MTBF, MTTR i MTTF to jedne z ważniejszych wskaźników przy wdrażaniu TPM (Total Productive Maintenance), który jest obecnie powszechnie wdrażany w polskich przedsiębiorstwach. Mierzenie efektywności wdrożenia tego systemu odbywa się zazwyczaj poprzez takie KPI jak: OEE, MTBF, MTTR i MTTF. Trudno jest wskazać firmę produkcyjną, która wdraża filozofię szczupłego zarządzania bez systemu TPM. Celem TPM jest poprawa efektywności wykorzystania parku maszynowego poprzez redukcję tzw. sześciu wielkich strat (ang. Six Big Losses):
- Awarie
- Zbyt długi czas przezbrojeń
- Mikroprzestoje w pracy maszyny
- Obniżona prędkość pracy
- Braki jakościowe
- Obniżona wydajność podczas rozruchu maszyny’
W systemie TPM używanych jest wiele wskaźników wspomagających mierzenie postępów w zakresie poprawy wykorzystania maszyn. Wśród nich są wskaźniki MTTF, MTBF i MTTR.
Co to są wskaźniki MTTF, MTBF i MTTR?
Wszyscy z pewnością zgodzą się, że przy wdrażaniu TPM w dowolnej firmie najczęściej używanym wskaźnikiem jest OEE (Overall Equipment Efficiency). Wskaźnik OEE pozwala przyporządkować sześć wielkich strat w pracy maszyny do 3 obszarów: dostępność, wykorzystanie oraz jakość produkowanych na niej wyrobów. Wskaźnik OEE mierzy więc efektywność wykorzystania maszyn. Wnioski wynikające z analizy wskaźnika OEE są przydatne zarówno dla działów Produkcji, jak i Utrzymania Ruchu. Kluczową, z punktu widzenia TPM, stratą w efektywności pracy maszyn są awarie. Ich redukcja ma wpływ na poprawę dostępności maszyn. Wskaźnik OEE ma wiele zastosowań. Pozwala między innymi zobrazować jaką część wszystkich strat w pracy maszyny stanowią awarie. Jednak wskaźnik ten nie analizuje szczegółowo samych awarii. Temu służą trzy kluczowe wskaźniki utożsamiane głównie z działami Utrzymania Ruchu:
- MTTR – Średni czas potrzebny do naprawy awarii (ang. Mean time to repair)
- MTTF – Średni czas do wystąpienia awarii (ang. Mean time to failure)
- MTBF – Średni czas pomiędzy awariami (ang. Mean time between failures)
Ich mierzenie, przeglądanie ich trendów i wyciąganie z nich wniosków jest kluczowe, aby minimalizować czas awarii, a tym samym poprawiać dostępność maszyn.
Jak obliczać i mierzyć wskaźniki MTTF, MTBF i MTTR?
Jeżeli w Twojej firmie liczony jest wskaźnik OEE to posiadasz wszelkie dane, aby obliczyć wskaźniki MTTR, MTTF i MTBF. Tak, ponieważ do ich obliczenia potrzebujesz następujących informacji:
- Dostępny czas produkcji (pomniejszony o przerwy planowane)
- Czas awaryjności (niezdatności)
- Liczba zdarzeń naprawczych
Dostępny czas produkcji jest jednym z trzech czynników budujących wskaźnik OEE. Czas awaryjności to dana, które jest niezbędna, aby obliczyć dostępność. Liczba zdarzeń naprawczych jest daną zbieraną przez wszystkie działy Utrzymania Ruchu, gdyż jest niezbędna, aby obliczyć czas awaryjności. Jak zatem powinno się obliczać wskaźniki MTTF, MTBF i MTTR.
