W artykule przedstawiono jak standaryzacja pracy wspiera wdrażanie autonomicznej obsługi maszyn. Zaprezentowano korzyści płynące z wdrażania TPM, AM i standaryzacji pracy. Pokazano w jaki sposób AM jest częścią standaryzacji pracy. W artykule przedstawiono przykłady praktycznych zastosowań standaryzacji w przemyśle.
Korzyści płynące z wdrażania autonomicznej obsługi maszyn – AM
Autonomiczna obsługa maszyn (ang. Autonomous Maintenance – AM) jest fundamentem systemu TPM, który został opracowany w Japonii na początku lat 70-tych ubiegłego wieku. Początki tej filozofii sięgają jednak wczesnych lat 50-tych ubiegłego wieku, kiedy firmy japońskie, wzorując się na przedsiębiorstwach amerykańskich, zaczęły stosować przeglądy konserwacyjne maszyn i urządzeń. Finalną koncepcją systemu TPM było przenoszenie możliwie dużej liczby czynności czyszcząco – konserwacyjnych na maszynach z pracowników utrzymania ruchu na pracowników bezpośrednio produkcyjnych. To operatorzy zaczęli odgrywać w systemie TPM znaczącą rolę, a wykonywane przez nich zadania konserwacyjne nazwane zostały właśnie autonomiczną obsługą maszyn. Duży potencjał dostrzeżony w operatorach wynikał głównie z tego, że to właśnie oni są najbliżej maszyn i najszybciej są w stanie reagować na ich problemy. Ponadto operatorów produkcyjnych w praktyce jest znaczniej więcej niż pracowników działu Utrzymania Ruchu (UR). Dzięki temu łatwiej jest podzielić między nich szereg zadań obsługowych na maszynach.
Wdrażanie procesu AM, jako filaru systemu produkcyjnego danej firmy, zazwyczaj przekłada się na szereg korzyści. Najważniejsze z nich przedstawiono poniżej.
- Poprawa świadomości pracowników w zakresie budowy i eksploatacji maszyn
Celem systemu TPM jest doprowadzenie do takiego stanu, że operator czuje się właścicielem maszyny. Dzięki temu nie tylko ją użytkuje, ale również dba o jej obsługę. Ewolucję procesów obsługowych na maszynach można przyrównać do opieki rodziców nad dziećmi (Rys. 1). Najważniejsze w tym procesie jest budowanie świadomości rodziców (operatorów), którzy w przypadku dostrzeżenia problemu (np. wysypki) przy codziennym „czyszczeniu i konserwacji” swojego dziecka (maszyny) poinformują o tym lekarza (służby UR). Przy każdym kolejnym dziecku (maszynie) świadomi rodzice (operatorzy) będą w stanie część problemów usuwać samodzielnie, bez konieczności wzywania lekarza (służb UR). Zdobędą doświadczenie, które jest kluczem w dobrym rodzicielstwie, jak i systemie TPM. Odciążą przy tym służbę zdrowia (Dział UR)!
Rys. 1. Autonomiczna obsługa dzieci i maszyn
- Mniejsza awaryjność maszyn poprzez zaangażowanie operatorów do zgłaszania usterek
Dzięki budowaniu świadomości operatorzy są w stanie dostrzegać usterki (anomalie) na maszynach i informować o nich służby UR, zanim te usterki przerodzą się w awarie i spowodują długi postój maszyn. To świadomość powoduje, że w przypadku niepokojącego stukania, czy wycieku, operator uda się z problemem do działu UR, a nie pominie je, bo przecież maszyna nadal „idzie”. Wspomniane usterki mogą być wychwytywane przez operatorów zarówno przy pracy maszyny, jak i wykonywania czynności AM. Sytuacja taka wystąpi wyłącznie wtedy, kiedy operatorzy będą wiedzieć na co zwracać uwagę.
- Poprawa wskaźnika całkowitej efektywności wykorzystania maszyn (ang. Overall Equipment Efficiency – OEE).
Usterki nie tylko poprzedzają awarię. Mogą również mieć wpływ na przedłużanie się procesów przezbrajania maszyn, obniżenie ich prędkości, powstawanie mikro-przestojów, tworzenie braków, czy wydłużanie czasu rozruchu. Te wszystkie 6 wielkich strat przekłada się na obniżenie efektywności. Im więcej usterek będzie identyfikowanych przez operatorów, tym większa szansa na eliminację tych strat i poprawę efektywności wykorzystania maszyny, a tym samym wskaźnika OEE.
- Skrócenie średniego czasu awarii maszyn (ang. Mid Time Between Failures – MTBF) dzięki szybszemu czasowi reakcji na awarię.
