Każda usterka przeradza się w awarie. Jedyną niewiadomą jest czas. Systemy zgłaszania usterek często przestają działać w firmach głównie przez problemy organizacyjne oraz komunikacyjne. Komunikacja we wdrażaniu systemu Total Productive Maintenance (TPM) jest fundamentem. Mówiąc więcej, w większości firm TPM umiera nie przez brak czasu na konserwacje, zły stan maszyn, czy brak kompetencji wśród pracowników, ale właśnie poprzez problemy komunikacyjne. W TPM podstawowym narzędziem komunikacji pomiędzy pracownikami bezpośrednio produkcyjnymi a pracownikami Utrzymaniu Ruchu jest system zgłaszania problemów i anomalii w pracy maszyny. Jaka jest jego główna rola? Zebranie informacji o problemach w pracy maszyny dostrzeżonych przez operatorów w trakcie pracy na maszynie i efektywne przekazanie ich do mechaników. Kluczem jest słowo „efektywne”, które odrzuca takie przypadki jak przekazanie ustne o problemie, czy telefon do mechanika. Takie sposoby komunikacji w przypadku drobnych problemów są nieefektywne bo mechanicy najzwyczajniej w Świecie o nich zapominają. Nie dzieje się tak dlatego, że nie chcą o nich pamiętać, ale ponieważ mają wiele innych zadań za które są odpowiedzialni – przeglądy, dokumentacja itd. Każdy człowiek ma tendencję do tego, aby skupiać się na dużych problemach, a drobne odrzucać. Odnosząc się na grunt praktyki produkcyjnej, każdy świetnie wie, że przełożony zareaguje wtedy, kiedy będzie duży problem. Drobnym nie ma coś się przejmować. Do czasu…
Seiichi Nakajima, twórca systemu TPM, już kilkadziesiąt lat temu zauważył, że to drobne problemy – zwane usterkami – są faktyczną zmorą wszystkich firm produkcyjnych. W praktyce wszyscy jednak skupiają się wyłącznie nad usuwaniem dużych problemów – awarii. Dlaczego należy zmienić ten paradygmat? Posłużę się przykładem efektu góry lodowej (rys. 1).
Rys. 1. Budowa góry lodowej a usterka/awaria
Wierzchołek góry lodowej, który symbolizuje awarie, łatwo zauważyć podczas podróży statkiem przez ocean. Każdy kapitan okrętu uważa przede wszystkim na to, aby o taki wierzchołek nie zahaczyć. To tak jak na produkcji wypatruje się awarii i reaguje się wtedy, kiedy się pojawi. Większa część góry lodowej, która symbolizuje usterki, ukryta jest jednak pod wodą i niestety każdego dnia jest wypiętrzana na powierzchnię tworząc wierzchołek coraz większym – trudniejszym do ominięcia. Seiichi Nakajima zaproponował, aby przede wszystkim eliminować drobne problemy (usterki) bo to one zawsze są powodem dużych problemów (awarii). Seiichi Nakajima poszedł o krok dalej i powiedział, że nie byłoby awarii gdyby nie było usterek na maszynach. Każda usterka prowadzi do awarii. Jest tylko jedna nie wiadoma: czas. Podążając logiką przyjętą przez Seiichi Nakajimę można wyjść z wnioskiem, że główny cel TPM – zero awarii – jest możliwy tylko wtedy, kiedy na bieżąco będziemy usuwać wszystkie usterki z maszyny. Innym słowem, nie będzie wierzchołka góry lodowej, kiedy pod wodą nie będzie samej góry. To dość logiczne.
System zgłaszania usterek powstał właśnie po to, aby możliwie szybko i efektywnie przekazywać do mechaników dostrzeżone przez operatorów usterki. Celem jest to, aby nigdy nie przerodziły się one w awarie. Podejście to zbieżnie jest z rozwiązywaniem problemów wg Lean Management, gdzie wszystkie działania powinny być zorientowane na eliminację przyczyn źródłowych. W TPM nie chcemy być specjalistami w usuwaniu awarii. TPM to prewencja.
