Jak co roku jeden z czołowych magazynów branżowych – Służby UR, przeprowadził największe ogólnopolskie badania wśród pracowników odpowiedzialnych za Zarządzanie Produkcją oraz Utrzymanie Ruchu. Ponownie zostaliśmy poproszenie o komentarz do wyników ankiet. W tym roku nasz ekspert odniósł się do bloku tematycznego: diagnostyka.
Jakiś czas temu pisaliśmy o diagnostyce artykuł dla magazynu Służby UR.
Wyniki tych badań będą pomocnym materiałem dla osób naukowo zajmujących się problematyką Zarządzania Produkcją oraz Utrzymania Ruchu, ale również dla osób, które chcą zobaczyć jakie są praktyczne spostrzeżenia osób na co dzień pracujących w obszarze produkcji. Zachęcamy do lektury i analizy!
Ogólnopolskie Badanie Zarządzania Produkcją i Utrzymania Ruchu 2016 – wyniki ankiety wśród pracowników działów UR
Branże które brały udział w badaniu:
- przemysł maszynowy 22%
- high-tech zaawansowane rozwiązania techniczne 10%
- przemysł chemiczny 5%
- przemysł spożywczy 31%
- przemysł energetyczny 12%
- przemysł motoryzacyjny 18%
- przemysł hutniczy 2%
Automatyka przemysłowa
W jakich obszarach będące pod nadzorem służb utrzymania ruchu stosowana jest automatyka przemysłowa? (możliwa wielokrotna odpowiedź)
- Infrastruktura budynków zakładu (np. oświetlenie, HVAC) 73,3%
- Pojazdy i urządzenia transportu wewnętrznego 46,7%
- Maszyny i urządzenia pomocnicze / wsparcie realizacji produkcji 93,3%
- Maszyny i urządzenia technologiczne / realizacja procesów produkcyjnych 98,2%
Jak duża część parku maszynowego objęta jest automatycznymi systemami kontrolno-pomiarowymi?
- Wszystkie maszyny i urządzenia lub niemal całość 26,4%
- Większa część 41,5%
- Mniej niż połowa 8,1%
- Wybrane maszyny, ale nie więcej niż jedna czwarta parku 46,7%
Jakie są plany rozwoju przedsiębiorstwa w zakresie automatyki przemysłowej w krótkim i średnim horyzoncie czasowym? (możliwa wielokrotna odpowiedź)
- Rozwój i automatyzacja systemów kontrolno-pomiarowych 67,6%
- Unowocześnienie systemów automatycznego sterowania, nowe sterowniki maszyn 54,1%
- Pełne objęcie parku maszynowego systemami automatycznego sterowania 9,5%
- Większa automatyzacja procesów pomocniczych i logistyki zakładowej 43,3%
- Pełna automatyzacja procesów wytwarzania 7%
- Większa automatyzacja procesów wytwarzania 73,2%
W jaki sposób wykorzystywane są dane z kontroli i pomiarów? (możliwa wielokrotna odpowiedź)
- Diagnostyka maszyn, urządzeń i systemów 65%
- Planowanie działań korygujących i zapobiegawczych 82,1%
- Optymalizacja procesów, zwiększanie efektywności 68,1%
- Bieżąca kontrola i nadzór nad realizowanymi procesami 97,3%
Jakie systemy łączności urządzeń kontroli i pomiarów z komputerami SUR są stosowane? (możliwa wielokrotna odpowiedź)
- Klasyczne interfejsy (RS 232C, GPIB, VXI) 85,5%
- Magistrale komputerowe (USB, FireWire, Centronics) 70,8%
- Transmisja na duże odległości (sieć Ethernet, radiomodemy, telefonia GSM/GPRS) 89,1%
- Transmisja na małe odległości (podczerwień, Bluetooth) 3%
Planowanie i sterowanie produkcją
Jaka dominująca strategia sterowania produkcją jest stosowana w przedsiębiorstwie?
