W artykule poruszono problematykę bezpieczeństwa pracy. Opisano w jaki sposób metoda TWI Bezpieczeństwo Pracy wpływa na poprawę bezpieczeństwa na halach produkcyjnych. Przedstawiono statystyki wypadków w polskich przedsiębiorstwach. Opracowano model identyfikacji zagrożeń i ich eliminacji.
Czy problem zapewniania bezpieczeństwa pracy na hali produkcyjnej jest naprawdę ważny?
W ostatnich latach wiele polskich przedsiębiorstw zaczęło wspierać swoistą „modę” na poprawę bezpieczeństwa pracy. Przyczyn takiego zachowania może być wiele, jednak dwie główne które nasuwają się same to: odpowiedzialność przełożonych za bezpieczeństwo pracowników jest zapisane prawnie w naszym ustawodawstwie, drugim elementem jest przejmowanie wzorców przez polskich menedżerów, którzy szlifowali swoje umiejętności w zagranicznych korporacjach. Obserwacje w przemyśle ciągle potwierdzają, że w wielu firmach nadal mamy podejście według tradycyjnego modelu, w którym „produkcja” jest od produkowania, a od bezpieczeństwa są służby BHP. Taki model ma wiele wad ponieważ z pewnością specjaliści z zakresu BHP posiadają olbrzymią wiedzę w temacie bezpieczeństwa pracy, ale zazwyczaj nie są blisko procesu produkcyjnego. Często nie są w stanie ogarnąć swoją opieką i wiedzą operatorów ponieważ często nadzór jednego pracownika BHP odbywa się nad grupą nawet kilkuset osób. Kto wobec tego powinien być odpowiedzialny w firmie za identyfikowanie zagrożeń na hali produkcyjnej oraz projektowanie środków zaradczych? Przeanalizujmy kilka faktów.
Analizując dane Głównego Urzędu Statystycznego (zwanego dalej GUS) w pierwszych kwartałach 2009 i 2010 roku w naszym kraju zostało poszkodowanych odpowiednio 11382 i 18139 osób. Wg GUS wypadki, w których uczestniczyły te osoby, zostały podzielone na trzy kategorie: wypadki śmiertelne, ciężkie i lekkie. Liczbę wypadków w poszczególnych kategoriach w latach 2009 i 2010 pokazano na rys.1.
Rys. 1. Liczby osób poszkodowanych w wypadkach przy pracy w pierwszych trzech kwartałach 2009 i 2010 roku [opracowanie własne na podstawie 1].
Nie są to jednak pełne dane. Należy uzupełnić je o informacje dotyczące długości trwania niezdolności do pracy, która powstała jako ich skutek. Wówczas dopiero uzyskamy pełny obraz. Pierwszy kwartał 2009 roku przyniósł 326 255 dni niezdolności do pracy, co przekłada się na blisko 894 lata! Ten sam okres 2010 roku z wartością 505 314 dni daje bez mała 1 385 lat niezdolności do pracy. Te dane to tylko statystyka. Nie ukazują one skutków społecznych. W każdej liczbie ukrywa się cierpienie i ból człowieka, związane z nimi problemy i pogorszenie sytuacji materialnej często całych rodzin.
Skąd wobec tego biorą się te wszystkie wypadki? Skąd tak drastyczne liczby?
Wzorując się na badaniach przeprowadzanych przez największych ekspertów w dziedzinie bezpieczeństwa pracy, przyczyny powstawania wypadków można podzielić na dwie główne kategorie [2]:
- błędy człowieka,
- problemy techniczne.
W grupie „błędy człowieka” najważniejsze czynniki powodujące wypadki są związane z nieprzydatnością (ewentualnie niewydolnością) fizyczną lub umysłową, nieuwagą bądź nieostrożnością, braku odpowiedniego szkolenia, brakiem dozoru. Kolejna kategoria „problemy techniczne” w uproszczeniu jest sprowadzana do wad maszyn i urządzeń, bądź ich uszkodzeń lub awarii. Analizując przyczyny źródłowe wypadków na hali produkcyjnej opublikowane przez GUS dojdziemy do zatrważającego wyniku, że 90% wypadków następuje wskutek błędu człowieka, a pozostałe 10% jest związane z problemami technicznymi (rys. 2).
Rys. 2. Przyczyny źródłowe wypadków na halach produkcyjnych [opracowanie własne na podstawie 2].
