TWI w Cooper Standard to case study opublikowane w 2018 roku, na początku procesu wdrażania programu Training WIthin Industry. Na rok 2024, Cooper Standard ma wdrożony program TWI globalnie. Cooper Standard jest wiodącym globalnym dostawcą systemów i komponentów dla przemysłu motoryzacyjnego. Produkty obejmują uszczelki gumowe i plastikowe, linie paliwowe i hamulcowe, przewody do transferu płynów oraz systemy tłumienia drgań. Cooper Standard zatrudnia ponad 30 000 osób na całym świecie i działa w 20 krajach (Rysunek 1).
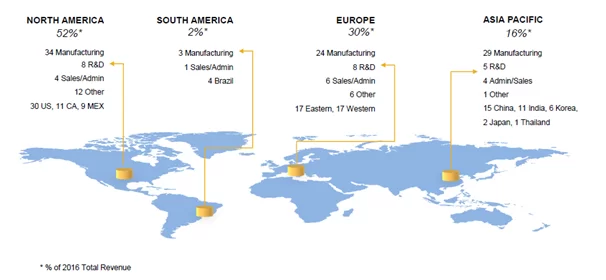
Zakłady Cooper Standard
Rys. 1. Globalna lokalizacja zakładów
Źródło: Strona internetowa: http://www.cooperstandard.com/
Cooper Standard przyspiesza przełomowe postępy w nauce o materiałach, aby tworzyć ekologiczne rozwiązania oraz komponenty motoryzacyjne, które redukują wagę, obniżają emisje, poprawiają design i zwiększają wydajność pojazdów dla swoich klientów.
Jako wiodący globalny dostawca systemów i komponentów dla przemysłu motoryzacyjnego, Cooper Standard zajmuje następujące pozycje na rynku:
- Wiodący globalny dostawca systemów uszczelniających;
- Drugi co do wielkości globalny dostawca systemów dostarczania paliwa i hamulców;
- Trzeci co do wielkości dostawca systemów przesyłu płynów;
- Lider na rynku północnoamerykańskim w zakresie systemów tłumienia drgań.
W 2013 roku Cooper Standard wdrożył Strategię Zyskownego Wzrostu, aby dostarczyć jasną wizję, zestaw wartości i strategię osiągnięcia misji, jaką jest stanie się jednym z 30 największych globalnych dostawców motoryzacyjnych pod względem sprzedaży oraz jednym z 5 najlepszych pod względem ROIC (zwrotu z zainwestowanego kapitału). Od tego czasu, globalny zespół liderów rozwinął i udoskonalił strategię, aby lepiej odzwierciedlała kulturę firmy i dostarczała ścieżkę dla dalszego wzrostu, napędzanego przez kulturę firmy, innowacje i wyniki (Rysunek 2).
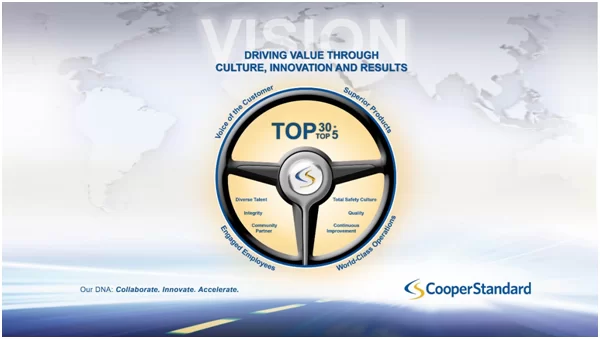
Wizja Cooper Standar
Rys. 2. Wizja Cooper Standard Automotive
Źródło: Strona internetowa: http://www.cooperstandard.com/
Strategia wdrażania filozofii ciągłego doskonalenia w Cooper Standard Automotive Europe
Organizacje, które korzystają z narzędzi Lean lub systemów Lean Manufacturing, często rozpoczynają od wdrażania pojedynczych rozwiązań, zapominając o jednym bardzo ważnym elemencie – planowaniu skutecznej strategii. Strategia wyraża długoterminowe cele organizacji, które są zgodne z głównymi kierunkami działalności i pozwala na efektywną alokację zasobów potrzebnych do osiągnięcia pożądanych efektów. Dobrze zaplanowana strategia może znacznie poprawić efektywność i szybkość zmian organizacyjnych wdrażanych w ramach zarządzania Lean, co pozwala w pełni wykorzystać efekt synergii pomiędzy wybranymi komponentami. Warunkiem tego jest odpowiednie zaplanowanie i przeprowadzenie strategii.