- Produkcja realizowana na żądanie, indywidualne zamówienie (sterowanie nadążne) 23,3%
- Wymuszony przepływ produkcji, produkcja masowa (pull) 70%
- Produkcja poprzez zlecanie, określona ilość produkcji w czasie, krótkie serie (push) 37,7%
W jakich obszarach sterowania produkcją w przedsiębiorstwie uczestniczą służby utrzymania ruchu? (możliwa wielokrotna odpowiedź)
- Podejmowanie działań korekcyjnych 95,3%
- Sprawdzanie wykorzystania czasu pracy pracowników i maszyn 52,1%
- Kontrola postępu prac 36,7%
- Przydział operacji do stanowisk 58,9%
- Wyznaczanie terminów rozpoczęcia i zakończenia wyrobów i operacji 29,1%
- Planowanie obciążeń 55,5%
Jaki główny priorytet warunkuje układanie harmonogramów produkcji?
- Aktualne cele firmy dotyczące produktywności, sprzedaży, kosztów itp. 31,5%
- Aktualne możliwości produkcyjne zakładu, dostępne moce przerobowe 23,3%
- Bieżące zapotrzebowanie na produkcję (wyroby gotowe, półwyroby) 83,3%
Jakie narzędzia kontroli realizacji planów produkcyjnych są stosowane w przedsiębiorstwie? (możliwa wielokrotna odpowiedź)
- Analiza stanów magazynowych (materiałów, wyrobów gotowych itp.) 85,4%
- Analiza raportów z postępów produkcji 73,3%
- Analiza czasu pracy maszyn i wyposażenia produkcyjnego 51,2%
- Moduły systemu MRP/ERP 46,7%
Jaki jest priorytet realizacji przepływu materiałów w przedsiębiorstwie?
- Terminowo-ilościowy 82,2%
- Wynikający z celów zarządzania zapasami 46,7%
- Wynikający z celów zarządzania jakością 33,3%
- Minimalizacja kosztów 66,7%
Media eksploatacyjne
Czy i w jaki sposób określane jest bieżące zapotrzebowanie na media eksploatacyjne?
- Tak, stosując modele wielokryterialne lub specjalne oprogramowanie 8,3%
- Tak, bazując na planach/harmonogramach produkcji 35,5%
- Tak, na podstawie danych historycznych 69,2%
- Nie, zużycie mediów nie jest planowane, płacimy za tyle, ile się zużyje 2%
Co w największym stopniu wpływa na efektywne gospodarowanie mediami eksploatacyjnymi?
- Zaangażowanie i inicjatywa kierownictwa 56,7%
- Zaangażowanie pracowników zakładu i zrozumienie przez nich istoty problemu 43,3%
- Systematyczne monitorowanie zużycia mediów na określonych stanowiskach / wydziałach 61,7%
- Ustalanie mierzalnych celów ograniczenia zużycia mediów 36,7%
- Opracowanie i nadzorowanie spójnego zestawu działań dla ograniczenia zużycia mediów 56,6%
Gdzie jest możliwe uzyskanie największych oszczędności mediów w praktyce UR?
- Maszyny i urządzenia technologiczne / realizacja procesów produkcyjnych 96,4%
- Maszyny i urządzenia pomocnicze / wsparcie realizacji produkcji 50%
- Pojazdy i urządzenia transportu wewnętrznego 16,7%
- Infrastruktura budynków zakładu (np. oświetlenie, HVAC) 81,1%
Jakie działania są podejmowane w celu ograniczenia strat mediów (w tym głównie energii) w podległych działach? (możliwa wielokrotna odpowiedź)
- Analiza zapotrzebowania na media i odpowiednie planowanie dostaw / przesyłu 72,3%
- Optymalizacja wykorzystania wyposażenia / likwidacja pustych przebiegów 72,3%
- Szkolenia pracowników w zakresie efektywnej eksploatacji maszyn i urządzeń 80,9%
- Korzystanie z usług zewnętrznych / mechanizm finansowy ESCO 32,2%
- Automatyka w budynkach (np. wyłączniki czasowe, sterowane ruchem) 74,5%
- Stosowanie izolacji / uszczelnień 38,1%
Które trzy najważniejsze kryteria wyboru dostawców narzędzi i materiałów eksploatacyjnych są stosowane w przedsiębiorstwie?
