W dzisiejszych czasach Lean Management jest sposobem zarządzania w większości firm produkcyjnych. Lean dostarcza szereg metod i narzędzi, które poprawiają organizację pracy, a tym samym przekładają się na poprawę efektywności procesów. Wśród wszystkich metod Lean najczęściej stosowane są: system 5S i TPM. Są one zorientowane na standaryzację procesów produkcyjnych, która stanowi podstawę sprawnego systemu zarządzania przedsiębiorstwem.
W dzisiejszych czasach Lean Management jest sposobem zarządzania w większości firm produkcyjnych. Lean dostarcza szereg metod i narzędzi, które poprawiają organizację pracy, a tym samym przekładają się na poprawę efektywności procesów. Wśród wszystkich metod Lean najczęściej stosowane są: system 5S i TPM. Są one zorientowane na standaryzację procesów produkcyjnych, która stanowi podstawę sprawnego systemu zarządzania przedsiębiorstwem. Na rysunku 1 przedstawiono tzw. dom Toyoty, w którym stabilne i standaryzowane procesy są traktowane jako fundament. Dom Toyoty to graficzny sposób prezentacji najbardziej skutecznego podejście do zarządzania produkcją – Systemu Produkcyjnego Toyoty (ang. Toyota Production System – TPS).
Rys. 1. Dom Toyoty
Źródło: Misiurek B., 2016, Standardized Work with TWI: Eliminating Human Errors in Production and Service Processes, Productivity Press, New York
Wspomniany system 5S i TPM związane są zarówno z działami Produkcji, jak i Utrzymania Ruchu. Angażują one przy tym pracowników bezpośrednio produkcyjnych. W systemie 5S operatorzy dbają o wysoką jakość stanowiska pracy, a w systemie TPM o utrzymanie sprawności pracy maszyn (głównie poprzez działania w zakresie autonomicznej konserwacji). Z moich doświadczeń z pracy dla przeszło 150 fabryk w Polsce wynika, że przy wspomnianych systemach narosło wiele błędnych stereotypów, które przekładają się na trudności w ich skutecznym wdrożeniu. Dwa z nich będę chciał się przedstawić w tym artykule podpowiadając przy tym jak z nimi skutecznie walczyć.
Pamiętaj, że nawet jeżeli któryś z tych stereotypów wrósł w firmę, w której pracujesz, to jest szansa, aby to zmienić. Kluczem jest przede wszystkim zrozumienie problemu.
Stereotyp nr 1. System 5S to sprzątanie stanowiska pracy, a system TPM to czyszczenie maszyn
Systemy 5S i TPM są przede wszystkim zorientowane na standaryzację procesów, w której kluczową część stanowi doskonalenie pracy (jap. kaizen). Jeżeli System 5S powstałby wyłącznie po to, aby utrzymywać porządek na stanowisku pracy, to jego wdrożenie kończyłoby się na 3.S – sprzątaniu. W praktyce skuteczne wdrożenie systemu 5S to przede wszystkim 4.S – standaryzacja i 5.S – samodyscyplina. To w tych krokach powstają rozwiązania doskonalące takie jak np. tablice cieni (rysunek 2), czy cały proces utrzymania wdrożenia poprzez audytowanie procesu.
Rys. 2. Przykład tablicy cieni
Źródło: Misiurek B., 2015, Metodyka standaryzacji autonomicznych procesów eksploatacyjnych zorientowana na poprawę efektywności maszyn zautomatyzowanych, Uniwersytet Technologiczny we Wrocławiu
Przedstawiona na rysunku 2 tablica cieni w oczywisty sposób przekłada się na porządek w miejscu pracy. Jednak najważniejszym celem jej wdrożenia jest szybka identyfikacja brakujących narzędzi, co przekłada się na poprawę efektywności wykorzystania stanowiska pracy. Porządek jest pozytywnym efektem ubocznym tego rozwiązania, a nie celem samym w sobie.
Dlaczego zatem System 5S utożsamiany jest przez większość operatorów jako sprzątanie stanowiska pracy? Dlatego, że najmniejszy nacisk w firmach przykłada się do angażowania pracowników w szukanie rozwiązań doskonalących przy wdrażaniu systemu 5S. Z moich doświadczeń wynika, że w przeszło 80% fabrykach system 5S sprowadza się wyłącznie do opracowania instrukcji sprzątania stanowiska pracy. Z czym zatem System 5S ma kojarzyć się operatorom? Odpowiedź jest oczywista – ze sprzątaniem.