Operatorzy są bliżej maszyny i mogą podjąć podstawowe działania naprawcze zanim przy maszynie zjawią się służby UR. Właśnie dlatego w ramach działań AM wielokrotnie tworzy się standardy reakcji operatora na awarię (np. przy zatrzymaniu maszyny wykonuje się zdefiniowane kroki zanim powiadomią się służby UR). Dzięki temu naprawa awarii następują o wiele szybciej, niż jest to w tradycyjnym modelu, w którym: „Produkcja jest od produkowania, a UR od naprawiania maszyn”.
Rola operatorów jest szczególną cechą systemu TPM, ponieważ wymaga pełnego i świadomego zaangażowania personelu produkcyjnego do wykonywania czynności obsługowych na maszynach. Ta świadomość jest szczególnie ważna! Buduje się ją poprzez szkolenia i treningi. To jeden z podstawowych elementów metodyki wdrażania AM, która składa się z 7 kroków:
- Gruntowne czyszczenie i sprawdzanie maszyny.
- Oznaczanie i eliminacja źródeł zabrudzeń.
- Określenie standardów czyszczenia i konserwowania.
- Szkolenie pracowników z zakresu codziennej autonomicznej konserwacji.
- Wdrażanie i nadzorowanie samodzielnej codziennej konserwacja maszyn przez operatora.
- Wdrażanie rozwiązań w zakresie poprawy organizacji i porządku poprzez sterowanie wizualne.
- Proces ciągłego doskonalenia.
Standaryzacja pracy – klucz do budowania świadomości operatorów przy wdrażaniu procesu AM
Słysząc określenie standaryzacja pracy, zapewne w pierwszej chwili pomyślałeś o instrukcjach wywieszonych gdzieś przy stanowisku pracy. To niestety powszechnie przyjmowane podejście, w którym proces standaryzacji pracy sprowadza się wyłącznie do dokumentowania. Należy zastanowić się, czy wisząca instrukcja przy stanowisku pracy zmienia cokolwiek w procesie produkcyjnym? Odpowiedź jest oczywiście przecząca! W firmach, w których standaryzację sprowadza się wyłącznie do dokumentowania, instrukcje pełnią rolę zaledwie estetyczną i formalną. Zazwyczaj wiszą przy stanowisku prze nikogo nietknięte, no może poza audytorem zewnętrznym.
Nie ulega jednak wątpliwości, że instrukcje przy standaryzacji pracy są istotne! Służą jednak wyłącznie do efektywnego poprowadzenia instruktażu stanowiskowego albo poddania operacji procesowi doskonalenia. Instrukcje są zatem wyłącznie środkiem pośrednim do osiągnięcia celu, jakim jest standaryzowanie procesu produkcyjnego. Instrukcje nie są celem samym w sobie. Czy wobec tego ważne jest w ogóle opracowywanie instrukcji stanowiskowych? Oczywiście, że tak! Jakość wykonania instrukcji wpływa w sposób znaczący na prowadzenie instruktażu stanowiskowego, jak i procesu analizy pracy pod względem doskonalenia. Jakość instrukcji ma istotny wpływ na budowanie świadomości operatorów. Standaryzacja pracy to zatem proces, w którym należy zapisać obecnie najlepszy sposób wykonywania operacji, poddać go doskonaleniu, a następnie przeszkolić z niego operatorów (Rys. 2). Cały problem polega na tym, że nie jest to zadanie łatwe!
Rys. 2. Trzy główne elementy standaryzacji pracy
Standaryzacja pracy niesie za sobą szereg korzyści. Wymaga jednak wcześniejszego ustabilizowania procesów, co wiąże się z:
- eliminacją zagrożeń na stanowisku pracy;
- eliminacją podstawowych problemów na maszynie (usterek, niezgodności);
- zorganizowaniem wysokiej jakości stanowiska pracy (porządek, czystość).
Nie ma możliwości poprawnej standaryzacji pracy bez wcześniejszej stabilizacji procesów. W tabeli 1 przedstawiono w jaki sposób standaryzacja pracy łączy się z metodyką wdrażania procesu AM.
