Jeśli pracujesz w środowisku Lean, ale jeszcze nie słyszałeś o Trainig Within Industry (TWI), to prawdopodobnie wkrótce usłyszysz. TWI „bez wątpienia jest najbardziej skutecznym programem do celów szkoleniowych, jaki powstał w Stanach Zjednoczonych” [1]. Początki programu TWI sięgają II Wojny Światowej. Po wojnie stał się on nieodłączną częścią Toyota Production System (TPS). Dzisiaj program TWI odradza się w Ameryce Północnej, aby pomóc zwiększyć skuteczność szkoleń oraz usprawnić proces wdrożenia filozofii ciągłego doskonalenia Kaizen.
Niestety Amerykanie postrzegali TWI jedynie jako program wojenny, a nie jako stałe narzędzie do praktykowania. TWI zaczęło znikać z amerykańskich firm produkcyjnych przed końcem II Wojny Światowej jak tylko zwycięstwo nad wrogimi siłami wydawało się być przesądzone. Wszyscy zaczęli dostrzegać brak potrzeby dla kontynuowania tego programu. Spełnił one swoje oczekiwania, dlatego uznano go za zakończony.
Po wojnie program TWI przetransferowano do Japonii, kraju otwartego na rozwój i naukę, gdzie głównym obszarem rozwoju był przemysł. Program TWI szybko dostosowano do potrzeb japońskich firm i stał się on podstawą dla całego przemysłu w zakresie rozwoju pracowników. Poprzez stabilizację i standaryzację program TWI przyczynił się do poprawy jakości usuwając zmienność w pracach wykonywanych przez operatorów. W Toyocie, Taiichi Ohno, wraz z pozostałymi pracownikami, wdraża program TWI znany jako „J-Programs”. Program oparty o najlepsze doświadczenia pracowników. Program TWI stał się integralną częścią Systemu Produkcyjnego Toyoty (TPS). Sześćdziesiąt lat później karty z programu TWI (ang. Pocket Cards) zostają przetłumaczone z japońskiego na angielski. Ich form i budowa praktycznie nie różni się od kart używanych podczas II Wojny Światowej. Program TWI, który stał się częścią systemu TPS, a który był niedoceniony w świecie Zachodu, zaczął pisać nowy rozdział w historii Świata.
Obecnie wiele firm korzystających z narzędzi Lean pracuje również nad tym, aby stworzyć kulturę ciągłego doskonalenia wolną od „obwiniania” pracowników. Jednak praca w kulturze Lean nie jest łatwa do utrzymania, ponieważ nie każdy lubi pracować w określonym standardzie. W wyniku tego nie osiągamy korzyści, bo nie trzymamy idei płynącej z Kaizen. TWI pomaga uporządkować proces wdrożenia pracowników do pracy, przełamanie ich emocjonalnej niechęci do zgodnego ze standardem sposobu pracy – fundamentu Pracy Standaryzowanej. TWI „J-Programs” pozwalają ludziom z łatwością wdrożyć się w środowisko pracy, którego wcześniej nie znali. Japończycy nie nauczyli się od razu zasad Pracy Standaryzowanej. Taiichi Ohno poprzez doświadczenie i ciągłe eksperymenty stwierdził, że TWI pomaga przezwyciężyć opór i negatywne podejście ludzi do pracy. TWI „J-Programs” przynosi korzyści i rezultaty nawet jeżeli nie jest wdrażany razem z narzędziami Lean, tak jak miało to przecież miejsce w czasie II Wojny Światowej.
W skrócie
Training Within Industry (szkolenia w przemyśle), zakorzenione w programach szkoleniowych, powraca po kilkudziesięciu latach, jako dobrze działający program, który dawno temu stał się „ukrytą częścią” Toyota Production System. Wykwalifikowani pracownicy, którzy korzystają z metod TWI „J-Programs”, wykorzystują własne doświadczenia opisując swoją pracę poprzez Arkusze Podziału Pracy. Dzięki takiemu podejściu doświadczeni liderzy wzmacniają swoje relacje z pracownikami, którzy docelowo mogą podtrzymywać i rozwijać standardy pracy. Niezdolność do utrzymania standardów pracy jest jednym z głównych powodów, dla których podejście Lean traci swoją siłę rozwoju w kierunku codziennej poprawy. TWI zostaje ponownie wskrzeszone w Stanach Zjednoczonych, gdzie wiele firm zaczyna osiągać znakomite rezultaty, korzystając z metod tego programu.
