Kluczem do wysokiej jakości i efektywnej pracy na stanowiskach jest standaryzacja pracy, która stanowi fundament podejścia Lean management. Szczupłe zarządzanie okazuję się być bardzo popularne w fabrykach produkcyjnych, jednak standaryzacja pracy jest często zapomina. Standaryzacja pracy najskuteczniej realizowana jest poprzez Training Within Industry.
Program TWI powstał w latach 40 ubiegłego wieku w odpowiedzi na konieczność wyszkolenia wielu niedoświadczonych pracowników, którzy mieli utrzymać jakość i efektywność produkcji zbrojeń w czasach II wojny światowej. W tamtych latach nie było mowy o automatyzacji, większość operacji produkcyjnych była manualna. Training Within Industry znakomicie rozwiązywał problem z wdrażaniem i rozwojem nowych pracowników na stanowiskach wymagających takich zdolności. Zdecydowana większość firm objętych rządowym programem wdrożenia TWI odnotowała ponad 25% wzrost wydajności, każda z nich zredukowała czas szkolenia pracownika o ponad 1/4. Po dziś TWI jest nieocenione przy wdrażaniu pracowników do wykonywania operacji krótkich i powtarzalnych. W obecnych fabrykach zaczyna dominować automatyzacja. Pozwala ona przenieść ciężką fizyczną pracę na maszyny tym samym odciążyć pracowników produkcyjnych. Rola operatorów ogranicza się do reagowania na problemy przy maszynie, przeprowadzanie przezbrojeń oraz dokonywanie konserwacji. Charakter umiejętności wymaganych na stanowisku pracy znacząco się zmienił, coraz większy nacisk kładzie się na rozwój świadomego pracownika. Jego głównym zadaniem jest zapewnienie ciągłości produkcji poprzez umiejętności poparte wiedzą i doświadczeniem. W tym miejscu pojawia się pytanie czy TWI jest tak samo skuteczne w środowisku zautomatyzowanym co w przypadku prac manualnych?
Standaryzacja procesów zautomatyzowanych krok po kroku
Przez wiele firm standaryzacja procesów zautomatyzowanych odkładana jest na boczne tory. Przyczyną, dla której tak się dzieje jest fakt, że są one specyficzne i trudne, ponieważ potrzeba wiedzy, doświadczenia i wysiłku, aby umiejętnie określić sposoby reagowania na awarię, czy też czy przebieg przezbrojenia. Bazując na naszych doświadczeniach z ponad 150 fabryk produkcyjnych na całym świecie, opracowaliśmy sposób standaryzowania procesów zautomatyzowanych, który zawarty jest w siedmiu głównych krokach. Jego skuteczność potwierdzona jest licznymi wdrożeniami w branży automotive, lecz z równie dużym powodzeniem może być on stosowany we wielu innych branżach. Cały schemat postępowania został umieszczony na Arkuszu Podziału Pracy wraz z wskazówkami i przyczynami.
Główne kroki | Wskazówki | Przyczyny |
---|---|---|
1. Wypisz maszyny i wyposażenie linii |
|
|
2. Pogrupuj maszyny i wyposażenie w obszary |
|
|
3. Wypisz operacje na linii |
|
|
4. Przygotuj Skill Matrix |
|
|
5. Określ priorytety dla rozwoju pracowników |
|
|
6. Przygotuj Instrukcje Pracy Standaryzowanej TWI |
|
|
7. Przeprowadź instruktaże na produkcji |
|
|
Krok 1: Wypisz wszystkie maszyny i wyposażenie linii
Standaryzacja pracy w pierwszy etapie skupia się na zdefiniowaniu zasobów produkcyjnych, które biorą udział w procesie. Każda lina zbudowana jest wielu różnych maszyn i elementów wyposażenia. Bardzo ważne, aby spis tych rzeczy przeprowadzany był bezpośrednio na stanowisku pracy. Będziemy mieli wówczas pewność, że do dalszej pracy przystępujemy z pełnymi informacjami dotyczącymi maszyn i urządzeń. Należy również zauważyć różnicę między maszyną (np. wytłaczarka), a wyposażeniem linii (np. podajnik), lecz traktować je jako integralne części całej linii. We wielu przypadkach awarie wyposażenia na linii wpływają w mniejszy stopniu na efektywność procesu, ale z uwagi na ilość i prawdopodobieństwo wystąpienia awarii nie mogą być pomijane przy aktywnościach związanych na przykład z konserwacja maszyn.
