System 5S to jedno z fundamentalnych narzędzi budujących filozofię Lean Management. Praktyka pokazuje, że większość firm zaczyna swoją przygodę ze szczupłym wytwarzaniem właśnie od wdrożenia systemu 5S. Jest to słuszne podejście, ponieważ ta metoda zorientowana jest na stabilizację procesów, co jest fundamentem systemu produkcyjnego Toyoty (ang. Toyota Production System). Niestety bardzo często system 5S kojarzony jest wśród pracowników wyłącznie ze sprzątaniem stanowiska pracy. Gdyby system 5S kończył się na sprzątaniu, to wówczas mielibyśmy wyłącznie 3 kroki tego podejścia – sprzątanie to 3.S. System 5S ma na celu przede wszystkim doskonalić i utrzymywać jakość stanowiska pracy. Jedna z głównych zasad systemu 5S brzmi: „Wszystko ma swoje miejsce i wszystko na swoim miejscu”.
W Tabeli 1 przedstawiono schemat postępowaniu przy wdrażaniu systemu 5S na dowolnym stanowisku pracy. Schemat ten został opracowany na Arkuszu Podziału Pracy wykorzystywanym w programie Training Within Industry – TWI.
Tabela 1. Schemat postępowania przy wdrażaniu systemu 5S
Główne kroki | Wskazówki | Przyczyny |
Co należy wykonać | Jako należy to wykonać | Dlaczego należy wykonać to tak, a nie inaczej |
1. Sortowanie | 1. Oddziel to co potrzebne, od tego co niepotrzebne:
· narzędzia, · instrukcje, · materiały, · Itd. |
1. Utrzymanie porządku na stanowisku jest łatwiejsze, kiedy masz na nim tylko to, co potrzebne na co dzień w pracy. |
2.Niepotrzebne części wyrzuć albo oznacz czerwoną etykietą | 2.Jeżeli nie jesteś pewien, czy wyrzucić daną część to zostaw ją na polu czerwonych etykiet i wróć do niej po określonym czasie (np. miesiącu). Wówczas podejmiesz działanie. Pozostałe niepotrzebne rzeczy wyrzuć. | |
2. Systematyka | 1. Oznacz miejsca na potrzebne części i narzędzia na stanowisku |
1. Zawsze będziesz wiedział, czego Ci brakuje na stanowisku pracy. Łatwiej będzie również utrzymać porządek. |
2. Wykorzystuj kolorystykę (sterowanie wizualne) | 2. Kolory są istotną częścią sterowania wizualnego. Ludzie przyswajają aż 83% informacji przez wzrok. Staraj się używać kolorystyki, wszędzie tam gdzie jest to możliwe. | |
3. Określ limity, poziomy i kierunki. |
3. Pomoże Ci to utrzymać wymaganą liczbę materiałów i narzędzi na stanowisku pracy. Ułatwi to samodyscyplinę w przestrzeganiu zasad. | |
3. Sprzątanie | 1.Czyszcząc szukaj usterek i problemów na stanowisku | 1. Czyszczenie to sprawdzanie. Nie czyścisz tylko po to, aby maszyna albo stanowisko było czyste. Głównym celem czyszczenia powinna być identyfikacja nieprawidłowości. |
2.Ustal harmonogram sprzątania | 2.Dzięki harmonogramowi będziesz mógł skutecznie audytować proces utrzymania systemu 5S w firmie. | |
4. Standaryzacja | 1. Ustal standardy czyszczenia oraz ułożenia narzędzi i materiałów na stanowisku. | 1.Stanowisko ma być tak zorganizowane, aby każdy umiał się w nim odnaleźć – nie tylko Ty. Zapisany standard w tym pomoże. |
2.Ustal harmonogram audytów | 2.Aby utrzymać system. Tylko przeglądy i audyty są gwarancją tego, że działania 5S wejdą w nawyk pracowników. | |
5. Samodyscyplina | 1. Realizuj zadania wynikające z audytów. | 1. Audyt to nie kontrola. To szansa na doskonalenie. Spodziewaj się audytów na swoim stanowisku. Jeżeli wynikną z niego jakieś rekomendacje, to je zrealizuj. Samodyscyplina polega na przestrzeganiu zasad każdego dnia. Nie bój się audytów. Traktuj je jako szansę sprawdzenia swojego postępowania. |
W wielu firmach na Świecie system 5S rozwinął się do podejścia zwanego: system 6S. Czym jest to tajemnicze 6.S? To bezpieczeństwo pracy (ang. Safety). Uważam, że wprowadzenie dodatkowego „S” bardzo dobra praktyka, ponieważ zawsze warto kłaść nacisk na bezpieczeństwo pracy. Jest jednak parę zagrożeń, kiedy będziesz chciał wzbogacić system 5S o 6.S – bezpieczeństwo pracy.