Bardzo ważnym krokiem w efektywnym wdrażaniu strategii ciągłego doskonalenia jest przygotowanie KPI (kluczowych wskaźników wydajności). Ważne jest zrozumienie, że KPI nie są tylko wskaźnikami obejmującymi całą firmę, ale mogą koncentrować się na efektywności działania poszczególnych części firmy, które mogą być następnie powiązane z tym, jak te części wpływają na całość. Śledzenie KPI pokazuje nie tylko, jak działy współpracują, aby osiągnąć cele, ale także jak poszczególne osoby w każdym dziale mogą przyczynić się do sukcesu organizacji. Celem KPI jest związanie wszystkich w organizacji z jednym wspólnym celem. Jest to bardzo ważne dla naszej organizacji.
Jednak zanim rozpocznie się jakiekolwiek działania, obecny stan organizacji powinien być dobrze zdefiniowany poprzez odpowiedź na następujące dwa pytania:
- Kto stanowi zespół w dziale, fabryce, dywizji, a nawet w całej korporacji?
- Na jakim poziomie zarządzania Lean znajduje się obecnie organizacja?
Pierwsze pytanie, dotyczące składu zespołu, jest szczególnie ważne w przypadku firm, które dopiero rozpoczynają swoją przygodę z filozofią ciągłego doskonalenia. Jednakże nie oznacza to, że nie dotyczy ono firm bardziej zaawansowanych w Lean. Ogólnie każdy zespół można podzielić na liderów zmian (około 10%), osoby, które dostosują się do zmian (około 80%) oraz przeciwników zmian (pozostałe 10%), których podstawowym argumentem jest to, że zawsze pracowali w taki sposób i nie widzą potrzeby zmieniania czegokolwiek (Rysunek 3) [Prasał 2016]. Dla każdej struktury organizacyjnej kluczowe są dwie grupy: koordynatorzy zmian oraz kadra zarządzająca. To od ich aktywnej postawy zależy sukces zarządzania Lean oraz efektywność każdego podjętego kroku, w tym aktywne promowanie kultury ciągłego doskonalenia.
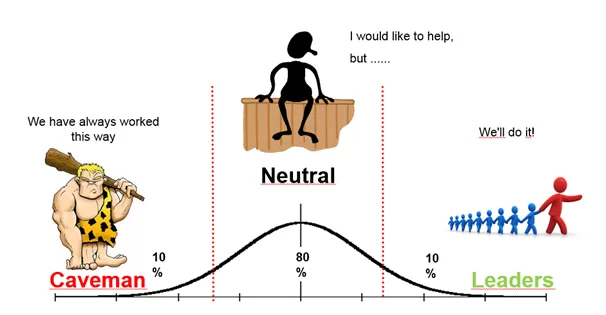
Struktura zespołu
Rys. 3. Struktura zespołu
Przy odpowiedzi na drugie pytanie należy wyróżnić trzy poziomy zarządzania Lean (Rysunek 4). Pierwszy poziom, tzw. poziom narzędzi, charakteryzuje głównie organizacje, które dopiero zaczynają swoją przygodę z optymalizacją procesów. Są to czasem organizacje, które traktują ciągłe doskonalenie jako program oszczędnościowy. Takie podejście w bardzo ograniczonym stopniu wykorzystuje możliwości zarządzania Lean. Jednak po początkowych sukcesach, zazwyczaj trudno jest ustabilizować i utrzymać podejście ciągłego doskonalenia przez dłuższy czas.