Obecnie w polskim przemyśle co raz więcej firm wdraża TPM tworząc przy tym najróżniejsze systemy zgłaszania usterek. Przez 9-lat mojej praktyki przy wdrażaniu TPM w ponad 80 fabrykach widziałem najróżniejsze systemy zgłaszania usterek. Od elektronicznych po papierowe. Od szaroburych po tryskających różnymi kolorami. Jednak nie forma jest najważniejsza. Nie zależnie jaka ona by była i tak najczęściej proszony byłem o pomoc przy reaktywacji systemu. Pracowałem dla firm, które swój system zgłaszania usterek reaktywowały nawet 5-krotnie przyjmując za każdym razem inną formę jego budowy i za każdym razem osiągając ten sam efekt. Albert Einstein powiedział kiedyś, że: „Szaleństwem jest robić wciąż to samo i oczekiwać różnych rezultatów”. Wdrożenie systemu zgłaszania usterek wymaga zmiany myślenia. Zdałem sobie sprawę, że każda z tych firm, dla których pracowałem, tworząc swój system zgłaszania usterek nie przestrzegała fundamentalnych zasad. W tym artykule chciałbym przedstawić Ci 5, a w praktyce 6, najważniejszych z nich. Pomogą Ci one opracować taki system zgłaszania usterek, który będzie funkcjonował w praktyce i przysporzy się do redukcji liczby awarii w Twojej firmie. Nie ważne przy tym jaką formę budowy systemu wybierzesz.
Zasada #0. Wytłumacz pracownikom różnicę: usterka vs awaria
Z premedytacją nadałem tej zasadzie numer zero. Kiedy jestem proszony o reaktywację systemu zgłaszania usterek, który działa w firmie od wielu lat, pierwsze co robię to idę na Gembe. Tam operatorom zadaje proste pytanie: co to jest usterka? Niestety najczęściej nie uzyskuję odpowiedzi. Oczywiście pojęcie awarii nie jest im obce. Na jednym wydechu potrafią wymienić mi 5 ostatnich. Zanim zaczniesz tworzyć w firmie system zgłaszania usterek to wytłumacz ludziom czym jest usterka! Bardzo pomocne w tym temacie jest przygotowanie katalogu usterek. To zebrane usterki z przykładami przedstawionymi na zdjęciu. Jeszcze lepiej jest opisać jak ta usterka może wpłynąć na powstanie awarii i jak może się objawiać. Przykład katalogu usterek możesz zobaczyć w Tabeli 1. Odniosłem się w nim do eksploatacji samochodów, która wszystkim nam jest bliska.
Tabela 1. Fragment katalogu usterek przy eksploatacji samochodu
Źródło: Opracowanie własne na podstawie: Świat Motoryzacji nr 12/2007, s.10-11
Usterka |
Przykład | Jak usterka może doprowadzić do awarii | Objawy usterki |
Uszkodzone przewodów zapłonowe | ![]() |
Uszkodzenia przewodów to duży problem bo to od nich w dużej mierze zależy siła iskier przeskakujących między elektrodami świec zapłonowych, co z kolei ma podstawowy wpływ na pewność zapłonu mieszanki paliwowo-powietrznej, a tym samym na pracę silnika. |
· Przerywana praca silnika · Skoki prędkości obrotowej · Trudność w uruchomieniu silniku w wilgotny dzień · Iskrzenie |
Katalog usterek jest więc nie tylko zobrazowaniem dla operatora najczęściej identyfikowanych problemów na maszynie. To również olbrzymie źródło informacji. Jednym z głównych celów TPM jest przecież budowanie świadomości wśród pracowników bezpośrednio produkcyjnych. Proces ten następuje, kiedy ludzie poznają konsekwencję. Naucz pracowników czym są usterki zanim zaczniesz wdrażać system, który będzie je zbierał i przekazywał informację o nich do mechaników.