W przypadku autonomicznej konserwacji, która jest częścią systemu TPM, sytuacja jest bardzo zbliżona. Często proszony jestem przez firmy produkcyjne o reaktywację w ich fabrykach systemu TPM, który z niewiadomych powodów „umarł”. Kiedy spotykam się z operatorami i pracownikami UR, którzy już próbowali swoich sił z TPM, zadaje zawsze to samo pytanie: z czym Wam kojarzy się TPM? Odpowiedź jest zawsze taka sama: z czyszczeniem maszyn. Przywołam w tym momencie maksymę Toyoty: nigdy nie wiń ludzi, zawsze wiń procesy. Zastanawiając się co było nie tak przy wdrożeniu TPM we wspomnianych firmach wniosek jest zawsze ten sam: System TPM „sprzedawany” jest tam pracownikom jako narzędzie wspomagające czyszczenie maszyn, a nie ich doskonalenie. To wina procesu nauczania, a nie ludzi, że nie rozumieją czym jest System TPM. Takie postępowanie to przykład 8. typu marnotrawstwa – utraconej kreatywności ludzi. Autonomiczna konserwacja, która jest odpowiedzialnością operatorów w systemie TPM, to czyszczenie i przeglądanie maszyny w jednym najważniejszym celu – identyfikacji niezgodności, anomalii i usterek. Czyszczenie jest potrzebne, aby dotknąć maszynę, poczuć ją. Czyszczenie jest po to, aby wychwycić usterkę zanim przerodzi się ona w awarię. Doskonalenie jest natomiast istotne, aby skuteczniej i efektywniej wykonywać zaplanowane zadania przeglądowe. Dlaczego zatem w tak wielu firmach TPM utożsamiane jest wyłącznie z czyszczeniem maszyn? Dlatego, że firmy te z dużym rozmachem wdrażają instrukcje czyszczenia maszyn (i czasami konserwacji) zapominając, że najważniejsza jest komunikacja operatorów z pracownikami UR w przypadku zidentyfikowanej usterki. Tą komunikację zapewnia system zgłaszania usterek. Na Rysunku 3 przedstawiono przykładowy system zgłaszania usterek z firmy LG Display Poland sp. z o.o.
Rys. 3. System zgłaszania usterek z firmy LG Display Poland sp. z o.o.
Źródło: Wolak M., Kotlarski B., Maczuga M., 2014, 5S Fundamentem Trwałego Systemu TPM, Materiały Konferencyjne do XIV Konferencja Lean Management, Wrocław
System ten został opracowany podczas warsztatów praktycznych zarówno przez operatorów, jak i pracowników UR. Jest on narzędziem komunikacji pomiędzy tymi dwoma grupami osób. Jego działanie jest proste. Operator zgłasza usterkę wypisując kartę, a następnie przykleja magnes (strona czerwona) z numerem karty na rysunku maszyny w miejscu, które odpowiada rzeczywistej lokalizacji usterki. Pracownicy UR mają 48 godzin na podjęcie działania z usterkę, wypisania karty usterki oraz obrócenie magnesu na stronę żółtą. Podjęte działanie nie musi oznaczać usunięcia usterki. Musi natomiast być zapisania informacja zwrotna dla operatora – jakie działanie podjęli pracownicy UR. Tak zbudowany system tworzy „kanał komunikacyjny” między operatorami i pracownikami UR.
System zgłaszania usterek powinien powstać przed instrukcjami TPM. Instrukcje czyszczenia i konserwacji maszyn powinny być opracowane po to, aby wskazać miejsca kluczowe pod względem identyfikacji usterek, które należy przeglądać. Instrukcje TPM nie powinny wskazywać miejsc, które należy czyścić, aby maszyna była czysta. W TPM ta czystość maszyny jest pozytywnym efektem ubocznym identyfikacji usterek i problemów. Podobnie jak to było w systemie 5S.