Drugi poziom można zaobserwować w firmach, które systematycznie zajmują się zagadnieniami Lean i są świadome, że dzięki takiemu podejściu można osiągnąć synergię, która wynika z kompleksowego wdrożenia wielu narzędzi Lean Manufacturing. Najwyższy poziom w obszarze Kaizen osiągają organizacje, dla których zarządzanie Lean stało się sposobem prowadzenia działalności gospodarczej. Pracownicy tych firm traktują poszczególne narzędzia i ciągłe doskonalenie jako naturalny sposób pracy. Na rynku dostępnych jest wiele rozwiązań umożliwiających określenie poziomu organizacji. Niektóre firmy mają wewnętrzne audyty, które są bardzo pomocne i stanowią część samego systemu. Zrozumienie celu nie jest tak istotne, jak zrozumienie punktu wyjścia, ponieważ to właśnie tam zaczyna się podróż.
Rys. 4. Trzy poziomy zarządzania Lean
Źródło: Prasał 2016
Cooper Standard Corporation rozwija narzędzia i systemy ciągłego doskonalenia w konkretnych lokalizacjach od wielu lat. Na podstawie tych praktyk oraz dostrzegając potencjał wymiany pomiędzy zakładami, opracowano jeden system World Class Operation (WCO), wspólny dla wszystkich lokalizacji. Stał się on integralną częścią kultury i wizji firmy, która nieustannie dąży do doskonałości.
Ocena WCO stała się narzędziem wspierającym rozwój systemu oraz umożliwiającym mierzenie postępów każdej lokalizacji. Jest to forma audytu zarządzania Lean, podzielona na 10 rozdziałów, z których każdy pozwala zmierzyć jedno narzędzie (Rysunek 5). Cała ocena WCO składa się ze 150 pytań – po 15 na każdy rozdział (na każde pytanie należy odpowiedzieć „Tak” lub „Nie”).
Rys. 5. Ocena World Class Operation
Na podstawie wyników audytu z 2016 roku (Rysunek 6) oraz uwzględniając opinie ze wszystkich lokalizacji w Europie, zespół ds. ciągłego doskonalenia przedstawił strategię krótkoterminową i długoterminową.
Rys. 6. Ocena WCO z 2016 roku
Wyróżniono cztery obszary, którymi CSA Europe chciałoby zająć się w pierwszej kolejności:
- Dalszy rozwój oceny WCO (tzw. ocena WCO 2.0),
- Mapowanie strumienia wartości (Value Stream Mapping),
- Całkowite Utrzymanie Ruchu (Total Productive Maintenance),
- Standaryzacja oparta na wymianie najlepszych praktyk.
Dalszy rozwój oceny WCO
Widząc korzyści i potencjał kompleksowego podejścia Lean Management, CSA Europe zdecydowało się dokładniej opisać wymagania i kryteria każdego narzędzia Lean. Celem jest stworzenie lub zaktualizowanie oceny WCO, co wzmocni i przyspieszy wdrożenie kultury Lean w organizacji. Kolejnym etapem będzie wprowadzenie niezależnej grupy audytorów (nie związanych z fabryką), którzy zapewnią obiektywną ocenę, co z kolei poprawi możliwość porównania narzędzi w poszczególnych zakładach oraz ułatwi identyfikację i wymianę najlepszych praktyk.
Mapowanie strumienia wartości
CSA Europe uznało także za kluczowe poprawę w obszarze Mapowania Strumienia Wartości. Korzyści wynikające z prawidłowego zastosowania tego narzędzia to m.in.:
- Wizualizacja przepływu informacji, procesów i materiałów na jednym arkuszu,
- Wsparcie w definiowaniu priorytetów ciągłego doskonalenia,
- Projektowanie przyszłego stanu,
- Redukcja zapasów (uwolnienie kapitału),
- Skrócenie czasu realizacji (Lead Time),
- Eliminacja marnotrawstwa (8 strat),
- Redukcja kosztów,
- Spełnienie wymagań systemu CSA – World Class Operation.
TPM i Utrzymanie Ruchu
Kolejnym obszarem wybranym jako priorytet w dziedzinie ciągłego doskonalenia jest Całkowite Utrzymanie Ruchu (TPM). Ogromny potencjał dostrzeżono w rozwijaniu podejścia do autonomicznego utrzymania ruchu. Główne cele rozwoju tego programu to:
- Opracowanie najlepszego globalnego standardu opartego na najlepszych praktykach z poszczególnych zakładów,
- Poprawa wskaźników wydajności (KPI),
- Zwiększenie zaangażowania pracowników bezpośredniej produkcji,
- Spełnienie wymagań systemu CSA – World Class Operation.