Training Within Industries: TWI J-Programs
Na początku II Wojny Światowej skuteczne szkolenia nowych (tzw. „zielonych) pracowników w przemyśle miało bardzo istotne znaczenie. W tym czasie powstała ikona pracy zawarta w piosence „Rosie the Riveter” (pol. Rózia Nitowaczka), gdzie Rosie, jako nowy pracownik w firmie, potrzebowała nauczyć się efektywnie wykonywać swoja pracę. Twórcy programu TWI stworzyli sesje szkoleniowe dla pracowników– trzy szkolenia dokładnie przetestowane w rzeczywistych warunkach produkcyjnych, każdy w komplecie z dokładnie spisanym podręcznikiem trenera. „J-Programs” (J – oznacza Job – ang. praca). Zostały wydane w jednym standardzie, który dzięki swojej formie był powtarzalny. Szkolenia dla trenerów (ang. Train the Trainers) polegało na szybkim uczeniu pracowników metod przy wysokim poziomie jakości szkolenia. Opisy podręczników trenerów musiały być ustandaryzowane, ponieważ twórcy TWI zdawali sobie sprawę, że Trenerzy maja różne poziomy doświadczenia oraz różne metody wykonywania tych samych operacji.
1.Job Instruction(JI) –Instruowanie Pracowników(IP) był w TWI „J-Programs” wdrożony jako pierwszy dlatego, że był jedną z najpilniejszych potrzeb. Karta Instruowania Pracowników (poniżej oryginał) była odzwierciedleniem 4 – krokowej metody instruowania stworzonej przez Charlesa Allena na początku 20. wieku. Celem szkolenia było nauczyć przełożonych jak stworzyć dobrą atmosferę z nowozatrudnionymi pracownikami tak, aby ich doświadczenie w nauczaniu przyniosło najlepsze efekty – pracę pracowników bez wad, wypadków i uszkodzeń sprzętu oraz narzędzi. Jeżeli przełożony nie posiada umiejętności instruowania to bez względu na wiedzę, stanowisko czy kompetencję, nie może skutecznie uczyć innych. W trakcie instruktażu błędy ludzkie powinny być korygowane natychmiastowo.
Źródło: War Production Board, Bureau of Training, Training Within Industry Service, 1944, Job Instruction: Sessions Outline and Reference Material (Washington D.C.: U.S. Government Printing Office), inside back cover
Instruowanie Pracowników uczy przełożonych jak podzielić pracę na etapy. IP sprawia, że praca staje się łatwiejsza do zrozumienia i przekazywania. Krok pierwszy opisuje przygotowanie pracownika do instruktażu. Następnie Instruktor prezentuje pracę z wykorzystaniem Arkusza Podziału Pracy, w którym podkreślone są główne kroki wraz ze wskazówkami i przyczynami występowania wskazówek. Uczeń trenuje wykonywaną czynność, a Instruktor w tym czasie nadzoruje go zmniejszając stopniowo nadzór.
2.Job Methods(JM) – Metody Pracy (MP) wdrożona jako kolejna część „J-Programs”. MP pomaga przełożonym poprawić jakość oraz produktywność na analizowanym stanowisku, dzięki wykorzystaniu dostępnej siły roboczej, maszyn i materiałów. Umiejętność skutecznego doskonalenia pracy była niezwykle konieczna, aby poprawić jakość pracy w firmie. Musiało się to odbywać bez udziału inżynierów i menadżerów, a jedynie z wykorzystaniem wiedzy operatorów i brygadzistów, ponieważ braki wykwalifikowanej kadry były ogromne.
Metody Pracy (MP) uczyły przełożonych dzielić pracę na zabiegi. Wchodząc w szczegóły i dzieląc pracę na małe części łączono najlepsze praktyki i pomysły upraszczając cały proces. Czy to nie brzmi jak podejście Kaizen? Tak jest, chociaż większość usprawnień była zrobiona przez osoby nadzorujące pracę i ograniczały się głównie do kaizen procesu, a o wiele mniej do kaizen przepływu.