Tab. 1. Związek pomiędzy siedmioma krokami autonomicznej konserwacji a standaryzacją procesów produkcyjnych
Nr kroku | Krok programu Autonomicznej Konserwacji | Element standaryzacji pracy | |
---|---|---|---|
1 | Gruntowne czyszczenie i sprawdzanie maszyny |
Stabilizacja procesu | |
2 | Oznaczanie i eliminacja źródeł zabrudzeń | ||
3 | Określenie standardów czyszczenia i konserwowania | Dokumentowanie standardów pracy | Standaryzacja procesów |
4 | Szkolenie pracowników z zakresu codziennej autonomicznej konserwacji |
Szkolenie ze standardów i ich utrzymywanie | |
5 | Wdrażanie i nadzorowanie samodzielnej codziennej konserwacja maszyn przez operatora | ||
6 | Wdrażanie rozwiązań w zakresie poprawy organizacji i porządku poprzez sterowanie wizualne |
Usprawnianie standardów | |
7 | Proces ciągłego doskonalenia |
Szczególnie istotne jest standaryzowanie autonomicznych działań obsługowych na maszynach, ponieważ największa rotacja pracowników występuje zazwyczaj w obszarze produkcji. Działy UR przeważnie cechują się małą rotacją i niewielką zmiennością zatrudnienia. W obszarze produkcji takie zmiany są powszechne, dlatego często dochodzić musi do instruktażu, który jest istotną częścią standaryzacji pracy. To wymaga natomiast opracowania bardzo dobrych instrukcji pracy, które wspierają ten proces!
Sprawne tworzenie instrukcji AM jako kluczowy problem przy skutecznym standaryzowaniu autonomicznych procesów obsługowych na maszynach
Jak wspomniano wcześniej, instrukcje są tylko elementem niezbędnym do szkolenia pracowników i doskonalenia pracy. Jednak ich jakość ma kluczowe znaczenia przy efektywności tych działań. Docelowo, przy wdrażaniu systemu TPM w dowolnej fabryce, wszystkie maszyny powinny mieć opisane zadania AM. Jednak każda z maszyn te zadania może mieć zupełnie inne. Przygotowanie instrukcji AM wymaga dużego wysiłku i nakładu czasu pracy, ponieważ dobra instrukcja AM powinna zawierać:
- sekwencję czynności (co się wykonuje) – główne kroki,
- sposób wykonania czynności (jak to się wykonuje) – wskazówki,
- przyczynę wykonania czynności w określony sposób (dlaczego to się wykonuje tak, a nie inaczej) – przyczyny,
- czas wykonania czynności (jak długo się to wykonuje),
- narzędzia i materiały potrzebne do wykonania czynności (czym się to wykonuje),
- zdjęcia, które pokazują sposób wykonania czynności – obrazują wskazówki.
Dzięki objaśnieniu w instrukcjach AM wskazówek i przyczyny ich występowania wpływa się na eliminację błędów ludzkich. Człowiek bowiem uczy się dowolnej operacji, kiedy dowiaduje się, jak ją należy wykonać (wskazówki) i dlaczego taki sposób wykonania jest najlepszy (przyczyny). W znaczącej większości fabryk, w których wdrażałem system TPM, instrukcje AM zawierały wyłącznie kroki często wymieszane ze wskazówkami, ale brak było w nich przyczyn. Sprawdź instrukcje AM w swojej fabryce i zwróć uwagę, czy występują w nich przyczyny. Z dużą dozą prawdopodobieństwa mogę stwierdzić, że nie! Należy pamiętać, że świadomość ludzi buduje się mówiąc im dlaczego, a nie wyłącznie jak, mają to robić! Świadomość ludzi buduje się poprzez uzasadnienie istotności pracy. Francis Bacon powiedział kiedyś, że: Prawdziwa wiedza to znajomość przyczyn.
Instrukcje spełniające powyższe cechy nazywa się instrukcjami pracy standaryzowanej (ang. Standard Work Instruction – SWI). Na rysunku 3 przedstawiono przykładową instrukcję AM z firmy LG Display Poland sp. z o.o., gdzie wspomagałem wdrażać system TPM. Instrukcja ta spełnia wszystkie cechy przypisywane SWI. Stanowi ona bardzo dobrą bazę pod instruktaż stanowiskowy i doskonalenie metod pracy.
Rys. 3. Przykład instrukcji AM zbudowanej w oparciu o zasady tworzenia SWI
Źródło: Wolak M., Kotlarski B., Maczuga M., 5S Fundamentem Trwałego Systemu TPM, Materiały Konferencyjne do XIV Konferencja Lean Management 10-12.06.2014, Wrocław
Niestety czas opracowania SWI jest bardzo długi. Szczególnie w wersji elektronicznej. W praktyce jest tak, że rozpisanie czynności na kartce papieru na hali produkcyjnej zajmuje około 15 minut. Kolejne 10 minut to wykonanie zdjęć do SWI. Natomiast zapisanie SWI w formie elektronicznej instrukcji zajmuje zazwyczaj około 60 minut! I to dla osoby doświadczonej w obsłudze programów edycyjnych. Sporym wyzwaniem jest poprawne sformatowanie instrukcji, dodanie symboli na zdjęciach itd. SWI powinni tworzyć liderzy i operatorzy z największym doświadczeniem. Często te osoby nie mają znajomości obsługi programów edycyjnych, stąd w firmach powoływana jest specjalna osoba, która zajmuje się przepisywaniem instrukcji napisanych przez operatorów i liderów. Wówczas często dochodzi do pomyłek i przeinaczeń. Pojawiają się wtedy marnotrawstwa: zbędne przetwarzanie i nadmierna komunikacja. Uważam, że SWI w formie elektronicznej również powinni tworzyć operatorzy i liderzy. Ale to wymaga przygotowania odpowiedniego systemu IT, który będzie ich w tym wspomagał.
