Macierz kompetencji to jedno z narzędzi do zarządzania procesem standaryzacji pracy zarówno w operacjach produkcyjnych, jak i w dziale Utrzymania Ruchu. Istnieje wiele definicji zarządzania. Większość z nich sprowadza się do tego, że zarządzanie to kierowanie ludźmi w taki sposób, aby osiągnęli postawione im cele. Podobnie brzmiącą definicję przyjął jeden z guru zarządzania – Ricky Griffin. Według niego zarządzanie to zestaw działań (planowanie, organizowanie, motywowanie, kontrola) skierowanych na zasoby organizacji (ludzkie, finansowe, rzeczowe, informacyjne) wykorzystywanych z zamiarem osiągnięcia celów organizacji. W przypadku wdrażania Total Productive Maintenance (z ang. totalne produktywne utrzymanie ruchu, TPM) nadrzędnym celem jest zero awarii na maszynach. Zasoby, które pomagają osiągnąć ten cel to ludzie, głównie operatorzy. Są oni najbliżej maszyny, a dzięki temu są w stanie najszybciej zareagować na usterki w jej funkcjonowaniu. Usterki są natomiast przyczyną awarii. W TPM operatorzy powinni być odpowiedzialni za wykonywanie codziennych kontroli w pracy maszyny, zwanych autonomiczną konserwacją. Właśnie wtedy są w stanie dostrzec wszystkie usterki zanim one przerodzą się w awarie.
Mając zdefiniowany cel i określone zasoby należy wyznaczyć szereg działań, aby cel został osiągnięty. Według Griffina działania te powinny następować według ustalonego cyklu:
- Planowanie zadań.
- Organizowanie pracy.
- Motywowanie i uczenie ludzi, aby chcieli te zadania realizować.
- Kontrolowanie poprawności wykonywanych zadań.
Cykl ten jest zbieżny z podejściem Plan-Do-Check-Act (z ang. zaplanuj-wykonaj-sprawdź nadzoruj, PDCA), które zostało opisane przez Williama Edwardsa Deminga. Efektywne przeprowadzenie tych działań z pewnością skutecznie przełoży się na osiągnięcie celu. I to jest zazwyczaj największe wyzwanie w każdej organizacji. Często określanie zadań dla pracowników sprowadza się w firmach wyłącznie do powiedzenia operatorowi, że musi on czyścić i konserwować maszynę. To jest niestety niewystarczające z dwóch głównych powodów. Po pierwsze operator prawdopodobnie nie będzie tego robił (brak świadomości po co ma to robić oraz brak fazy kontrolowania i nadzorowania). Po drugie, jeżeli mimo tego zacznie to robić, to z pewnością będzie popełniać błędy. Często w fabrykach słyszy się stwierdzenie, że powstała awaria spowodowana była właśnie przez błąd ludzki. Nigdy się z tym nie zgadzam. Uważam, że błąd ludzki jest tylko efektem złego systemu zarządzania, a precyzyjnie źle realizowanych zadań zarządczych. Przyczyn źródłowych błędów ludzkich należy doszukiwać się w (Rysunek 1):
- Braku albo złym procesie szkolenia operatorów.
- Nieprzestrzeganiu standardu pracy przez operatorów, ale z tego powodu, że standard pracy był źle opracowany.
- Braku systemu nadzorowania i audytowania operatora po szkoleniu.
Rys. 1. Przyczyny źródłowe błędów ludzkich
Źródło: Misiurek B., 2015, Metodyka standaryzacji autonomicznych procesów eksploatacyjnych zorientowana na poprawę efektywności maszyn zautomatyzowanych, Praca doktorska, Uniwersytet Technologiczny we Wrocławiu, s.50
Dokładniej przedstawione powyżej przyczyny źródłowe błędów ludzkich zobrazuje przykład z fabryki z branży Automotive. Na wtryskarce pracującej w trybie automatycznym zauważono, że najwięcej zdefiniowanych strat w jej wykorzystaniu spowodowanych jest przez awarię podajnika wibracyjnego A (Rysunek 2).