3.Job Relations(JR) –Relacje z Pracownikami (RP) było ostatnią częścią „J-Programs”. Relacje z Pracownikami, jak sama nazwa mówi, pomagały przełożonym poprawić relacje z podwładnym oraz wzmacniały i promowały pracę zespołową. Zmiana nastawienia i podejścia do ludzi u osób nadzorujących pracę to pierwszy krok w budowaniu zaufania do współpracy z pracownikami. Przełożony, który nie wydobywa od ludzi najlepszych wzorców, jest po prostu nieskuteczny. Najważniejsza dla wyników przełożonego jest jego dobra współpraca z pracownikami. Relacje z Pracownikami (RP), gdzie przełożony i pracownik mają silnie zbudowaną więź współpracy, zapobiega pojawianiu się różnych problemów, a jeżeli już się pojawią, zostają rozwiązane w efektywny sposób (u źródła).
Relacje z Pracownikami uczą przełożonych dostrzegać istotne fakty, podejmować decyzje, sprawdzać wyniki podjętych działań. Podstawowe zasady tej metody obejmują: zapewnienie konstruktywnej informacji zwrotnej, zapewnienie uznania, mówienie ludziom z wyprzedzeniem o zmianach, które ich dotyczą, jak najlepsze wykorzystanie zdolności każdego człowieka oraz lojalność i współpracę pracowników. To brzmi jak kultura Lean!
Podczas II Wojny Światowej TWI bardzo się rozwinęło. Około 16,500 zakładów wzięło udział w szkoleniach TWI. Około 1,75 miliona ludzi zostało przeszkolonych i certyfikowanych z tego programu.
Jak TWI sprawdziło się w Toyota Production System (TPS)
Narzędzia TPS, od 5S aż po Kanban, zostały opracowane w latach 1950-1960. Miedzy nimi właśnie możemy doszukać się trzech filarów TWI, jakimi są „J-Programs”. Sukces kultury TPS polega na łączeniu wszystkich narzędzi i używaniu ich w efektywny sposób. W tym również są „J-Programs”. Dla przykładu, trudno jest stać się najlepszym instruktorem, kiedy jest się egocentrykiem. Gdy stosujesz samodzielnie „J-Programs” i nie korzystasz z żadnych narzędzi lean, a chcesz propagować kulturę pracy podobną do tej w Toyocie, to bez Lean zabraknie Ci wsparcia, aby rozwijać się dalej. Oryginalny „J-Programs” nie miał na celu stworzenie kultury „bez obwiniania” pracowników. Dzięki programowi TWI ludzie sami zaczynali podążać w kierunku kultury Lean.
W samej Toyocie oryginalne karty TWI z lat 50. nie są znane wszystkim pracownikom. Program TWI tworzy element wsparcia dla pracowników przy budowaniu systemu TPS. Jest jego częścią. Toyota nigdy nie pozbyła się brygadzistów. Zgodnie z podejście Lean zostali oni przeszkoleni w zespół mentorów i instruktorów – liderów. Tworzyli oni tzw. pierwsze wsparcie dla pracowników produkcyjnych w przypadku problemów. Pełnili oni rolę osób uzupełniających wiedzę oraz doświadczenia w wykonywanych czynnościach przez pracowników. Dawali pomysły na ciągłe doskonalenie procesu. Mieli oni również dyscyplinować pracowników w razie potrzeby, ale głównym ich zadaniem było prowadzenie oraz rozwój małych grup poprzez ich ciągłe instruowanie.
Bez względu na to jak często praca jest analizowana i poprawiana, bez względu na zmieniające się otoczenie oraz warunki, pracownicy w Toyocie pozostają otwarci na zmiany oraz na rozwiązywanie coraz to nowych problemów wykrytych w procesie. Większą część problemów stanowią błędy pracowników, które przekładają się między innymi na braki. TPS eliminuje wiele z nich w zarodku, ale tylko wtedy, kiedy uda się je szybko zidentyfikować oraz wdrożyć rozwiązania, które staną się również elementem Pracy Standaryzowanej.
