Tworzenie instrukcji jest kluczowym aspektem przy wdrażaniu działań autonomicznej konserwacji (ang. Autonomous Maintenance, zwana dalej AM). Działania AM są natomiast podstawowym krokiem przy implementacji systemu TPM (ang. Total Productive Maintenance). Za wykonywanie działań AM odpowiedzialni są operatorzy, którzy są najbliżej maszyn i najlepiej „czują” problemy jakie mogą się pojawiać przy ich eksploatacji. Uzupełnieniem AM są systemy zgłaszania usterek do działów UR, z których operatorzy korzystają w momencie wykrycia usterki. Jednak zanim skorzystają z takich systemów muszą być świadomi co powinni sprawdzać i na co powinni zwracać szczególną uwagę poszukując usterek. W tym pomocne są dobrze zdefiniowane i opracowane standardy AM.
Instrukcje to istotny etap w procesie standaryzacji dowolnej pracy. Kluczową sprawą jest jednak uzyskanie odpowiedzi na pytanie: do czego są tak naprawdę potrzebne instrukcje stanowiskowe? Naturalną odpowiedzią jest to, aby zapisać poszczególne kroki w procesie – np. przeglądu maszyny dokonywanego przez operatora w ramach działań AM. Ale czy tylko do tego można ich użyć? Zdecydowanie nie! Instrukcje są niezbędne do efektywnego szkolenia operatorów oraz doskonalenia pracy. Ponadto instrukcje mogą być przydatne do audytowania procesów, a także do podkreślenia kluczowych punktów w zakresie: bezpieczeństwa, jakości czy poprawności w pracy. Jest tylko jeden warunek: instrukcje muszą być opracowane poprawnie i powinny odzwierciedlać rzeczywistość.
Powszechnie przyjmuje się, że wdrażanie procesu AM na wybranym stanowisku składa się z 7 kroków:
- Gruntowne czyszczenie i sprawdzanie maszyny.
- Oznaczanie i eliminacja źródeł zabrudzeń.
- Ułatwianie dostępu do czyszczenia i inspekcji maszyn.
- Określenie standardów czyszczenia i konserwowania.
- Poprawa ogólnych umiejętności inspekcyjnych u operatorów.
- Autonomiczna inspekcja maszyn.
- Proces ciągłego doskonalenia.
Trzy pierwsze kroki związane są ze stabilizacją procesów – doprowadzenia maszyny do możliwie najlepszego stanu używalności. Kroki 4.-7. to część standaryzacji pracy, gdzie standardy odgrywają kluczową rolę. Z moich doświadczeń wdrożeniowych z zakresu TPM, jakie mam z przeszło 50 fabryk, wynika że firmy zazwyczaj dochodzą do 4. kroku. Tworzy się wówczas standardy pracy zapominając, że sama instrukcja nie ma żadnej mocy sprawczej, dopóki nie wykorzysta się jej do szkolenia pracowników (krok 5. i 6.) oraz doskonalenia pracy (krok 7.). Ponadto bardzo często opracowane standardy w firmach są po prostu kiepskie. Nie zwracają one uwagi na to, co w moim przekonaniu jest najważniejsze – na sposób wykonania pracy i uzasadnienie potwierdzające, że przyjęty sposób jest najlepszy. Przy wdrażaniu TPM, a w szczególności AM, zapisanie wiedzy fachowej jest szczególnie ważne, bo przecież w AM chodzi o transfer wiedzy z pracowników UR na operatorów produkcyjnych.
W artykule przedstawię Ci trzy najważniejsze (fundamentalne) zasady tworzenia instrukcji. Nie tylko instrukcji AM, ale ogólnie standardów. Zasady te powstały w oparciu o kilka tysięcy instrukcji, które pomagałem tworzyć albo weryfikowałem w przeszło 150 fabrykach w Europie. Wszystkie zasady opisałem bardzo precyzyjnie w napisanej przeze mnie książce: Standardized Work with TWI: Eliminating Human Errors in Production and Service Processes, która wydana została przez Productivity Press. Ponadto zachęcam Ciebie do skorzystania systemu IT – LeanTrix, w którym przygotujesz instrukcje średnio w czasie o 80% krótszym niż w tradycyjnych programach (np. z pakietu Office). W systemie tym wszystkie te zasady są wbudowane jako ściąga dla użytkowników.
