, ergonomie i porządek. Dlaczego jednak tak proste narzędzie jest tak trudne do wdrożenia? Co sprawia, że spotyka się ono z tak dużym oporem wśród pracowników? Ten artykuł nie będzie opowiadał o tym czym jest 5S i z jakich kroków się składa. Ten artykuł stawia czoła realnym problemom zaobserwowanym podczas wdrożeń oraz przedstawia propozycje skutecznej implementacji na obszarach w przedsiębiorstwie.
Problem 1. Wdrażamy 5S, bo tego wymagają klienci.
To nie profesjonalny marketing sprawił, że narzędzie w postaci 5S jest obecnie standardem we wielu korporacjach. Idei 5S dla kadry świadomej zarządzającej praktycznie nie trzeba sprzedawać, wystarczy, że zaobserwują poprawę podstawowych wskaźników podczas pracy na stanowiskach. I właśnie poprawa Kluczowych Wskaźników Efektywności (KPI) jest podstawą do rozpoczęcia implementacji. Każdy z menadżerów jest rozliczany z KPI, dlatego tak dużym zainteresowaniem cieszą się narzędzia pozwalające ich w tym wesprzeć. Z doświadczenia wynika, że sprawnie i świadomie wdrożony system 5S poprawia przedewszystkim bezpieczeństwo pracy na stanowisku, efektywność pracy pracowników oraz jakość wykonywanych wyrobów. Biorąc pod uwagę powyższe fakty, każdy menager powinien być wewnętrznie zainteresowany wdrożeniem 5S na swoim obszarze. Zdarzają się jednak sytuacje, gdzie brakuje tej świadomości wśród kadry zarządzającej, dlatego najlepszą metodą na przekonanie ich do zmiany myślenia jest benchmarking, bądź pokazanie skuteczności na przykładzie obszaru pilotażowego. Niestety bez wsparcia i nadzoru nad wynikami przez wyższe kierownictwo, nie będzie możliwości implementacji żadnego narzędzia w perspektywie całej organizacji.
Problem 2. 5S to sprzątanie
Każdy z nas pamięta z dzieciństwa sobotnie poranki, kiedy to „ochoczo” pomagaliśmy w cotygodniowych porządkach. Sprzątanie dla większości z nas nie jest najwspanialszą aktywnością szczególnie, gdy ktoś od nas tego wymaga. Nie było by problemu, gdyby nie przekonania większości pracowników niższego szczebla, że 5S to właśnie sprzątanie. Trudno wyjaśnić zjawisko, przy którym kierownicy na ogół rozumieją idee 5S, ale nie potrafią jej skaskadować na niższe szczeble. Nie chodzi tu o dobry system szkoleń, a to z czego pracownicy są najczęściej rozliczani. Ocenia porządku na stanowisku pracy jest najłatwiejsza do zrealizowania, dlatego na tym często polega ocena systemu 5S. Konsekwencją takich działań jest przeświadczenie pracowników o tym, że 5S to sprzątanie. Niezależnie jak skutecznie przeprowadzimy szkolenia i jak często będziemy mówić, że te narzędzie nie polega na sprzątaniu, to jeśli będziemy rozliczać pracowników ze sprzątania to właśnie z tym będzie im się on kojarzył.
Problem 3. Forma audytów
Audyty, czyli ocena, która z natury nie podoba się ludziom, dlatego trudno, aby patrzyli oni na nie przychylnie. Jednak audytowanie systemu zapewnia jego skuteczny rozwój, więc aktywności z nimi związane powinny być traktowane jako możliwości poprawy, a nie jak wytykanie błędów. Brak audytów to podstawowy błąd. Jeśli nie sprawdzamy „jak” coś funkcjonuje to prędzej czy później się to popsuje. Przykładem jest tu zarówno maszyna jaki i system 5S. Audyty są tak samo ważne jak konserwacja urządzeń i prewencyjne wymiany elementów. W przypadku konserwacji maszyn dokładnie wiemy „dlaczego” to robimy – aby utrzymać ciągłość produkcji, a jak to to wygląda w przypadku audytów 5S? Odpowiedzi na te pytania bywają różne: aby był porządek na stanowisku, aby utrzymać system 5S, czasami po to, aby pracownikom pracowało się lepiej. Ta ostatnia odpowiedź daje nam światełko w tunelu, lecz gdy przychodzi audyt gaśnie, bo sprawdzamy, czy pracownicy utrzymują porządek. Podstawową kwestią jaką należy poruszyć przed zapisywaniem pytań audytowych jest cel wdrożenia 5S. Celem jest zawsze poprawa wskaźników efektywności i to je w pierwszej kolejności powinniśmy badać. Następnie sprawdzamy te elementy, które najbardziej wpływają na poprawę KPI, czyli ergonomie pracy i bezpieczeństwo pracy. Polega to na rewidowaniu standardów. Dopiero na samym końcu, kiedy mamy pewność, że działania 5S na danym stanowisku poprawiają jakość pracy, zaczynamy audytować zachowania ludzi.
Przed wewnętrznymi audytorami systemu 5S, stoi bardzo trudne zadanie. Można by rzec, jeśli chcesz by ludzie na produkcji Cię nie lubili zostań wewnętrznym audytorem. We wielu firmach rzeczywiście tak jest, traktujemy audytorów i audyty jako zło konieczne. Jeśli jednak tworząc karty audytów określimy jasno cele i na ich podstawie zapiszemy pytania audytowe to będzie zdecydowanie łatwiej realizować ten proces.
Jak wygląda zły audyt z perspektywy operatora – historia w artyule pod tym linkiem.