Zasada #1. Odseparuj system zgłaszania usterek od systemu zgłaszania awarii
W większości firm, które prosiły mnie o pomoc przy reaktywacji systemu zgłaszania usterek, największym problemem było to, że usterki i awarie zgłaszane były na tym samym druczku, czy to papierowym, czy elektronicznym. Statystyki w tych firmach zawsze były zbliżone. Średnio na 10 zgłoszonych awarii zgłaszana była jedna usterka. To tak jakby na oceanie było 10 różnych wierzchołków gór, a tylko jedna góra. To absurd! Oczywiście proporcja powinna być w tym przypadku zupełnie odwrotna. To średnio na około 50 usterek przypadać powinna 1 awaria! Piszę to na bazie moich doświadczeń. Jeżeli system dedykowany jest do zbierania awarii i usterek to ludzie zawsze i mimo wolnie wpisywać będą tylko awarie. Tak się dzieje i już. Musisz wyznaczyć w swojej firmie dedykowany system zgłaszania usterek jeżeli chcesz, aby ludzie z niego korzystali. Nie ma na to innego rozwiązania.
Zasada #2. System powinien być dostosowany do specyfiki obszaru produkcyjnego, a nie ujednolicony dla całej fabryki
Z pewnością w swojej firmie masz różne procesy. Być może masz obszar wytłaczania, gdzie dominują maszyny, a tuż za drogą transportową obszar montażu, gdzie raczej występuje praca ręczna i drobne narzędzia. Na obu obszarach z pewnością występują usterki. Z tymże system ich zgłaszania powinien być zupełnie inny. W obszarze montażu, gdzie występuje kilkadziesiąt stanowisk, system zgłaszania usterek może być zobrazowany na Lay-Oucie, gdzie operator może przyczepić czerwony „Tag” przy szkicu danego stanowiska. Do numeru „Tag-a” może być w kuwecie przypisana karta usterki z dokładnym opisem problemu. Mechanicy dzięki temu w ciągu kilkudziesięciu sekund, patrząc na lay-out obszaru, będą widzieć wszystkie zgłoszone usterki. W obszarze wytłaczania może lepiej sprawdzić się system kartkowy, w którym po wypisaniu karty usterki operator przyczepi ją bezpośrednio do maszyny w miejscu, gdzie problem występuję. Jak wspomniałem, form budowy systemów zgłaszania usterek może być naprawdę wiele. Jedna co najważniejsze płynie z tej zasady: system zawsze powinien być dostosowany do obszaru produkcyjnego, a nie całej firmy.
Zasada #3. System zgłaszania usterek powinni tworzyć wspólnie operatorzy i mechanicy
Ta zasada jest ściśle połączona z zasadą nr 2. Jeżeli podzielisz firmę na kilka obszarów i zdecydujesz, że każdy z nich powinien mieć swój dedykowany system zgłaszania usterek, to wówczas powinieneś zebrać doświadczonych operatorów z tego obszaru oraz mechaników i dać im zadanie: przygotujcie system, który będzie pomagał Wam się komunikować. W tym kroku ważne jest pokazanie kilku przykładów systemów już funkcjonujących jako inspiracja. Twoja rola sprowadzać się będzie do moderowania dyskusji. Z moich doświadczeń wynika, że opracowanie samego projektu systemu zgłaszania usterek przez operatorów i mechaników zajmuje nawet 4 godziny! Pamiętaj, że każda z tych grup ma swoje własne cele i oczekiwania. Na przykład operatorom zależy aby system był blisko ich stanowisk, a mechanikom, aby oni mieli jak najmniejszy dystans do pokonania. Dyskusja miedzy tymi dwoma grupami może być zażarta, ale jeżeli ich zaangażujesz to istnieje naprawdę duża szansa, że system będzie działać po wdrożeniu.
Zasada #4. Jeżeli chcesz mieć system elektroniczny to najpierw wykonaj system papierowy
Nie wystarczyłoby mi palców u rąk aby policzyć ile firm cofało się przy reaktywacji systemu zgłaszania usterek z formy elektronicznej na papierową. Na rynku są dostępne systemy zgłaszania usterek w formie elektronicznej, ale zazwyczaj są one powiązane z systemami zgłaszania awarii (patrz zasada #1). Firmy IT chcą być kompleksowe. Niestety nie rozumieją one istoty TPM. To co ja polecam to przećwiczenie sposobu funkcjonowania systemu zgłaszania usterek na formie papierowej. Nie koniecznie myślę tutaj o kartkach papieru. Można zastosować tablice magnetyczne, lay-outy maszyny itd. Ważne jest, aby system powstał przy wykorzystaniu obecnych materiałów i żeby dawał się łatwo zmienić i dostosować. Na rysunku 2 zaprezentowałem system zgłaszania usterek jaki wspomagałem tworzyć w firmie LG Display Poland sp. z o.o.. To wersja nr 3. Wersje nr 1 i 2 wiele się nie różniły, a zmiany wynikały głównie z poprawek wynikających z praktyki.