Przedstawione w artykule zasady powstały w oparciu o rozwiązania z programu Training Within Industry (z ang. szkolenia w przemyśle, TWI), który powstał w USA podczas II Wojny Światowej, a po wojnie stał się fundamentem Systemu Produkcyjnego Toyoty, a potem Lean Management. Program TWI jest uzupełnieniem standaryzacji pracy.
Zasada #1. W instrukcji nie skupiaj się wyłącznie na opisie metody pracy, ale głównie na zapisaniu sposobu pracy wraz z uzasadnieniem
Uważam, że najlepszy format instrukcji pracy to ten, który powstał w programie TWI – Instruowanie Pracowników. W tym formacie instrukcję pracy dzieli się na: główne kroki, wskazówki i przyczyny występowania wskazówek (Rysunek 1). Taki podział pracy użyty w instrukcji opisuje zarazem metodę pracy poprzez główne kroki, jak i sposób wykonania pracy poprzez wskazówki z ich przyczynami.
Rys. 1. Podział pracy na instrukcji pracy
(źródło)
Dzięki objaśnieniu w instrukcji wskazówek i przyczyny ich występowania wpływa się na eliminację błędów ludzkich. Człowiek uczy się dowolnej operacji, kiedy dowiaduje się, jak ją należy wykonać (wskazówki) i dlaczego taki sposób wykonania jest najlepszy (przyczyny). Jest to szczególnie ważne przy wdrażaniu AM, gdzie dla operatora czynności konserwacyjne są czymś zupełnie nowym. Dlatego tak ważne jest uczenie go nie tylko tego co ma robić i jak to robić, ale przede wszystkim budowanie świadomości dlaczego ten sposób jest najbardziej optymalny.
W znaczącej większości fabryk, dla których pracowałem, instrukcje pracy zawierały kroki często wymieszane ze wskazówkami, ale brak było w nich przyczyn. Sprawdź instrukcje w swojej fabryce i zwróć uwagę, czy występują w nich przyczyny. Z dużą dozą prawdopodobieństwa mogę stwierdzić, że nie!
Zasada #2. Nigdy nie przekazuj instrukcji przed instruktażem
Z moich doświadczeń wynika, że w 80% przypadków operator dostaje instrukcję do poczytania przed instruktażem. Nie ważne, czy jest szkolony z czynności produkcyjnych, czy AM. Nauka na podstawie nawet najlepszej instrukcji jest mało efektywna. Dlaczego? Bo ludzie zapamiętuję zaledwie 10% informacji przeczytanych (Rysunek 2). Najbardziej skuteczny sposób przyswajania wiedzy to zobaczenie pracy w praktyce i równoczesne przysłuchiwanie się opisowi słownemu, a następnie przećwiczenie pracy przez ucznia z omówieniem wszystkich punktów przekazanych przez trenera.
Rys. 2. Krzyw uczenia – jak przyswajamy wiedzę
(źródło)
Taki sposób przekazywania wiedzy jest zbieżny z najbardziej skuteczną metodą prowadzenia instruktażu – TWI Instruowanie Pracowników. Jednak, aby z tej metody korzystać w praktyce, należy opracować standardy pracy w takim podziale, jak opisałem w zasadzie #1. W programie TWI instrukcja jest dla trenera, aby z niej korzystał jak ze ściągi podczas instruktażu. Następnie po instruktażu trafia ona do operatora jako uzupełnienie wiedzy. Nigdy operator nie dostaje instrukcji przed instruktażem. Poza tym, że jest to mało skuteczne, co wspomniałem wcześniej opierając się o wnioski z krzywej uczenia, to może to prowadzić do dwóch innych istotnych problemów:
- Interpretacji instrukcji, która może być różna w zależności od osoby czytającej
- Niezrozumienia słów zapisanych w instrukcji, które w danej firmie są powszechne, ale nie dla nowego pracownika.
