Diagnostyka maszyn. W artykule opisano w jaki sposób angażować operatorów do działań diagnostycznych na maszynie w ramach autonomicznej konserwacji. Przedstawiono formularz wspierający identyfikację usterek podczas gruntownego czyszczenia maszyn. Pokazano w oparciu o przykład rzeczywisty w jaki sposób tworzyć system zgłaszania usterek w firmie.
Diagnostyka to pojęcia, które towarzyszy nam w każdym dniu naszego życia. Z definicji diagnostyka (gr. diagnosis – rozpoznanie, ustalenie) jest nauką zajmującą się rozpoznaniem problemów w danym obiekcie, zarówno w człowieku, jak i maszynie. Wykonując badania krwi diagnozujemy stan naszego ciała. Jesteśmy w stanie określić problemy zanim ich objawy zewnętrzne będą zagrażały naszemu życiu. Diagnozowanie jest zatem działaniem prewencyjnym, którego głównym celem jest możliwie szybkie i bezinwazyjne zdefiniowanie problemu. Diagnostyka techniczna jest natomiast oceną stanu technicznego maszyn, narzędzi i urządzeń na podstawie obserwacji skutków ich działania. Zazwyczaj diagnostyka techniczna kojarzona jest z wykorzystaniem zaawansowanych narzędzi wspomagających ten proces. Kiedy podjeżdżamy nowym samochodem do serwisu jest on podłączany do stacji diagnostycznej, która wskazuje pracownikowi serwisu potencjalne problemy z naszym samochodem. Często na halach produkcyjnych, podobnie jak w serwisach samochodowych, diagnostyka techniczna realizowana jest przez specjalistyczny personel podczas zaplanowanych gruntownych przeglądów maszyny. Bez udziału operatorów, czy też jak w przypadku ruchu drogowego kierowców. Niestety w odróżnieniu od ruchu drogowego, w którym co raz więcej występuje samochodów nowych, o tyle na halach produkcyjnych dominują maszyny uznawane za starsze, wiekowe. Ich plusem jest duża niezawodność, a minusem utrudnione zastosowanie nowoczesnych rozwiązań diagnostycznych.
Nowe maszyny – jedyna szansa w efektywnej diagnostyce?
Powszechnie uważa się, że zakup nowych maszyn przełoży się na poprawę efektywności całego procesu produkcyjnego. Maszyny te są zazwyczaj rozbudowane o zaawansowane rozwiązania diagnostyczne. Zakup takich maszyn praktycznie zawsze wiąże się z dużymi wydatkami inwestycyjnymi, na które wiele firm nie może sobie pozwolić. Inną możliwością jest poprawa efektywności wykorzystania dostępnego parku maszynowego. Istnieje błędny pogląd, według którego nowa maszyna oznacza zawsze natychmiastową poprawę efektywności. Nowe maszyny, wyposażone w najnowocześniejsze rozwiązania diagnostyczne, bez dobrze zaprojektowanego i realizowanego planu utrzymania ruchu oraz dobrze wyedukowanej załogi bardzo szybko utracą swoją maksymalną efektywność wykorzystania (Rysunek 1).
Rys. 1 Wykres obrazujący spadek efektywności wykorzystania maszyny bez odpowiednio przygotowanego systemu przeglądów maszyny
Zupełnie odwrotna sytuacja jest w momencie wdrożenia rozwiązań poprawiających organizację pracy z maszyną. Dobrze zaprojektowany plan utrzymania ruchu oraz dobrze przeszkoleni operatorzy dają fundamenty pod osiągnięcie maksymalnej możliwej efektywności, a w przypadku usprawnień w pracy człowieka z maszyną, możliwe jest nawet zwiększenie efektywności od tej, która została założona przez producenta (Rysunek 2).