Problem 4. Wdrażanie wszystkich kroków za jednym razem
Nauczyliśmy się na warsztatach 5S przeprowadzać wszystkie kroki tej metody za jednym razem. Dzięki temu łatwo możemy zobrazować na zdjęciach jak było wcześniej, a jak jest teraz. Niemalże od razu widać wizualne efekty naszej pracy. Problem pojawia się na następny dzień, kiedy pracownicy przychodzący do pracy i nie mogą się odnaleźć w nowym środowisku. Lean to ewolucja, drobne kroki stawiane każdego dnia przez wszystkich pracowników. Przykład wdrażania 5S zobrazowany wcześniej jest przykładem rewolucji. Niewiele w historii świata jest rewolucji, które przebiegały w zgodzie i porządku, dlatego nie oczekujmy tych wartości po nagłym wprowadzaniu 5S. Do zmian ludzie musza się stopniowo adoptować, niezależnie czy to są zmiany społeczne, polityczne, kulturowe czy te dotyczące ich miejsca pracy. Po to w metodzie jest 5 kroków, aby stawiać je oddzielnie. Dzięki temu pracownicy mają czas na zaklimatyzowanie się z drobnymi zmianami, które w konsekwencji poprowadzą do skutecznego wdrożenia 5S.
Niezmiernie ważnym elementem podczas wdrażania jest również zaangażowanie w nie pracowników bezpośrednio związanych z danym stanowiskiem. Powodów jest wiele. Podstawowa kwestia techniczna to taka, że pracownicy doskonale znają ich własne stanowisko pracy, dokładnie wiedzą czego używają częściej, a co rzadziej. Bez wykorzystania tej podstawowej wiedzy pracowników próby implementacji 5S skończą się fiaskiem i utraconym zaufaniem. Natomiast podstawowa kwestia psychologiczna, polega na tym, że zaangażowany w zmiany pracownik łatwiej je zaakceptuje, bo to będą w końcu jego zmiany. Nie lubimy jak narzucane jest coś z góry, lecz jeśli sami to zmieniamy wierzymy, że pomoże osiągnąć lepsze rezultaty.
Problem 5. Odpowiedzialność za wdrożenie spoczywa na dziale Lean.
Działy Lean bardzo często są jednymi z najbardziej innowacyjnych działów w przedsiębiorstwie. Równie często jednak odpowiadają za wyniki wdrożenia narzędzi, które nie są dedykowane dla nich. Narzędzia Lean, maja pomagać w realizowaniu produkcji na jeszcze wyższym poziomie i słowo produkcja jest tu kluczem. Najbardziej zainteresowanym działem, jeśli chodzi o wdrożenie 5S powinien być właśnie dział produkcji i to na nim powinna spoczywać odpowiedzialność jego implementacji. Działy Lean w tej sytuacji pełnią rolę doradczą, a nie wykonawczą. To produkcja ze względu na wyznaczone zadanie wdrożenia 5S, powinna szukać wsparcia we dziale Lean. W przeciwnym razie, dochodzi do sytuacji, gdzie nie znajdujemy w organizacji czasu na realizacje działań związanych z doskonaleniem stanowiska pracy. Skuteczne wdrożenie narzędzia 5S zależy między innymi od kwestii ustalenia właściwego adresata celu. Jeśli zależy nam na poprawie jakości, efektywności i bezpieczeństwa pracy to cel musi być skierowany w stronę działu, któremu te miejsca podlegają w strukturach organizacji i które mają największy wpływ na jego funkcjonowanie.
Skuteczne wdrożenie 5S w oparciu o cykl PDCA
Cykl PDCA to podstawowe narzędzie, które stosowanej jest w obliczu implementacji nowych rozwiązań. W każdej firmie proces ten powinien być dostosowany do środowiska w jakim działa organizacja, jednak można znaleźć punkty, które powinny znaleźć się w każdym z tych programów wdrożeń. Poniżej przedstawiono ścieżkę wdrożenia jaką można się posłużyć przy implementacji narzędzia 5S.
Główny Krok | Wskazówka |
1. Zaplanuj wdrożenie narzędzia 5S |
|
2. Wdróż 5S na obszar pilotażowy |
|
3. Sprawdź skuteczność wdrożenia |
|
4. Rozszerzaj działania na pozostałe obszary |
|
Podsumowanie
Narzędzia Lean są z natury bardzo łatwe do zrozumienia, jednak ich największą wadą, ale też zaletą jest to, że zależą przede wszystkim od ludzi. Każdy system jest tak skuteczny jak jego najsłabsze ogniwo, w przypadku 5S tym ogniwem jest umiejętność postępowania z ludźmi. Jeśli zależy na skutecznym, czyli świadomym wdrożeniu musimy w pierwszej kolejności zadbać o miękką stronę.
Autor: Kamil Müller
Artykuł został opublikowany na łamach czasopisma SzefUR
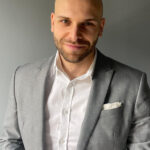
Praktyk programu Training Within Industry i Lean Management.
Wykłada na Wyższej Szkole Bankowej we Wrocławiu. Jest autorem i współautorem kilku pozycji literaturowych poświęconych programowi TWI.
Obecnie pełni funkcję partnera zarządzającego w firmie LeanTrix, jak i master Trenera Na Europę. Dodatkowo zaangażowany jest w projekty takie eTWI System i Lean Community
Prowadził projekty między innymi dla: Lotte Wedel, Danone, Kompania Piwowarska, eobuwie.pl, Arvato, Whirlpool, B/S/H, Geberit, RECARO, Tenneco, Sumitomo Electric, Stadler, Vesuvius Poland