Wyobraź sobie, że operator otrzymuje instrukcję AM, w której niefortunnie napisane jest: dolej olej do pełna. Autorowi instrukcji chodziło w tym zapisie, aby dolać do poziomu MAX. Operator może to zinterpretować jako dolanie pod samą „nakrętkę”. Skutki tego mogą być katastrofalne. Dlatego nie warto dawać instrukcji uczniowi przed instruktażem – nigdy!
Zasada #3. Zdjęcia do instrukcji powinny prezentować sposób pracy, a nie efekt
Zdjęcia są nierozłączną częścią najlepszych instrukcji. Tekst w instrukcji jest ważny, bo pełni on ściągę dla trenera podczas instruktażu. Zdjęcia jednak są bardzo pomocne dla ucznia kiedy zostaje po treningu sam na stanowisku pracy. Ludzie są wzrokowcami. Ponad 83% informacji z otoczenia przyjmujemy przez oczy. Warto dodawać zdjęcia do instrukcji, ale kiedy to robimy musimy spełnić jeden warunek: zdjęcia muszą być dobre – odzwierciedlać sposób pracy, a nie efekt.
Z mojego doświadczenia wiem, że wykonanie poprawnych zdjęć do instrukcji to bardzo trudne wyzwanie. Przede wszystkim zdjęcia powinny przedstawiać wskazówki! Zdjęcia mają pokazywać, jak wykonać dany główny krok, a nie – co jest efektem tego kroku. Na hali produkcyjnej, przy tworzeniu instrukcji pracy, czy AM, zauważam często, że ludzie najpierw robią zdjęcia, a potem staraj się do tych zdjęć dorobić treść. Problemem przy takiej sekwencji postępowania jest to, że często w opisie słownym pomijane są istotne wskazówki, których nie udało się uchwycić na zdjęciu. Sekwencja powinna być odwrotna. Najpierw zalecam dwu- albo trzykrotne wykonanie pracy, następnie wypisanie w pracy głównych kroków, potem wyszczególnienie wskazówek i przyczyn występowania wskazówek. Dopiero na końcu powinieneś zastanowić się, jak wypisane wskazówki przedstawić na zdjęciach. Wtedy będziesz w stanie tak przemyśleć zdjęcie, by np. na jednym z nich pokazać dwie albo trzy wskazówki. Ponadto zwracaj uwagę na perspektywę, z której wykonujesz zdjęcie do instrukcji pracy. Robiąc zdjęcie, zwracaj uwagę, aby obraz, który na nim pokazujesz, był odzwierciedleniem tego, co widzi osoba czytająca daną instrukcję. Nie popełniaj błędu, gdzie zdjęcie robisz z wygodnej sobie pozycji. Później czytający nie jest w stanie poprawnie zrozumieć wskazówki pokazywanej na zdjęciu.
I najważniejsza rzecz, esencja tej zasady. Zdjęcia musza obrazować wskazówki (sposób pracy), a nie kroki (metodę pracy). W tym miejscu muszę zaznaczyć, że w 70% audytowanych przeze mnie instrukcji stanowiskowych zdjęcia użyto, aby pokazać kroki w procesie. Takie zdjęcia mają małą wartość. Równie dobrze mogłoby ich nie być. Przecież każdy może zobaczyć efekt końcowy na produkcie finalnym. Kluczem jest uchwycić sposób wykonania pracy, a więc wskazówkę. Dlaczego zatem ludzie robią zdjęcia kroków? Bo takie zdjęcia jest po prostu łatwiej zrobić. Wystarczy podejść i kliknąć zdjęcie. Dobre wykonanie zdjęcia do wskazówki wymaga czasami dużo pracy i wysiłku, aby dobrze pokazać sposób wykonania pracy.