- MTTR = czas awaryjności/liczba zdarzeń naprawczych [min]
- MTTF = (dostępny czas pracy – czas awaryjności)/liczba zdarzeń [min]
- MTBF = MTTR + MTTF [min]
Analiza wskaźników MTTF, MTBF i MTTR najlepiej sprawdza się poprzez śledzenie ich trendów w kolejnych dniach/tygodniach/miesiącach. Wówczas uwidacznia się, czy działania TPM przynoszą zamierzone efekty. Kluczowym wyzwaniem jest to, jak głęboko schodzić z analizą wskaźników MTTF, MTBF i MTTR w firmie. Czy analizować wszystkie maszyny w całej fabryce? Czy skupić się na wybranej maszynie? A może wybrać konkretne części albo narzędzia na maszynie? Na wszystkie te pytania odpowiedź jest: TAK. Wskaźniki MTTF, MTBF i MTTR należy śledzić zarówno dla całej fabryki (aby śledzić efektywność pracy służb UR), jak i również dla wybranych części konkretnej maszyny (aby wiedzieć, kiedy należy prewencyjnie przeglądnąć albo wymienić tą część). Aby skutecznie wybrać maszyny, które powinny być szczegółowo analizowane pod względem mierzenia wskaźników MTTF, MTBF i MTTR, należy posłużyć się podejściem zwanym Lean Maintenance (ang. Szczupłe Utrzymanie Ruchu). W tym podejściu wyszczególnia się priorytetowe maszyny w procesie poprzez analizę ich:
- Wpływu na system produkcyjny
- Pozycji w strumieniu wartości
- Wpływu na klientów
Kiedy dana maszyna zostanie wybrana jako priorytetowa, należy przeanalizować awaryjność jej części (narzędzi, wyposażenia) biorąc pod uwagę:
- Wpływ awarii części maszyny na działanie maszyny
- Przewidywalność występowania awarii na danej części
- Częstotliwość występowania awarii na danej części
W ten sposób można wyznaczyć priorytetowe maszyny, a na nich kluczowe części (narzędzia i wyposażenia). Jest to niezbędne, aby skutecznie wyznaczyć te części, które powinny zostać objęte mierzeniem poprzez wskaźniki MTTF, MTBF i MTTR.
Po co obliczać i mierzyć wskaźniki MTTF, MTBF i MTTR?
Aby planować czas przeglądów albo wymian prewencyjnych kluczowych części na priorytetowych maszynach
Kiedy wyznaczone są kluczowe części na priorytetowych maszyn, wówczas można założyć czas prewencyjnej wymiany danej części. Ten czas najczęściej ustala się przyjmując zasadę: prewencyjna wymiana części co 85% MTBF. Jeżeli średni czas pomiędzy awariami dla danej części wynosi przykładowo 1000 minut, wówczas prewencyjna jej wymiana powinna odbyć się po 850 minutach. Ustalone 85% MTBF jest ogólnie przyjmowaną zasadą, która może być dostosowana do potrzeb każdego zakładu z osobna. Istotne jest jednak to, aby taka prewencyjna wymiana odbywała się na kluczowych częściach maszyny. Można to przyrównać do wymiany żarówki w lampie. W domu wymiana żarówki następuje wtedy, kiedy ulegnie ona awarii – spali się. Jest to mało kluczowa część, której awaria nie ma większego wpływu na nasze życie. Mamy w domu wiele innych lamp i możemy żarówkę wymienić po dłuższym czasie. Na salce operacyjnej w szpitalu awaria żarówki może mieć olbrzymi wpływ na jakość wykonywanej operacji. W takiej sytuacji wymiana prewencyjna może odbywać się co 85%MTBF. Znaczy to tyle, że wymieniana jest żarówka, która wciąż jest sprawna! Jednak lampa na salce operacyjnej jest priorytetowym urządzeniem i nigdy nie powinno się doprowadzać do sytuacji, w której jej część przestanie świecić. Dlatego tak ważne jest przed mierzeniem wskaźników MTTF, MTBF i MTTR wyznaczenie priorytetowych maszyn, a na nich wyznaczenie kluczowych części.