Rys. 2. System zgłaszania usterek z firmy LG Display Poland sp. z o.o.
Źródło: Wolak M., Kotlarski B., Maczuga M., 2014, 5S Fundamentem Trwałego Systemu TPM, Materiały Konferencyjne do XIV Konferencja Lean Management, Wrocław
O ile łatwiejsza i mniej czasochłonna jest drobna zmiana w systemie papierowym, niż komputerowym. To nie ulega wątpliwości. Dlatego na początku polecam zdobyć jak najwięcej doświadczenia w tworzeniu systemu zgłaszania usterek, a dopiero potem tworzyć wersje elektroniczne. Tworzenia systemu zgłaszania usterek to ciągła nauka i wymiana doświadczeń. Trzeba być w tym temacie bardzo elastycznym.
Zasada #5. System zgłaszania usterek powinien być „Lean”
Co oznacza sformułowanie „Lean”? Z angielskiego znaczy to „szczupłe”, ale często tłumaczone jest jako „sprytne”, „łatwe”, czy „proste” . System zgłaszania usterek właśnie taki powinien być. Chciałbym podać Tobie kilka reguł, które zacznę od słowa:
Im…
• więcej sterowania wizualnego
• mniej wypisywana treści
• bliżej do stanowiska pracy
• prostszy w obsłudze
• ….
….tym lepiej!
Jeżeli system zgłaszania usterek w firmie tworzą wyłącznie mechanicy to bardzo często system ten jest naładowany rozwiązaniami technicznymi, które natychmiastowo odrażają operatorów. Wymyślne opisy w kartach, skomplikowany proces decyzyjny, czy trudne słowa powodują, że operatorzy nie mają najmniejszych ochoty korzystać z systemu. Oczywiście w zasadzie #3 wspomniałem, że system zgłaszania usterek powinni tworzyć operatorzy i mechanicy. To gwarantuje, że już na poziomie projektu system będzie „lean”.
Podsumowanie
System zgłaszania usterek to konieczności przy skutecznym wdrażaniu TPM. Im mniej usterek tym mniej awarii. To prawda, z którą trudno dyskutować. Jeżeli jeszcze nie przekonałeś się, czy to co napisałem jest prawdą, pójdź na swój obszar produkcyjny i sprawdź jaki jest stosunek liczby zgłoszonych awarii do liczby zgłoszonych usterek. Sprawdź przy tym kto zgłasza usterki. Jeżeli przy tworzeniu systemu zgłaszania usterek nie trzymałeś się tych fundamentalnych zasad to mogę przypuszczać, że jest u Ciebie zgłoszonych więcej awarii niż usterek, a usterki jeżeli już są zapisane to raczej przez mechaników niż operatorów. Idź również do operatora na Gembe i zrób wywiad. Zapytaj czy wie on co to jest usterka? Operatorzy są skarbnicą wiedzy o problemach. Największym marnotrawstwem jest nie korzystanie z tej wiedzy. To 8. typ marnotrawstwa: utracona kreatywność.
Autor: dr inż. Bartosz Misiurek
Artykuł opublikowany w magazynie Służby Utrzymania Ruchu (nr 4/2016).
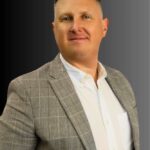
Jestem popularyzatorem Lean Management oraz programu Training Within Industry. Jestem praktykiem. Współtworzę wiele startupów. Od 2015 roku jestem CEO w Leantrix - czołowej firmie z zakresu konsultingu Lean w Polsce, która począwszy od 2024 roku organizuje jedną z największych konferencji poświęconych szczupłemu zarządzaniu w Polsce - Lean TWI Summit. Od 2019 roku jestem CEO w firmie Do Lean IT OU zarejestrowanej w Estonii, która tworzy software etwi.io używany przez kilkadziesiąt firm produkcyjnych i usługowych w Europie i USA.