Filozofia Lean Management (z ang. szczupłe zarządzanie, zwana dalej Lean) w co raz większej liczbie przedsiębiorstw staje się sposobem na kompleksowe zarządzanie ich procesami. Już od kilkunastu lat filozofia ta nie jest wyłącznie kojarzona z produkcją. Obecnie powszechnie stosowana jest w obszarach: usługowych, administracyjnych, czy służbie zdrowia. Jej skuteczne stosowanie wymaga od pracowników poznania szeregu metod i narzędzi, które wchodzą w jej skład. Kluczem do efektywnego wdrożenia tych metod w organizacji jest przede wszystkim zrozumienie, czym tak naprawdę Lean jest. Niestety o filozofii tej krąży wiele błędnych stereotypów traktujących ją wyłącznie jako „skrzynkę z narzędziami” optymalizującymi procesy w firmie. Ten artykuł będzie miał na celu obalić część z tych stereotypów.
Artykuł ten jest zbiorem komentarzy do wybranych odpowiedzi udzielonych przez ankietowanych w ogólnokrajowej ankiecie o szczupłym zarządzaniu. Na potrzeby ankiety opracowano 11 pytań, które swoim zakresem obejmowały całą istotę wdrażania filozofii szczupłego zarządzania. Pytania zadane w ankiecie nie były nastawione na sprawdzane wiedzy o Lean, ale poziomu świadomości na temat tej filozofii. W artykule skomentowano tylko te zagadnienia, na które większość odpowiedzi, zdaniem naszego eksperta, były błędne. Odpowiedzi na pytania zostały przedstawione w takiej sekwencji, aby przeprowadzić Państwa przez proces wdrażania systemu 5S.
Ankieta została wypełniona przez 380 osób i prowadzona była przez 2 miesiące. Promowana była przez wiele specjalistycznych portali, takich jak HrPolska.pl.
Ankieta była przeznaczona dla osób, które deklarowały znajomość filozofii Lean. Każda z osób poproszona została o określenie poziomu tej znajomości (Rysunek 1). Ponadto 46% ankietowanych osób zadeklarowało, że pracuje w firmach, gdzie filozofia Lean jest wdrażana i stosowana w codziennych działaniach.
Rys. 1. Ocena poziomu wiedzy o szczupłym zarządzaniu
Ankieta miała na celu sprawdzić poziom zrozumienia Lean, również wśród pracowników działów HR. Spośród wszystkich osób, które wypełniły ankietę, aż 56% pracuje na co dzień w obszarze zarządzania personelem.
Schemat części merytorycznej artykułu będzie zbliżony dla każdego z wybranych pytań z ankiety. Po przedstawieniu pytania, zaprezentowane zostaną wyniki odpowiedzi ankietowanych, odpowiedź eksperta oraz jego komentarz.
Czy Lean Management to przede wszystkim zbiór metod i narzędzi zorientowanych na optymalizację i poprawę wydajności pracy?
Rys. 2. Odpowiedzi ankietowanych
Odpowiedź eksperta: NIE
To jeden ze stereotypów na temat filozofii szczupłego zarządzania. Lean to przede wszystkim sposób zarządzania przedsiębiorstwem, a nie tylko zbiór metod i narzędzi optymalizacyjnych. Firmy, które na poważnie chcą wdrożyć filozofię Lean powinny rozpocząć ten proces od ustalenia celów ich organizacji w obszarach: jakości, kosztów, produktywności, efektywności, bezpieczeństwa i rozwoju ludzi. Dla tych celów należy następnie określić mierzalne zadania, a dopiero dla tych zadań zdefiniować wymagane metody i narzędzia (Rysunek 3). To podejście nazywa się Hoshin Kanri (Hoshin z jap. „kierunek,” „lśniąca igła”, „kompas”, Kanri z jap. „zarządzanie”).