Na Rysunku 3 przedstawiłem instrukcję AM dla operacji biurowej – cotygodniowe czyszczenie ekspresu do kawy. Tą instrukcję wykonałem razem z koleżanką z mojej poprzedniej pracy. Koleżanka ta była odpowiedzialna w systemie 5S za obszar kącika kuchennego, gdzie ekspres się znajdował. Instrukcja ta została przygotowania w oparciu o program TWI i przedstawione tu zasady. Instrukcja ta daje łatwość zrozumienia procesu i możliwość jego szybkiego przypomnienia. To zmotywowało mnie do tego, aby identyczny ekspres zakupić do domu. Kiedy wykonuje jego czyszczenie pierwsze co robię to wyciągam instrukcję i w przeciągu kilkudziesięciu sekund przypominam sobie cały proces.
Rys. 3. Przykład instrukcji AM dla konserwacyjnej obsługi ekspresu do kawy.
Jeżeli zastanawiasz się dlaczego do opisania głównych kroków i wskazówek użyłem maksymalnie 5 słów, a przy opisanych przyczynach jest ich dużo więcej, jeżeli jesteś ciekaw w jaki sposób wyznaczyłem czas oraz przydzieliłem symbolikę, to zachęcam Ciebie do sięgnięcia po książkę, o której wspomniałem wcześniej. Jest tam opisanych 41 zasad tworzenia instrukcji pracy, o których trudno w jednym artykule wspomnieć.
Podsumowanie
Opisane w artykule zasady są fundamentalne przy tworzeniu instrukcji. Nie przypadkowo wybrałem te trzy konkretne. Zazwyczaj to w tych punktach jest popełnianych najwięcej błędów! Doskonale wiadomo, że jeżeli fundament jest zły to i jakość domu niska.
Zapamiętaj, aby nie traktować instrukcji pracy jako zło konieczne. Pamiętaj, że to szansa na zapisanie wiedzy eksperckiej, jaką mają w głowie najbardziej doświadczeni pracownicy – specjaliści UR, liderzy, mistrzowie. Dokumentowanie wiedzy to krok 4. we wdrażaniu AM – początek procesu standaryzacji pracy. Instrukcja jest świetną podstawą pod prowadzenie instruktażu (metoda TWI Instruowanie Pracowników) i szukania usprawnień (metoda 5W1H, która jest elementem kaizen).
Tworzenie instrukcji nie jest prostym procesem, dlatego właśnie opracowałem wspomniane 41 zasad oraz system IT – LeanTrix. Mam nadzieję, że moje doświadczenia zainspirują Ciebie do tworzenia w Twojej firmie doskonałych instrukcji pracy, które zaczną żyć na hali produkcyjnej!
Autor: Dr inż. Bartosz Misiurek
Źródła literaturowe:
Horbal R., Misiurek B., 2009, Lepsza wydajność dzięki szkoleniom stanowiskowym metodą TWI, MM Magazyn Przemysłowy, nr 8/9, s. 44-47
Horbal R., Misiurek B., 2009, Rozwój umiejętności mistrzów i brygadzistów wg metody TWI. Szkolenie podwładnych, Zarządzanie Jakością, nr 1, s. 27-29, s. 31-35
Liker J., Meier D., 2008, Toyota Talent. Rozwijaj swoich pracowników na sposób Toyoty, MT Biznes, Warszawa
Misiurek B., 2016, Standardized Work with TWI: Eliminating Human Errors in Production and Service Processes, Productivity Press, New York
Nakajima S., 1988, Introduction to TPM: total productive maintenance, Productivity Press, New York
Artykuł opublikowany w magazynie Służby Utrzymania Ruchu (Lipiec 2016)
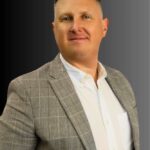
Jestem popularyzatorem Lean Management oraz programu Training Within Industry. Jestem praktykiem. Współtworzę wiele startupów. Od 2015 roku jestem CEO w Leantrix - czołowej firmie z zakresu konsultingu Lean w Polsce, która począwszy od 2024 roku organizuje jedną z największych konferencji poświęconych szczupłemu zarządzaniu w Polsce - Lean TWI Summit. Od 2019 roku jestem CEO w firmie Do Lean IT OU zarejestrowanej w Estonii, która tworzy software etwi.io używany przez kilkadziesiąt firm produkcyjnych i usługowych w Europie i USA.