Standaryzacja (globalna)
Standaryzacja narzędzi Lean Management jest realizowana w przypadku trzech wyżej wymienionych narzędzi. Dodatkowym elementem wspierającym ten proces jest tworzenie globalnych materiałów szkoleniowych – Akademia WCO. Tak jak w przypadku jednego zakładu, pierwszym krokiem dalszego doskonalenia w całej korporacji jest stworzenie i określenie wspólnego standardu opartego na wiedzy i doświadczeniu każdego pracownika.
System BTO – część operacji World-Class (WCO) i wdrożenie TWI w Cooper Standard
System „Budowanie Utalentowanej Organizacji” (BTO) to inicjatywa rozwijająca umiejętności doświadczonych pracowników w zakresie efektywnego przekazywania wiedzy (szkolenie pracowników). Podstawą systemu BTO jest program Training Within Industry (TWI), a konkretnie jedna z jego metod – TWI JI (Job Instruction, czyli Instruktaż Stanowiskowy) (Rysunek 7).

Buliding Talented Organization
Rys. 8. System BTO i program TWI
Program TWI jest niezbędny do wdrażania standaryzacji pracy, która nie sprowadza się tylko do tworzenia instrukcji pracy, ale przede wszystkim do umiejętności korzystania z nich podczas szkolenia pracowników i doskonalenia metod pracy Kaizen. System BTO jest obecnie 11. filarem systemu WCO w europejskim oddziale naszej organizacji.
Metoda TWI JI jako kluczowa część systemu BTO
Metoda TWI JI jest zorientowana na efektywny sposób wprowadzenia pracowników do pracy. Jednym z mitów na temat tej metody jest to, że skraca ona czas szkolenia. To nieprawda. Metoda TWI JI skraca czas wdrożenia pracownika do pracy – czyli czas, w którym pracownik osiąga pełną efektywność. Nie jest to tożsame z samym szkoleniem. Metoda TWI JI kładzie również nacisk na świadome wykonywanie pracy przez pracownika. Dlatego w tej metodzie tak dużą wagę przykłada się do wyjaśniania powodów kluczowych punktów pracy.
Głównym celem metody TWI JI jest nauczenie doświadczonych pracowników, jak przekazywać swoją wiedzę i doświadczenie mniej wykwalifikowanym operatorom. Kluczowym elementem szkolenia jest odpowiednie przygotowanie dokumentacji. W naszej organizacji, w obszarach objętych systemem BTO, dokumentacja jest przygotowywana przez inżynierów we współpracy z doświadczonymi operatorami i liderami. Dzięki temu istnieje pewność, że instrukcje pracy zawierają triki i ułatwienia, które skracają czas wdrożenia pracowników do pełnej wydajności pracy. W systemie BTO istnieją dwa rodzaje dokumentacji opisującej pracę operatorów:
- Karty Podziału Pracy (JBS – Job Breakdown Sheets),
- Standardowe Instrukcje Pracy (WI – Work Instructions).
Karta Podziału Pracy (JBS) to narzędzie dla instruktora prowadzącego szkolenie. Zawiera główne kroki, kluczowe punkty i powody kluczowych punktów (Rysunek 9).
Rys. 9. Tworzenie karty podziału pracy w metodzie TWI JI
Źródło: Misiurek 2016
Standardowa Instrukcja Pracy (WI) to dokument dla uczącego się pracownika po zakończeniu szkolenia. W porównaniu do JBS, WI jest wzbogacona o zdjęcia, symbole i objaśnienia, takie jak cechy szczególne.
