W ostatnim czasie mieliśmy przyjemność realizować projekt wdrożeniowy u klienta z branży meblarskiej, w którym kluczowym celem było zoptymalizowanie przepływu materiału oraz poprawa efektywności produkcji. Projekt opierał się na wykorzystaniu dwóch sprawdzonych podejść – Value Stream Mapping (VSM) oraz algorytmów i procedur optymalizacji rozmieszczania obiektów – Facility Layout Problem (FLP). Całość odbywała się w w ramach Lean Management. W projekcie uczestniczyli trenerzy Leantrix, inżynierowie procesu, oraz specjaliści Lean, którzy wspólnie analizowali przepływy produkcyjne, identyfikowali źródła marnotrawstwa oraz projektowali nowy layout produkcji. Podczas realizacji projektu konsultowano się z ekspertami w obszarze optymalizacji projektowania layoutów z Politechniki Wrocławskiej – Prof. Jerzy Grobelny i Prof. Rafał Michalski – i wykorzystywano opracowane przez nich metody i narzędzia wspomagające podejmowanie decyzji w tym obszarze.
W niniejszym artykule omówimy:
- Czym jest Value Stream Mapping (VSM) i jaką rolę pełni w identyfikacji problemów produkcyjnych.
- Podstawy Lean Management oraz koncepcję eliminacji marnotrawstwa – w tym osiem typów marnotrawstwa.
- Metodę FLP – jej założenia, praktyczne zastosowanie i znaczenie w projektowaniu layoutu produkcyjnego.
- Case study – szczegółowy opis projektu u klienta z branży meblarskiej, gdzie zastosowano VSM i FLP, a także omówienie osiągniętych rezultatów.
- Podsumowanie oraz bibliografię, z odniesieniami do prac Profesora Rafała Michalskiego i Profesora Jerzego Grobelngo w zakresie FLP, publikacji Johna Sooka i Mike’a Rothera w zakresie VSM oraz książki „The Toyota Way” autorstwa Jeffreya Likera.
Czym jest Value Stream Mapping (VSM) i o co w nim chodzi?
Definicja i cel VSM
Value Stream Mapping (VSM) to metoda wizualizacji i analizy przepływów materiałowych oraz informacji w procesach produkcyjnych lub usługowych. Głównym celem VSM jest identyfikacja wszystkich etapów niezbędnych do przekształcenia surowców w gotowy produkt oraz wykrycie obszarów generujących marnotrawstwo. Dzięki mapowaniu strumienia wartości przedsiębiorstwa mogą:
- Zobaczyć cały proces „oczami” przepływu – od zamówienia po dostarczenie produktu klientowi.
- Identyfikować działania dodające wartość oraz te, które nie przynoszą realnych korzyści.
- Określać punkty, w których można wprowadzić usprawnienia, aby skrócić cykl produkcyjny i obniżyć koszty operacyjne
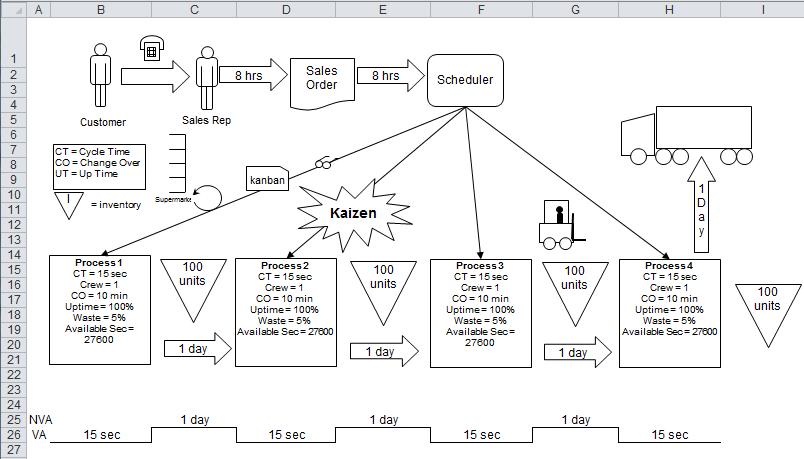
Przykład VSM – źródło
Etapy realizacji VSM
Proces tworzenia mapy przepływu wartości można podzielić na kilka kluczowych etapów:
- Planowanie i przygotowanie: Zbieranie danych o obecnym stanie procesów, takich jak czas cyklu, zapasy, przepływy materiałowe oraz informacje. W tym etapie uczestniczą zarówno pracownicy produkcyjni, jak i specjaliści ds. Lean.
