Poprawa wartości wskaźnika całkowitej efektywności sprzętu OEE (ang. Overall Equipment Efficiency) na wybranych maszynach jest często jednym z najważniejszych celów wielu przedsiębiorstw produkcyjnych. Z naszych badań przeprowadzonych w przeszło 100 firmach produkcyjnych mających swoje fabryki w Polsce wynika, że aż 70% z nich mierzy efektywność swoich maszyn właśnie w oparciu o wskaźnik OEE (Rysunek 1). Wskaźnik ten został opracowany przez Seiichi Nakajimę w latach 50. XX wieku. Zorientowany jest on na wyszczególnienie strat w dostępności, wykorzystaniu oraz jakości produkowanych wyrobów na maszynie.
Rys. 1. Najczęściej wykorzystywane wskaźniki do mierzenia efektywności wykorzystania maszyn w badanych przedsiębiorstwach produkcyjnych
Źródło: Badania zespołu LeanTrix w krajowym przemyśle
Wskaźnik OEE w uproszczonej wersji można policzyć jako procentowy udział czasu produkcji dobrych sztuk w dostępnym czasie pracy maszyny:
Podstawowym celem obliczania wskaźnika OEE jest określenie, gdzie w procesie eksploatacji maszyn występuje największa ilość strat. Jest to podstawa pod zdefiniowanie środków zaradczych, które powinny być podjęte w celu poprawy efektywności wykorzystania maszyn. Dlatego przyjmuje się, że im szczegółowiej rozpisze się wzór na obliczanie wskaźnika OEE, tym więcej informacji o stratach na maszynie można uzyskać. Z tego też względu zaleca się oddzielnie obliczanie dostępności maszyny, jej wykorzystania oraz jakości wytwarzanych przez nią produktów.
Przeprowadzone badania w krajowym przemyśle wykazują, że średnia wartość wskaźnika OEE w firmach, które mierzą ten wskaźnik, wynosi 66%. Na Rysunku 2 przedstawiono ile procent ankietowanych firm znalazło się w zdefiniowanych zakresach wartości wskaźnika OEE.
Rys. 2. Zestawienie obrazujące ile procentowo firm osiąga wartość wskaźnika OEE w zdefiniowanych czterech zakresach
Źródło: Badania zespołu LeanTrix w krajowym przemyśle
Światowy poziom wskaźnika OEE (ang. Wordl Class OEE) został ustalony na poziomie 85%. Oznacza to, że zaledwie 13% spośród ankietowanych firm osiąga zakładaną wartość wskaźnika OEE. Należy zaznaczyć, że badania przeprowadzone były wśród firm, które deklarują aktywność we wdrażaniu nowoczesnych koncepcji zarządzania i organizacji pracy takich jak: Lean Managemtn, Six Sigma, czy Training WIthin Industry. Z dużym prawdopodobieństwem oznacza to, że średnia wartość wskaźnika OEE we wszystkich przedsiębiorstwach produkcyjnych mających swoje fabryki na terenie Polski, jest niższa niż średnia wartość wskaźnika OEE w ankietowanych firmach.
Na ustalenie wartości światowego poziomu wskaźnika OEE (wspomniane 85%) wpływ mają oddzielne poziomy docelowe ustalone dla jego trzech czynników: dostępności, wykorzystania i jakości (Tabela 1).
Tab. 1. Poziomy docelowe dla każdego czynnika składającego się na wskaźnik OEE
Nazwy czynników składających się na wskaźnik OEE | Poziom docelowy |
---|---|
Dostępność maszyny | 90% |
Wykorzystanie maszyny | 95% |
Jakość wyprodukowanych wyrobów na maszynie | 99% |
Iloczyn wartości poziomów docelowych poszczególnych czynników wskaźnika OEE przyjmuje wartość 85%, z tego powodu wartość ta ustalona została jako światowa wartość wskaźnika OEE.
Poprawa dostępności – największy potencjał do poprawy wskaźnika OEE
Z analizy światowego wskaźnika OEE wynika, że największy potencjał na poprawę efektywności maszyn możliwy jest do osiągnięcia w ich dostępności. Na jej obniżenie wpływ mają dwie kluczowe straty:
- Awarie.