Rys. 3. Podejście Hoshin Kanri do zarządzania przedsiębiorstwem
Źródło: Opracowanie własne na podstawie Hutchins D., Hoshin Kanri: The Strategic Approach to Continuous Improvement, Gower Publishing Limited, England: 2008
Podejście to stało się fundamentem Toyota Production System (z ang. System Produkcyjny Toyoty, zwany dalej TPS). Głównym celem tego podejścia jest:
- Identyfikacja głównych problemów organizacji.
- Struktura oparta o PDCA.
- Atmosfera sprzyjająca kreatywności i ciężkiej pracy.
Metody i narzędzia są bardzo istotne w filozofii Lean, ale ich użycie ma być efektem ustalonych wcześniej celów i konkretnych zadań. Ponadto metody i narzędzia Lean nie tylko wpływają na poprawę produktywności i wydajności pracy. W Lean znacząca część metod zorientowana jest przede wszystkim na rozwój ludzi (Lean HR, PDCA, Kółka Jakości itd.) oraz poprawę jakości świadczonych usług (Jidoka, Poka Yoke, 5xDlaczego itd.).
Z moich doświadczeń wynika, że większość niepowodzeń we wdrażaniu filozofii Lean w przedsiębiorstwach bierze się z tego, że firmy te zorientowane są wyłącznie na wdrażanie poszczególnych metod i narzędzi, bez wcześniej określonego celu. Takie działanie można przyrównać do strzelania z łuku do celu z zamkniętymi oczami. Jest to mało skuteczne, choć niestety najczęściej stosowane podejście przy wdrażaniu filozofii Lean.
Czy najważniejszym celem Lean Management jest eliminacja marnotrawstwa (jap. muda)?
Rys. 4. Odpowiedzi ankietowanych (rysunek powyżej)
Odpowiedź eksperta: NIE
Najczęściej filozofia Lean kojarzona jest z eliminacją marnotrawstwa (jap. Muda). Marnotrawstwo to każdy rodzaj pracy, który nie powoduje dodawania wartości dla klienta. Wyszczególnia się 7 typów marnotrawstwa[1]:
- zapasy,
- nadprodukcja,
- poprawianie braków i błędów,
- zbędne przetwarzanie,
- zbędne przemieszczanie materiału,
- nadmierny ruch,
- oczekiwanie
W Lean Management eliminacja marnotrawstwa to bardzo ważny element poprawy efektywności, jednak nie najważniejszy! W Lean chodzi przede wszystkim o wyszczuplanie przypływu materiału i informacji. To, co ten przepływ zakłóca, to właśnie marnotrawstwo. Dlatego przyjmuje się, że marnotrawstwo jest efektem nieregularności i nadmiernego obciążenia (Rysunek 5).
Rys. 5. Hierarchia celów Lean Management wg Toyota Production System
Źródło: Opracowanie własne na podstawie Shook J., Marchwinski C., Lean Lexicon: A Graphical Glossary for Lean Thinkers, Cambridge: 2014
Najważniejszym celem filozofii Lean jest zatem eliminacja wszelkich nieregularności, które wpływają na zachwianie przepływu informacji i materiału w firmie (jap. Mura). Efektem tej nieregularności jest nadmierne obciążenie pracą (jap. Muri), a to dopiero powoduje pojawianie się marnotrawstwa (jap. Muda). Podstawą skutecznego rozwiązywania problemów jest uderzanie w ich przyczyny źródłowe, którymi w tej sytuacji są wszelkie nieregularności w procesie (jap. Mura), a nie marnotrawstwo (jap. Muda).
Schodząc na grunt praktyki, wdrażanie Lean powinno zaczynać się od mapowania procesów, gdyż to ono wskazuje nieregularności. Następnie należy z mapy stanu obecnego wyszczególnić nadmierne obciążenia procesu, które to powodują marnotrawstwo. Dopiero wtedy należy użyć metod i narzędzi zorientowanych na eliminację tego marnotrawstwa.