- Tworzenie mapy stanu obecnego: Wizualizacja aktualnego przepływu produkcyjnego, gdzie każdy etap – zarówno dodający wartość, jak i generujący straty – jest dokładnie opisywany.
- Analiza i identyfikacja problemów: Określenie punktów krytycznych, gdzie występują nadmierne zapasy, długie czasy oczekiwania, zbędne przemieszczenia czy inne formy marnotrawstwa.
- Projektowanie mapy stanu przyszłego: Opracowanie koncepcji usprawnień, które mają na celu eliminację zidentyfikowanych problemów. Kluczowe jest zaangażowanie zespołu interdyscyplinarnego.
- Implementacja usprawnień: Wdrożenie zmian w procesie produkcyjnym oraz monitorowanie ich efektów, często w iteracyjnej formie.
Stosowanie metody VSM pozwala przedsiębiorstwom na:
- Redukcję czasów przetwarzania oraz skrócenie cyklu produkcyjnego.
- Identyfikację i eliminację zbędnych operacji, co przekłada się na zmniejszenie kosztów operacyjnych.
- Usprawnienie przepływu informacji między działami, co umożliwia lepszą koordynację i szybsze reagowanie na zmiany w popycie.
- Poprawę jakości produktów oraz zwiększenie satysfakcji klientów.
Lean Management jako orientacja na eliminację marnotrawstwa
Podstawy Lean Management
Lean Management to filozofia zarządzania koncentrująca się na ciągłym doskonaleniu procesów poprzez eliminację marnotrawstwa. Inspiracją dla tej koncepcji była produkcja Toyoty, gdzie dążono do maksymalnej efektywności operacyjnej. Kluczowe zasady Lean Management obejmują:
- Orientację na klienta oraz dostarczanie maksymalnej wartości przy minimalnych zasobach.
- Ciągłe doskonalenie procesów (kaizen).
- Zaangażowanie pracowników na każdym poziomie organizacji.
- Utrzymanie płynności przepływu produkcyjnego oraz eliminację zbędnych zapasów.
Osiem typów marnotrawstwa
W Lean Management koncepcja marnotrawstwa stanowi fundament, który umożliwia identyfikację i eliminację działań nieprzynoszących wartości dodanej dla klienta. Według Taiichi Ohno wyróżnia się osiem podstawowych rodzajów marnotrawstwa, z których każdy wpływa na efektywność operacyjną przedsiębiorstwa:
-
Nadprodukcja:
Produkowanie więcej niż jest wymagane prowadzi do gromadzenia zbędnych zapasów. Nadprodukcja generuje dodatkowe koszty związane z magazynowaniem, utrzymaniem zapasów oraz ryzykiem, że produkty te mogą się przeterminować lub ulec uszkodzeniu. W praktyce, nadprodukcja często maskuje inne problemy w procesach produkcyjnych, takie jak nieefektywne planowanie czy niewłaściwa synchronizacja między działami, co może dodatkowo obciążać system operacyjny przedsiębiorstwa. -
Czas oczekiwania:
Czas oczekiwania to okresy, w których maszyny, pracownicy lub systemy informacyjne są nieaktywne, czekając na rozpoczęcie kolejnego etapu pracy. Może to wynikać z opóźnień w dostawach surowców, awarii sprzętu czy nieprawidłowego planowania procesów. Każda minuta marnowanego czasu oczekiwania wydłuża cykl produkcyjny, co z kolei zwiększa koszty operacyjne i obniża zdolność przedsiębiorstwa do szybkiego reagowania na potrzeby rynku. -
Transport:
Transport oznacza niepotrzebne przemieszczanie materiałów, komponentów lub gotowych produktów między poszczególnymi etapami produkcji. Nadmierne przemieszczanie się może wynikać z nieoptymalnego rozmieszczenia stanowisk pracy lub źle zaprojektowanego layoutu produkcyjnego. Każdy dodatkowy transport generuje koszty – zarówno finansowe, jak i czasowe – oraz zwiększa ryzyko uszkodzenia produktów w trakcie przemieszczania. -
