Zero awarii, zero braków, zero błędów, wysoki wskaźnik OEE – to marzenie każdego kierownika produkcji i każdej służby utrzymania ruchu. Dlaczego wobec tego w tak wielu firmach TPM po fazie początkowego entuzjazmu po prostu umiera? W artykule w ciekawy sposób opisano historię pewnego wdrożenia TPM. Przedstawiono problemy z jakimi napotkały się osoby wdrażające ten program. Zdefiniowano przyczyny tych problemów i przedstawiono praktyczne rozwiązania, które mogą być inspiracją dla każdej firmy wdrażającej program TPM.
System TPM (ang. Total Productive Maintenance, w tłumaczeniu – kompleksowe produktywne utrzymanie ruchu) to opracowany w zakładach Toyoty zestaw technik, pozwalający na utrzymanie stabilnie pracującego, niezawodnego paku maszynowego. System TPM polega na obsłudze konserwacyjnej maszyn i urządzeń, realizowanej wewnątrz przedsiębiorstwa przez operatorów i personel utrzymania ruchu. Dzięki odpowiedniemu zorganizowania współpracy między UR a produkcją pozwala na utrzymanie w ruchu nawet mocno już wyeksploatowanego parku maszynowego i znaczne zmniejszenie takich zagrożeń ciągłości produkcji jak awarie czy nieplanowane przestoje.
Zero awarii, zero braków, zero błędów, wysoki wskaźnik OEE – to marzenie każdego kierownika produkcji i każdej służby utrzymania ruchu. Dlaczego wobec tego w tak wielu firmach TPM po fazie początkowego entuzjazmu po prostu umiera?
Historia pewnego wdrożenia TPM
Jestem kierownikiem produkcji. Pół roku temu podjęliśmy w firmie decyzję o wdrożeniu TPM. Rozpoczęliśmy warsztatami, w czasie których gruntownie wyczyściliśmy kilka maszyn, znaleźliśmy i pooznaczaliśmy po kilkadziesiąt usterek na każdej z nich. Wiele z nich udało nam się stosunkowo szybko usunąć. Pozostałe rozciągnęły się w czasie, ale ostatecznie też się z nimi uporaliśmy. Warsztaty zadziałały bardzo dobrze na poprawę komunikacji między produkcją a SUR, wiele się od siebie dowiedzieliśmy zapewne dzięki temu, że lepiej poznaliśmy nawzajem swoje stanowiska i priorytety. Można było zauważyć wzrost świadomości i zaangażowania w obu zespołach. Kolejnym krokiem było ustalenie zakresu działań w ramach autonomicznej konserwacji dla operatorów. Wybraliśmy czynności, ustaliliśmy, że będziemy na to poświęcać 20 min na zmianę, opracowaliśmy instrukcje. Ten czas i tak był dostępny wcześniej, ale nikt tak naprawdę nie wiedział co kto wykonywał w tych 20 minutach. Wystartowaliśmy z programem. Niestety niemal natychmiast zaczęły pojawiać się problemy. Mistrzowie zgłaszali mi, że czynności związane z autonomiczną konserwacją pochłaniają więcej czasu niż uzgodnione 20 min. Czasem podawali to jako powód mniejszego zejścia z maszyny. Utrzymanie Ruchu z kolei narzekało, że operatorzy rezygnują z wykonania niektórych czynności, które sobie dowolnie losowo wybierają, kierując się głównie własną wygodą i tłumacząc się „że i tak przecież nie są w stanie zrobić tego wszystkiego”. Inni pracownicy zaś z powodu pośpiechu uzgodnione czyszczenie i konserwację wykonywali po łebkach. Musieliśmy jakoś zareagować na te problemy, zwłaszcza że kierownictwo bardzo naciskało, aby wdrożenie TPM zakończyło się sukcesem. Po ciężkiej i burzliwej dyskusji zdecydowaliśmy się zmniejszyć zakres Autonomicznej Konserwacji. Ze strony SUR pojawiły się głosy, że po takim okrojeniu to „cała zabawa przestaje mieć sens”. Z drugiej strony mistrzowie wytoczyli argument, że „tracą 20 min co zmianę na robienie roboty SUR a i tak nigdy nie odzyskają tego na produkcję”. Nie trafiało do nich zupełnie, że dzięki temu będą mieli mniej awarii i spokojniejszą pracę („przecież awarie to sprawa SUR”).