To właśnie praktyka tworzy siłę programu TWI. Wszystkie trzy „J-Programs” są w rzeczywistości sprawdzonymi metodami rozwiązywania problemów, szkoleń pracowników oraz doskonalenia metod pracy, które wspólnie zmniejszają prawdopodobieństwo wystąpienia powtarzających się problemów. Dopiero wtedy, kiedy metody i procesy są wzbogacone o wiedzę i doświadczenia pracowników, możemy osiągnąć ciągłą poprawę na Gembie.
Stały rozwój ciągłego doskonalenia zależny jest on poziomu wdrożenia Pracy Standaryzowanej. Pomimo tego, że metoda 5xWhy (pol. 5 x Dlaczego) wspomaga rozwiązywać wiele problemów to Plan-Do-Check-Act (PDCA, koło Deminga) pozostaje podstawowym narzędziem Toyoty w procesie rozwiązywania problemów. Na Rysunkach 1 i 2 przedstawiono wszystkie trzy metody TWI, metodę Charles Allen’s o 4-stopniowym szkoleniu oraz popularną metodę naukową.
Rys. 1. Porównanie metody Charlesa Allena, TWI i metod naukowych
Rys. 2. Porównanie metod TWI i PDCA
Chociaż podejście PDCA jest najbliższe metodzie naukowej, to jednak ona sama nie daje jednej generalnej definicji, która określałaby krok po kroku działanie [2]. Najważniejszą zasadą, z którą wszyscy naukowcy się zgadzają, jest wyciąganie wniosków w oparciu o fakty, a nie opinie. Takie podejście oparte na stawianych argumentach daje mocny fundament w procesie nauczania, gdzie dzięki logice i danym nie jesteśmy zdani wyłącznie na osobowość instruktora – czynnik ludzki. Zmieniamy więc sposób zachowania ludzi, ich postawy. Tworzymy kulturę „ bez obwiniania”, w której rozwiązanie problemów odbywa się w oparciu o rzeczywiste dane i fakty.
Bazując na Rysunkach 1 i 2, największa różnica pomiędzy podejściem PDCA a metodą naukową polega na tym, że metody naukowe rzadko mają praktyczne odniesienie. To, co jest przecież kluczowe dla firm produkcyjnych. Redukcję problemów przy wdrażaniu pracy standaryzowanej przynosi program TWI „J-Programs”. Narzędzia Lean natomiast zazwyczaj tworzą środowisko pracy, w którym problemy są dostrzegane. Konsekwentne dążenie do celu to ukryta moc Lean i prawdziwa siła TPS.
Toyota, jak i inne japońskie firmy, rozumiała metodę PDCA, jako narzędzie do analizy i rozwiązywania najróżniejszych problemów. Niektóre cykle PDCA mogą być traktowane jako duże projekty. Inne stanowią małe elementy, które pomagają rozwiązać większe problemy. Rysunek nr 3 prezentuje funkcjonalność tego rozwiązania.
Rys. 3. TWI i cykl Deminga (PDCA)
W ten sposób program TWI staje się częścią PDCA tworząc fundament i „pierwszą linię frontu” w działaniach produkcyjnych. Toyota kultywuje w pracownikach podejście do rozwiązywania problemów wg zasady: rozwiązuj tak dużo problemów i tak często, jak to tylko możliwe. Aby to zrobić, Toyota angażuje pracowników w działania Kaizen i standaryzację pracy. Uczy ich jak opracować najlepszą znaną metodę pracy. Standaryzacja jest jednak nie możliwa do wdrożenia dopóki pracownicy nie nauczą się jak tworzyć standardy pracy, które można wykorzystać do instruktażu pracowników. To są właśnie metody TWI Metody Pracy i TWI Instruowanie Pracowników. Częścią połączoną przy ich stosowaniu są TWI Relacje z Pracownikami.
Kiedy sposób organizacji pracy umożliwia zmianę rozwiązań eliminujących podstawowe problemy w utrzymywaniu standardów pracy można przejść do kolejnego kroku- doskonalenia obecnych metod pracy. Kiedy nie ma tej stabilizacji to każde usprawnienie (Kaizen) musi być dokładnie monitorowany, aby sprawdzić, co tak naprawdę wywoła lub co wprowadzi nowego w istniejący proces. W takiej sytuacji przewidywalność wpływu na proces jest bardzo mała. Różnice w usprawnianiu procesów bez i ze standaryzacją pracy przedstawiono na Rysunku 4.
