Wdrażanie TPM jednorazowo na wszystkich maszynach wymagałoby zaangażowania wielu osób w fabryce, co może być kłopotliwe i niepraktyczne. W artykule przedstawiono, w jaki sposób dokonać wyboru pilotażowej maszyny albo obszaru maszyn, aby wdrażanie TPM zakończyło się skucesem.
Przemysł to najszybciej rozwijająca i najważniejsza gałąź gospodarki. Przedsiębiorstwa produkcyjne muszą nieustannie usprawniać swoje procesy wytówrcze między innymi poprzez efektywne wykorzystywanie swojego parku maszynowego. TPM staje naprzeciw tym wyzwaniom. Jego głównym zadaniem jest maksymalizacja efektywności pracy maszyn poprzez stałe zwiększanie ich dostępności, wykorzystania oraz jakości produkowanych na nich wyrobów. Wdrażanie TPM jednorazowo na wszystkich maszynach wymagałoby zaangażowania wielu osób w fabryce, co może być kłopotliwe i nie praktyczne. Dlatego kluczowe jest wybranie obszaru pilotażowego. Doświadczenia w przemyśle pokazują, że przedsiębiorstwa wybierając taki obszar kierują się różnymi kryteriami. W Tabeli 1 zestawiono najczęściej wybierane obszary pilotażowe na wdrażanie TPM w firmach wraz z uzasadnieniem dokonanego wyboru.
Tab. 1. Najczęściej przyjmowane kryteria wyboru obszaru pilotażowego na wdrażanie TPM w firmach produkcyjnych
Wybrany obszar pilotażowy | Uzasadnienie wyboru obszaru |
---|---|
Najnowsza maszyna albo grupa maszyn | W takim obszarze przede wszystkim wdrożenie jest stosunkowo łatwe ze względu na brak usterek na maszynach. Ponadto system TPM może uchronić wykorzystywane tam maszyny przed awariami i ułatwia utrzymywanie ich w możliwie najlepszym stanie technicznym. |
Najstarsza maszyna albo grupa maszyn | W tym obszarze system TPM może poprawić radykalnie efektywność występujących tam maszyn. |
Najbardziej awaryjna maszyna | Implementacja systemu TPM na najbardziej awaryjnej maszynie daje możliwość osiągnięcia szybkich i widocznych korzyści szczególnie w pierwszych fazach wdrożenia. |
Najmniej obciążona maszyna | Wdrożenie systemu TPM na najmniej obciążonej maszynie umożliwia przetestowanie pewnych rozwiązań bez wpływu na proces produkcyjny. |
Maszyna, które ze względu na swoją zdolność produkcyjną wykazują duże wykorzystanie względem innych zasobów (tzw. „wąskie gardła”) | Wdrożenie systemu TPM na maszynie uznawanej za „wąskie gardło” daje możliwość poprawy jej dostępności, co jest kluczowe w kontekście poprawy wydajności całego procesu produkcyjnego. |
Wszystkie przedstawione strategie wyboru obszaru pilotażowego mają swoje logiczne uzasadnienia. Niestety żadna z nich nie uwzględnia kompleksowo takich kryteriów jak: rola maszyny w systemie produkcyjnym, jej wpływu na opóźnienie dostaw do klientów, czy jej pozycji w strumieniu wartości. W artykule przedstawiono w jaki sposób dokonać wyboru pilotażowej maszyny albo obszaru maszyn do wdrażania systemu TPM.
Kryteria wyboru obszaru pilotażowego na wdrażanie TPM
W wielu fabrykach, w przypadku awarii kilku maszyn, trudno jest zdefiniować do której jako pierwszej powinien udać się pracownik UR. Jednym słowem brak jest wyznaczonej priorytetowości maszyn. Pracownicy intuicyjnie czują, która maszyna jest najbardziej kluczowa. Dla operatorów kluczową maszyną może być ta, która stanowi „wąskie gardło” i decyduje o efektywności np. linii produkcyjnej. Dla pracowników UR kluczową maszyną jest ta, która najczęściej ulega awariom. Natomiast dla działu finansowego najistotniejszą maszyną może być ta, na której odbywa się produkcja wyrobów dla kluczowego klienta. Każda z tych grup patrzy zupełnie z innej perspektywy na występujące w procesie produkcyjnym maszyny. Istotne jest zatem zunifikowanie podejścia i określenie priorytetu każdej z maszyn. Jest to pomocne przy reagowaniu na awarię, ale również w przypadku wyboru maszyny albo obszaru maszyn do wdrażania systemu TPM. W celu wyznaczenia maszyn kluczowych należy wziąć pod uwagę trzy najważniejsze kryteria:
- wpływ na system produkcyjny (X),
- pozycję w strumieniu wartości (Y),
- wpływ na klientów (Z).