W tej chwili sprawa TPM utknęła w martwym punkcie i po fazie początkowego entuzjazmu stała się główną kością niezgody w stosunkach między SUR a produkcją.
Zapewne wiele osób w tej historii odnajdzie odbicie swojej sytuacji. Jest to typowy rozwój wypadków, który stał się udziałem dziesiątek firm produkcyjnych mierzących się z niełatwym zadaniem wdrażania systemu TPM. Dlaczego ta historia potoczyła się akurat w ten sposób?
Problem nr 1
Konflikt interesów między działem Służb Utrzymania Ruchu (SUR) a Działem Produkcji.
Opis problemu
W każdej firmie produkcyjnej, każdy z działów ma swoje własne kluczowe wskaźniki (ang. KPI), z których jest rozliczany przed najwyższym kierownictwem. W przypadku działu SUR są to zazwyczaj takie wskaźniki jak MTBF (średni czas pomiędzy awariami) oraz MTTR (średni czas potrzebny na naprawę awarii). Dział Produkcji zazwyczaj rozliczany jest m. in. z wydajności, produktywności oraz jakości. Oczywiście wskaźników KPI dla każdego działu może być o wiele więcej. Jest jednak pewna zasada: są one różne dla różnych działów. W większości przypadków wdrażanie systemu TPM zaczyna się od zaangażowania operatorów w działania czyszczące na maszynie, a następnie również w działania konserwujące. Jest to tak zwana autonomiczna konserwacja. Niestety to zaangażowanie wymaga tego, aby przeznaczyć przykładowe 20 minut na każdą zmianę produkcyjną na wykonanie działań autonomicznej konserwacji w czasie, w którym maszyna zazwyczaj musi być wyłączana z ruchu. W tym momencie pojawia się konflikt interesów, ponieważ pracownicy produkcyjni, którzy przypisani są kosztowo do Działu Produkcji, wykonują zadania, które wpływają na poprawę wskaźników KPI działu SUR. Równocześnie obniżają się wskaźniki KPI Działu Produkcji ponieważ we wspomnianych wyznaczonych 20 minutach wytwarzanie na maszynie zostaje zatrzymane, a w konsekwencji spada liczba wyprodukowanych wyrobów na zmianę.
Przyczyna nr 1
Wskaźniki KPI są przypisywane do poszczególnych działów, a nie do konkretnej linii produkcyjnej bądź obszaru produkcji.
Rozwiązanie
Sposobem eliminacji tej przyczyny problemu może być wyznaczenie w firmie menadżera strumienia wartości, który odpowiedzialny jest za efektywność danej linii produkcyjnej albo danego obszaru produkcji. W tym rozwiązaniu sugerujemy odejście od tradycyjnego podziału na działy: SUR i Produkcję. W to miejsce zalecamy wyznaczenie określonej liczby strumieni wartości w fabryce, a następnie wyznaczenie dla tych strumieni menadżerów i ujednoliconych wskaźników KPI. Każdy strumień wartości ma te same wskaźniki KPI. Menadżer strumienia wartości powinien być zatem na równi rozliczany z awaryjności maszyn, jak i z liczby wyprodukowanych wyrobów. Menadżer strumienia wartości miałby pod sobą część mechaników oraz mistrzów, liderów i operatorów przypisanych do obszarów produkcyjnych w danym strumieniu wartości. Przed najwyższym kierownictwem menadżer strumienia wartości powinien rozliczać się z efektywności linii produkcyjnej czy też obszaru produkcji, a zatem zarówno z dostępności, wykorzystania, jak i jakości. W zależności od specyfiki firmy menadżer strumienia wartości może mieć pod swoją opieką np. dwie linie produkcyjne albo np. trzy obszary produkcji.
Przyczyna nr 2
Krótkoterminowe patrzenie na wyniki wskaźników KPI w przedsiębiorstwie.