Rys. 2. Bezpośrednie przyczyny postojów dla wybranego procesu automatycznego formowania wtryskowego na obrabiarce
Źródło: Horbal R., Misiurek B., 2009, Lepsza wydajność dzięki szkoleniom stanowiskowym metodą TWI, MM Magazyn Przemysłowy, nr 8/9, s. 44-47
Analiza kart spływu z produkcji wykazała, że owszem awaria podajnika A zdarza się najczęściej, ale tylko u jednego operatora i tylko na jego zmianie. Okazało się, że operator ten, podczas działań związanym z autonomicznym utrzymaniem ruchu, czyścił podajnik suchą szmatką. Standard przewidywał czyszczenie go szmatką nasączoną denaturatem. W efekcie opiłki kurzu osiadały na podajniku i doprowadzały do wielu drobnych przestojów. Problem z początku techniczny, okazał się problemem związanym z błędem ludzkim. Jak jednak wspomniałem wcześniej, nie uważam, że określenie „błąd ludzki” wskazuje rzeczywisty problem. Okazało się, że operator ten nie miał świadomości, dlaczego powinien używać do czyszczenia podajnika szmatki nasączonej denaturatem. Ponadto denaturat zamykany był w szafce oddalonej o kilkaset metrów od stanowiska. Okazało się również, że operator po szkoleniu ani razu nie był sprawdzony przez swojego przełożonego. W tym wspomnianym przypadku zaistniała każda z przyczyn źródłowych straty przypisywanych do błędu ludzkiego. Z moich doświadczeń wynika, że większość strat w procesach produkcyjnych związanych jest z błędami ludzkimi. Ich przyczyną źródłową są przede wszystkim zaniedbania w zarządzaniu. I nie ma tu znaczenia, czy są to procesy manualne, czy maszynowe. Wszędzie występuje praca ludzka, chociaż może zmieniać się jej charakter. Błąd ludzki to problem, który należy wyeliminować. Problemy natomiast eliminuje się wyłącznie wtedy, kiedy uderza się w ich przyczyny źródłowe.
Program TWI jako wsparcie dla przełożonych w skutecznym zarządzaniu pracą ludzi
Wróćmy do definicji zarządzania, a więc określania działań, które powinno się realizować z wykorzystaniem zasobów, aby osiągnąć postawiony cel. Przełożonych w realizacji tych działań wspiera program Training Within Industry (z ang. szkolenia w przemyśle, TWI). Program TWI powstał podczas II Wojny Światowej w USA, aby wspierać przełożonych w zarządzaniu personelem. Program TWI kierowany był głównie do mistrzów, brygadzistów i doświadczonych operatorów. Pierwotnie jego celem było wyćwiczenie w nich umiejętności instruowania pracowników, doskonalenia obecnych metod pracy oraz utrzymywanie dobrych relacji z pracownikami. Po II wojnie światowej program TWI przekazano między innymi do Japonii, gdzie takie firmy, jak Toyota czy Sanyo wykorzystały go, aby zbudować fundamenty do rozwijania swoich efektywnych metod produkcji. Jak dowodzą badania, japoński system produkcyjny Toyoty (ang. Toyota Production System, TPS) został oparty w 100% na programie TWI. Obecnie program TWI utożsamiany jest z filozofią szczupłego zarządzania (ang. Lean Management, Lean). Wiele narzędzi i metod należących do filozofii Lean powstało w oparciu o program TWI. Japończycy zauważyli, że program TWI daje skuteczne metody wspierające proces zarządzania pracownikami przez przełożonych. W Tabeli 1 zestawiono w jaki sposób program TWI wspiera realizację działań w procesie zarządzania.
Tabela 1. Jak program TWI wspomaga przełożonych w zarządzaniu ludźmi
Działania przy zarządzaniu | Metody programu TWI wspierające realizację zarządzania procesem autonomicznej konserwacji w TPM |
Planowanie zadań | Macierz kompetencji (ang. Skill Matrix) |
Organizowanie pracy | Tworzenie instrukcji pracy standaryzowanej dla zadań autonomicznej konserwacji |
Motywowanie i uczenie | Przekazywanie wiedzy metodą TWI Instruowanie Pracowników |
Kontrolowanie poprawności wykonywanych zadań | Audytowanie procesów |
W tym artykule przedstawione zostanie w jaki sposób planować zadania autonomicznej konserwacji z wykorzystaniem macierzy kompetencji (ang. Skill Matrix). Sposób tworzenia instrukcji pracy standaryzowanej, który związany jest z organizowaniem procesu autonomicznej konserwacji, został opisany przeze mnie w artykule Rola standaryzacji w autonomicznej obsłudze maszyn, który ukazał się w magazynie Służby Utrzymania Ruchu w numerze 5 (55)/2015 (wrzesień – październik 2015). W artykule tym można zobaczyć przykładową instrukcję autonomicznej konserwacji z firmy LG Display. Znajdują się tam również wskazówki na co należy zwracać uwagę tworząc Instrukcję Pracy Standaryzowanej. W tym samym numerze ukazał się artykuł Pani Doroty Bieniek o temacie: 7. Filar TPM. Szkolenia – czyli jak efektywnie działać z TPM. W artykule tym została opisana metoda TWI Instruowania Pracowników. Jest to najbardziej efektywna metoda przekazywania wiedzy praktycznej. Jej stosowanie możliwe jest wyłącznie wtedy, kiedy dla operacji opracowana została wcześniej Instrukcja Pracy Standaryzowanej. Ostatnie działanie związane z kontrolowaniem poprawności wykonywanych zadań, a więc z audytowaniem, opisane zostanie w kolejnym numerze. Tam przedstawionych zostanie między innymi 10 zasad tworzenia kart audytowych oraz przykłady takich kart dla działań autonomicznej konserwacji z różnych fabryk.