Nadmierny proces:
Nadmierny proces to wykonywanie czynności lub operacji, które nie dodają wartości do produktu. Mogą to być zbędne kontrole, nadmierne formalności czy skomplikowane procedury, które nie wpływają na poprawę jakości finalnego wyrobu. Przeprowadzanie nadmiernych procesów obciąża pracowników, wydłuża cykl produkcyjny i zwiększa koszty, bez przynoszenia realnych korzyści dla klienta. -
Nadmierne zapasy:
Nadmierne zapasy to sytuacja, gdy w magazynach gromadzone są zbyt duże ilości surowców, produktów w toku lub gotowych wyrobów. Utrzymywanie wysokich stanów magazynowych wiąże się z kosztami przechowywania, ryzykiem przeterminowania produktów, a także może prowadzić do problemów związanych z zarządzaniem i rotacją zapasów. Nadmierne zapasy często wynikają z nieoptymalnego planowania produkcji lub niewłaściwego dopasowania produkcji do rzeczywistego popytu. -
Niepotrzebny ruch:
Niepotrzebny ruch dotyczy zbędnych przemieszczeń pracowników podczas wykonywania swoich zadań. Może to obejmować długie drogi pomiędzy stanowiskami, źle zorganizowane miejsce pracy lub brak odpowiednich narzędzi wspomagających pracę. Zbędne ruchy prowadzą do zmęczenia pracowników, zwiększenia ryzyka urazów oraz marnotrawstwa czasu, który mógłby być lepiej wykorzystany na wykonywanie wartościowych działań. -
Wady:
Produkcja wyrobów niespełniających norm jakości, czyli wady, to kolejny rodzaj marnotrawstwa. Niska jakość produktów skutkuje koniecznością przeprowadzania kosztownych poprawek, poprawek lub odrzutów, co generuje dodatkowe koszty i obniża zaufanie klientów do marki. Wady mogą wynikać z niedokładnych procedur kontrolnych, niewłaściwych materiałów czy błędów w procesie produkcyjnym. -
Niewykorzystany potencjał pracowników:
Niewykorzystany potencjał pracowników to sytuacja, w której zdolności, kreatywność i umiejętności pracowników nie są odpowiednio wykorzystywane. Może to wynikać z braku szkoleń, nieodpowiedniej struktury organizacyjnej czy nieangażowania pracowników w procesy decyzyjne. Niewykorzystany potencjał ogranicza innowacyjność oraz możliwości doskonalenia procesów, co w dłuższej perspektywie może wpłynąć negatywnie na konkurencyjność firmy.
Każdy z tych rodzajów marnotrawstwa, choć może wydawać się niezależny, często wzajemnie na siebie oddziałuje. Dlatego eliminacja marnotrawstwa w Lean Management wymaga systematycznego podejścia i ciągłego doskonalenia procesów. Dzięki temu przedsiębiorstwa są w stanie osiągnąć znaczne usprawnienia operacyjne, zmniejszyć koszty produkcji oraz zwiększyć satysfakcję klientów.
Metoda FLP – założenia i praktyczne ujęcie
Podstawy Facility Layout Problem (FLP)
Facility Layout Problem (FLP) to problem optymalizacji rozmieszczenia zasobów w przedsiębiorstwie. Jego celem jest znalezienie takiego układu maszyn, stanowisk pracy czy magazynów, który minimalizuje koszty przepływu materiałów oraz poprawia ergonomię pracy. Główne założenia FLP obejmują:
- Minimalizację sumarycznego kosztu przepływu materiałów, wynikającego głównie z przemieszczania się pracowników i produktów między stanowiskami.