6S – Safety jako pierwsze, czy jako szóste „S”?
W wielu zakładach produkcyjnych, które używają podejścia 6S, bezpieczeństwo pracy traktowane jest jako 6.S. Uważam to za błąd. System 5S składa się z 5 kroków, które należy realizować w zadanej kolejności. Nie jest to żadnych 5 złotych zasad. Jest to ścieżka 5 kroków, która pokazuje jak poprawić jakość stanowiska pracy. Jednym słowem, nie można realizować 2.S bez 1.S. Dodawanie bezpieczeństwa pracy jako 6.S tworzy przekaz, że na bezpieczeństwo pracy powinniśmy zwracać uwagę dopiero na końcu! To jest oczywiście błędne podejście, z którym trudno się zgodzić. Czy bezpieczeństwo pracy powinno być zatem 1.S? Również uważam, że to zły pomysł. W tej sytuacji 2.S przyjmie nazwę: Sortowanie. Każdy z pracowników, który będzie chciał poczytać w literaturze o systemie 5S, będzie miał nie lada mętlik w głowie. Wszędzie w książkach i w artykułach znajdzie informację, że 1.S to Sortowanie, a u niego w pracy będzie to 2.S.
Jaki zatem numer przypisać bezpieczeństwu pracy? Najlepiej zapisać je jako 0.S – fundament, punkt startowy przed podjęciem jakichkolwiek działań poprawiających jakość organizacji stanowiska pracy. Dzięki temu nadal w firmie można używać podejścia 6S, które składa się z kroku 0.S -Bezpieczeństwo Pracy i z 5 pozostałych kroków budujących tradycyjny system 5S.
Jak realizować 0.S – bezpieczeństwo pracy?
Z pełną premedytacją w Tabeli 1 przedstawiłem APP dla schematu usprawniania stanowiska pracy zgodnie z systemem 5S. APP dzieli dowolnie wykonywaną pracę na:
- Główne kroki (co robimy?)
- Wskazówki (jak to robimy?)
- Przyczyny występowania wskazówek (dlaczego to robimy tak, a nie inaczej?)
Powstało wiele książek o tym jak realizować poszczególne kroki 5S. Podstawowe wskazówki zawarłem w Tabeli 1. Pracownicy po szkoleniach o systemie 5S doskonale wiedzą co powinni w konkretnym „S” realizować. Problemem w zakładach produkcyjnych jest to, że praktycznie nie daje się wskazówek jak poprawnie realizować szóste „S” – bezpieczeństwo pracy. Często to dodatkowe „S” sprowadza się do dwóch rzeczy:
- Hasła informujące o tym, że trzeba pracować bezpiecznie
- Nakaz używania środków ochrony osobistej
Te dwa punkty są z pewnością ważne i należy je promować. Są jednak dużo bardziej skuteczne sposoby jak poprawnie realizować dodatkowe „S” – bezpieczeństwo pracy (rys. 1).
Rys. 1. Hierarchia skuteczności środków zaradczych w zakresie bezpieczeństwa pracy
Uważam, że jeżeli firma decyduje się na wdrażanie systemu 6S w miejsce systemu 5S to powinna przede wszystkim podjąć działania, aby efektywnie podejść do problemu zapewnienia bezpieczeństwa pracy. Najbardziej skutecznym działaniem w budowaniu bezpiecznego miejsca pracy dla pracowników jest eliminowanie zagrożeń. Jeżeli taka eliminacja jest niemożliwa to powinno się wdrożyć środki techniczne, które będę możliwie skutecznie chronić pracowników. Dopiero kolejnym krokiem są ostrzeżenia o zagrożeniach i szkolenia pracowników. Niemniej skutecznym środkiem zaradczym są środki ochrony osobistej. Niestety w dużej części firm produkcyjnych bezpieczeństwo pracy sprowadza się głównie do przestrzegania używania środków ochrony osobistej.
Metodą, która zorientowana jest na budowanie bezpiecznego miejsca pracy, jest TWI Bezpieczeństwo Pracy. Metoda ta powstała podczas II Wojny Światowej w ramach programu TWI. Opiera się ona na badaniach słynnego naukowca amerykańskiego Herbert William Heinrich, który nazywany jest pionierem bezpieczeństwa pracy. Żył on na przełomie XVIII i XIX wieku. Główną konkluzją badań Heinricha było stwierdzenie, iż koncentrowanie się jedynie na sprawnym reagowaniu na występujące zdarzenia wypadkowe nie przyniesie poprawy w zakresie bezpieczeństwa. Ważna jest prewencja. Metoda TWI BP skupia się na identyfikacji zagrożeń zanim przerodzą się one w wypadki. Metoda ta składa się z 4 kroków:
- Krok 1. Identyfikacja miejsc będących przyczynami zagrożeń
- Krok 2. Określenie środków zaradczych
- Krok 3. Wprowadzanie w życie działań zaradczych.