Czy Lean HR to eliminacja 7 typów marnotrawstwa w dziale HR?
Rys. 6. Odpowiedzi ankietowanych
Odpowiedź eksperta: NIE
Lean HR to koncepcja zarządzania rozwojem pracowników w przedsiębiorstwie. Mylnie utożsamiana jest ze stosowaniem filozofii Lean w Dziale HR. Niektóre z firm uważają, że poprzez redukcję 7 typów marnotrawstwa w procesach wykonywanych w Dziale HR (np. eliminację błędów i poprawek w zakresie wykonywania oceny pracowniczej, skrócenie czasu przetwarzania dokumentacji kadrowej itp.), wdrażają podejście Lean HR. To nie prawda. Takie działanie, jak przedstawione w przykładach powyżej, jest tożsame dla podejścia Lean Office (z ang. szczupłe zarządzanie w biurze). Lean HR polega na wspieraniu zaangażowania i rozwoju pracowników. Jej głównym celem jest eliminacja 8. typu marnotrawstwa: utraconej kreatywności pracowników. To marnotrawstwo jest często pomijane przez kierownictwo firm, ponieważ nie wpływa bezpośrednio na poprawę KPI`s (z ang. kluczowe wskazówki efektywności przedsiębiorstwa). Kierownictwo w firmach najczęściej skupia się wyłącznie na usprawnianiu procesów związanych z organizacją pracy i rozwiązaniami technicznymi zapominając, że duży potencjał do poprawy tkwi w pracownikach. Utracona kreatywność pracowników jest dużym problemem, ponieważ wpływa pośrednio na występowanie pozostałych 7 typów marnotrawstwa. Lean HR pomaga właśnie pobudzić kreatywność wśród pracowników. Wdrażanie Lean HR jest niezbędne, aby skutecznie wdrożyć w przedsiębiorstwie filozofię Lean. Więcej o podejściu Lean HR dowiesz się czytając artykuł: Jak efektywnie wdrażać szczupłe zarządzanie?, który opublikowany jest w tym numerze.
Czy najważniejszym celem systemu 5S jest utrzymanie czystości, ładu i porządku na stanowisku pracy?
Rys. 7. Odpowiedzi ankietowanych (rysunek powyżej)
Odpowiedź eksperta: NIE
System 5S to jedno z podstawowych narzędzi należących do filozofii Lean Management zorientowane na poprawę jakości stanowiska pracy. Nazwa systemu 5S wywodzi się od następujących po sobie krokach[2]:
- S – Sortowanie (jap. Seiri).
- S – Systematyka (jap. Seiton).
- S – Sprzątanie (jap. Seiso).
- S – Standaryzacja (jap. Seiketsu).
- S – Samodyscyplina (jap. Shitsuke).
Błędnie jednak przyjmuje się, że najważniejszym celem systemu 5S jest utrzymanie porządku i ładu na stanowisku pracy. Tak, to ważny element. Jeżeli jednak byłby on najważniejszy to wówczas wdrażanie tego systemu kończyło by się na 3.S – sprzątaniu. Głównym celem systemu 5S jest doskonalenie stanowiska pracy. Odbywa się ono poprzez standaryzację, gdzie w ramach działań kaizen (z jap. ciągłe doskonalenie) powstają rozwiązania usprawniające, takie jak kontrola wizualna. Na Rysunku 8 przedstawiono zastosowanie kontroli wizualnej do zarządzania segregatorami klientów w Biurze Rachunkowym. Powstałe rozwiązania były efektem działań podczas wdrażania systemu 5S. Kolor segregatorów jest przydzielony do każdego pracownika, który opiekuje się danymi klientami. Ponadto każdy segregator posiada magnetyczną tabliczkę znamionową, na której znajduje się jego numer oraz miejsce na oznaczenie brakujących dokumentów. Dzięki temu w przeciągu kilku sekund patrząc na wszystkie segregatory można stwierdzić, w których z nich brakuje jeszcze niezbędnych dokumentów. Głównym celem tego rozwiązania nie było utrzymanie porządku, a skrócenie czasu identyfikacji segregatorów z brakującymi dokumentami. To efekt doskonalenia pracy, a nie sprzątania.