Dane z hal produkcyjnych mają swoje odzwierciedlenie w naszym życiu codziennym. W popularnej akcji pod hasłem: „Zatrzymaj się i żyj” promującej bezpieczne przejazdy przez tory kolejowe kierowców próbuje się nakłonić do zmiany nawyków poprzez dane statystyczne, które mówią, że ponad 93% wypadków na przejazdach spowodowanych było przez nieostrożność kierowców [3]. Podobnie z wypadkami na drogach. Zastanów się ile z nich to wina zbyt brawurowej jazdy albo nieprzestrzegania przepisów przez kierowców, a ile wypadków jest wynikiem przestającego nagle działać układu hamulcowego?
Poprawa bezpieczeństwa pracy na hali produkcyjnej musi zacząć się od oddziaływania na świadomość pracowników.
Kto powinien być odpowiedzialny w firmie za tworzenie bezpiecznego środowiska pracy?
Przedstawione powyżej dane jednoznacznie podpowiadają, że za poprawę bezpieczeństwa pracy powinni być odpowiedzialni bezpośredni przełożeni pracowników produkcyjnych. Tą grupę stanowią przede wszystkim liderzy, mistrzowie i kierownicy tzw. średniego szczebla. Dodatkowo osoby odpowiedzialne za poziom bezpieczeństwa w firmie również powinny być nadzorowane przez swoich przełożonych, tak aby dawali dobry przykład operatorom i nie popełniali najczęściej pojawiających się błędów w ich pracy:
- Przełożeni nie dają dobrego przykładu podwładnym.
- Przełożeni nie instruują każdego pracownika odnośnie zasad bezpieczeństwa na jego stanowiskach pracy, bądź wykonują to w sposób nieodpowiedni.
- Przyrządy i narzędzia mające zapewniać bezpieczeństwo pracy nie są wykorzystywane poprawnie.
- Pojawiają się odstępstwa od zasad bezpieczeństwa, które na które przełożeni „przymykają oko”.
Model tradycyjny, w którym poziom bezpieczeństwa pracy jest odpowiedzialnością specjalistów ds. BHP nie sprawdza się. Potwierdzają to dane statystyczne. W nowoczesnej organizacji każda zmiana powinna rozpoczynać się od audytu BHP, każde stanowisko powinno mieć przeprowadzoną ocenę ryzyka, ale nie przez specjalistów BHP, tylko przez bezpośrednich przełożonych. To oni mają największą wiedzę na temat zagrożeń na stanowisku pracy. W takim modelu cel jest jeden: ZERO WYPADKÓW.
Jak poprawiać bezpieczeństwo pracy na stanowiskach produkcyjnych?
Problem bezpieczeństwa pracy wydaje się być „świeżym” tematem. Jednak korzenie jego rozwoju sięgają lat 40. ubiegłego wieku, kiedy to w ramach programu Training Within Industry (z ang. Szkolenia dla przemysłu, zwany dalej TWI) zostały rozwinięte trzy umiejętności jakie powinien mieć bezpośredni przełożony [4]:
- Instruowanie Pracowników (zwaną dalej IP)
- Doskonalenie Metod Pracy (zwaną dalej MP)
- Poprawa Relacji z Pracownikami (zwaną dalej RP)
Twórcy programu TWI szybko zdali sobie sprawę, że nie ma możliwości, aby bezpośredni przełożony skutecznie zarządzał swoim obszarem pracy kiedy nie jest on bezpieczny. Nie ma możliwości osiągnięcia stabilizacji procesu bez poprawy bezpieczeństwa. Dlatego parę lat po stworzeniu modelu trzech głównych umiejętności dobrego przełożonego opracowana czwartą metodę, która miała wyćwiczyć w przełożonych umiejętność kreowania bezpiecznego środowiska pracy (rys. 3.).