Rys. 4. Korzyści z utrzymywania standaryzacji pracy
Rysunek 4 prezentuje, dlaczego w wielu firmach przejście na pracę zgodną z filozofią Lean nie daje oczekiwanych rezultatów. Jednym z głównych powodów jest stagnacja. Pozornie wygląda to prosto. Niestety rozwój liderów i pracowników, którzy będą sami tworzyć, usprawniać i utrwalać opracowane standardy pracy, trwa około 2-3 lat. Tyle czasu zajmuje nauczenie się pracować wg standardów. Dlatego Toyota twierdzi, że wdrażanie standaryzacji pracy jest długim etapem przemiany prowadzącym do kultury TPS. Metody należące do programu TWI są sposobem, aby przejść tą ścieżkę bez zbędnego „bólu”.
W oryginalnej literaturze poświęconej TWI J-Programs nie ma nic wspomnianego o kulturze tzw. „nieobwiniania” pracowników. Taka kultura buduje się sama wtedy, kiedy praktykujesz 4-krokowe metody J-Programs, a szczególnie metodę TWI Relacje z Pracownikami(RP). Wspólny wpływ na środowisko pracy, w którym podejście wszystkich osób jest wykorzystane w jak najlepszy sposób, daje metoda TWI Metody Pracy (MP). Standaryzowana i powtarzalna praca, wykonywana przez wszystkich pracowników, jest wynikiem metody TWI Instruowania Pracowników(IP). Metody z TWI J-Programs nie marnują czasu na bezproduktywne dyskusje o budowaniu zespołu, znajdowania konsensusu, czy tworzenia środowiska pracy, które dzisiaj zniekształcają obraz prawdziwej wizji kultury Lean. Program TWI skupia się po prostu na rozwiązaniu problemów, poprawie efektywności i tworzeniu bezpiecznego środowiska pracy, co przekłada się na korzyści zarówno dla pracowników, firmy, jak i społeczeństwa.
4-kroki metody TWI są bardzo pragmatyczne i usystematyzowane w swoim przekazie. Ich stosowanie przekłada się na znakomite rezultaty w postaci poprawy zysku firmy, który jest ważnym wyznacznikiem, jak również w podejściu ukierunkowanym na ludzi i ich potrzeby. Wynikiem korzystania z programu TWI jest poprawa atmosfery w pracy zespołu, który nieustannie rozwija się i idzie do przodu. Budowanie takiej kultury można osiągnąć, jeżeli tworzy się ją od fundamentów. Ten fundament właśnie zapewniają TWI J-Programs.
TWI J-Programs powinny być stosowane każdego dnia, w każdej sytuacji i w każdych warunkach. Pracownicy uczeni są metod 4-kroków w ciągu cykli szkoleń z każdego programu. Nacisk na szkoleniach położony jest na przestrzeganie tych metod i ich utrwalanie przez doświadczonych pracowników i przełożonych, dla których powinny być one częścią codziennej pracy. W TWI nazywa się takie szkolenia „nauką przez działanie”, ponieważ stosowanie tego, czego się nauczyli pracownicy odbywa się każdego dnia. Dlatego ciągłe rozwijanie umiejętności odbywa się poprzez własne doświadczenia.
TWI i Przywództwo
W jaki sposób zatem organizacja powinna rozwijać przywództwo i umiejętności swoich pracowników tak, aby utrzymywać „swój” TPS tak jak to się dzieje w Toyocie? Zastosować program TWI jako fundamentalnym elementem zarządzania w firmie. Program TWI w Toyocie używany jest od ponad 50 lat. W tym czasie wszyscy menadżerowie Toyoty, również najwyższe kierownictwo (w tym Fujio Cho), zostali przeszkoleni z metod programu TWI. Zdobyli w tym temacie doświadczenie i praktykę.