Rys. 8. Przykład zastosowania sterowania wizualnego w systemie 5S.
Źródło: Rozwiązanie przedstawione za zgodą Biura Rachunkowego Mismart
Pierwsze 3S (sortowanie, systematyka i sprzątanie) zorientowane są zatem wyłącznie na stabilizację procesu. To w tych krokach należy doprowadzić stanowisko do czystości i ładu, tak aby poddać go w 4.S – standaryzacji. Równie istotnym krokiem w systemie 5S jest samodyscyplina (5.S), którą rozwija się poprzez uświadamianie pracowników oraz proces audytowania. Należy zatem traktować system 5S jako narzędzie doskonalące, w którym porządek i ład jest efektem wprowadzonych usprawnień i procesu audytowania.
Czy w Lean Management standaryzacja pracy związana jest głównie z tworzeniem standardów pracy?
Rys. 9. Odpowiedzi ankietowanych
Odpowiedź eksperta: NIE
Standaryzacja pracy to fundament w TPS. To również 4.S w systemie 5S. Z pewnością słysząc określenie standaryzacja pracy, w pierwszej chwili pomyślałeś o instrukcjach wywieszonych gdzieś przy stanowisku pracy. To niestety powszechnie przyjmowane podejście, w którym proces standaryzacji pracy sprowadza się wyłącznie do dokumentowania. Należy zastanowić się, czy wisząca instrukcja przy stanowisku pracy zmienia cokolwiek w procesie? Odpowiedź jest oczywiście przecząca! W firmach, w których standaryzację sprowadza się wyłącznie do dokumentowania, instrukcje pełnią rolę zaledwie estetyczną i formalną.
Instrukcje przy standaryzacji pracy są ważne! Służą jednak wyłącznie do efektywnego poprowadzenia instruktażu stanowiskowego albo poddania operacji procesowi doskonalenia (kaizen). Instrukcje są zatem wyłącznie środkiem pośrednim do osiągnięcia celu, jakim jest standaryzowanie procesu produkcyjnego. Instrukcje nie są celem samym w sobie. Czy wobec tego ważne jest w ogóle opracowywanie instrukcji stanowiskowych? Oczywiście, że tak! Jakość wykonania instrukcji wpływa w sposób znaczący na prowadzenie instruktażu stanowiskowego, jak i procesu analizy pracy pod względem doskonalenia. Jakość instrukcji ma istotny wpływ na budowanie świadomości operatorów. Standaryzacja pracy to zatem proces, w którym należy zapisać obecnie najlepszy sposób wykonywania operacji, poddać go doskonaleniu, a następnie przeszkolić z niego operatorów (Rysunek 10).
Rys. 10. Trzy główne elementy standaryzacji pracy
Źródło: Misiurek Bartosz, Rola standaryzacji w autonomicznej obsłudze maszyn, Służby Utrzymania Ruchu, wrzesień – październik 2015, str. 47-51
Odpowiedź na pytanie postawione w ankiecie jest przecząca, gdyż dwoma głównymi celami standaryzacji jest:
- Szkolenie pracowników, aby wykonywali oni pracę poprawnie, bezpiecznie i świadomie.
- Doskonalenie metod pracy.
Instrukcje i standardy są tylko po to, aby te dwa główne cele osiągnąć. Zwróć uwagę raz jeszcze na przykład z segregatorami (Rysunek 8). Na ile byłoby to skuteczne rozwiązanie, gdyby nie opracowano dla niego instrukcji postępowania i nie przeszkolono by w oparciu o nią pracowników?