Rys. 2. Wykres obrazujący możliwość poprawy efektywności wykorzystania maszyny przy poprawnie wdrożonym systemie planowych przeglądów oraz działań doskonalących
Firmy powinny zatem zwiększać efektywność wykorzystania swoich maszyn poprzez poprawę organizacji pracy, zaprojektowanie i przestrzegania standardów konserwacji, skuteczny system szkolenia pracowników oraz proces usprawniania pracy. Diagnozowanie stanu technicznego maszyn wiekowych powinno angażować przede wszystkim operatorów, którzy są najbliżej maszyny. To oni są w stanie wychwycić wszystkie problemy, zanim przerodzą się one w poważne awarie.
Sposoby angażowania operatorów w diagnostykę techniczną maszyn
Problem w pracy maszyny, który nie powoduje jej przestoju, nazywa się usterką. Praktycznie każda maszyna ma jakąś usterkę. Z pewnością w swoim samochodzie masz wiele mniejszych, czy większych usterek. Twój samochód jednak jeździ. Wydaje się być sprawny. Czy na pewno?
Każda usterka zawsze doprowadzi do awarii! Jest tylko jedna niewiadoma: czas. Nawet uszkodzony podajnik na kawę w samochodzie może doprowadzić do wypadku, kiedy zapomnisz się i włożysz do niego kawę, która wyleję się na Twoją nogę podczas jazdy. To oczywiście bardzo mało prawdopodobne, dlatego w tej sytuacji wspomniany czas może być bardzo długi. Zupełnie inaczej będzie w przypadku mocno wytartej opony. Do nieplanowanego zatrzymania samochodu (awarii koła) może dojść w bardzo krótkim czasie. Zasada jest jedna: im mniej usterek na maszynie tym mniejsza jest szansa na wystąpienie awarii. Istotne jest wobec tego skuteczne identyfikowanie usterek zanim przerodzą się one w poważne problemy. Takie diagnozowanie stanu maszyny jest najbardziej skuteczne, kiedy wykonuje je operator.
Dwa sposoby angażowania operatorów w proces diagnozowania stanu technicznego maszyny
-
Diagnozowanie usterek podczas gruntownego czyszczenia maszyn
To punkt startowy. Podczas gruntownego czyszczenia operatorzy uczą się dużo na temat swojej maszyny. Ważne, aby w ten proces zaangażowani byli również pracownicy UR, którzy na bieżąco przekazują operatorom wiedzę zarówno o budowie maszyn, jak i ich obsłudze. Hasłem przewodnim tego procesu nie może być: „sprzątanie maszyny”. Musi nim być: „identyfikacja problemów w maszynie”. Czyszczenie jest operacją pomocniczą w dobrej identyfikacji problemów. Kluczowe w tym procesie jest korzystanie przez operatorów z arkusza identyfikacji usterek (Tabela 1), który definiuje jakie obszary maszyny powinny być sprawdzone pod względem występowania nieprawidłowości.
Tab. 1. Arkusz identyfikacji usterek
Na co należy zwrócić uwagę podczas analizy stanowiska przy maszynie Sprawdź czy występują w danej grupie: |
Układ elektryczny
|
Układ smarowania
|
Połączenia śrubowe
|
Narzędzia
|
Działanie maszyny
|
Czystość / Zanieczyszczenia
|
Istniejące procedury / standardy czyszczenia i konserwacji
|
Obudowa maszyny
|
Oświetlenie
|
Otoczenie maszyny / urządzenia
|
Panel sterowniczy
|
Oznaczenia na urządzeniach
|
-
Diagnozowanie usterek podczas codziennej pracy na maszynie
Gruntowne czyszczenie i identyfikowanie problemów w pracy maszyny opisane w punkcie 1 jest zazwyczaj akcją wykonywaną na maszynie maksymalnie kilka razy w roku. Istotne jest, aby nawyk identyfikacji usterek wszedł w codzienną rutynę pracy operatorów. Dlatego kluczowe jest opracowanie dla nich instrukcji autonomicznej konserwacji, które prowadzić ich będą przez przeglądy najważniejszych elementów maszyny. Zalecane jest również opracowanie katalogu usterek. W nim zestawione są opisy potencjalnych usterek (Tabela 1) wraz z przykładowymi zdjęciami. Dobrym momentem opracowania katalogu usterek jest proces gruntownego czyszczenia maszyny. Wówczas większość z tych typów usterek uda się zidentyfikować i przedstawić na zdjęciach. Ostatnim etapem powinno być zaprojektowanie systemu zgłaszania usterek. To poprzez niego operatorzy będą zgłaszać pracownikom UR zidentyfikowane podczas codziennych przeglądów usterki. System ten powinien być przejrzysty i zrozumiały dla operatora, ponieważ to głównie operator odpowiedzialny jest za informowanie pracowników UR na temat wszelkich nieprawidłowości w pracy maszyny. Formy karty zgłaszania usterek mogą być różne (papierowe, elektroniczne itp.). Istotne jest aby taka karta zawierała podstawowe informacje, takie jak:
- Nazwisko i imię osoby zgłaszającej usterkę.