Rozwiązanie
Rozwiązane przedstawione powyżej dla przyczyny 1 (powołanie menadżera strumienia wartości), pośrednio wpływa również na eliminację tej przyczyny. To właśnie w interesie menadżera strumienia wartości jest patrzenie na wyniki w ujęciu długoterminowym. Jeżeli taki menadżer jest rozliczany z efektywności wykorzystania linii produkcyjnej albo obszaru produkcji, to jest on zainteresowany redukcją czasu awarii, nawet kosztem krótkoterminowej straty wydajności. Świadomy menadżer strumienia wartości wie, że nakład na inwestycję, jaką jest poświęcenie czasu na autonomiczną konserwacją, z pewnością przełoży się na mniejszą liczbę awarii w przyszłości, a tym samym na większą wydajność. Tego faktu z pewnością świadomi są również wszyscy kierownicy Działu Produkcji w tradycyjnej strukturze produkcyjnej, ale oni również doskonale wiedzą, że działania związane z autonomiczną konserwacją w pierwszej kolejności wpłyną na poprawę wskaźników KPI działu SUR.
Problem nr 2
Czynności wykonywane przez operatorów w ramach autonomicznej konserwacji zajmują zbyt dużo czasu.
Opis problemu
Zanim jeszcze operatorom zostaną przydzielone konkretne czynności do wykonania w ramach autonomicznych przeglądów maszyny i zanim będzie można wymagać od nich ich prawidłowej realizacji, musi zostać podjętych szereg ustaleń i działań. Po pierwsze, należy określić zakres czynności oraz standard ich wykonywania. Jednym słowem należy opracować instrukcję, w której zapisany zostanie najlepszy znany i prawidłowy sposób czyszczenia, sprawdzania, smarowania i dokręcania kluczowych elementów dla danej maszyny. Kolejnym krokiem jest przeszkolenie operatorów, poparte procesem audytowania. Standard czynności konserwacyjnych, tak jak wspomniano, wspierają wizualne instrukcje, które pozwalają operatorom w krótszym czasie nauczyć się prawidłowego wykonywania czynności, a osobom nadzorującym skutecznie audytować proces autonomicznej konserwacji. Problem polega na tym, że mimo prawidłowego procesu wdrożenia autonomicznej konserwacji szybko okazuje się, że uzgodnione czynności zajmują operatorom więcej czasu niż jest na nie przeznaczone (przykładowo 15 czy 20 minut na zmianę). To z kolei powoduje, że operatorzy zaczynają sami ten problem „rozwiązywać”: nie wykonują wszystkich uzgodnionych czynności, odrzucając niejednokrotnie te najbardziej niewygodne lub nieważne z ich punktu widzenia, lub też wykonują wszystkie czynności, ale z powodu pośpiechu nieprawidłowo.
Przyczyna nr 1
Czynności jest za dużo, nie mają przypisanych priorytetów i częstotliwości wykonania.
Rozwiązanie
Naturalną skłonnością jest, żeby włączyć do czynności autonomicznej konserwacji „na wszelki wypadek” jak najwięcej punktów. Ograniczenia czasowe jednak w oczywisty sposób powodują, że zestaw czynności powinien być dokładnie przemyślany. Czynności do autonomicznej konserwacji dobiera się mając na uwadze, które z nich są najważniejsze oraz które z nich mają najwyższy priorytet. Następnie dla każdej czynności ustala się optymalną częstotliwość jej wykonywania, która powinna być zaznaczona na instrukcji. Czy te najmniej ważne w ogóle powinniśmy wykonywać? Z pewnością, ale może wystarczy, jeśli dokręcę przykładową śrubę to raz dziennie zamiast raz na zmianę? Ważne jest też, żeby czynności dobierać z punktu widzenia historii awarii („co sprawdzać, żeby ta awaria już nam się nie powtórzyła”), a nie estetyki maszyny („żeby maszyna była czysta”).
Przyczyna nr 2
W momencie ustalania zestawu czynności do autonomicznej konserwacji nie znamy prawdziwego czasu ich wykonania. Decydujemy o tym, co powinno być wykonane na podstawie szacunków, a nie rzetelnych empirycznych danych.
Rozwiązanie
Po ustaleniu standardu wykonywania czynności czyszczenia, sprawdzania, smarowania i dokręcania trzeba je przećwiczyć „na żywo” i zweryfikować pierwotne szacunki z rzeczywistym pomiarem wykonanym stoperem. Zebranie empirycznych danych z jednej strony pozwoli nam podjąć właściwą decyzję w danym konkretnym przypadku, które czynności mają wejść w skład autonomicznej konserwacji, a z drugiej ułatwi planowanie działań konserwacyjnych w przyszłości i ich standaryzowanie.