Czy za zgłaszane wnioski Kaizen powinno płacić się pracownikom pieniądze?
Rys. 11. Odpowiedzi ankietowanych
Odpowiedź eksperta: TO ZALEŻY
Kaizen to pochodzące z języka japońskiego określenie, które oznacza orientację na ciągłe doskonalenie. Dosłownie kaizen tłumaczy się jako: dobrą zmianę. W praktyce to podejście niesie za sobą pewne fundamentalne zasady, takie jak: praca zespołowa, nastawienie na usuwanie źródła problemów, posługiwanie się faktami i danymi czy zaangażowanie każdego pracownika. Są dwa rodzaje podejścia kaizen[3]:
- Kaizen przepływu,
- Kaizen procesu.
Kaizen przepływu zorientowany jest na doskonalenie przepływu materiału i informacji. Często utożsamiany jest z reorganizacją całego obszaru produkcyjnego, a nawet przedsiębiorstwa. Kaizen procesu to natomiast usprawnianie pojedynczych stanowisk pracy. Doskonalenie sposobu pracy pracowników produkcyjnych jest zatem częścią kaizen procesu. Natomiast model kaizen łączy te dwa podejścia. Z założenia dominować ma jednak kaizen procesu, który oznacza koncentrację pracowników na ciągłych, drobnych usprawnieniach. Jest to zupełnie inna koncepcja niż w podejściu do doskonalenia w modelu tradycyjnym, który opiera się na dużych projektach reorganizacyjnych. W takiej sytuacji czas pomiędzy powstaniem koncepcji a realizacją projektu jest bardzo długi. W modelu kaizen szuka się głównie drobnych pomysłów, które można wdrożyć najlepiej tego samego dnia. Na Rysunku 12 pokazano różnicę pomiędzy modelem kaizen a modelem tradycyjnym.
Rys. 12. Różnica pomiędzy modelem kaizen a modelem tradycyjnym przy doskonaleniu pracy
Źródło: Misiurek B., Metodyka standaryzacji autonomicznych procesów eksploatacyjnych zorientowana na poprawę efektywności maszyn zautomatyzowanych, Uniwersytet Technologiczny we Wrocławiu, praca doktorska, Wrocław: 2014, s.126
W modelu tradycyjnym tworzy się grupy projektowe i poświęca się dużo czasu na analizę. Wymagane jest również, przy każdym projekcie, zaangażowanie szeregu działów, takich jak: służby BHP, dział finansowy, dział jakości itd. Realizacja wniosków reorganizacyjnych jest zdecydowanie lepsza, niż w ogóle brak podejmowania inicjatyw doskonalących. To pewne! Problemem jest to, że działań reorganizacyjnych, ze względu na czas i koszty może być maksymalnie kilka w roku. Czasami zdarzają się sytuacje, gdzie zostaje przeprowadzona pełna analiza przedwdrożeniowa, a projekt reorganizacyjny upada ze względu na zmianę np. budżetu. Drobne usprawnienia, będące częścią modelu kaizen, mają to do siebie, że są odporne na takie sytuacje. Głównie ze względu na krótki okres wdrożenia. Dzięki temu takich usprawnień mogą być tysiące! Przewaga modelu kaizen nad modelem tradycyjnym polega więc na efekcie skali. W modelu kaizen najistotniejszym jest skracanie czasu pomiędzy wypracowaniem koncepcji, czy też zdefiniowaniem problemu, a samym wdrożeniem usprawnienia. I wcale nie jest tak, że w modelu kaizen istnieją wyłącznie małe usprawnienia. Zwróć raz jeszcze uwagę na Rysunek 12. Tam w modelu kaizen również zdarzają się wyższe schody symbolizujące duże projekty usprawniające związane z kaizen przepływu. Jednak zdecydowanie