Wdrażanie TPM powinno rozpoczynać się się na maszynach o najwyższym priorytecie. Jednak to nie wszystko. W zależności od kategorii priorytetu maszyn powinna zostać przyjęta odpowiednia strategia funkcjonowania systemu TPM np. w zakresie zarządzania częściami zamiennymi, czy szybkości reagowania na zidentyfikowane usterki.
Wpływ maszyny na system produkcyjny (X)
Analizując wpływ maszyn na proces produkcyjny należy zastanowić się, czy ich przestój spowodowany np. awarią może wstrzymać produkcję. Kluczem w tej analizie powinno być określenie wykorzystania zdolności produkcyjnych maszyn. Oblicza się ją jako iloraz średniej liczby zamówień na maszynie względem jej maksymalnej wydajności w określonym czasie. Ponadto kluczowe jest określenie, czy dana maszyna w procesie posiada ewentualne rezerwy wyposażenia, wydajności i zasobów. Informacje te służą określeniu oceny wpływu maszyny na system produkcyjny (Tab. 2).
Tab. 2. Klucz oceny wpływu maszyn na system produkcyjny (X)
Wykorzystanie zdolności produkcyjnych | Istnieją rezerwy? | Opis | Wpływ | Ocena |
---|---|---|---|---|
<= 75% | TAK | Przerwy w działaniu są nie odczuwalne dla produkcji | bez zakłóceń | 1 |
>75%<=95% | TAK | Przerwy w działaniu są minimalizowane własnymi rezerwami w wydajności | bardzo drobne zakłócenia | 2-3 |
>95% | TAK | Przerwy w działaniu są minimalizowane własnymi urządzeniami rezerwowymi | drobne zakłócenia | 4-5 |
<=75% | NIE | Przerwy w działaniu będą miały niewielki wpływ na system produkcyjny | małe zakłócenia | 6-7 |
>75%<=95% | NIE | Dłuższe przerwy w działaniu urządzeń spowodują spore zakłócenia w systemie produkcyjnym |
umiarkowane zakłócenie | 8-9 |
>95% | NIE | Krótkie przerwy w działaniu urządzeń spowodują spore zakłócenia w systemie produkcyjnym |
poważne zakłócenia | 10 |
Im maszyna otrzyma większą ocenę w obszarze wpływu na system produkcyjny, tym jej przestój generuje większe zakłócenia i problemy dla produkcji.
Pozycja maszyny w strumieniu wartości (Y)
Nie tylko wpływ na system produkcyjny powinien mieć znaczenie przy określaniu priorytetów maszyn. Równie istotna jest pozycja maszyny w strumieniu wartości, a co za tym podąża, czas na usunięcie jej ewentualnej awarii. Im maszyna ulokowana jest w procesie bliżej klienta (tzw. dołu strumienia wartości), tym czas na usunięcie awarii jest mniejszy. W praktyce oznacza to, że im więcej zapasów w toku produkcji, tym czas na usunięcie potencjalnej awarii jest dłuższy. Niemniej należy pamiętać, że zapasy to marnotrawstwo. Określając pozycję maszyny w strumieniu wartości należy zestawić jej czas na usunięcie awarii z najdłuższym dostępnym czasem usunięcia awarii w systemie produkcyjnym (Tab. 3).
Tab. 3. Klucz oceny pozycji maszyn w strumieniu wartości (Y)
Udział w najdłuższym czasie na usunięcie awarii w systemie produkcyjnym | Przykład / Wyjaśnienie | Wpływ | Ocena |
---|---|---|---|
>=80% | Brak strat ilościowych lub czasowych | niekrytyczny | 1 |
<80% >= 70% | Przerwy nie mają żadnego dalszego wpływu na datę dostawy lub wydajność | mało krytyczny | 2-3 |
<70% >= 50% | W rzadkich wypadkach, daty dostaw mogą być lekko przekroczone | średnio krytyczny | 4-5 |
<50% >= 30% | Dłuższe przerwy mogą powodować przekroczenie istotnych terminów | umiarkowanie krytyczny | 6-7 |
<30% >= 10% | Należy liczyć się ze stratami ilościowymi lub przekroczeniem ważnych terminów | krytyczny | 8-9 |
<10% | Przerwy mają istotny wpływ na wydajność ilościową lub datę dostawy | bardzo krytyczny | 10 |
Im bliżej dołu strumienia wartości, tym procentowy udział czasu usunięcia awarii maszyny wobec najdłuższego czasu usunięcia awarii w procesie produkcyjnym będzie mniejszy. Tym samym pozycja w strumieniu wartości będzie bardziej krytyczna.