- Optymalne wykorzystanie dostępnej przestrzeni – zarówno pod kątem produkcyjnym, jak i ergonomii.
- Ujęcie kryteriów jakościowych, takich jak bezpieczeństwo i komfort pracy, które często trudno ująć w ścisłe równania matematyczne.
Praktyczne aspekty zastosowania FLP
Wdrożenie metody FLP w praktyce składa się z kilku kluczowych etapów, z których każdy ma istotny wpływ na ostateczną jakość zaprojektowanego układu. Poniżej przedstawiam rozwinięcie poszczególnych etapów:
-
Analiza obecnego layoutu
Na tym etapie przeprowadza się szczegółową analizę istniejącej organizacji przestrzeni produkcyjnej. Kluczowe działania obejmują:- Dokładne pomiary odległości między maszynami, stanowiskami pracy i magazynami, co pozwala na uzyskanie realnego obrazu przestrzennego i identyfikację ewentualnych „wąskich gardeł”.
- Analizę przepływów materiałowych – zarówno surowców, jak i gotowych produktów – w celu określenia, jak efektywnie odbywa się przemieszczanie materiałów w zakładzie. Badane są również ścieżki, które pokonują pracownicy, aby zidentyfikować zbędne przemieszczanie się.
- Ocenę aspektów ergonomicznych stanowisk pracy. W tym celu zbiera się dane dotyczące warunków pracy, dostępu do narzędzi i maszyn, a także bada się, czy obecny układ przestrzeni sprzyja bezpieczeństwu i komfortowi pracowników.
-
Identyfikacja obszarów do poprawy
Na podstawie zebranych danych dokonuje się oceny, które elementy obecnego layoutu powodują marnotrawstwo lub ograniczają efektywność operacyjną. Na tym etapie:- Wskazuje się miejsca, gdzie występują nadmierne przemieszczania – zarówno w obrębie przepływu materiałowego, jak i ruchów pracowników.
- Analizuje się obszary, w których gromadzone są nadmierne zapasy lub dochodzi do opóźnień w dostawie surowców, co wskazuje na potencjalne źródła strat.
- Dokonuje się identyfikacji elementów, które wpływają negatywnie na ergonomię stanowisk pracy – na przykład niewłaściwe rozmieszczenie narzędzi, maszyn lub niewystarczająco przemyślana organizacja przestrzeni, która zmusza pracowników do zbędnych ruchów.
- Wszystkie zidentyfikowane problemy są dokumentowane, co pozwala na precyzyjne określenie, które obszary wymagają zmiany.
-
Projektowanie nowego layoutu
W oparciu o wyniki analizy przystępuje się do projektowania nowego, zoptymalizowanego układu produkcyjnego. Etap ten obejmuje:- Tworzenie nowych propozycji rozmieszczenia maszyn i stanowisk pracy. Do tego celu często wykorzystuje się algorytmy optymalizacyjne, takie jak heurystyki inspirowane symulowanym wyżarzaniem, które umożliwiają generowanie różnych wariantów układu.
- Wykorzystanie technik wizualnych, na przykład scatter plotów, które pozwalają zobrazować potencjalne konfiguracje przestrzenne. Takie narzędzia graficzne pomagają w szybkiej identyfikacji układów, które minimalizują odległości między kluczowymi punktami przepływu materiałów.
- Projektowanie nowego layoutu odbywa się z uwzględnieniem zarówno kryteriów kosztowych (minimalizacja kosztów transportu i przemieszczania), jak i ergonomicznych (poprawa komfortu i bezpieczeństwa pracy). Każda propozycja jest oceniana pod kątem osiągalnych korzyści, a także zgodności z zasadami Lean Management.