- Przezbrojenia maszyn.
W przedsiębiorstwach produkcyjnych redukuje się te straty poprzez zapobieganie występowaniu awariom (Total Productive Maintenance – TPM z działaniami autonomicznej konserwacji) oraz skracanie czasów przezbrojeń (System Single Minute Exchange of Die – SMED). Jest jednak jeszcze jeden obszar, w którym istnieje olbrzymi potencjał poprawy dostępności maszyn. To proces, którym jest usuwanie awarii. Jednym z celów TPM jest zero awarii. Ten cel choć ambitny, w praktyce jest nieosiągalny. Awarie się zdarzają. Dlatego istotne jest, aby mieć przygotowaną procedurę reakcji w przypadku ich wystąpienia. Usuwanie awarii jako proces niestety w większości firm produkcyjnych nie jest analizowany i usprawniany. Dzieje się tak dlatego, że awarie często są przypisywane do działu Utrzymania Ruchu, a nie do produkcji. Zakłada się, że awarie się zdarzają, a mechanicy robią wszystko, aby je efektywnie usunąć. Zapomina się przy tym, że usuwanie awarii to nie tylko praca przy maszynie, ale również szereg działań organizacyjnych. Należy pamiętać, że awaria obniża efektywność maszyny i nie ma tutaj znaczenia, gdzie się ją formalnie przypisze. Usuwanie awarii nie jest analizowane w firmach również dlatego, że awarie utożsamia się z pewną spontanicznością – nigdy nie wiemy, kiedy się przytrafią. Inaczej jest z przezbrojeniami, czy działaniami podczas autonomicznej konserwacji. Je się planuje. To jednak nie jest do końca prawda. W TPM obliczany jest wskaźnik MTBF (ang. Mid Time Between Failures), który pozwala oszacować częstotliwość występowania awarii. Jednym słowem odpowiedzialny jest on za „planowanie” potencjalnych awarii. Inny wskaźnik, MTTR (ang. Mid Time To Repair) prezentuje średni czas potrzebny na usuwanie awarii. Analiza procesu zwanego usuwanie awarii wpływa zatem nie tylko na poprawę dostępności, ale również na skrócenie czasu MTTR.
Jak doskonalić proces, w którym kluczowe jest usuwanie awarii?
Doskonalenie procesu usuwania awarii składa się z 5 etapów. Opracowaliśmy je na podstawie kilkudziesięciu projektów wdrożeniowych w tym zakresie w firmach produkcyjnych. Przejście wspomnianych 5 etapów zapewni, że skutecznie zidentyfikujesz marnotrawstwo w procesie, wygenerujesz szereg działań usprawniających ten proces i co najważniejsze – poprawisz wartość wskaźnika OEE. Etapem pierwszym jest nakręcenie filmu z usuwania awarii. Drugi etap to opisanie sposobu pracy osób zaangażowanych w usuwanie awarii. Trzecim etapem jest wizualizacja procesu na mapie i oddzielenie zadań dodających wartość od tych, które jej nie dodają. Czwarty etap to generowanie pomysłów doskonalących zgodnie z podejściem 5W1H. Ostatni, piąty, etap to wdrożenie rozwiązań poprzez zbudowanie instrukcji i szkolenie pracowników. W Tabeli 2 przedstawiono kompletną procedurę wykorzystując do tego Arkusz Podziału Pracy należący do programu Training Within Industry – TWI.