- Dotychczasowa współpraca 71,3%
- Renoma dostawcy 23,5%
- Rekomendacje 36,7%
- Jakość dostaw 75,1%
- Czas dostawy 51,5%
- Ceny usług 94,5%
- Serwis i wsparcie 56,7%
- Lokalizacja 16,7%
Diagnostyka
Czy wykorzystują Państwo techniki diagnostyczne w utrzymaniu ruchu?
- Nie 2,5%
- Tak 97,5%
Jakie metody badań diagnostycznych wykorzystują Państwo w swoich przedsiębiorstwach?
- Metoda magnetyczna 13,3%
- Radiografia 27%
- Badanie ultradźwiękami 36,7%
- Metoda wibroakustyczna 55,5%
- Termowizja 83,3%
- Badania akustyczne 63,1%
- Badanie produktów zużycia 56,7%
- Badania wizualne 98,1%
Jakie korzyści daje według Pani/Pana włączenie diagnostyki do systemu prewencyjnej obsługi technicznej?
- Stworzenie ścieżki inspekcji z uwzględnieniem miejsc, metod i interwałów pomiaru 67,8%
- Transparentność gromadzenia danych 25,4%
- Możliwość optymalizacji czasu pracy 66,1%
- Lepsza kontrola wykonania prac 73,7%
- Regularność pomiarów 52%
Jakie trendy w diagnostyce i obsłudze prewencyjnej zaobserwował Pan/Pani w firmie w ciągu ostatnich 2 lat?
- Nie zaobserwowałem/am żadnych zmian służących rozwojowi diagnostyki 26,3%
- Rozwój kompetencji pracowników 70,8%
- Inwestycje w wyposażenie pomiarowe 50,2%
- Przeniesienie odpowiedzialności za diagnostykę z firm zewnętrznych na pracowników utrzymania ruchu 71,8%
- Pełniejsze i bardziej efektywne wykorzystanie możliwości CMMS 47,6%
Jakie są kluczowe zasady doboru metod diagnostycznych w Pana/Pani firmie?
- Brak konieczności posiadania specjalistycznego wyposażenia 25%
- Niski koszt 35,7%
- Brak uciążliwości dla eksploatacji maszyn 80,3%
- Łatwość zastosowania 74,8%
- Szybkość diagnozy 33,2%
- Dokładność metody 43,5%
- Doświadczenie własne 81,2%
Kto w Pana/Pani firmie odpowiada za diagnostykę parku maszynowego?
- Diagnosta 28,8%
- Kierownik UR 36,7%
- Mechanik 36,8%
- Technik UR 69,5%
- Doraźnie, specjaliści mechanicy, automatycy, elektrycy (zależnie od rodzaju awarii) 50,9%
Jakimi kryteria wyboru kieruje się Pan/Pani przy wyborze dostawcy i sprzętu diagnostycznego
- Oferta wyposażenia odpowiadająca naszym potrzebom 92,2%
- Pozytywne doświadczenia w użytkowaniu sprzętu producenta 41,8%
- Renoma producenta 28,2%
- Cena 51,8%
- Wsparcie techniczne i merytoryczne 77,8%
- Warunki gwarancji i serwisu 31%
Czy Państwa system diagnostyczny zakłada coroczny remont (postój)?
- Nie 36,7%
- Tak 63,3%
Czy w Pana/Pani firmie tworzone są następujące dokumenty/procedury służące utrzymaniu założonej eksploatacji maszyn?