-
Wdrożenie i ocena efektów
Ostatnim etapem jest wdrożenie nowo zaprojektowanego layoutu oraz monitorowanie jego efektywności. W praktyce oznacza to:- Stopniowe wprowadzanie zmian – często realizuje się to etapowo, aby umożliwić pracownikom adaptację do nowego układu oraz ułatwić identyfikację ewentualnych problemów na wczesnym etapie wdrożenia.
- Szkolenia dla pracowników, które mają na celu zapoznanie ich z nowymi procedurami i zasadami organizacji pracy, co pozwala na sprawne wykorzystanie nowego layoutu.
- Systematyczne monitorowanie wyników wdrożenia poprzez mierzenie kluczowych wskaźników efektywności, takich jak redukcja kosztów transportu, skrócenie czasu przepływu materiałowego czy poprawa ergonomii stanowisk. Dzięki temu możliwe jest szybkie wykrywanie i korygowanie ewentualnych odchyleń od oczekiwanych rezultatów.
- Ocena efektów wdrożenia pozwala także na zebranie opinii pracowników i kierowników produkcji, co jest cennym źródłem informacji do dalszych usprawnień oraz doskonalenia procesów.
Wdrożenie metody FLP wymaga kompleksowej analizy obecnego stanu zakładu, precyzyjnej identyfikacji obszarów wymagających poprawy, przemyślanego projektowania nowego layoutu oraz systematycznego monitorowania efektów wprowadzonych zmian. Takie podejście nie tylko pozwala na znaczne obniżenie kosztów operacyjnych, ale również przyczynia się do poprawy ergonomii pracy i zwiększenia efektywności całego systemu produkcyjnego.
Integracja FLP z Lean Management
Integracja metody FLP z Lean Management stanowi doskonałe połączenie podejścia analitycznego oraz filozofii ciągłego doskonalenia. W naszym projekcie u klienta z branży meblarskiej:
- Wykorzystaliśmy VSM do identyfikacji problematycznych obszarów i zbędnych przepływów.
- Następnie, na podstawie wyników analizy VSM, przeprowadziliśmy analizę FLP, co pozwoliło zaprojektować nowy układ produkcji z naciskiem na eliminację marnotrawstwa.
- Projekt uwzględniał zarówno optymalizację przepływów materiałowych, jak i poprawę ergonomii stanowisk, co przyczyniło się do zwiększenia komfortu pracy i redukcji ryzyka błędów operacyjnych.
Case Study – Wdrożenie VSM i FLP u klienta z branży meblarskiej
Charakterystyka projektu
W opisywanym projekcie klient z branży meblarskiej zmagał się z problemami nieefektywnego przepływu materiałów oraz nieoptymalnym rozmieszczeniem stanowisk pracy. W wyniku analizy procesów produkcyjnych stwierdzono, że:
- Częste przestoje i nadmierne przemieszczanie się pracowników skutkują długimi czasami realizacji zamówień.
- Rozmieszczenie maszyn i stanowisk pracy nie spełniało norm ergonomii, co wpływało negatywnie na komfort oraz bezpieczeństwo pracy.
- Brak spójności między przepływem materiałowym a fizycznym układem produkcji generował zbędne koszty operacyjne.
Etap 1 – Analiza przepływu materiału z wykorzystaniem VSM
Na początku projektu przeprowadziliśmy warsztaty z udziałem trenerów Leantrix, inżynierów procesu oraz specjalistów Lean. Celem warsztatów było:
- Szczegółowe zmapowanie obecnego stanu produkcji.
- Identyfikacja etapów nie dodających wartości oraz miejsc, gdzie występowało marnotrawstwo.
- Określenie głównych problemów, takich jak nieoptymalne rozmieszczenie zapasów i zbędne przemieszczanie się pracowników.
Dzięki wizualizacji przepływu materiałowego udało się wyłonić obszary, w których zastosowanie narzędzi Lean mogło znacząco poprawić efektywność procesów. W firmie dostrzeżono, że lay-out nie jest dobrze zaprojektowany i występuje dużo marnotrawstwa szczególnie związanego z nadmiernym przemieszczaniem, zbędnym przetwarzaniem.