Tab. 2. Procedura doskonalenia procesu usuwania awarii w firmie zapisana na Arkuszu Podziału Pracy
Etap | Wskazówka | Przyczyna |
---|---|---|
Co należy zrobić? | Jak wykonać etap? | Dlaczego należy wykonać wskazówkę? |
1.Nagraj film z procesu „usuwanie awarii” | 1.Sprowokuj awarię | 1.Wtedy rzeczywiście zobaczysz jak wygląda proces „usuwanie awarii”. Prawdopodobnie przyjęty standard różnić się będzie od rzeczywiście funkcjonującego. |
2.Nie informuj pracowników o zamiarze nagrywania filmu | 2.Będziesz miał pewność, że analiza dotyczyć będzie rzeczywistego procesu, a nie dostosowanego do potrzeb filmu. | |
3.Podążaj z kamerą za pracą ludzi | 3.W procesie „usuwanie awarii” bierze udział kilka osób (operator, mechanik itd.). Musisz starać się uchwycić co robi dany człowiek w danym momencie (jak się komunikuje, gdzie idzie, czego szuka itp.). | |
2.Zapisz sposób postępowania na kartce | 1.Pracę opisuj poprzez zabiegi (najmniejsza część pracy, która może być transferowalna) | 1.Podział na zabiegi umożliwia doskonalenie pracy. Jako zabiegi traktuj przemieszczanie pracownika (np. przejście z maszyny do magazynu), pracę manualną (np. wymiana narzędzia) oraz pracę maszynową (np. uruchomienie maszyny). |
2.Numeruj poszczególne zabiegi | 2.Będzie to potrzebne, aby zaprezentować je na mapie stanu obecnego. | |
3.Zabiegi wypisuj w oparciu o przygotowany film | 3.Łatwiej będzie je uchwycić i poprawnie zapisać . | |
3.Opracuj mapę stanu obecnego | 1.Zaznacz całkowity czas awarii na osi czasu | 1.Względem tej długości będziesz prezentować numery poszczególnych zabiegów. |
2.Oznacz zabiegi w zależności kto je wykonywał i w którym momencie procesu | 2.Dobrze zobrazuje to takie sytuacje jak moment pierwszej reakcji mechanika itp. | |
3. Do oznaczenia zabiegów użyj kolorów:
|
3.W ten sposób wizualnie oddzielisz działania, które są marnotrawstwem od tych, które dodają wartość w procesie albo jej nie dodają, a są potrzebne. | |
4.Usprawnij proces | 1.Eliminuj marnotrawstwo (czerwony kolor) | 1.Zgodnie z cytatem Peter Druckera: „Najbardziej nieefektywne jest efektywne robienie rzeczy, których w ogóle nie powinno się robić”. Jeżeli dostrzegasz marnotrawstwo to zaproponuj rozwiązanie, aby je usunąć. Nigdy nie usprawniaj marnotrawstwa. |
2.Zastanów się jak usprawnić pozostałe działania (żółte i zielone) pytając kolejno:
|
2.Jest to część podejścia zwanego 5W1H do doskonalenia pracy wg programu TWI Metody Pracy. Przed szukaniem usprawnień w sposobie wykonywania pracy (pytanie: jak to lepiej zrobić?) należy najpierw zastanowić się, czy obecne miejsce, czas i osoba są najlepsze do jej wykonania. Ostatnim pytaniem powinno być jak lepiej wykonać dany zabieg. | |
5.Wdróż rozwiązania | 1.Opisz usprawniony proces usuwania awarii na instrukcji pracy standaryzowanej | 1.Najbardziej skuteczny sposób opisywania pracy w danym procesie. Operacje na Instrukcji Pracy Standaryzowanej dzieli się na: główne kroki, wskazówki i przyczyny (tak jak w tej tabeli). |
2.Przeszkól pracowników wykorzystując metodę TWI Instruowanie Pracowników | 2.Jest to najbardziej skuteczna metoda przekazywania wiedzy wg krzywej uczenia. Aby ją wykorzystać należy mieć opracowaną Instrukcję Pracy Standaryzowanej. |
Kluczowym krokiem w zaprezentowanej procedurze jest mapowanie procesu (etap nr 3). Przykładową uproszczoną mapę zaprezentowano na Rysunku 3. Analizowany proces usuwania awarii składał się z 40 zabiegów i trwał 67 minut.