WI jest przygotowywana dla każdej referencji. JBS jest głównym dokumentem, który prowadzi instruktora przez szkolenie. Kluczowe punkty z JBS odnoszą się do konkretnych referencji w WI. Używając przykładu domowego, można powiedzieć, że istnieje jedna główna JBS dla procesu prania, w której nie ma szczegółowych danych, takich jak wybrana temperatura czy prędkość obrotów pralki. Każdy rodzaj prania (np. białe delikatne tkaniny, odzież robocza) ma swoje WI, z określoną temperaturą prania. Podczas szkolenia zgodnie z metodą TWI JI, instruktor używa głównej JBS oraz WI dla konkretnej referencji. Dzięki temu podejściu dokumenty opisujące pracę stały się podstawą szkoleń na stanowisku pracy oraz pomocą dla uczniów po szkoleniu.
Szkolenia wewnętrzne są nieodzownym etapem we wdrażaniu metody TWI JI. W ich trakcie pracownicy uczą się, jak tworzyć poprawną dokumentację. Jest to spore wyzwanie, ponieważ tworzenie standardów zgodnie z TWI nie jest prostym procesem. Wymaga dostosowania się do wielu zasad i reguł, które są nieintuicyjne dla osób codziennie sporządzających instrukcje. Wypełnienie formularza WI i napisanie poprawnej WI to dwie różne rzeczy, co nasi instruktorzy i inżynierowie już doświadczyli.
Wdrożenie systemu BTO w Cooper Standard Automotive (Oddział Europejski)
Wdrożenie systemu BTO w europejskim oddziale naszej organizacji zostało podzielone na trzy fazy (Tabela 1). Obecnie realizowana jest tzw. druga fala wdrożenia, która obejmuje:
- Nowe projekty;
- Projekty krytyczne (np. ważne pod względem jakości i bezpieczeństwa);
- Komórki Diamentowe (Diamond Cells).
Tab. 1. Trzy fazy wdrożenia systemu BTO w Cooper Standard (Oddział Europejski)
Faza wdrożenia | Czas realizacji | Opis fazy |
---|---|---|
Wdrożenie pilotażowe w 4 zakładach | Marzec 2016 – Czerwiec 2016 | Projekt pilotażowy obejmował cztery zakłady – z Polski, Niemiec, Francji i Włoch. W każdym zakładzie wybrano jeden obszar pilotażowy. Wszyscy menedżerowie i pracownicy z obszaru pilotażowego zostali przeszkoleni w metodzie TWI JI. Po szkoleniu każdy zakład przeszedł audyt i sesję Follow Up prowadzoną przez TWI Lead Coach Europe. Celem tej sesji było zweryfikowanie dokumentacji i umiejętności instruktorów w zakresie korzystania z metody TWI JI. Następnie przeprowadzono szkolenia na stanowisku pracy i zmierzono efekty. Cała faza zakończyła się wspólnym spotkaniem przedstawicieli czterech zakładów, wymianą doświadczeń i zapisaniem rekomendacji dla innych zakładów dotyczących wprowadzania systemu BTO w pierwszej fali wdrożenia. Dodatkowo wybrano 6 osób z czterech krajów, które przeszły szkolenie na wewnętrznych trenerów TWI. |
Pierwsza fala wdrożenia we wszystkich zakładach | Lipiec 2016 – Grudzień 2016 | Pierwsza fala wdrożenia opierała się na rekomendacjach zakładów biorących udział w pilotażu. Każdy europejski oddział Cooper Standard miał za zadanie wybrać obszar pilotażowy, w którym wdrożona zostanie metoda TWI JI. Szkolenia i sesje Follow Up były głównie prowadzone przez wewnętrznych trenerów. |
Druga fala wdrożenia we wszystkich zakładach | Styczeń 2017 – do teraz | Druga fala wdrożenia skupia się na wszystkich nowych projektach uruchamianych w europejskiej dywizji Cooper Standard. Dodatkowo, system BTO i program TWI obejmą wszystkie Komórki Diamentowe. |
Wdrożenie systemu BTO w europejskiej dywizji Cooper Standard przebiega metodycznie. Wiemy, że zmiana sposobu szkolenia pracowników i tworzenia dokumentacji w firmie to trudne wyzwanie. Wymaga to czasu i zrozumienia. Dzięki takiemu podejściu osiągnięto bardzo dobre wyniki. Wszystkie zakłady, które brały udział we wdrożeniu programu TWI w ramach tzw. pierwszej fali, zwiększyły produktywność pracy średnio o 17,55%, a poziom defektów został zredukowany średnio o 35,83%.