Stereotyp nr 2. System 5S jest odpowiedzialnością Produkcji, a System TPM Utrzymania Ruchu
Celem działów Produkcji i UR jest podnoszenie wartości wskaźnika całkowitej efektywności wykorzystania maszyn (ang. Overall Equipment Efficiency – OEE). Systemy 5S i TPM skutecznie im w tym pomagają. System 5S wpływa głównie na poprawę wydajności maszyn, a System TPM na ich dostępność. Choć należy zauważyć, ze usterka w maszynie może mieć wpływ na pojawienie się każdej z sześciu wielkich strat w pracy maszyny, tj.: awaria, zbyt długie przezbrojenie, mikroprzestój, obniżona prędkość pracy, brak, czy obniżona wydajność podczas rozruchu maszyny. Dlatego System TPM ma praktycznie wpływ na poprawę wszystkich czynników należących do wskaźnika OEE. Najczęściej w firmach odpowiedzialność za wdrożenie systemu 5S spoczywa na dziale Produkcji, a systemu TPM na dziale UR. Uważam to za błędne podejście, bo te systemy się wzajemnie uzupełniają i powinny być wdrażane wspólnie. Można założyć, że system 5S odpowiada za utrzymanie wysokiej jakości stanowiska pracy wokół maszyny, a system TPM za funkcjonalność samej maszyny. Dlatego przyjmuje się, że systemy 5S i TPM tworzą jedność, w której 5S jest fundamentem. Z tego też powodu systemy te powinny być wdrażane jako jedno kompletne rozwiązanie. Również powinny być one objęte jednym procesem audytowania. Niestety z tego względu, że system 5S przypisywany jest często do działu Produkcji, a system TPM do działu UR następuje problem z przypisaniem wskaźników. Z jednej strony Produkcja nie chce brać na swoją odpowiedzialność autonomicznej konserwacji maszyn, z drugiej strony UR interesuje sama maszyna. Sposobem eliminacji tego problemu może być wyznaczenie w firmie menadżera strumienia wartości, który odpowiedzialny jest za efektywność maszyny. W tym rozwiązaniu następuje odejście od tradycyjnego podziału na działy: UR i Produkcję. W to miejsce zalecam zawsze wyznaczenie określonej liczby strumieni wartości w fabryce, a następnie wyznaczenie dla tych strumieni menadżerów i ujednoliconych wskaźników KPI. Menadżer strumienia wartości powinien być zatem na równi rozliczany z dostępności, jak i z wydajności maszyn. Menadżer strumienia wartości powinien mieć pod sobą część mechaników oraz mistrzów, liderów i operatorów przypisanych do obszarów produkcyjnych w danym strumieniu wartości. Przed najwyższym kierownictwem menadżer strumienia wartości powinien rozliczać się z całej efektywności maszyn (wskaźnik OEE). W takim rozwiązaniu menadżer strumienia wartości będzie traktować Systemy 5S i TPM jako jedność, której celem jest poprawa wskaźnika OEE.
Podsumowanie
Przedstawione w artykule dwa stereotypy na temat systemów 5S i TPM dość często występują w polskich przedsiębiorstwach. Niestety są one również przyczyną niepowodzeń we wdrażaniu tych systemów. Skuteczność implementacji wszystkich metod i narzędzi Lean zależna jest od dwóch czynników: zaangażowania najwyższego kierownictwa i pracowników. Najwyższe kierownictwo musi odczuwać płynące korzyści z wdrożenia systemów 5S i TPM. W rozwiązaniu z powołaniem menadżera strumienia wartości te korzyści można o wiele łatwiej osiągnąć. Zaangażowanie pracowników można zdobyć, kiedy aktywnie wciągnie się ich w działania praktyczne. Rolą najwyższego kierownictwa jest budowanie świadomości wśród pracowników. Ta świadomość jest zdobywana poprzez zrozumienie dlaczego w firmie wdrażane są systemy 5S i TPM. Dlatego zamiast mówić ludziom jak mają coś robić, powiedz im dlaczego mają to robić. Kiedy zrozumieją dlaczego mają to robić, to wówczas sami przyjdą i zapytają jak to zrobić. Guru w zarządzaniu, Peter Drucker, powiedział kiedyś: „Dajcie ludziom swobodę i możliwość działania, a zaskoczą was swoją pomysłowością.” Filozofia Lean, a w tym systemy 5S i TPM, wspomagają kreatywność pracowników. Wykorzystaj tą szansę!
Autor
Bartosz Misiurek, dr inż.
Artykuł opublikowany w magazynie Szef UR (kwiecień 2016)
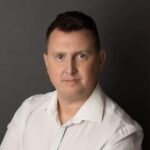
Jestem popularyzatorem Lean Management oraz programu Training Within Industry. Jestem praktykiem. Współtworzę wiele startupów. Od 2015 roku jestem CEO w Leantrix - czołowej firmie z zakresu konsultingu Lean w Polsce, która począwszy od 2024 roku organizuje jedną z największych konferencji poświęconych szczupłemu zarządzaniu w Polsce - Lean TWI Summit. Od 2019 roku jestem CEO w firmie Do Lean IT OU zarejestrowanej w Estonii, która tworzy software etwi.io używany przez kilkadziesiąt firm produkcyjnych i usługowych w Europie i USA.