Skuteczny przełożony | ||
---|---|---|
Umiejętność Instruowania Pracowników |
Umiejętność doskonalenia Metod Pracy |
Umiejętność budowania dobrych Relacji z Pracownikami |
Zapewnienie Bezpieczeństwa Pracy |
Rys. 3. Umiejętności jakie powinien posiadać skuteczny (dobry) przełożony [opracowanie własne na podstawie: 4]
TWI Bezpieczeństwo Pracy stało się fundamentem całego programu, który przyniósł olbrzymie korzyści w USA podczas II Wojny Światowej. Był on opracowany szczególnie po to, aby efektywnie wdrażać do przemysłu zbrojeniowego kobiety. Było to spowodowane tym, że wielu mężczyzn musiało wstąpić do wojska ze względu na zbliżającą się wojnę. Wdrożenie metod TWI dało nadspodziewanie dobre rezultaty, według raportu sporządzanego w ramach programu w 1945 roku (przeanalizowano 600 uczestniczących w programie firm) [4]:
- 100% uczestniczących firm skróciło czas szkolenia nowych pracowników o 25% lub więcej,
- 86% firm zwiększyło wydajność o 25% lub więcej,
- 88% firm zredukowało pracochłonność na produkt o 25% lub więcej,
- 55% firm zredukowało braki o ponad 25%,
- 100% firm zredukowało reklamacje o ponad 25%.
Mimo takich dobrych rezultatów po wojnie stopniowo zarzucono dalszy rozwój programu TWI w USA, natomiast przekazano go Japonii w ramach planu Marshalla. Dopiero w ostatnich latach, dzięki badaniom nad koncepcją Lean Management, program TWI odrodził się w Stanach Zjednoczonych. Metoda TWI Bezpieczeństwo Pracy opiera się silnie na badaniach słynnego naukowca amerykańskiego Herbert William Heinrich, który nazywany jest pionierem bezpieczeństwa pracy. Żył on na przełomie XVIII i XIX wieku. Główną konkluzją badań Heinricha było stwierdzenie, iż koncentrowanie się jedynie na sprawnym reagowaniu na występujące zdarzenia wypadkowe nie przyniesie poprawy w zakresie bezpieczeństwa. W grupie 330 zdarzeń tego samego rodzaju, 300 nie powoduje urazu – są to zdarzenia potencjalnie wypadkowe, 29 powoduje uraz lekki, a jeden z tych urazów może być ciężki i skutkować nieobecnością w pracy (rys. 4). Różnica pomiędzy tymi grupami polega wyłącznie na szczęściu. Kolokwialnie można zobrazować to w ten sposób: ktoś kto miał tylko zdarzenia potencjalnie wypadkowe miał szczęście, a ten kto miał wypadek ciężki miał pecha.
Rys. 4. Statystyczny rozkład zdarzeń związanych z bezpieczeństwem dla jednej osoby [opracowanie własne na podstawie 2].
Już pobieżna analiza tego modelu wyznacza nowy kierunek działania – koncentracja powinna spoczywać na sytuacjach potencjalnie niebezpiecznych. Jeśli zmniejszymy ich ilość, tym samym obniżymy prawdopodobieństwo wystąpienia wypadków. Potrzebna jest tutaj profilaktyka. I jest ona głównym tematem związanym z doskonaleniem Bezpieczeństwa Pracy. Każda z metod programu TWI opiera się na 4 krokach. Podobnie metoda TWI Bezpieczeństwo Pracy. Postępowanie według tej metody gwarantuje, że stanowisko zostanie przeanalizowane pod względem potencjalnych zagrożeń.
Działanie metody TWI Bezpieczeństwo Pracy
KROK 1. IDENTYFIKACJA MIEJSC BĘDĄCYCH PRZYCZYNAMI ZAGROŻEŃ
Celem tego kroku jest przeanalizowanie stanowiska pod względem wyszczególnienia zagrożeń. Bezpośredni przełożony wykonując krok 1. metody powinien udać się na analizowane stanowisko i postępować według schematu zobrazowanego na rys. 5.
Rys.5. Schemat postępowania w kroku 1. metody TWI Bezpieczeństwo Pracy
Pierwszym krokiem podczas procesu doskonalenia wg TWI Bezpieczeństwo Pracy jest gruntowna identyfikacja zagrożeń w miejscu ich występowania – odbywać się to musi w rzeczywistym miejscu pracy. Przełożony musi zapoznać się z jego historią – szuka danych i faktów na temat przeszłości, wypadków i zagrożeń które miały miejsce w danym obszarze produkcyjnym, bądź które są z nim związane. Celem tego etapu jest zdobycie gruntownej wiedzy na temat panujących warunków na stanowisku. Po uzyskaniu obrazu dotyczącego historii, przełożony musi dokonać przeglądu pod kątem przepisów i standardów pracy. Musi być przy tym bardzo sceptyczny. Każdy standard powinien być ściśle zweryfikowany przez operatora. Przełożony musi się dowiedzieć czy jest to prawdziwy standard wg którego operatorzy pracują, czy tylko „martwy” dokument, który zawisł przy stanowisku. Taka analiza wymaga przeprowadzenia wywiadu z pracownikiem – to kolejny etap identyfikacji zagrożeń. To właśnie pracownicy najlepiej znają swoje stanowisko pracy i bardzo szybką mogą wskazać przełożonemu miejsca szczególnie niebezpieczne.