dominują małe usprawnienia – kaizen procesu. Są one zgłaszane zazwyczaj przez pracowników. I to tutaj pojawia się pytanie: czy płacić za zgłoszone wnioski kaizen? Pierwsza podpowiedź jest taka: jeżeli płacić, to nie za zgłoszone, ale za wdrożone rozwiązania! W kaizen chodzi o to, aby to zgłaszający dany pomysł był w stanie wcielić go w życie. Nie jest wielką sztuką wyłapać marnotrawstwo w procesie, zaproponować rozwiązanie i czekać na jego wdrożenie. Jeżeli tak w firmie budowany jest system kaizen, to zazwyczaj ulega on „zapchaniu” przez nadmierną liczbę wniosków kaizen oraz brak osób, które mogłyby te pomysły wdrażać. Prawdziwy kaizen jest wtedy, kiedy autor wniosku sam go wdroża! Jeżeli ktoś natomiast pyta mnie, czy płacić za wdrożone rozwiązania kaizen to odpowiadam: jeżeli są na to pieniądze to płać! Zawsze warto ludziom płacić za ich pracę. Niestety nie zawsze są na to pieniądze. Wówczas są dwie zasady, którymi się zawsze kieruje:
- Płać za wdrożenie rozwiązań kaizen pracownikom, kiedy wdrażają je po pracy albo w przysługującej im przerwie.
- Nie płać za wdrożenie rozwiązań kazien pracownikom, kiedy robią to w czasie pracy. Wówczas ich aktywność w doskonaleniu traktuj jako część oceny pracowniczej.
Przy zasadzie nr 2 polecam uhonorowywać najbardziej aktywnych pracowników w systemie kaizen np. poprzez przyznanie bonu, karnetu na siłownie, czy innego prezentu, który nie jest finansowy. Takie uhonorowanie może odbywać się standardowo z cyklicznością miesięczną, czy kwartalną.
Pamiętaj, że o tym czy system kaizen zadziała w Twojej firmie decyduje kultura przedsiębiorstwa. Jeżeli będziesz rozwijać swoich pracowników w oparciu o koncepcję Lean HR, będziesz często angażować ich w działania doskonalące, to jestem pewien, że zadziała u Ciebie system kaizen niezależnie czy będziesz płacić za wdrożone rozwiązania kaizen, czy też nie!
Czy głównym celem audytowania w Lean Management jest kontrola pracowników w zakresie przestrzegania zasad (np. systemu 5S)?
Rys. 13. Odpowiedzi ankietowanych
Odpowiedź eksperta: NIE
Opracowanie instrukcji pracy, a także przeszkolenie operatorów, nie gwarantuje, że pracownicy będą zgodnie z tymi instrukcjami pracować. Istotnym elementem kultury doskonalenia, oraz przestrzegania ustalonych standardów pracy, są audyty. Stanowią one 5.S w systemie 5S. Audyt to jednak nie kontrola procesu! Audyt nie jest wymierzony w pracownika, ale jest narzędziem doskonalącym, którego celem jest identyfikacja problemów w procesie i skierowanie działań zaradczych, aby wyeliminować ich przyczyny źródłowe. To znacząca różnica pomiędzy audytowaniem a kontrolą.
Arkusz audytu (Rysunek 14) powinien składać się z pytań zamkniętych, na które odpowiedź powinna być jednoznaczna: TAK lub NIE. Odpowiedź: TAK oznacza, że audytor nie ma żadnych uwag względem audytowanego obszaru albo procesu. Audytor sam, podczas audytowania podejmuje decyzje zakreślając odpowiedź na arkuszu audytu. Posiłkuje się przy tym obserwacją stanowiska, instrukcjami oraz wykonywaną pracą. Każda niezgodność ze standardem pracy powinna zostać zapisana na arkuszu, a zmiany powinny być wdrożone do następnego audytu.