Krok 2: Pogrupuj maszyny i wyposażenie w obszary
Linie produkcyjne to często złożone zespoły maszyn, obsługiwane przez kilku operatorów. Pracownicy mają ściśle określone obszary co ułatwia zarządzanie umiejętnościami oraz rozwojem pracownika. Dzięki wybraniu dedykowanych obszarów na całej linii jesteśmy w stanie określić stopień trudności danego obszaru i tym samym opracować ścieżkę rozwoju pracowników. Ścieżka ta definiowana jest przez dwa czynniki. Pierwszy z nich jest związany z obecnymi potrzebami, innymi słowy zapełnianiem luk kompetencyjnych. Drugi czynnik determinuje zrównoważony rozwój pracownika, który przechodzi wyznaczone obszary po kolei, by w konsekwencji stać w pełni gotowym do pracy na linii. Taka osoba zwykle pełni rolę dowodzącego (Line Driver) po nabraniu odpowiedniego doświadczenia.
Krok 3: Wypisz operacje na linii
Standaryzacja pracy w procesach zautomatyzowanych ma jeden ważnykrok a tym krokiem jest krok 3, ponieważ błędy popełnione w tym miejscu mogą skutkować znacznymi utrudnieniami w kolejnych krokach. Wypisując operacje musimy mieć na uwadze 3 podstawowe kategorie: Przezbrojenie, TPM oraz produkcja. Stanowią one odrębne działy, lecz dopiero znajomość wszystkich kluczowych instrukcji z poszczególnych działów zapewnia, że pracownik może samodzielnie pracować na wybranym obszarze. Podział ten pozwala skutecznie zarządzać szkoleniami, gdyż poszczególne kategorie różnią się warunkami przeprowadzania szkolenia. Dla trzeciego kroku warto opracować tabelę, na której będą wszystkie wypisane maszyny z wcześniejszym podziałem oraz kolumny dla kategorii operacji. Tym sposobem za pomocą „X” możemy oznaczać instrukcje do wykonania przy danej maszynie według określonej kategorii. Ważnym elementem z punktu widzenia jakości przyswajanej wiedzy jest podział długich operacji na mniejsze. Z naszych doświadczeń bazujących na ponad 150 zakładach wynika, że 10 Głównych kroków to optymalna wartość jaką podczas jednego szkolenia jest w stanie przyswoić nowy pracownik.
Krok 4: Przygotuj Skill Matrix
Skill Matrix to nadrzędny dokument podczas zarządzania procesem szkoleń stanowiskowych. Pozwala on określić kogo i z jakiej operacji szkolić. Bazując na wyznaczonych celach, planujemy szkolenia dla operatorów. Do przygotowania Skill Matrix potrzebujemy informacji na temat kadry pracującej przy linii produkcyjnej oraz wcześniej przygotowanej listy operacji. W przypadku skomplikowanych zespołów maszyn ilość instrukcji może być duża i przekraczać nawet 50-60.
Krok 5: Określ priorytety dla rozwoju pracowników
Z uwagi na znaczną ilość instrukcji przy tak złożonych procesach, należy zadecydować które operacje są kluczowe, a którymi można zająć się w drugiej kolejności. W tym celu oceniamy każdą operację w skali od 1-10, pod kątem 4 czynników. Pierwszy dotyczy skomplikowania operacji. Im większa ocena tym operacja jest bardziej skomplikowana i dłużej zajmuje proces szkolenia pracowników. Drugi czynnik odwołuje się do wpływu na baraki. Źle lub w ogóle nieprzeszkolony pracownik pracując przy operacji o wysokiej ocenie w tym aspekcie przyczyni się do generowania większego odpadu. Błąd podczas przezbrojenia przy podajniku będzie miał mniejszy wpływ na braki niż w przypadku np. wytłaczarki, która bezpośrednio bierze udział w produkowaniu wyrobów. Trzeci czynnik w podobny sposób jak drugi ocenia wpływ na wydajność linii. Czwarty czynnik dotyczy wpływu awarii na długość przestoju całej linii. Tak jak przenośnik taśmowy możemy wymienić z łatwością na inny tak awaria w przypadku pieca przekłada się na znacznie dłuższy postój. Po dokonaniu oceny dla wszystkich operacji, mnożymy je przez siebie czego wynikiem jest ostateczny współczynnik istotności. Można wykorzystać pareto i rozpocząć następny krok od 20% tych operacji, które w sumie maja 80% wartości współczynnika istotności.