Po tym etapie przełożony wraz z operatorami powinien przeanalizować stanowisko pod względem istniejących zagrożeń. Na tym etapie również należy być bardzo sceptycznym. Przełożony powinien szukać zagrożeń w obszarze pracy człowieka, jak i pracy maszyny. Pomocnym narzędzie do gruntownej analizy zagrożeń może być arkusz Identyfikacji Zagrożeń (zwany dalej arkuszem IZ) (tab. 1). Mało doświadczony w zakresie BHP lider albo mistrz może nie być odpowiednio „wyczulony” na zagrożenia. Dzięki arkuszowi IZ musi on postępować wg wskazanych punktów, które pokazują najczęściej występujące zagrożenia. Lista zagrożeń powstała w oparciu o warsztaty praktyczne przeprowadzone w kilkudziesięciu firmach produkcyjnych na terenie Polski. Jeżeli przełożony zidentyfikuje dane zagrożenie na stanowisku oznacza na arkuszu IZ stwierdzenie „Tak” przy danym zagrożeniu, opisuje to zagrożenie oraz zapisuje czy są już obecnie na tym stanowisku wprowadzone jakiekolwiek środki zaradcze dla tego zagrożenia. Arkusz IZ stanowi dla przełożonego w pewnym rodzaju listę sprawdzającą.
L.P. | Typ zagrożenia | Czy zagrożenie występuje? | Opis zagrożenia | Obecne sposoby eliminacji zagrożenia |
---|---|---|---|---|
1 | Zagrożenia związane z ergonomią pracy | Tak / Nie | ||
2 | Zagrożenia elementami ruchomymi i luźnymi | Tak / Nie | ||
3 | Nieporządek na stanowisku – brak 5S | Tak / Nie | ||
4 | Ostre krawędzie | Tak / Nie | ||
5 | Dźwiganie/przenoszenie sprzętu | Tak / Nie | ||
6 | Sprężone powietrze | Tak / Nie | ||
7 | Zagrożenia związane z przemieszczaniem się ludzi | Tak / Nie | ||
8 | Zagrożenia związane z przemieszczaniem towarów (wózki widłowe, inne…) | Tak / Nie | ||
9 | Zagrożenia związane z upadkiem z wysokości | Tak / Nie | ||
10 | Zagrożenie związane ze śliskimi, nierównymi powierzchniami | Tak / Nie | ||
11 | Zagrożenie porażeniem prądem elektrycznym | Tak / Nie | ||
12 | Zagrożenie pożarem i/lub wybuchem | Tak / Nie | ||
13 | Awarie maszyny | Tak / Nie | ||
14 | Awaria budynku lub instalacji związanych z budynkiem | Tak / Nie | ||
15 | Defekt produktu | Tak / Nie | ||
16 | Hałas | Tak / Nie | ||
17 | Promieniowanie optyczne widzialne | Tak / Nie | ||
18 | Wibracja (ogólna i oddziałująca przez kończyny górne) | Tak / Nie | ||
19 | Pole elektrostatyczne | Tak / Nie | ||
20 | Pyły przemysłowe | Tak / Nie | ||
21 | Substancje toksyczne | Tak / Nie | ||
22 | Substancje drażniące | Tak / Nie | ||
23 | Obciążenia fizyczne statyczne (praca w niedogodnej pozycji, powtarzanie monotypowych czynności) | Tak / Nie | ||
24 | Obciążenia fizyczne dynamiczne (praca o znacznym wydatku energetycznym) | Tak / Nie | ||
25 | Inne…. | Tak / Nie |
Tab. 1. Arkusz Identyfikacji Zagrożeń [opracowanie własne].