W Toyocie większość menadżerów środkowego i najwyższego szczebla przez wiele lat było prowadzonych i rozwijanych w jednym środowisku pracy. Nic więc dziwnego, że kultura zarządzania w Toyocie została zinstytucjonalizowana na wszystkich szczeblach organizacyjnych. Fujio Cho, który był uczony przez samego Taichii Ohno, kiedy obejmował stanowisko Prezesa Toyoty powiedział: „Robiliśmy dużo rzeczy bez zastanawiania się, tak jak byliśmy uczeni przez naszych poprzedników, i to działało, więc po prostu to robiliśmy”[3].
Droga Toyoty (ang. Toyota Way) składa się z konkretnych działań, które stają się nawykiem w funkcjonowaniu pracowników w całej organizacji. „Toyota od dawna utrzymuje, że Droga Toyoty może być wyłącznie zrozumiana poprzez jej praktykowanie każdego dnia na produkcji pod okiem doświadczonych przełożonych. Dyrektorzy Toyoty twierdzą, że sukces Drogi Toyoty tkwi we właściwej postawie pracowników, a także w dyscyplinie i ciężkiej pracy”[4].
Odrodzenie programu TWI
W Ameryce Północnej garstka firm zaczęła ponownie stawać się pionierami we wdrażaniu metod programu TWI. Jedną z pierwszych firm, która ponownie powróciła do korzeni TWI, była ESCO Turbine Technologies in Chittenango, NY. ESCO Turbine jest światowej klasy producentem części precyzyjnie odlewanych, stosowanych w silnikach samolotowych, sprzęcie o dużej mocy, czy w pociskach.
Na dzień powstania artykułu (2006 rok, przyp. red.), ponad 60 pracowników firmy ESCO Turbine zostało przeszkolonych z metody TWI IP. Setki Instrukcji Pracy zostało napisanych i dodanych do procedur przedsiębiorstwa. Rezultatem wdrożenia metody TWI IP na wydziale form było zmniejszenie błędów o 96% pomiędzy latami 2002 i 2004, poprawa wskaźnika dostępności form woskowych na czas z 73,2% do 98.6% i skrócenie czasu wdrożenia pracowników do pełnej wydajności pracy z dwóch miesięcy do dwóch tygodni. Paul Smith, Dyrektor HR w ESCO powiedział, że „program TWI skrócił o połowę zakładany czas realizacji celów”. W tym czasie braki spadły o 76% co przełożyło się na olbrzymią korzyść ekonomiczną przedsiębiorstwa.
Tak jak ESCO, tak też inne organizacje wprowadzające TWI, zaczęły prężnie działać i osiągać, tak jak nigdy wcześniej, wysokie wyniki finansowe oraz szybki rozwój umiejętności pracowników. Program TWI stał się centralną częścią tego sukcesu, która wspomagała pozostałe aktywności w zakresie Lean Management. Dokładnie tak, jak program TWI odgrywał swoją rolę w Toyocie przy budowaniu TPS.
Jeżeli zacząłeś wdrażać filozofię Lean Management w swojej organizacji, ale jeszcze nie słyszałeś o Training Within Industry, to prawdopodobnie wkrótce o nim usłyszysz. Podobnie jak ESCO, firmy uczą się programu TWI, aby wspierać zrównoważony rozwój w oparciu o filozofię Lean Management, gdzie jednym z punktów kluczowych jest praca zgodna z obecnie najlepszymi standardami. Program TWI zaczyna wracać do Amerykańskiego przemysłu, a takie firmy jak ESCO uczą się dzięki niemu jak zdobywać przewagę konkurencyjną.
Jak zauważył Clay Chandler podczas dyskusji o TPS prowadzonej na łamach magazynu Fortune: „Esencją systemu TPS jest przekonanie, że inżynierowie, menadżerowie i szeregowi pracownicy stale współpracują w standaryzowaniu zadań produkcyjnych oraz w stopniowym wprowadzaniu ulepszeń, aby praca odbywała się płynnie i bez zakłóceń. To proces, w którym wszystko działa z doskonałą precyzją wzmacnianą przez masę drobnych usprawnień w każdym dniu pracy”[5].