Krok 6: Przygotuj Instrukcje Pracy Standaryzowanej TWI
Bazując na danych z poprzedniego kroku, należy przystąpić do przygotowywania Instrukcji Pracy Standaryzowanej TWI. Pełnią one rolę ściągi dla instruktora podczas szkolenia stanowiskowego. Przygotowanie dokumentów musi opierać się o zasady TWI, w innym przypadku utrudnione będzie korzystanie z nich podczas instruktażu. Zasady dotyczące tworzenia standardów pracy można znaleźć na naszej stronie internetowej [Link: Zasady tworzenia instrukcji TWI]. Warto pamiętać, że celem przygotowania instrukcji jest sprawne przeprowadzenie szkolenia, dlatego adresatem w pierwszej kolejności jest trener. Instrukcja dla ucznia dostępna jest dopiero po zakończeniu instruktażu – Nigdy przed.
Rys.1. Standaryzacja pracy w procesach zautomatyzowanch – Przykładowa instrukcja
Krok 7: Przeprowadź instruktaże na produkcji
Szkolenia z zakresu instrukcji pracy standaryzowanej TWI rozpoczynamy zgodnie z ustalonym harmonogramem opartym o ustalone priorytety z kroku piątego. Posługujemy się przy tym czterokrokową metodą przekazywania wiedzy zgodnie z TWI dzięki temu instrukcje i proces instruowania pracowników będzie ze sobą spójny. Ograniczeniem przy stosowaniu standardowej metody może być fakt, że niektóre operacje są długie i mało powtarzalne (np. Reagowanie na problemy, przezbrojenia). W tym celu możemy posłużyć się zmodyfikowaną metodą TWI, skuteczna jest tam, gdzie trudno zastosować metodę standardowa. Przebieg metody opisany jest w tabeli …
Podsumowanie
Standaryzacja pracy według programu TWI dla procesów manualnych jaki zautomatyzowanych jest równie skuteczna. Wynika to z tego, że TWI opiera się na tym w jaki sposób ludzki umysł przyswaja wiedzę. Standaryzacja pracy procesów zautomatyzowanychjest o wiele trudniejsza szczególnie jeśli mamy do czynienia z liniami produkcyjnymi zawierającymi wiele maszyn i urządzeń są trudniejsze. Wynika to z tego z faktu, iż operacje są zdecydowanie bardziej skomplikowane i wymagają dużej wiedzy i świadomości pracowników. Proces siedmiu kroków opisanych w tym artykule jest uniwersalnym drogowskazem standaryzowania pracy na stanowiskach zautomatyzowanych dla działów utrzymania ruchu i produkcji.
Artykuł został opublikowany na łamach czasopisma Szef UR
Autor: Kamil Müller
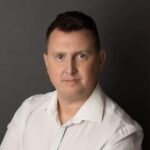
Jestem popularyzatorem Lean Management oraz programu Training Within Industry. Jestem praktykiem. Współtworzę wiele startupów. Od 2015 roku jestem CEO w Leantrix - czołowej firmie z zakresu konsultingu Lean w Polsce, która począwszy od 2024 roku organizuje jedną z największych konferencji poświęconych szczupłemu zarządzaniu w Polsce - Lean TWI Summit. Od 2019 roku jestem CEO w firmie Do Lean IT OU zarejestrowanej w Estonii, która tworzy software etwi.io używany przez kilkadziesiąt firm produkcyjnych i usługowych w Europie i USA.