Po przeprowadzeniu na stanowisku identyfikacji zagrożeń przełożony może przejść do 2. kroku metody TWI BP – określenie środków zaradczych.
KROK 2. – OKREŚLENIE ŚRODKÓW ZARADCZYCH
Głównym celem tego kroku jest dopasowanie do zidentyfikowanych zagrożeń odpowiednich środków zaradczych. Analiza powinna być prowadzona przy udziale pracowników, którzy dobrze znają aspekty swojego miejsce pracy. Najbardziej efektywnym środkiem zaradczym jest eliminacja zagrożenia, najmniej skutecznym są środki ochrony osobistej (rys. 6).
Rys. 6. Hierarchia skuteczności środków zaradczych wg TWI Bezpieczeństwo Pracy
Najlepiej hierarchię zobrazowaną na rysunku 6 można zrozumieć opisując warunki na drodze po której poruszają się samochody. Wyobraźmy sobie, że w pewnej małej wiosce, przez którą biegnie tylko jedna droga, dzieci bawią się blisko domów, a co za tym idzie blisko tej drogi. Wioska ta leży przy drodze krajowej więc ruch na niej jest bardzo duży. Zagrożeniem w tej wiosce są pędzące samochody, które mogą potrącić bawiące się dzieci. Wdrażając środki zaradcze najbardziej skutecznym z nich jest eliminacja. W przedstawionym przykładzie wyeliminować zagrożenie można budując obwodnicę wioski i przerzucając cały ruch poza teren zabudowany. Jest to najbardziej skuteczne rozwiązanie. Kolejnym środkiem zaradczym w hierarchii są środki techniczne, które należy rozumieć jako wdrożenie pewnych rozwiązań, które minimalizują zagrożenie. Jeżeli nie dałoby się wybudować obwodnicy albo zajmie to parę lat należy zastanowić się jaki środek techniczny zastosować, aby zmniejszyć zagrożenie. Dobrym przykładem środka technicznego przy analizowanym zagrożeniu może być zamontowanie świateł przy przejściach, postawienie foto radaru albo wybudowanie barierek oddzielających chodnik od drogi. Może być to bardzo skuteczny środek zaradczy, ale należy pamiętać, że zagrożenie nadal istnieje. Przecież bawiące dzieci mogą przeskoczyć przez barierki. Następnym w hierarchii środkiem zaradczym są ostrzeżenia. W naszym przykładzie mogą to być znaki informujące kierowcę o miejscu często uczęszczanym przez dzieci. Na pewno taki środek zaradczy pomoże, ale jego skuteczność zależna będzie od tego jak kierowca się do niego ustosunkuje. Kolejnym środkiem zaradczym są szkolenia. W analizowanym przykładzie mogą one dotyczyć zarówno dzieci, jak i kierowców. Celem Szkoleń jest oddziałowywanie na świadomość. W Polsce pomimo tego, że takie szkolenia się odbywają nadal dochodzi do wielu wypadków głównie wynikających z nieuwagi kierowcy albo pieszego. To potwierdza niską skuteczność instruktażu jako środka zaradczego chociaż z pewnością jest to ważny element. Najmniej skutecznym środkiem zaradczym są środki ochrony osobistej. Pomimo tego, że dzieci ubrane zostaną koszulki odblaskowe oraz kaski szanse na bezszkodowe wyjście z kolizji z autem są dla nich niewielkie. Środki ochrony osobistej są ważnym elementem prewencyjnym, ale z pewnością najmniej skutecznym.
Praktyka produkcyjna pokazuje, że większość firm zaczyna wdrażać swój system bezpieczeństwa od środków ochrony osobistej zapominając, że najbardziej skuteczne jest wyeliminowanie zagrożenia. Jeżeli eliminacja nie jest możliwa to można łączyć ze sobą pozostałe cztery środki zaradcze wychodząc założenia, że im więcej środków zaradczych tym szansa wypadku mniejsza. Dobrane metody oddziałowywania na zagrożenia należy zweryfikować z istniejącą polityką, procedurami bądź z wymogami prawnymi. Jeśli spodziewamy się, iż niektóre z proponowanych działań nie zostaną zrealizowane, dobrze jest opracować plan awaryjny, który będzie realizowany na wypadek niepowodzenia.