Aby sprawdzać skuteczność działania służb UR w zakładzie
Tak, wskaźniki MTTF, MTBF i MTTR są doskonałymi KPI (Kluczowe Wskaźniki Efektywności) dla działu Utrzymania Ruchu, a w szczególności wskaźnik MTTR. Wykorzystując wskaźniki MTTF, MTBF i MTTR jako KPI dla działu Utrzymania Ruchu powinno się przede wszystkim śledzić je z punktu widzenia całej fabryki (wszystkich maszyn i urządzeń), aby uchwycić generalny trend. Dobry trend jest wówczas, kiedy dla przykładu wskaźniki MTTR maleje. Znaczy to tyle, że średni czas usuwania awarii jest co raz krótszy.
Aby mierzyć postępy w skracaniu czasu usuwania awarii w zakładzie
Artykuł o mapowaniu procesu usuwania awarii został opublikowany w jednym z wcześniejszych numerów Służb UR. Mapowanie procesu usuwania awarii pomaga przeanalizować ten proces i odseparować od siebie operacje, które dodają wartość, od tych, które są marnotrawstwem. Praktyka pokazuje, że przeszło 50% działań w procesie usuwania awarii to marnotrawstwo! Są to np. próba odszukania mechanika przez operatora, szukanie części przez mechaników, brak narzędzi i materiałów i wiele innych. Są to typowe problemy organizacyjne. Im czas usuwania awarii jest dłuższy, tym spada dostępność maszyny. Analiza procesu usuwania awarii, szukanie rozwiązań doskonalących w zakresie poprawy organizacji tego procesu, przekłada się na obniżenie wskaźnika MTTR.
Aby mierzyć postępy we wdrażaniu działań Autonomicznej Konserwacji (Autonomous Maintenance)
Autonomiczna Konserwacja (AM) jest jednym z filarów systemu TPM. Większość zakładów produkcyjnych zaczyna swoją przygodę z TPM właśnie od wdrożenia AM. I słusznie! Dzięki AM zwiększa się świadomość operatorów w obszarze technicznym. Operatorzy zaczynają dbać o swoją maszynę, jak o swój prywatny samochód. Zaczynają dostrzegać usterki, zanim przerodzą się one w awarie. Dzięki AM następuje poprawa wartości wskaźnika MTBF. Po prostu rzadziej dochodzi do awarii ponieważ usuwane są ich przyczyny (usterki) zanim przeobrażą się one w poważny problem na maszynie.
Case Study: Zastosowanie MTBF, MTTR i MTTF w poprawie efektywności maszyn
Wprowadzenie
Jedna z wiodących firm produkcyjnych w Polsce postanowiła skupić swoje działania na zwiększeniu efektywności swojego parku maszynowego poprzez wdrożenie systemu TPM (Total Productive Maintenance). W szczególności postanowiono skupić się na monitorowaniu i analizie wskaźników MTBF (Mean Time Between Failures), MTTR (Mean Time to Repair) oraz MTTF (Mean Time to Failure), aby lepiej zrozumieć procesy związane z awaryjnością maszyn i minimalizować przestoje.
Problem
Przed wdrożeniem systemu TPM firma zmagała się z częstymi awariami maszyn, które miały bezpośredni wpływ na jakość i terminowość produkcji. Zarząd firmy dostrzegł, że kluczowe problemy dotyczą:
- Zbyt częstych awarii kluczowych maszyn na liniach produkcyjnych,
- Długiego czasu reakcji na awarie,
- Braku odpowiedniego harmonogramu przeglądów prewencyjnych.
Analiza wskaźnika OEE wykazała, że największe straty dotyczyły dostępności maszyn, co wynikało z długiego czasu napraw i częstych awarii. W związku z tym postanowiono wdrożyć bardziej szczegółową analizę przy użyciu wskaźników MTBF, MTTR oraz MTTF.