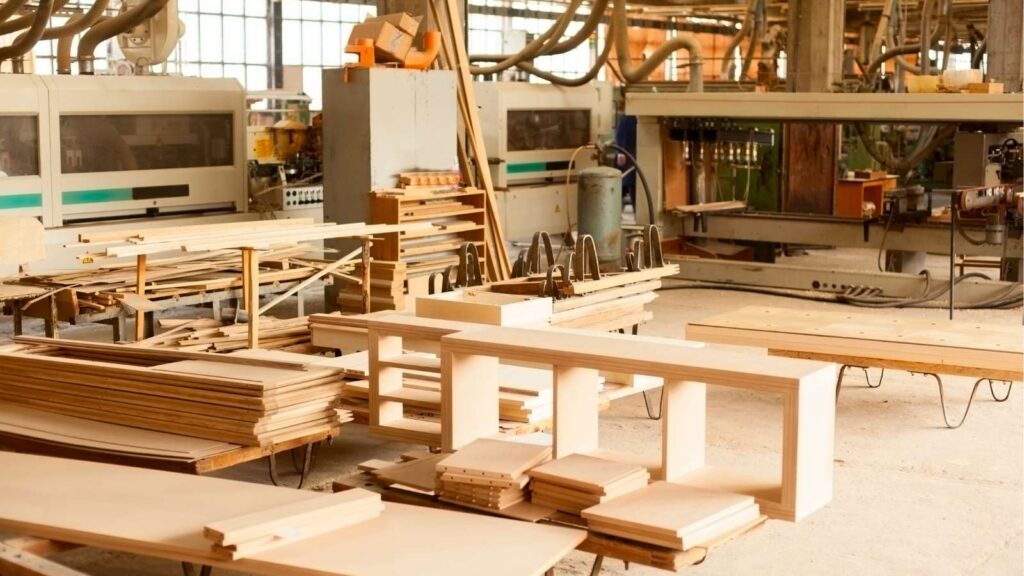
Stan Obecny – przed wdrożeniem VSM i FLP
Etap 2 – Projektowanie nowego layoutu z wykorzystaniem FLP
Na podstawie wyników analizy VSM przystąpiliśmy do projektowania nowego layoutu produkcyjnego, wykorzystując metodykę FLP. W tym etapie:
- Dokonaliśmy szczegółowej analizy przestrzennej zakładu, mierząc odległości między stanowiskami oraz określając optymalny przepływ materiałowy.
- Zastosowaliśmy algorytmy optymalizacyjne do symulacji różnych wariantów rozmieszczenia maszyn i stanowisk pracy.
- Wyłoniono rozwiązanie minimalizujące łączny koszt przepływu materiałowego przy jednoczesnej poprawie ergonomii i komfortu pracy.
Opracowano nowy lay-out dla obszarów kluczowych i wdrożono rozwiązania optymalizujące w zakresie redukcji marnotrawstwa.