Rys. 3. Uproszczona mapa procesu usuwania awarii w przykładowym przedsiębiorstwie
Już pobieżna analiza mapy stanu obecnego wskazuje, że jedynie około 35% wszystkich zabiegów dodaje wartość do procesu usuwania awarii (zielone zadania). Reszta to marnotrawstwo, które można usunąć natychmiastowo (czerwone zadania) albo zadania niedodające wartości, ale potrzebne z punktu widzenia procesu (żółte zadania). Je należy usprawniać. Czerwone i żółte zadania stanowiły sumarycznie około 65% wszystkich zabiegów, co daje blisko 44 minuty całego procesu usuwania awarii! Podczas wielu podobnych analiz jakie prowadziliśmy w przemyśle, średnio około 40% zadań to było marnotrawstwo (czerwone zadania), które można było usunąć natychmiastowo! Marnotrawstwem w procesie usuwania awarii mogą być: przedłużającą się próba usunięcia problemu przez operatora, szukanie brygadzisty przez operatora, chodzenie do narzędziowni po podstawowe narzędzia pracy, czy wypełnianie zbędnej dokumentacji.
Czy warto analizować i standaryzować proces „usuwanie awarii”?
W wielu firmach produkcyjnych, aby poprawić dostępność maszyn, dąży się wyłącznie do maksymalnego skracania czasu przezbrojeń i zapobiegania występowaniu awarii. Dla przykładu, inwestuje się duże środki finansowe, aby zredukować czas przezbrojenia maszyny o kilka minut zapominając, jaki potencjał tkwi w skracaniu czasu usuwania awarii. Zbyt długi czas przezbrojenia maszyny, podobnie jak zbyt długi czas usuwania awarii, identycznie obniżają dostępność maszyny. W obu sytuacjach maszyna po prostu nie może pracować. Warto przede wszystkim poprawiać organizację pracy przy przezbrojeniu maszyny oraz zapobiegać występowaniu awariom. Ale czasami, zanim zainwestuje się w drogie rozwiązania techniczne, które ucinają kolejne minuty przy przezbrojeniu maszyny, lepiej jest przeanalizować proces usuwania awarii, aby skrócić jego czas wykorzystując do tego dostępne środki i materiały. Tym bardziej, że jak pokazuje praktyka, blisko 40% zadań wykonywanych podczas usuwania awarii to marnotrawstwo!
Jeżeli nigdy nie analizowałeś procesu „usuwanie awarii” w swojej firmie to zrób to czym prędzej! Dzięki temu, przy niewielkim nakładzie pracy, jesteś w stanie zredukować czas awaryjności maszyn nawet o przeszło 40%! Tak, bo na czas awaryjności maszyny wpływ mają zarówno czas usuwania samej awarii, jak i szereg zadań organizacyjnych. Je można doskonalić często bez żadnych nakładów finansowych.
Warto wspomnieć, że jednym z celów TPM jest zero awarii. Z tego punktu widzenia doskonalenie procesu usuwania awarii jest niczym doskonalenie marnotrawstwa. Jednak faktem jest to, że awarie się zdarzają. Często przyczyną ich powstania są np. czynniki zewnętrzne, na które pracownicy w firmie nie mają żadnego wpływu. Z resztą w TPM istnieją wskaźniki MTBF i MTTR, które poświęcone są analizie awarii. Zatem sam system TPM zakłada ich występowanie. Warto być dobrze przygotowanym w momencie pojawienia się awarii, bo to wpływa na poprawę dostępności maszyny, a tym samym wskaźnika OEE!
Literatura
Seiichi Nakajima, Introduction to TPM: total productive maintenance, 1988, Productivity Press
Misiurek B., Standardized Work with TWI: Eliminating Human Errors in Production and Service Processes, 2016, Productivity Press
Portal Internetowy LeanTrix, stan na 01.03.2016, link: https://leantrix.com/pl/jak-przekazac-wiedze-innowacyjne-zastosowanie-metody-twi-instruowanie-pracownikow/
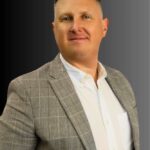
Jestem popularyzatorem Lean Management oraz programu Training Within Industry. Jestem praktykiem. Współtworzę wiele startupów. Od 2015 roku jestem CEO w Leantrix - czołowej firmie z zakresu konsultingu Lean w Polsce, która począwszy od 2024 roku organizuje jedną z największych konferencji poświęconych szczupłemu zarządzaniu w Polsce - Lean TWI Summit. Od 2019 roku jestem CEO w firmie Do Lean IT OU zarejestrowanej w Estonii, która tworzy software etwi.io używany przez kilkadziesiąt firm produkcyjnych i usługowych w Europie i USA.