Przywództwo w Toyocie rozwijało się dzięki własnym doświadczeniom czerpanym z produkcji i przekazywanym do najwyższego kierownictwa. Dzisiejsze firmy, takie jak ESCO, zaczynają swoje lekcje chcąc czerpać z nich jak najwięcej korzyści. Program TWI, pomimo tego, że pierwotnie skupiał się na relacji przełożony-pracownik w zakładzie, obecnie przekształcił się w dwa podejścia: praktykę i filozofię, która prowadzi pracowników i buduje kulturę organizacyjną poprzez „uczenie się przez działanie”. Celem jest danie pracownikom i całej organizacji zdolność do tworzenia standardów, wprowadzania ulepszeń i zdobywania kolejnych szczebli rozwoju (jak pokazano na Rysunku 4). Mentor Fujio Cho, Taiichi Ohno, w najlepszy dla siebie sposób wyraził czym jest najważniejsza zasada programu TWI. Taichii Ohno uważał, że „menadżerowie w Toyocie powinni być tak zaangażowani w produkcję, aby myli ręce co najmniej trzy razy dziennie”[6]. To jest właśnie TWI!
Autor: Jim Huntzinger
Tłumaczenie i korekta: dr Bartosz Misiurek, Łukasz Sobolewski
Artykuł opublikowany na stronie Polskiego Stowarzyszenia Praktyków TWI
Opracowanie to jest tłumaczeniem artykułu Jima Huntzingera: Why Standard Work is not Standard: Training Within Industry Provides an Answer, 2006, AME Association for Manufacturing Excellence, Fourth Issue. Artykuł został przetłumaczony za zgodą autora –Jima Huntzingera, jak i również Association for Manufacturing Excellence (www.ame.org), która wydaje magazyn Target.Zgoda na publikację artykułu otrzymana od Polskiego Stowarzyszenia Praktyków TWI – Partnera LeanTrix
Pobierz artykuł w PDF:
(Wskazówka: Otwierając w nowym oknie)
Adnotacja autora:
Wielkie podziękowania dla Boba Wrony i Patricka Grauppa za ich wkład w postanie artykułu, jak i dla Karen Wilhelm z SME, dzięki której artykuł ukazał się również w Lean Directions, w e-newsletterze Society of Manufacturing Engineers.
Adnotacja Polskiego Stowarzyszenia Praktyków TWI do artykułu
Jim Huntzinger na końcu swojego artykułu polecił kilka pozycji literaturowych, które opisują program TWI. Sam artykuł powstał w 2006 roku, kiedy na rynku nie było dostępnych zbyt wielu publikacji o programie TWI. PSP TWI prowadzi i aktualizuje zbiór wszystkich książek o programie TWI, które można przejrzeć tutaj. Wśród tych pozycji są oczywiście również te rekomendowane w 2006 roku przez Jima.
Literatura i notatki autora:
[1] Alan Robinson and Sam Stern, 1997, Corporate Creativity: How Innovation and Improvement Actually Happen (San Francisco, CA: Berrett-Koehler Publishers), p. 77.
[2] The PDCA cycle is often referred to as the Deming Circle (for W. Edwards Deming). This method is in fact originally known as the Shewhart Cycle, which was developed by Walter Shewhart in the 1930s. Deming was one of his pupils.
[3] Clay Chandler, February 7, 2005, “Full Speed Ahead,” Fortune, p. 84.
[4] Clay Chandler, February 7, 2005, “Full Speed Ahead,” Fortune, p. 82.
[5] Clay Chandler, February 7, 2005, “Full Speed Ahead,” Fortune, p. 82.
[6] Clay Chandler, February 7, 2005, “Full Speed Ahead,” Fortune, p. 84
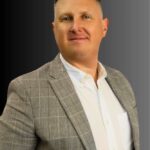
Jestem popularyzatorem Lean Management oraz programu Training Within Industry. Jestem praktykiem. Współtworzę wiele startupów. Od 2015 roku jestem CEO w Leantrix - czołowej firmie z zakresu konsultingu Lean w Polsce, która począwszy od 2024 roku organizuje jedną z największych konferencji poświęconych szczupłemu zarządzaniu w Polsce - Lean TWI Summit. Od 2019 roku jestem CEO w firmie Do Lean IT OU zarejestrowanej w Estonii, która tworzy software etwi.io używany przez kilkadziesiąt firm produkcyjnych i usługowych w Europie i USA.