Przyczyna nr 3
Czynności zawierają wiele marnotrawstwa (np. chodzenia). Nikt nigdy nie przeprowadził analizy ile tak naprawdę w nich jest efektywnie zużytego czasu (ang. Value Adding – VA), a ile wszelkiego rodzaju nieefektywności (ang. Non-Value Adding – NVA). Nie było procesu usprawniania i eliminacji marnotrawstwa (np. metodą 5W1H). Komórki „Lean” odpowiedzialne w firmach za proces eliminacji marnotrawstwa, są zwykle przypisane personalnie do działu produkcji, a nie SUR. To powoduje, że komórki Lean często nie interesuje usprawnianie czynności obsługowych, skoro i tak jest na nie przeznaczonych 20 min (których produkcja nigdy nie odzyska na produkowanie). Działy SUR za to nie mają ani doświadczenia, ani kompetencji, żeby prowadzić tego rodzaju proces doskonalący.
Rozwiązanie
Czynności wykonywane w ramach AM powinny podlegać normalnemu procesowi doskonalenia jak każda inna praca produkcyjna czy logistyczna. Typowo 60-80% czasu przeznaczanego na autonomiczną konserwację pochłania marnotrawstwo (obchodzenie maszyny, żeby dojść do drugiej strony, schylanie się pod nią, wchodzenie na górę, żeby coś sprawdzić, odkręcanie osłon itp.) Wiele mówi już samo proste narysowanie diagramu spaghetti. Podobnie jak usprawnia się czynności wykonywane na stanowisku pracy poprzez analizę, zmianę kolejności wykonywania czynności, zmianę layotu, ułożenia narzędzi itp., tak też powinno wyglądać usprawnianie działań autonomicznej konserwacji. Otwiera to też ogromne pole do kreatywności operatorów i pomysłów usprawniających.
Podsumowanie
Z naszych wieloletnich praktycznych doświadczeń wynika, że system TPM jest narzędziem „miękkim” – to znaczy zależnym od czynnika ludzkiego i komunikacji między ludzkim. Jeżeli ktoś pierwszy raz spotyka się z definicją systemu TPM to z pewnością pomyśli od razu o mechanikach, czy operatorach pracujących na poprawę efektywności wykorzystania maszyn. Tak to bardzo ważny element TPM. Niemniej najważniejsze przy rozpoczynaniu wdrażania systemu TPM jest budowanie dobrej komunikacji i dokonanie rozsądnego podziału odpowiedzialności już na wczesnym etapie wdrożenia. Problemy pojawiające się na linii produkcja – służby utrzymania ruchu wynikają niejednokrotnie z przyczyn systemowych takich jak sposób rozliczania z osiągania celów i odpowiedzialności za wskaźniki. Z drugiej strony doskonalenie czynności obsługowych przy maszynie jest w wielu firmach „ziemią niczyją”, za którą nikt się nie czuje odpowiedzialny. Podjęcie tych tematów już na początku wdrożenia pozwala znacznie przedłużyć życie TPM w firmie, a tym samym zbliżyć się do celu zera strat, zera awarii i zera braków.
Informacje o artykule:
Artykuł opublikowano w magazynie Służby Utrzymania Ruchu (marzec – kwiecień 2015)
Autorzy:
Dr inż. Bartosz Misiurek, Zofia Maśluszczak
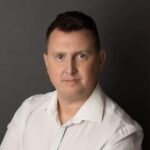
Jestem popularyzatorem Lean Management oraz programu Training Within Industry. Jestem praktykiem. Współtworzę wiele startupów. Od 2015 roku jestem CEO w Leantrix - czołowej firmie z zakresu konsultingu Lean w Polsce, która począwszy od 2024 roku organizuje jedną z największych konferencji poświęconych szczupłemu zarządzaniu w Polsce - Lean TWI Summit. Od 2019 roku jestem CEO w firmie Do Lean IT OU zarejestrowanej w Estonii, która tworzy software etwi.io używany przez kilkadziesiąt firm produkcyjnych i usługowych w Europie i USA.