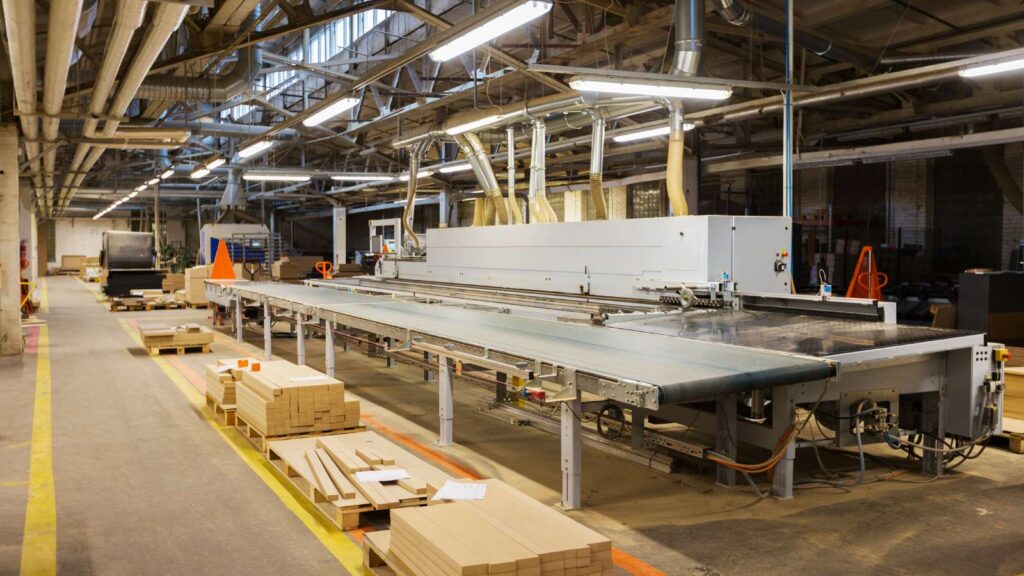
Stan docelowy – VSM i FLP
Etap 3 – Wdrożenie i rezultaty
Wdrożenie nowego layoutu odbyło się etapowo, z uwzględnieniem szkoleń dla pracowników oraz bieżącego monitoringu efektywności. Rezultaty wdrożenia obejmowały:
- Redukcję kosztów transportu: Usprawnienie przepływu materiałowego zmniejszyło dystanse pokonywane przez pracowników, co przełożyło się na obniżenie kosztów operacyjnych.
- Skrócenie cyklu produkcyjnego: Eliminacja zbędnych przemieszczeń i optymalizacja układu stanowisk przyczyniły się do szybszej realizacji zamówień.
- Poprawę ergonomii i bezpieczeństwa: Nowy layout został zaprojektowany z myślą o ergonomii, co wpłynęło na zmniejszenie ryzyka kontuzji oraz zwiększenie komfortu pracy.
- Zwiększenie efektywności maszyn: Lepsza synchronizacja przepływu materiałowego oraz optymalizacja przestrzenna zakładu pozwoliły na bardziej efektywne wykorzystanie zasobów, co skutkowało wyższą wydajnością systemu.
Poniżej przedstawiamy wyniki wdrożenia rozwiązania:
Obszar | Przed | Po | Poprawa o (%) |
---|---|---|---|
Dystans pokonywany w cyklu pracy przez operatora | 97 m | 47 m | ok. 52% |
Czas cyklu pracy operatora | 17 minut | 12 minut | ok. 29% |
Liczba zagrożeń (wizualizowanych dla pracowników) | 10 zagrożeń | 2 zagrożenia | 80% |
Wskaźnik OEE maszyny | 62% | 67% | ok. 8% |
Celem zakładanym przez organizację jest osiągnięcie wskaźnika OEE na poziomie 70%. W związku z tym planowane są kolejne aktywności, w tym analiza awaryjności maszyn, aby poprawić aspekt związany z dostępnością, co było jednym z głównych obszarów analizy w tym projekcie. Dzięki zastosowaniu narzędzi VSM i FLP w ramach Lean Management firma z branży meblarskiej osiągnęła znaczące usprawnienia operacyjne, co potwierdziły zarówno wewnętrzne audyty, jak i opinie pracowników.
Podsumowanie
Wdrożenie metodologii opartej na integracji Value Stream Mapping oraz Facility Layout Problem stanowi doskonały przykład synergii narzędzi Lean Management. W opisywanym case study:
- Dokładna analiza przepływu materiałowego umożliwiła identyfikację obszarów generujących marnotrawstwo.
- Projektowanie nowego layoutu przy użyciu metod FLP pozwoliło stworzyć optymalny układ zakładu produkcyjnego, redukując koszty transportu oraz poprawiając ergonomię stanowisk pracy.