Wdrożenie
W pierwszej fazie projektu wyznaczono kluczowe maszyny, które miały największy wpływ na całą produkcję. W tym celu zespół wdrożył podejście Lean Maintenance, analizując strumień wartości i wpływ awaryjności na całą produkcję. Po wytypowaniu priorytetowych maszyn, rozpoczęto szczegółowe monitorowanie awarii i ich przyczyn.
Przykład: Jedną z maszyn o kluczowym znaczeniu była prasa hydrauliczna, która regularnie ulegała awariom z powodu zużycia określonych części. Wskaźniki MTTF oraz MTBF dla tej maszyny były analizowane na poziomie poszczególnych części, takich jak uszczelki i pompy hydrauliczne.
- MTBF: Analiza pokazała, że średni czas pomiędzy awariami pompy wynosił 1200 godzin.
- MTTF: Średni czas do awarii uszczelki wynosił 800 godzin.
Na podstawie tych danych zaplanowano harmonogram przeglądów prewencyjnych – np. uszczelki były wymieniane co 680 godzin, zgodnie z zasadą prewencyjnej wymiany przy 85% MTBF.
Rezultaty – MTBF, MTTR i MTTF
Po roku monitorowania wskaźników i wdrażania przeglądów prewencyjnych firma odnotowała znaczne zmniejszenie liczby awarii i skrócenie czasu napraw. MTTR na kluczowych maszynach zmniejszył się o 30%, a MTBF wzrosło o 25%. Dzięki tym działaniom, dostępność maszyn znacząco się poprawiła, co bezpośrednio wpłynęło na wskaźnik OEE, który wzrósł o 10% w ciągu roku.
Wnioski
Dzięki zastosowaniu wskaźników MTBF, MTTF i MTTR, firma była w stanie:
- Zidentyfikować kluczowe maszyny, których awarie miały największy wpływ na proces produkcji.
- Skutecznie zaplanować przeglądy prewencyjne, co pozwoliło uniknąć kosztownych przestojów.
- Poprawić efektywność działania służb Utrzymania Ruchu, dzięki regularnej analizie wskaźników i skracaniu czasu napraw.
Podsumowanie – MTBF, MTTR i MTTF
Mierzenie wskaźników MTTF, MTBF i MTTR nie jest wyłącznie po to, aby widzieć ogólne trendy w działaniu służb Utrzymania Ruchu w zakładzie. Dzięki tym wskaźnikom można planować prewencyjne przeglądy i wymiany części na priorytetowych maszynach. Dają one również możliwość analizy skuteczności wdrażania działań związanych ze skracaniem czasu usuwania awarii. Są również doskonałym miernikiem wdrażania działań Autonomicznej Konserwacji, które są podstawą przy wdrażaniu systemu TPM. Wskaźniki te są ściśle związane z analizą awaryjności, dlatego są dużym wspomaganiem dla działów Utrzymania Ruchu w zakładach produkcyjnych. Warto stosować te wskaźniki, ale nie tylko aby je mierzyć, ale po to by na ich podstawie wyciągać wnioski i wdrażać działania mające na celu obniżyć poziom awaryjności maszyn i skracać czas usuwania awarii. To wszystko przełoży się na zwiększenie dostępności maszyn i poprawę wskaźnika OEE.
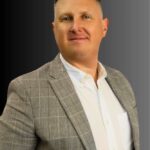
Jestem popularyzatorem Lean Management oraz programu Training Within Industry. Jestem praktykiem. Współtworzę wiele startupów. Od 2015 roku jestem CEO w Leantrix - czołowej firmie z zakresu konsultingu Lean w Polsce, która począwszy od 2024 roku organizuje jedną z największych konferencji poświęconych szczupłemu zarządzaniu w Polsce - Lean TWI Summit. Od 2019 roku jestem CEO w firmie Do Lean IT OU zarejestrowanej w Estonii, która tworzy software etwi.io używany przez kilkadziesiąt firm produkcyjnych i usługowych w Europie i USA.