Macierz kompetencji – narzędzie wspomagające planowanie zadań autonomicznej konserwacji
Podczas planowania zadań do realizacji w ramach autonomicznej konserwacji ważne jest opracowanie narzędzia zwanego macierz kompetencji. Macierz kompetencji powinna zawierać zbiór wszystkich operacji wchodzących w skład działań autonomicznej konserwacji (min. czyszczenie, smarowanie, dokręcanie itd.) oraz wykaz operatorów, którzy dane operacje powinni wykonywać. Przykład jak powinna wyglądać macierz kompetencji przedstawiono na Rysunku 3. Przedstawiona macierz kompetencji pochodzi ze stanowiska zrobotyzowanego z firmy, która jest czołowym producentem narzędzi do spawania.
Rys. 3. Macierzy kompetencji dla działań autonomicznej konserwacji
Źródło: Misiurek B., 2015, Metodyka standaryzacji autonomicznych procesów eksploatacyjnych zorientowana na poprawę efektywności maszyn zautomatyzowanych, Praca doktorska, Uniwersytet Technologiczny we Wrocławiu, s.225-229
Macierz kompetencji powinna być użytkowana przez bezpośrednich przełożonych. W przypadku działań autonomicznej konserwacji wyjątkowo tą osobą może być pracownik działu Utrzymania Ruchu. To on również wyznacza operacje jakie powinni posiąść operatorzy bezpośrednio produkcyjni w ramach działań konserwujących na maszynach. Macierz kompetencji przedstawiona w przykładzie wyszczególnia sześć operacji składających się na autonomiczną konserwację:
- Czyszczenie maszyny.
- Inspekcję maszyny.
- Dokręcanie luźnych elementów (min. śrub).
- Smarowanie maszyny.
- Reakcja na najczęściej pojawiające się awarie w pracy maszyny bez potrzeby wzywania pracowników UR.
- Wypełnianie i zgłaszanie karty usterki.
Dla każdej operacji zawartej w macierzy kompetencji powinna zostać opracowana Instrukcja Pracy Standaryzowanej, na której wyszczególnione są główne kroki, wskazówki i przyczyny występowania wskazówek. Taki podział jest istotny, aby można było poprowadzić szkolenie zgodnie z metodą TWI Instruowanie Pracowników. Ponadto macierz kompetencji pozwala ocenić każdego z pracowników przez swojego bezpośredniego przełożonego z tego, na jakim poziomie potrafi wykonywać daną operacją. Taka ocena jest niezbędna przy planowaniu szkoleń. Macierz kompetencji wymaga również określenia optymalnej liczby operatorów, którzy potrafią wykonywać daną operację (cel) i porównać ją z rzeczywistą liczbą operatorów, którzy mogą samodzielnie przy tej operacji pracować. Bazując na legendzie opisanej na przykładzie (macierz kompetencji – rysunek 3), pracownik nie jest w stanie samodzielnie wykonywać pracy kiedy:
- Nie przeszedł szkolenia w ogóle.
- Jest w trakcie szkolenia (ma oznaczone 25% umiejętności).
- Ma 50% umiejętności, co oznacza, że potrafi wykonywać operację, ale cały czas pod kontrolą przełożonego. Z tego też powodu instruktaż nadal trwa, a pracownik nie jest całkowicie samodzielny.