- Zaangażowanie zespołu interdyscyplinarnego – trenerów Leantrix, inżynierów procesu oraz specjalistów Lean – umożliwiło skuteczną implementację zmian oraz osiągnięcie wymiernych rezultatów.
Integracja metod analitycznych (VSM) z optymalizacyjnym modelem FLP nie tylko przyczyniła się do redukcji kosztów operacyjnych, ale również wpłynęła na poprawę warunków pracy, co jest kluczowe w dążeniu do ciągłego doskonalenia i budowania przewagi konkurencyjnej. W dynamicznych warunkach rynkowych przedsiębiorstwa, które decydują się na wdrożenie Lean Management, mogą liczyć na trwałe usprawnienia procesów produkcyjnych, lepsze wykorzystanie zasobów oraz zwiększenie satysfakcji klientów.
Bibliografia
- Grobelny J., Michalski R. (2024). Linguistic pattern-based facility layout optimization in designing sustainable manufacturing systems. IEEE Transactions on Fuzzy Systems, 1-12. https://doi.org/10.1109/TFUZZ.
2024.3426946 - Grobelny J., Michalski R. (2022). Linguistic patterns as a framework for an expert knowledge representation in agent movement simulation. Knowledge-Based Systems. 243, 108497, 1-21. https://doi.org/10.1016/j.
knosys.2022.108497 - Grobelny J., Michalski R. (2017). A novel version of simulated annealing based on linguistic patterns for solving facility layout problems. Knowledge-Based Systems, 124, 55-69. https://doi.org/10.1016/j.
knosys.2017.03.001 - Sook, J. & Rother, M. Learning to See: Value Stream Mapping to Add Value and Eliminate MUDA.
- Liker, J. K. (2004). The Toyota Way: 14 Management Principles from the World’s Greatest Manufacturer.
Podsumowanie Artykułu
W artykule przedstawiono kompleksowe podejście do wdrożenia Lean Management w firmie produkcyjnej z branży meblarskiej, w którym kluczową rolę odegrały narzędzia Value Stream Mapping oraz metodyka FLP. Analiza przepływu materiałowego umożliwiła identyfikację źródeł marnotrawstwa, natomiast projektowanie layoutu oparte na FLP przyczyniło się do poprawy ergonomii i efektywności produkcji. Integracja wiedzy eksperckiej z zastosowaniem algorytmów optymalizacyjnych oraz narzędzi wizualnych, takich jak scatter ploty, pozwoliła na wdrożenie rozwiązań, które znacząco zmniejszyły koszty operacyjne i poprawiły warunki pracy. Takie podejście, poparte doświadczeniem trenerów Leantrix oraz specjalistów ds. Lean, stanowi przykład skutecznej implementacji metod naukowych w praktyce biznesowej.
Projekt ten pokazuje, że połączenie narzędzi analitycznych (VSM) z optymalizacyjnym modelem FLP daje wymierne korzyści – od redukcji kosztów, przez skrócenie cyklu produkcyjnego, aż po poprawę ergonomii stanowisk pracy. W obliczu rosnącej konkurencji i dynamicznych zmian na rynku, przedsiębiorstwa, które decydują się na wdrożenie rozwiązań Lean, mogą liczyć na trwałe usprawnienia operacyjne oraz wzrost satysfakcji klientów.
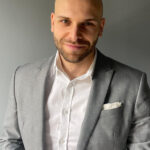
Praktyk programu Training Within Industry i Lean Management.
Wykłada na Wyższej Szkole Bankowej we Wrocławiu. Jest autorem i współautorem kilku pozycji literaturowych poświęconych programowi TWI.
Obecnie pełni funkcję partnera zarządzającego w firmie LeanTrix, jak i master Trenera Na Europę. Dodatkowo zaangażowany jest w projekty takie eTWI System i Lean Community
Prowadził projekty między innymi dla: Lotte Wedel, Danone, Kompania Piwowarska, eobuwie.pl, Arvato, Whirlpool, B/S/H, Geberit, RECARO, Tenneco, Sumitomo Electric, Stadler, Vesuvius Poland