Systemy IT rozwiązaniem przy skutecznym standaryzowaniu autonomicznych czynności obsługowych na maszynach!
Instrukcje pracy standaryzowanej (SWI) są fundamentem przy efektywnym prowadzeniu instruktażu stanowiskowego, który opiera się na relacjach pomiędzy trenerem i uczniem. Stosowanie rozwiązań IT przy instruktażu stanowiskowym może być wyłącznie dodatkiem, który urozmaica ten proces. Nie jest jednak warunkiem koniecznym. Zupełnie odwrotna sytuacja występuje w przypadku tworzenia SWI, które muszą powstawać w formie elektronicznej. Nie tylko dlatego, że jest to bardziej estetyczna forma prezentacji, ale przede wszystkim instrukcje te ulegają ciągłym zmianom, a to wymaga ich aktualizacji.
Dobry system tworzenia instrukcji pracy standaryzowanej musi być przy tym intuicyjny i prosty dla użytkownika. System powinien mieć wbudowane najważniejsze zasady tworzenia SWI, min. takie jak:
- Określoną liczbę słów, którą należy używać do opisania głównych kroków, wskazówek i przyczyn występowania wskazówek (np. maksymalnie 5 słów do opisania głównych kroków i wskazówek);
- Informację o tym, jakich słów nie używać przy tworzeniu SWI (np. właściwy wymiar, czy odpowiedni rozmiar);
- Sposób mierzenia czasu wykonania głównego kroku (określenie najkrótszego powtarzalnego czasu wykonania);
- Informacje, jak wykonywać zdjęcia, aby skutecznie obrazowały wskazówki (jaka perspektywa, na co zwracać uwagę);
- Sposób przypisania symboli do przyczyn występowania wskazówek (kategoria przyczyn związanych z: BHP, jakością, poprawnością i trikami);
Celem systemu IT powinno być spowodowanie, aby każda osoba, nawet ta która ma małą wiedzę o obsłudze komputerów, była w stanie sama opracować SWI w formie elektronicznej w maksymalnie 10 minut. To oszczędność blisko 50 minut pracy na jedną instrukcję! Praca człowieka przy tworzeniu wersji elektronicznej powinna sprowadzać się wyłącznie do wypełnienia komórek treścią (główne kroki, wskazówki i przyczyny), zaciągnięcia wykonanych zdjęć, oznaczenia punktów kluczowych strzałkami i wydrukowania instrukcji do formatu PDF. Beż żadnego formatowania i edycji ze strony człowieka. To powinna być rola systemu informatycznego!
Wdrażanie standaryzacji prac niejednokrotnie zostaje wstrzymane w firmach w wyniku ogromu pracy związanego właśnie z tworzeniem instrukcji w nowy, lepszy sposób. Należy pamiętać, że kluczem w pracy standaryzowanej jest szkolenie pracowników i doskonalenie metod pracy. Jednak te działania nie są możliwe bez dobrych instrukcji pracy standaryzowanych. Systemy informatyczne powinny wspierać ich tworzenie.
Informacje o artykule:
Artykuł opublikowany w magazynie Służby Utrzymania Ruchu (wrzesień – październik 2015).
Autor:
Dr inż. Bartosz Misiurek
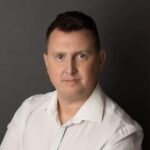
Jestem popularyzatorem Lean Management oraz programu Training Within Industry. Jestem praktykiem. Współtworzę wiele startupów. Od 2015 roku jestem CEO w Leantrix - czołowej firmie z zakresu konsultingu Lean w Polsce, która począwszy od 2024 roku organizuje jedną z największych konferencji poświęconych szczupłemu zarządzaniu w Polsce - Lean TWI Summit. Od 2019 roku jestem CEO w firmie Do Lean IT OU zarejestrowanej w Estonii, która tworzy software etwi.io używany przez kilkadziesiąt firm produkcyjnych i usługowych w Europie i USA.