L.p. | Pytanie audytowe | TAK | NIE | Uwagi, jeśli odpowiedź jest na NIE | Proponowane działanie korygujące | Kto? | Do kiedy? |
---|---|---|---|---|---|---|---|
1 | W pokoju jest umieszczony standardowy layout, w standardowym miejscu, a liczba i położenie sprzętu są zgodne z layoutem. | ||||||
2 | Biurka, krzesła i szafki są opisane imieniem i nazwiskiem właściciela. | ||||||
3 | Okablowanie jest zabezpieczone przed ewentualnym szarpnięciem, zaplątaniem. | ||||||
4 | Na czystych biurkach znajdują się wyłącznie przedmioty określone standardem w miejscach dla nich wyznaczonych. W kuwecie dokumentów bieżących oraz na polu dokumentów przychodzących znajduje się rozsądna ilość dokumentów. | ||||||
5 | Oznaczenia (kolorowe taśmy i opisy) są estetyczne (czyste, nie odklejają się). | ||||||
6 | Szuflady biurek są opisane a ich wnętrza zorganizowane i opisane wg standardu. | ||||||
7 | Środki zaradcze z poprzednich audytów zostały w pełni wdrożone. |
Rysunek 14. Przykładowy arkusz audytu systemu 5S
Źródło: Opracowanie własne na podstawie Harris, Rother, Tworzenie Ciągłego Przepływu. Przewodnik dla menadżerów, inżynierów i pracowników produkcji, Lean Enterprise Institute Polska sp. z o.o., Wrocław: 2008, s.93
Audyt jest zatem narzędziem doskonalącym, który ma wyłapywać wszelkie zakłócenia w procesie. Celem audytowania nie jest kontrola pracowników!
Podsumowanie
Celem artykułu było przełamanie kilku stereotypów, które traktują filozofię Lean Management wyłącznie jako narzędzie optymalizujące procesy. Lean Management to przede wszystkim budowanie kultury organizacji zorientowanej na ciągły rozwój i uczenie się pracowników. Ważniejsze od eliminacji marnotrawstwa jest dbanie o rozwój ludzi, bo tylko wtedy będą oni w stanie to marnotrawstwo wychwycić. Na koniec chciałbym odnieść się do jeszcze jednego pytania z ankiety: Czy Lean Management można zastosować w każdej, dowolnej branży? 97% osób ankietowanych odpowiedziało, że tak! Z czym również ja się zgadzam. Lean zadziała wszędzie, gdzie występują procesy i ludzie. Niestety jego wdrożenie wymaga wysiłku, aby przestawić ludzi z codziennego „gaszenia pożarów” na ciągłe doskonalenie! Jest to jednak możliwie, co udowodniło tysiące przedsiębiorstw produkcyjnych i usługowych z całego Świata!
[1] Dolcemascolo D, Improving the Extended Value Stream: Lean for the Entire Supply Chain, New York 2006: Productivity Press, s. 35-40
[2] Hirano H, 5 Pilars of the Visual Workplace, Productivity Press, New York: 1995, s. x-xv
[3] Hamel M.R, Kaizen Event Fieldbook: Foundation. Framework. and Standard Work for effective events, Society of Manufacturing Engineers, Dearborn: 2010, str. 31-32.
Autor:
Dr inż. Bartosz Misiurek
Artykuł opublikowany w magazynie Personel Plus.
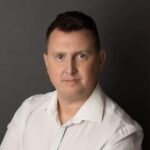
Jestem popularyzatorem Lean Management oraz programu Training Within Industry. Jestem praktykiem. Współtworzę wiele startupów. Od 2015 roku jestem CEO w Leantrix - czołowej firmie z zakresu konsultingu Lean w Polsce, która począwszy od 2024 roku organizuje jedną z największych konferencji poświęconych szczupłemu zarządzaniu w Polsce - Lean TWI Summit. Od 2019 roku jestem CEO w firmie Do Lean IT OU zarejestrowanej w Estonii, która tworzy software etwi.io używany przez kilkadziesiąt firm produkcyjnych i usługowych w Europie i USA.