Natomiast jako pełnoprawnego pracownika do wykonania pracy uznaje się operatora, który:
- Ma 75% umiejętności, co oznacza, że przeszedł szkolenie i samodzielnie może pracować na stanowisku pracy.
- Może szkolić (100% umiejętności), co oznacza, że poza wykonywaniem pracy, operator może szkolić innych operatorów (posiada wiedzę jak to robić).
Dla przykładu operacja czyszczenia maszyny ma określony cel w liczbie 7 pracowników, którzy powinni potrafić ją wykonywać. Ten cel jest osiągnięty. Ponadto dwóch z tych pracowników może również szkolić innych operatorów. Zupełnie inna sytuacja jest ze smarowaniem maszyny. Tam cel został określony w liczbie 4 pracowników, a operację tą potrafi wykonywać tylko 2 pracowników. Macierz kompetencji, aby mógł działać w praktyce, musi mieć określone cele dla każdego pracownika. Dzięki nim wiadomo kogo należy szkolić i z jakiej operacji. Zalecam zawsze rozpocząć proces standaryzacji od opracowania narzędzia zwanego własnie macierz kompetencji, bo ono nie tylko wskazuje luki kompetencyjnej, ale określa dla których operacji powinno zacząć się przygotowywać Instrukcje Pracy Standaryzowanej jako pierwsze.
Podsumowanie
Opracowanie macierzy kompetencji stanowi początek we wdrażaniu procesu autonomicznej konserwacji maszyn. Macierz kompetencji wskazuje luki kompetencyjne wśród pracowników, pozwala wybrać operacje do standaryzacji oraz wyznaczyć zarówno trenerów wewnętrznych, jak i osoby, które muszą przejść trening. Po opracowaniu Instrukcji Pracy Standaryzowanej dla poszczególnych operacji i przeszkoleniu z nich pracowników w oparciu o metodę TWI Instruowanie Pracowników, należy utrzymać system poprzez kontrolę pracowników. W szczupłym zarządzaniu narzędziem wspierającym utrzymanie poszczególnych systemów jest audytowanie. Audyty to jednak nie tradycyjnie rozumiana kontrola pracowników. To narzędzie doskonalące procesy. Najważniejsza zasada audytowania brzmi: zawsze wiń procesy, nigdy nie wiń ludzi. O tym, jak utrzymywać autonomiczną konserwację dowiesz się w następnym numerze magazynu. To ostatni krok w działaniach zarządczych przy wdrażaniu autonomicznej konserwacji.
LITERATURA
- Griffin R., 2013, Management, Texas A&M University, South – Western, USA
- Horbal R., Misiurek B., 2009, Lepsza wydajność dzięki szkoleniom stanowiskowym metodą TWI, MM Magazyn Przemysłowy, nr 8/9, s. 44-47
- Horbal R., Misiurek B., 2009, Rozwój umiejętności mistrzów i brygadzistów wg metody TWI. Szkolenie podwładnych, Zarządzanie Jakością, nr 1, s. 27-29, s. 31-35
- Portal Internetowy LeanTrix, stan na 04.01.2016, link: https://leantrix.com/pl/o-twi/
- Liker J., Meier D., 2008, Toyota Talent. Rozwijaj swoich pracowników na sposób Toyoty, MT Biznes, Warszawa
- Misiurek B., 2015, Metodyka standaryzacji autonomicznych procesów eksploatacyjnych zorientowana na poprawę efektywności maszyn zautomatyzowanych, Praca doktorska, Uniwersytet Technologiczny we Wrocławiu
- Misiurek B., 2016, Standardized Work with TWI, Productivity Press, New York
Autor: dr inż. Bartosz Misiurek, CEO LeanTrix
Artykuł opublikowano w magazynie Służby Utrzymania Ruchu (Styczeń – Luty 2016)
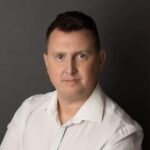
Jestem popularyzatorem Lean Management oraz programu Training Within Industry. Jestem praktykiem. Współtworzę wiele startupów. Od 2015 roku jestem CEO w Leantrix - czołowej firmie z zakresu konsultingu Lean w Polsce, która począwszy od 2024 roku organizuje jedną z największych konferencji poświęconych szczupłemu zarządzaniu w Polsce - Lean TWI Summit. Od 2019 roku jestem CEO w firmie Do Lean IT OU zarejestrowanej w Estonii, która tworzy software etwi.io używany przez kilkadziesiąt firm produkcyjnych i usługowych w Europie i USA.