- Nazwa maszyny.
- Data zgłoszenia.
- Wydział.
- Dokładny (szczegółowy) opis usterki oraz zdefiniowanie miejsca jej występowania na maszynie.
- Propozycja usunięcia usterki.
Wszystkie informacje zawarte na karcie są bardzo istotne bo umożliwiają pracownikom UR określić, gdzie znajduje się usterka i jaki jest jej priorytet. Na Rysunku 3 przedstawiono przykładowy system zgłaszania usterek z firmy LG Display Poland sp. z o.o.
Rys. 3. System zgłaszania usterek z firmy LG Display Poland sp. z o.o.
Źródło: Wolak M., Kotlarski B., Maczuga M., 2014, 5S Fundamentem Trwałego Systemu TPM, Materiały Konferencyjne do XIV Konferencja Lean Management, Wrocław
System ten został opracowany podczas warsztatów praktycznych przez wspólny zespół operatorów i pracowników UR. Jest on narzędziem komunikacji pomiędzy tymi dwoma grupami osób. Jego działanie jest proste. Operator zgłasza usterkę wypisując kartę, a następnie przykleja magnes (strona czerwona) z numerem karty na rysunku maszyny w miejscu, które odpowiada rzeczywistej lokalizacji usterki. Pracownicy UR mają 48 godzin na podjęcie działania z usterkę, wypisania karty usterki oraz obrócenie magnesu na stronę żółtą. Podjęte działanie nie musi oznaczać usunięcia usterki. Musi natomiast być zapisania informacja zwrotna dla operatora – jakie działanie podjęli pracownicy UR. Tak zbudowany system tworzy „kanał komunikacyjny” między operatorami i pracownikami UR.
Podsumowanie
Nowoczesne rozwiązania techniczne w zakresie diagnostyki są z pewnością skutecznym sposobem na rozpoznawanie problemów w pracy maszyn. Niestety zakup takich rozwiązań może być dużym wydatkiem, a czasami, przy starszych maszynach, implementacja takich rozwiązań może być nie możliwa. Natomiast angażowanie operatorów w działania diagnostyczne jest możliwe zawsze, nie zależnie czy stosowane są równolegle rozwiązania techniczne. Nie jest to jednak proces łatwy. Trzeba zmienić w nim świadomość ludzi na to, że praca na maszynie to również opieka nad maszyną. Instrukcje autonomicznej konserwacji, katalogi anomalii, czy systemy zgłaszania usterek to tylko narzędzia, które bez świadomych operatorów nie zadziałają. Z drugiej strony aktywność operatorów w zakresie diagnostyki usterek w pracy maszyny przekłada się na znaczną redukcję poziomu awaryjności. Na Rysunku 4 zaprezentowano liczbę zgłoszonych problemów w pracy maszyn w latach 2008-2014 przez operatorów w firmie Nidec Motors & Actuators (Poland) sp. z o.o.