- Plan konserwacji i przeglądów 99,1%
- Roczny plan remontów 77,5%
- System rejestracji wykonanych przeglądów i konserwacji 89,1%
- Plan smarowania maszyn 85,3%
- Plan rejestracji wykonanych smarowań 63,3 %
- System komunikacji do zgłaszania awarii i niesprawności maszyn 83,7%
Komentarz naszego eksperta do tematu: Diagnostyka
Diagnostyka to nauka zajmującą się rozpoznaniem problemów w danym obiekcie, zarówno w człowieku, jak i maszynie. Diagnostyka jest podstawą w prewencyjnym podejściu do zarządzania parkiem maszynowym w dowolnym przedsiębiorstwie. W przeprowadzonym badaniu ankietowym przez Służby UR aż 97,5% firm deklaruje, że diagnostyka jest wykonywana na ich maszynach regularnie. To bardzo dobrze bo zawsze jest lepiej zapobiegać, niż leczyć! Z badań wynika, że wśród firm, które diagnozują procesy aż 98,1% korzysta z metod wizualnych. Ludzie wzrokowo są w stanie wychwycić blisko 83% informacji z otoczenia. Jednak kluczowe jest uczyć osoby diagnozujące również „wyczuwania” zmian w maszynie poprzez węch, czy dźwięk.
W przeprowadzonym badaniu dużą uwagę należy zwrócić na fakt, że 71,8% firm zauważyło trend, że co raz więcej czynności diagnostycznych przenoszonych jest z outsourcingu na pracowników UR. Moim zdaniem ten trend będzie się jeszcze bardziej pogłębiał, a firmy pójdą krok na przód – podstawowa diagnostyka będzie przenoszona z pracowników UR na operatorów! Dlaczego? Przede wszystkim operatorów w firmach jest więcej niż pracowników UR, a koszt ich pracy jest zazwyczaj niższy. Co jednak najważniejsze, operatorzy są najbliżej maszyny i najszybciej są w stanie „poczuć” jej problem. Wcześniej jednak istotne jest uczenie operatorów przez pracowników UR i zmiana ich świadomości, że nie są wyłącznie od pracy na maszynie, ale są od tego, żeby efektywnie wykorzystywać maszynę i dbać o nią. Dla wielu firm to gigantyczna zmiana kulturowa! Można oczywiście zamiast budować świadomość operatorów wdrażać różne rozwiązania techniczne, które mają zastąpić czujność pracownika. Jednak jak pokazują badania ankietowe, aż 81,2% firm dobiera działania diagnostyczne bazując na swoich doświadczeniach! Warto te doświadczenia zapisać w przejrzystych standardach Autonomicznej Konserwacji (AM), a następnie szkolić z nich pracowników budując ich świadomość. Należy również pamiętać o systemie zgłaszania usterek, który jest łącznikiem w procesie diagnozowania pomiędzy operatorami a pracownikami UR.
Przy tworzeniu takiego systemu należy angażować obie grupy pracowników i dążyć do tego, aby był on:
• Dedykowany tylko do usterek (nie awarii!).
• Prosty w obsłudze.
• Szybki w wypełnieniu.
• Łatwo dostępny.
• Wymyślony przez operatorów i pracowników UR, co chcę podkreślić raz jeszcze.
Wdrożenie systemu zgłaszania usterek, przeszkolenie pracowników, opracowanie standardów, skategoryzowanie usterek jest o wiele tańsze niż inwestycja w rozwiązania techniczne. Niestety jest to proces o wiele trudniejszy. Związany jest on ze zmianą podejścia do zarządzania – zmianą kultury firmy. Z drugiej strony każda firma dąży do ciągłej nauki. Moim zdaniem większą nauką dla firmy jest budowanie świadomości wśród pracowników, niż wdrażanie nawet najlepszych środków technicznych (diagnostycznych). Życie w kulturze Lean Management nauczyło mnie jednego: pracuj nad kulturą organizacji, a nie nad wdrażaniem narzędzi. Każde narzędzie i tak w konsekwencji będzie używane albo interpretowane przez człowieka.
Komentarz: Bartosz Misiurek
dr inż., LeanTrix sp. z o.o.