Bardzo ważną częścią systemu BTO jest raportowanie. Oddziały europejskie są zobowiązane do cotygodniowego składania raportu z wdrożenia systemu BTO. Raport definiuje stan wdrożenia i zapisuje wszystkie „Lessons Learned” z danego tygodnia.
Obecnie jesteśmy w trakcie szkolenia naszych wewnętrznych trenerów BTO. Każdy zakład ma co najmniej jedną osobę pełniącą funkcję trenera BTO w zakładzie. Docelowo ci trenerzy będą odpowiedzialni za utrzymanie systemu BTO na poziomie zakładowym.
Podsumowanie – TWI w Cooper Standard
CSA Europe zidentyfikowała szczegółowe działania w obszarze ciągłego doskonalenia na kolejne lata (Rysunek 10), aby móc działać długoterminowo.
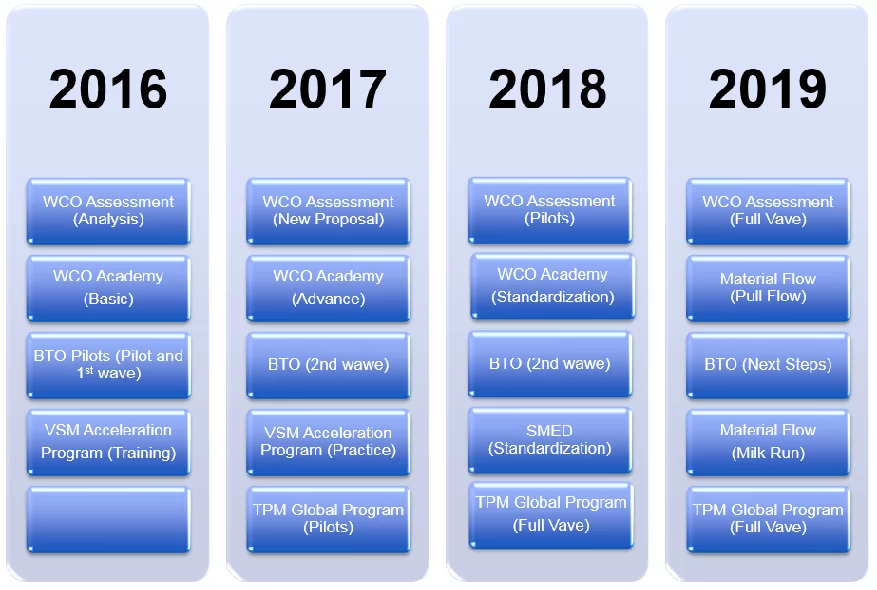
TWI w Cooper Standard
Rys. 10. Strategia na lata 2016–2019
Organizacja wierzy, że działania prowadzone w sposób systematyczny i uporządkowany przynoszą długotrwałe rezultaty i pozwalają na skuteczne konkurowanie z innymi graczami na rynku.
Literatura:
- Strona internetowa: http://cooperstandard.com/ [8 kwietnia 2017]
- Misiurek B., 2016, Standardized Work with TWI: Eliminating Human Errors in Production and Service Processes, Productivity Press, Nowy Jork
- Prasał M., 2016, Masa krytyczna, Czasopismo Kaizen, 3/2016
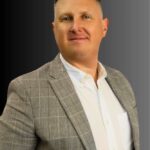
Jestem popularyzatorem Lean Management oraz programu Training Within Industry. Jestem praktykiem. Współtworzę wiele startupów. Od 2015 roku jestem CEO w Leantrix - czołowej firmie z zakresu konsultingu Lean w Polsce, która począwszy od 2024 roku organizuje jedną z największych konferencji poświęconych szczupłemu zarządzaniu w Polsce - Lean TWI Summit. Od 2019 roku jestem CEO w firmie Do Lean IT OU zarejestrowanej w Estonii, która tworzy software etwi.io używany przez kilkadziesiąt firm produkcyjnych i usługowych w Europie i USA.