- Krok 4. Kontrola rezultatów
Główną zaletą metody TWI BP jest to, że pozwala ona na analizę stanowiska pracy pod względem identyfikacji potencjalnych zagrożeń (krok 1). Kiedy wszystkie zagrożenia są wylistowane to powinno się przeprowadzić analizę usprawniającą (krok 2) wykorzystując hierarchię środków zaradczych przedstawionych na rysunku 1. Kolejnym etapem powinno być wprowadzenie w życie działań zaradczych (krok 3) i kontrola rezultatów (krok 4). Dopiero po wykonaniu takiej analizy można przejść na stanowisku pracy do kroków opisanych w systemie 5S. Wówczas mamy pewność, ze stanowisko jest bezpieczne – wolne od części zagrożeń, a te zagrożenia, które pozostały, są zabezpieczone.
Jeżeli w firmie zostanie przyjęty taki sposób postępowania to wówczas na APP dla systemu 6S bezpieczeństwo pracy będzie traktowany jako zerowy główny krok (Tabela 2).
Tabela 2. Schemat postępowania dla 0.S – bezpieczeństwo pracy
Główne kroki | Wskazówki | Przyczyny |
Co należy wykonać | Jako należy to wykonać | Dlaczego należy wykonać to tak, a nie inaczej |
1.Stworzenie Bezpiecznego stanowiska pracy | 1. Identyfikuj miejsca będące zagrożeniami | 1. Aby prewencyjnie określić, gdzie w przyszłości mogłoby dojść do wypadku. Używaj arkusza identyfikacji zagrożeń jako inspiracji. |
2.Określ środki zaradcze dla zagrożeń | 2.Aby zabezpieczyć wszystkie zagrożenia, które mogą doprowadzić do wypadku. | |
3.Wprowadź w życie działania zaradcze | 3.Te działania w praktyce będą chronić pracowników. Pamiętaj, aby zacząć od eliminowania zagrożeń, a dopiero ewentualnie przy braku możliwości, wdrożenia środków technicznych. Środki ochrony osobistej traktuj jako najmniej skuteczny środek zaradczy. | |
4.Przeszkól pracowników z występujących zagrożeń na stanowisku | 4.Aby zdobyli świadomość na temat ewentualnych niebezpieczeństw na stanowisku pracy zanim zaczną wdrażać system 5S. | |
5.Kontroluj wyniki | 5.Aby sprawdzać, że środki zaradcze są stosowane i czy nie pojawiły się dodatkowe zagrożenia. |
System 5S czy system 6S? Podsumowanie
Jestem zwolennikiem systemu 6S, w którym bezpieczeństwo pracy jest fundamentem – 0.S. Uważam, że bez identyfikacji zagrożeń na stanowisku pracy nie powinno się dokonywać działań usprawniających z wykorzystaniem systemu 5S. Jeżeli firma decyduje się na wdrażanie systemu 6S powinna przede wszystkim ustalić jak należy stworzyć bezpieczne stanowisko pracy. W innym przypadku bezpieczeństwo będzie kojarzone przez pracowników wyłącznie z noszeniem środków ochrony osobistej. Prawdziwe podejście do zapewnienia bezpieczeństwa pracy związane jest prewencją. Zapobiegaj poprzez identyfikację zagrożeń zanim one przerodzą się w wypadki. Załóż, że na każdym stanowisku są zagrożenia. Dopiero po realizacji 0.S. przejdź do wdrażania systemu 5S.
Autor: Dr inż. Bartosz Misiurek
Artykuł opublikowany w magazynie Szef UR (Nr 1/2017)
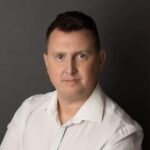
Jestem popularyzatorem Lean Management oraz programu Training Within Industry. Jestem praktykiem. Współtworzę wiele startupów. Od 2015 roku jestem CEO w Leantrix - czołowej firmie z zakresu konsultingu Lean w Polsce, która począwszy od 2024 roku organizuje jedną z największych konferencji poświęconych szczupłemu zarządzaniu w Polsce - Lean TWI Summit. Od 2019 roku jestem CEO w firmie Do Lean IT OU zarejestrowanej w Estonii, która tworzy software etwi.io używany przez kilkadziesiąt firm produkcyjnych i usługowych w Europie i USA.