Technologia i systemy informatyczne
Czy stosowane są w Pana/Pani firmie narzędzia informatyczne wspierające produkcję?
- Nie 6,7%
- Tak 93,3%
Czy stosowane są w Pana/Pani firmie narzędzia informatyczne wspierające utrzymanie ruchu?
- Nie 15%
- Tak 85%
Czy Pani/Pana firma wykorzystuje następujące systemy wspomagania produkcji i/lub utrzymania ruchu?
- ERP (Enterprise resource planning) 52,9%
- SCADA HMI (Supervisory Control And Data Acquisition) 61,1%
- CMMS (Computerised Maintenance Management System) 64,3%
- EAM (Enterprise asset management) 24,3%
- MES (Manufacturing Execution System) 52,9%
- APS (Advanced Planning System) 31,4%
Jakie były/są główne powody wdrożenia systemów IT dla wsparcia produkcji?
- Podniesienie efektywności pracy 92,3%
- Uporządkowanie i rejestracja działań 95,1 %
- Określenie odpowiedzialności Kadry za poniesione działania 41,7%
- Usprawnienie przepływów materiałowych 52,5%
Jakie były/są główne powody wdrożenia systemów SUR dla wsparcia produkcji?
- Podniesienie efektywności pracy 87,4%
- Uporządkowanie i rejestracja działań 83,3%
- Określenie odpowiedzialności Kadry za poniesione działania 43,1%
- Usprawnienie przepływów materiałowych 52%
Czy wdrożenia systemów informatycznych IT wspierających produkcję i utrzymanie ruchu ustalane są w Pana/Pani firmie odgórnie czy z inicjatywy pracowników?
- Inicjatywa kierowników produkcji i/lub utrzymania ruchu 23,3%
- Wspólna decyzja kierownictwa oraz inżynierów produkcji i UR 76,7%
- Decyzja naczelnego kierownictwa 31%
Czy w Pani/Pana firmie planowany jest zakup MES?
- Planujemy wdrożenie 0 – 2 lat 28,3%
- Wdrożyliśmy system MES 45,7%
- Nie, z uwagi na ograniczenie wydatków inwestycyjnych 31,4%
- Planujemy wdrożenie 2 – 5 lat 38,6%
- Nie, nie ma takiej potrzeby 2,1%
Jakich korzyści oczekuje Pani/Pan od systemów MES?
- Większa elastyczność 25,4%
- Szybka adaptacja w dynamicznym środowisku produkcyjnym 35,85
- Obniżenie kosztów produkcji SUR 71,5%
- Dostarczanie informacji o wskaźnikach efektywności 82,9%
- Efektywniejsze wykorzystanie posiadanych zapasów 63,8%
- Raportowanie w czasie rzeczywistym 100%
Czy Pani/Pana zdaniem wykorzystywany w firmie CMMS jest prosty i intuicyjny w obsłudze?
- Nie 20,8%
- Raczej nie 18,5%
- Raczej tak 38%
- Nie mam zdania 36,7%
- Tak 45,1%
Jakie możliwości CMMS okazały się decydujące przy zakupie?
- Nadzór nad aparaturą kontrolno-pomiarową 27,1%
- Budżety i ich wykorzystanie – kontrola 41,7%
- Zgłoszenie usterek, uwag i potrzeb użytkowników maszyn 75,1%
- Rozliczenie prac 83,3%
- Zarządzanie zleceniami prewencyjnymi i doraźnymi 92,3%
- Ewidencja i opis maszyn/urządzeń 75,2%
- Planowanie czynności obsługowych, modernizacyjnych, inwestycyjnych 69,1%
- Rejestracja aktualnych prac i awarii 99,7%
Co jest dla Pani/Pana czynnikiem decydującym o skuteczności wdrożonego CMMS?