Wpływ przestoju maszyny na klienta (Z)
Ostatnim aspektem przy określaniu priorytetów maszyny jest ustalenie, w jaki sposób produkty wytwarzane przy ich udziale wpływają na klientów końcowych. Jeżeli klient jest w stanie poczekać na opóźniony wyrób produkowany na maszynie wówczas ocena wpływu na klienta jest niska. Taką informację w przedsiębiorstwie można pozyskać w dwojaki sposób: bezpośrednio od klienta albo z działu sprzedaży. Na podstawie zebranych danych szacuje się wpływ awarii maszyny na klienta (Tab. 4).
Tab. 4. Klucz oceny wpływu wyrobów na klientów (Z)
Wpływ awarii maszyny na klienta | Przykład / Wyjaśnienie | Wpływ | Ocena |
---|---|---|---|
<= 2 | Krótkie opóźnienia nie mają wpływu na klientów | Żaden | 1 |
< 2 < = 3 | Opóźnienia nie mają poważnego wpływu na klientów | bardzo niewielki | 2-3 |
> 3 < = 5 | Opóźnienia powodują drobne przerwy u klientów | Niewielki | 4-5 |
> 5 < = 7 | Opóźnienia powodują problemu u klientów | Średni | 6-7 |
> 7 < = 9 | Opóźnienia powodują poważne problemu u klientów |
Poważny | 8-9 |
> 9 | Opóźnienia powodują zatrzymanie produkcji u klientów |
bardzo poważny | 10 |
USTALENIE STRATEGII NA WDRAŻANIE TPM
Oceny uzyskane na podstawie tabel 2,3 oraz 4 powinny posłużyć do określenia kategorii priorytetu maszyny wg schematu przedstawionego na rysunku 1.
Rys. 1. Określenie kategorii priorytetów maszyn
Wdrażanie systemu TPM powinno odbywać się przede wszystkim na maszynach kluczowych (o największej kategorii priorytetowej). Są to maszyny oznaczone na Rysunku 1 kategoriami: „F” i „H”. Kolejne maszyny w systemie produkcyjnym, które powinny być skierowane na wdrażanie TPM, oznaczone zostały kategoriami: „E” i „G”. Najmniej krytyczne maszyny w systemie produkcyjne oznaczone kategoriami: „D”, „B”, „C” i „A” mogą zostać skierowane na wdrażanie TPM w ostatniej kolejności.
W zależności od kategorii priorytetowej maszyn należy przyjąć odpowiednią strategię na wdrażanie TPM (Tab. 5).
Tab. 5. Strategia na wdrażanie TPM w zależności od kategorii priorytetu maszyny
Kategoria priorytetowa | Autonomiczna konserwacja – strategia wdrażania | Planowa konserwacja – strategia wdrażania |
---|---|---|
Maszyny kluczowe w procesie produkcyjnym Kategoria: „H” i „F” |
|
|
Maszyny średnio kluczowe w procesie produkcyjnym
Kategoria: „G” i „E” |
|
|
Maszyny mało kluczowe w procesie produkcyjnym Kategoria: „D”, „C”, „C” i „A” |
|
|
Im maszyna ma większa kategorię priorytetową, tym lepiej i dokładniej powinna być przygotowania dla niej strategia planowej i autonomicznej konserwacji. Części do wymiany podczas przeglądów powinny znajdować się możliwie blisko maszyny. Każda awaria maszyny powinna być szczegółowo przeanalizowana w celu zdefiniowania środków zaradczych, aby w przyszłości jej zapobiec. Dodatkowo służby UR powinny być dostępne przy takich maszynach podczas całego jej czasu pracy. Maszyny te powinny stanowić obszar pilotażowy wdrażania systemu TPM w każdej firmie produkcyjnej. Również do takich maszyn jako pierwszych powinni podążać pracownicy UR w przypadku wystąpienia awarii.
Informacja o artykule:
Artykuł opublikowano w magazynie Służby Utrzymania Ruchu (maj – czerwiec 2015)
Autor:
Dr inż. Bartosz Misiurek
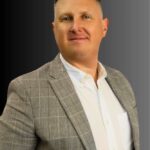
Jestem popularyzatorem Lean Management oraz programu Training Within Industry. Jestem praktykiem. Współtworzę wiele startupów. Od 2015 roku jestem CEO w Leantrix - czołowej firmie z zakresu konsultingu Lean w Polsce, która począwszy od 2024 roku organizuje jedną z największych konferencji poświęconych szczupłemu zarządzaniu w Polsce - Lean TWI Summit. Od 2019 roku jestem CEO w firmie Do Lean IT OU zarejestrowanej w Estonii, która tworzy software etwi.io używany przez kilkadziesiąt firm produkcyjnych i usługowych w Europie i USA.