KROK 3. WPROWADZANIE W ŻYCIE DZIAŁAŃ ZARADCZYCH
Trzeci krok polega na wprowadzeniu w życie środków zaradczych. Należy tutaj szczególny nacisk położyć na samodzielną pracę. Opiera się to na prostym założeniu, że przełożonemu najbardziej zależy na skutecznym wdrożeniu działania. Gdy nie jest możliwe, aby przełożony samodzielnie wdrożył w życie opracowany w kroku 2. środków zaradczych należy prosić o pomoc mistrza, kierownika, czy nawet dyrektora. Musi on dowiedzieć się jakie problemy były związane z realizacją działania. Z pewnością jego pomoc będzie nieoceniona w kwestii doboru współpracowników, którzy mogą wspierać mistrza, czy kierownika we wdrażaniu. Wprowadzone w życie działania dzielimy na natychmiastowe oraz długoterminowe. Działania natychmiastowe to te, które należy wdrożyć od razu ponieważ na stanowisku jest zagrożenie, które musi być opanowane. Działania długoterminowe wymagają zazwyczaj dogłębnej analizy.
KROK 4. KONTROLA REZULTATÓW
Ostatni, czwarty krok jest związany z oceną osiągniętych wyników. Niestety jest on bardzo często zaniedbywany bądź pomijany. Audyty, reagowanie na odstępstwa, nieustanna praca z ludźmi i angażowanie szeregowych pracowników w cykliczne kontrole stanu bezpieczeństwa nie powinny nigdy mieć końca. Im więcej zagrożeń, wypadków „o włos” i incydentów zostanie zidentyfikowanych i wyeliminowanych, tym niższe jest prawdopodobieństwo wystąpienia poważnych wypadków i nieszczęśliwych zdarzeń. To w interesie najwyższego kierownictwa jest przestrzeganie czy system bezpieczeństwa działa w firmie. Im mniej wypadków tym większa wydajność procesu produkcyjnego.
Podsumowanie
Problem bezpieczeństwa pracy jest obecnie „modnym” tematem w wielu firmach. Zwiedzając fabryki coraz częściej można zaobserwować kolorowe plakaty promujące bezpieczeństwo pracy, informacje o konieczności stosowania środków ochrony osobistej, informacje o zagrożeniach. Skuteczny system bezpieczeństwa pracy to jednak przede wszystkim identyfikacja zagrożeń i próba ich eliminowania, analizowanie stanowiska pracy przez brygadzistów i mistrzów we współpracy z operatorami. Skuteczny system bezpieczeństwa to proces ciągłego doskonalenia. Nie wystarczy tylko szkolić pracowników i wyposażać ich w środki ochrony osobistej. Należy pracować z nimi nad eliminacją zagrożeń, a jeżeli nie jest to możliwe, to nad projektowaniem możliwie najlepszych środków technicznych, które mogą uchronić ich przez zagrożeniem. Należy założyć, że na każdym stanowisku są zagrożenia. Ważne żeby je identyfikować zgodnie ze słynnym cytatem: „Brak problemów to największy problem”.
Literatura
[1] Oficjalne dane Głównego Urzędu Statystycznego.
[2] Heinrich H. W., Industrial Accidents Prevention. New York, Toronto, London, Mc Graw Hill Book Company, Inc. 1959
[3] http://www.bezpieczny-przejazd.pl/dla-mediow/informacja-prasowa/
[4] Doskonalenie niezbędnych umiejętności przełożonych – Program TWI, Graupp P., Wrona R.J., Lean Enterprise Institute Polska, 2011, Wrocław
Informacja o artykule:
Artykuł opublikowany w magazynie Zarządzanie Jakością (nr 04/2011)
Autor:
Bartosz Misiurek
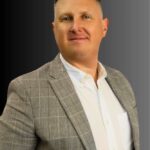
Jestem popularyzatorem Lean Management oraz programu Training Within Industry. Jestem praktykiem. Współtworzę wiele startupów. Od 2015 roku jestem CEO w Leantrix - czołowej firmie z zakresu konsultingu Lean w Polsce, która począwszy od 2024 roku organizuje jedną z największych konferencji poświęconych szczupłemu zarządzaniu w Polsce - Lean TWI Summit. Od 2019 roku jestem CEO w firmie Do Lean IT OU zarejestrowanej w Estonii, która tworzy software etwi.io używany przez kilkadziesiąt firm produkcyjnych i usługowych w Europie i USA.