- Redukcja liczby wypadków i poprawa bezpieczeństwa 18,5%
- Sprawne zarządzanie gospodarką magazynową na podstawie analizy rozchodu 69,7%
- Możliwość budżetowania w zależności od różnych aspektów 19,3%
- Zgłoszenie usterek, uwag i potrzeb użytkowników maszyn 99,8%
- Umożliwienie przygotowania analiz niezawodnościowych na podstawie dostępnych danych historycznych 82,42%
- Efektywniejsze harmonogramowanie i planowanie prac prewencyjnych 72,1%
Kto w Pani/Pana firmie jest odpowiedzialny za analizę danych „zbieranych” przy pomocy CMMS/EAM/MES?
- Nie ma wyznaczonej osoby 28,2%
- Diagnosta 18,4%
- Dyrektor produkcji 2%
- Kierownik produkcji 53,2%
- Technik UR 25,5%
- Planista UR 60%
- Szef/kierownik UR 82,1%
Rozwinięcia których elementów oczekuje Pani/Pan jako użytkownik informatycznych systemów wspomagania zarządzania UR?
- Rozwój funkcji raportowania i analizy danych 87,7%
- Większy stopień dostosowania do potrzeb klientów branżowych 59,2%
- Większy zakres wymiany danych z systemami zarządczymi 29,7%
- Możliwość wykorzystania metody SaaS – system IT w chmurze 8,2%
Bezpieczeństwo i higiena pracy
Ile wszystkich wypadków przy pracy miało miejsce w Państwa zakładzie przez ostatnie 2 lata?
a 0 0,2%
b 1 – 5 97,5%
c 5 – 10 2,2%
d 10 – 20 0,1%
e > 20 0%
Jakie były najczęstsze przyczyny wypadków pracowników w Państwa zakładzie? (wielokrotna odpowiedź)
a brawura i nadmierne ryzyko 40,1%
b narzucono zbyt wysokie normy wydajnościowe stanowiska 0,3%
c omijanie/celowa dezaktywacja urządzeń bezpieczeństwa 91,5%
d brak odpowiedniego nadzoru7,3%
e brak lub niewłaściwe przeszkolenie pracowników 2,0%
f brak środków ochrony osobistej 3,5%
g niewłaściwa organizacja stanowiska pracy (niewłaściwe przejścia, nieodpowiednio składowane detale) 80, 7%
h przyczyny medyczne (zasłabnięcie, choroba) 2,1%
i przypadek (nieszczęśliwy wypadek – brak przyczyn zewnętrznych) 78,3%
Czy w następstwie wypadków ich ewentualne przyczyny zostały usunięte?
a nie 0,1%
b tak, ale tylko tam, gdzie miał miejsce wypadek 90,5%
c tak, na większości stanowisk 5,7%
d tak, na wszystkich stanowiskach 3,5%
e nie wiem 0,2%
Czy przez ostatnie 2 lata w Pana/Pani firmie wprowadzono zmiany służące poprawie bezpieczeństwa pracy?
a nie 1,7%
b tak 96,1%
c nie wiem 2,2%
Jeśli TAK to: (odpowiedź TAK/NIE, na każdy podpunkt)
a przeprowadzono analizę ryzyka tak 95,6% nie 4,4%
b zmieniono organizację pracy na niektórych stanowiskach tak 72,3% nie 27,7%
c wprowadzono ściślejszy nadzór nad operatorami i/lub pracownikami UR tak 91,5% nie 8,5%
d zastosowano dodatkowe środki ochrony indywidualnej tak 97,3% nie 2,7%
e przeprowadzono dodatkowe szkolenia operatorów tak 70,5% nie 29,5 %
f zdecydowano o zastosowaniu technicznych środków ochronnych tak 82,4% nie 17,6%
g zmodyfikowano część/wszystkie maszyny stosując nowe techniczne środki ochronne tak 41,8% nie 58,2%
h wynajęto zewnętrzną firmę do wykonania analizy ryzyka/projektu/wykonania zmian tak 2,4 % nie 97,6%
Jak ocenił(a)by Pan(i) swoją wiedzę na temat wymagań bezpieczeństwa dla maszyn (Dyrektywa Maszynowa, normy zharmonizowane)