Rys. 4. Liczba zgłaszanych problemów i usterek na maszynach w latach 2008-2015
Źródło: Danek M., Misiurek B., 2015, Jak zdobyć zaangażowanie operatorów do nowych zadań niezbędnych przy efektywnym wdrażaniu filozofii Lean Management na przykładzie Nidec Motors & Actuators (Poland) sp. z o.o., Materiały Konferencyjne do XV Konferencja Lean Management, Wrocław
Dzięki tej aktywności udało się znacząco zredukować liczbę awarii na maszynach. W 2008 roku, kiedy system zgłaszania usterek i problemów zaczął funkcjonować, awarie obniżały efektywność wykorzystania maszyn o 3,8%, a w 2014 roku zaledwie o 1,31% (Rysunek 5).
Rys. 5. Procentowo wyrażona awaryjność maszyn w całkowitej efektywności wykorzystania maszyn
Źródło: Danek M., Misiurek B., 2015, Jak zdobyć zaangażowanie operatorów do nowych zadań niezbędnych przy efektywnym wdrażaniu filozofii Lean Management na przykładzie Nidec Motors & Actuators (Poland) sp. z o.o., Materiały Konferencyjne do XV Konferencja Lean Management, Wrocław
Widać zatem dużą korelację pomiędzy zaangażowaniem operatorów w diagnozowanie problemów w pracy maszyny a wynikami produkcyjnymi, które w tej sytuacji przejawiają się obniżoną awaryjnością maszyn.
Na koniec…
Peter Drucker powiedział kiedyś: Dajcie ludziom swobodę i możliwość działania, a zaskoczą was swoją pomysłowością. Warto angażować operatorów w działania diagnostyczne, bo to z pewnością przełoży się na sukces firmy. To ludzie tworzą każdą organizację i to ludzie są ich największą wartością.
LITERATURA
- Danek M., Misiurek B., 2015, Jak zdobyć zaangażowanie operatorów do nowych zadań niezbędnych przy efektywnym wdrażaniu filozofii Lean Management na przykładzie Nidec Motors & Actuators (Poland) sp. z o.o.,
- Materiały Konferencyjne do XV Konferencja Lean Management, Wrocław
Legutko S., 2004, Podstawy eksploatacji maszyn i urządzeń, Warszawa: Wydawnictwo Szkolne i Pedagogiczne S.A., s. 10, s. 13, s.37 - Liwowski B., Kozłowski R., 2007, Podstawowe zagadnienia zarządzania produkcją, Wolters Kluwer Polska sp. z o.o., s. 124
- Misiurek B., 2015, Metodyka standaryzacji autonomicznych procesów eksploatacyjnych zorientowana na poprawę efektywności maszyn zautomatyzowanych, Praca doktorska, Uniwersytet Technologiczny we Wrocławiu, s. 35-37, Wrocław
- Wolak M., Kotlarski B., Maczuga M., 2014, 5S Fundamentem Trwałego Systemu TPM, Artykuł na XIV Konferencje Lean Management, Lean Enterprise Institute Polska, Wrocław
Informacja o artykule:
Artykuł opublikowany w magazynie Służby Utrzymania Ruchu (listopad – grudzueń 2015)
Autor:
Dr inż. Bartosz Misiurek
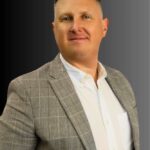
Jestem popularyzatorem Lean Management oraz programu Training Within Industry. Jestem praktykiem. Współtworzę wiele startupów. Od 2015 roku jestem CEO w Leantrix - czołowej firmie z zakresu konsultingu Lean w Polsce, która począwszy od 2024 roku organizuje jedną z największych konferencji poświęconych szczupłemu zarządzaniu w Polsce - Lean TWI Summit. Od 2019 roku jestem CEO w firmie Do Lean IT OU zarejestrowanej w Estonii, która tworzy software etwi.io używany przez kilkadziesiąt firm produkcyjnych i usługowych w Europie i USA.