1 3,0%
2 4,2%
3 47,3%
4 39,4%
5 6,1%
5 oznacza „bardzo dobrze”, 4 „dobrze”, 3 „dostatecznie”, 2 „słabo”, 1″ – w ogóle nie poruszam się w tej tematyce”)
Czym kieruje się Pan/Pani przy wyborze rozwiązań technicznych w zakresie bezpieczeństwa do danej maszyny/stanowiska pracy? (odpowiedź TAK/NIE, na każdy podpunkt, lub wskazanie hierarchii poszczególnych odpowiedzi)
a wynikami analizy ryzyka 1
b normą PN-EN ISO 12100 3
c normą PN-EN ISO 13849-1 2
d decyzją przełożonego 4
e ceną rozwiązania 9
f jakością produktu 5
g popularnością producenta/rozwiązania na rynku 6
h kompetencjami i jakością obsługi firmy oferującej urządzenia bezpieczeństwa 7
i obecnością danego rozwiązania na innych maszynach w zakładzie 8
Jaki zakres ma proces zarządzania ryzykiem zawodowym w Pana(i) przedsiębiorstwie
a identyfikacja i opis ryzyk 5,9%
b identyfikacja, opis i analiza ryzyk 75,1%
c wszystkie powyższe oraz plany reakcji 8,9%
d wszystkie powyższe oraz śledzenie i kontrola ryzyk 10,1%
Outsourcing produkcji i utrzymania ruchu
Czy Pan/Pani firma korzysta z outsourcingu produkcji lub/i utrzymania ruchu?
- Tak 60%
- Nie 40%
jeśli tak to: W jakim zakresie korzystacie Państwo ze współpracy z firmami zewnętrznymi?
- Inne 24,2%
- Outsourcing zarządzania i monitorowania mediów eksploatacyjnych 21,1%
- Outsourcing zarządzania gospodarką olejowo – smarowniczą 1,5%
- Outsourcing IT 14,2%
- Kompleksowo – outsourcing całego działu UR 12,2%
- Outsourcing diagnostyki 46,1%
- Outsourcing usług elektrycznych 33,3%
Czy w ciągu najbliższych 2 lat planujecie Państwo korzystać z outsourcingu UR?
- Nie wiem 7,1%
- Raczej nie 28,3%
- Raczej tak 37,5%
- Tak 44,3%
- Nie 21,4%
Czy w ciągu najbliższych 2 lat planujecie Państwo korzystać z outsourcingu pracowników produkcyjnych?
- Nie wiem 3%
- Raczej nie 15,2%
- Raczej tak 14,3%
- Nie 35,7%
- Tak 28,6%
Jakie powody skłaniają Pana/Pani firmę do korzystania z outsourcingu?
- Oszczędność czasu, który można poświęcić na realizacje podstawowych zadań 36,4%
- Profesjonalizm pracy firmy zewnętrznej – dostęp do nowoczesnych rozwiązań 54,5%
- Większa wydajność pracy zewnętrznej firmy w zakresie realizowania usług na rzecz produkcji i utrzymania ruchu 36,4%
- Uniezależnienie się od pracy jednego/kilku specjalistów zatrudnionych na etacie 34,5%
- Kryzys i konieczność oszczędzania 9,1%
- Możliwość zmniejszenia zatrudnienia 18,2%
Jakie zagrożenia według Pana/Pani wynikają ze współpracy z outsourcerem?
- Brak odpowiedzialności za poniesione straty związane z przestojem w produkcji 45,5%
- Brak fachowej wiedzy o specjalistycznym parku maszynowym 54,5%
- Utrudniony kontakt ze specjalistami – brak „hot line” 18,2%
- Trudności w nadzorowaniu pracowników firmy outsourcingowej 36,4%
- Udostępnienie firmie zewnętrznej wrażliwych dla firmy danych 54,5%
- Długi czas oczekiwania na reakcję/serwis 17,8%
Logistyka produkcji i części zamienne
Czy w Pana/Pani firmie określono wartość magazynu MRO (magazyn części zamiennych)?
- Tak 66,7%
- Nie 26,7%
- Nie wiem 6,7%
Z jakimi problemami magazynowania części zamiennych spotyka się Pan/Pani najczęściej?
- Nieuzasadnione duże zapasy 32,4%
- Wielu właścicieli części 28,6%
- Obecność części bez numeru – problem identyfikacji 42,9%
- Brak ujednoliconych procedur korzystania z magazynu 21,4%
- Kilka rodzajów magazynów 48,3%
- Dublowane numery lub pozycje magazynowe 21,4%
- Praktyka tworzenia nowych pozycji magazynowych dla powtarzającego się w czasie zakupów tego samego sprzętu (części) 28,6%
Jak często inwentaryzujecie Państwo części w magazynie części zamiennych?
- 1 raz/rok 60%
- 2 razy/rok 6,7%
- Nie wiem 13,3%
- Nieregularnie – brak ustalonych zasad 20%
- Częściej niż 2/rok 1,7%
Jakie wskaźniki wykorzystywane są w Pana/Pani magazynie części zamiennych w celu optymalizacji zarządzania zapasami?
- Wartość magazynu 71,4%
- Max/min/średnia ilość na stanie 50%
- Działania na redukcję stanów 21,4%
- Raport z inwentaryzacji (deklaracji ilości na stanie, a ilość w programie) 50%
- Liczba pozycji magazynowych 28,6 %
- Ilość zatrzymań/awarii będąca konsekwencją braku części na stanie 14,3%
- Działania na standaryzację części zamiennych 35,7%
Które z części zamiennych w Pana/Pani firmie są badane, rejestrowane i wyróżnione w strategii zarządzania produkcją?
- Wyróżnia się części strategiczne 83,3%
- Wyróżnia się części o największej dynamice ruchu 54,5%
- Wyróżnia się części o największej liczbie wydań 48,7%
- Wyróżnia się części o największej wartości 41,7%
- Wyróżnia się części najmniej istotne 8,3%
Z uwagi na jakie kryterium maszyny powinny posiadać zmagazynowane części zamienne?
- Czas realizacji zamówienia od dostawcy 92,9%
- Specyfika maszyny i prognozowany czas zużycia części 50%
- Ważność dla UR 71,4%
- Koszty magazynowania (koszt akumulacji) 8,3%
- Nie przeprowadziliśmy analizy kryteriów 5,7%
- Koszty zamówienia pojedynczej sztuki vs pakiet (efekt skali) 4,6%
Czy w Pana/Pani firmie podejmowane są działania mające na celu badanie i wybór najlepszych dostawców części zamiennych?
- Nie prowadzimy takich działań 7,1%
- Raczej nie 0,5%
- Trudno powiedzieć 14,3%
- Tak, ale podejmowane są sporadycznie 28,6%
- Tak, mają charakter systematyczny 54,8%
Kto w Pana/Pani firmie decyduje o poziomie zapasów/licznie części zamiennych na magazynie?
- Kierownik UR 50%
- Nie ma jednej osoby 35,7%
- Dyrektor produkcji 14,3%
- Kierownik produkcji 3%
- Logistyk 7,1%
Źródło: Badania opublikowane za zgodą magazynu Służby UR.
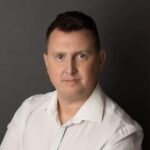
Jestem popularyzatorem Lean Management oraz programu Training Within Industry. Jestem praktykiem. Współtworzę wiele startupów. Od 2015 roku jestem CEO w Leantrix - czołowej firmie z zakresu konsultingu Lean w Polsce, która począwszy od 2024 roku organizuje jedną z największych konferencji poświęconych szczupłemu zarządzaniu w Polsce - Lean TWI Summit. Od 2019 roku jestem CEO w firmie Do Lean IT OU zarejestrowanej w Estonii, która tworzy software etwi.io używany przez kilkadziesiąt firm produkcyjnych i usługowych w Europie i USA.