Training Within Industry (TWI) is a program that complements Lean Management. Lean is a path our company has been following for many years. Lean helps us streamline processes by eliminating waste, build high quality into our products and processes, and meet customer expectations. The Lean philosophy provides a range of methods and tools that help achieve this goal. However, what we have learned from our practical actions is that without the engagement of everyone in the organization, implementing Lean will end in failure. We realized that our products are the result not only of modern machines or the best methods, but above all, the passion of the people who work in our organization every day. It is the same with implementing Lean—if we want to do it with the highest quality, we need not only Lean methods and tools but also the greatest involvement of our employees. The richest man in human history, John Davison Rockefeller, once said: “The ability to deal with people is as purchasable a commodity as sugar or coffee. And I will pay more for that ability than for any other under the sun.” This ability is related to engaging and motivating employees, which is strengthened by building their awareness.
An excellent complement to the Lean implementation process in our organization became the Training Within Industry (TWI) program, which focuses on developing managerial skills in experienced employees. These skills include transferring knowledge (TWI Job Instruction), improving work methods through Kaizen (TWI Job Methods), and building relationships and solving problems (TWI Job Relations). The Training Within Industry program is the missing link in successfully implementing Lean, as it develops managerial skills in experienced employees, leaders, and supervisors—those who determine the effectiveness of Lean principles’ implementation and sustainability. The Training Within Industry program addressed a key issue in our organization: extensive knowledge about processes and methods exists in the “heads” of our employees and is not effectively passed on in the learning process.
The TWI program was foundational in developing the management culture at Toyota, which was based on continuous improvement and the ongoing learning process. The foundation of the Toyota Production System (TPS) was work standardization, which the TWI program creates. Taichi Ohno, the creator of TPS, once said, “My first action when I became a manager in the machine shop was to implement work standardization.” The TWI program has begun another transformation in our company—from a Lean Enterprise to building a learning organization.
Our company – Tarczyński S.A.
The TARCZYŃSKI Group focuses on processing pork and poultry, as well as the sale and distribution of meat and sausage products under the TARCZYŃSKI brand. It operates three production plants. The main plant, located in Ujeździec Mały, is one of the most modern sausage production facilities in Europe. The Group also includes production plants in Sława and Bielsko-Biała.
Implementation of Training Within Industry in Our Organization – The First Wave
The goal of the “first wave” was to acquire knowledge and skills in the Training Within Industry program among selected employees from three production plants. The first wave was carried out with the support of a consultant from LeanTrix sp. z o.o., who had 9 years of experience in implementing the Training Within Industry program. The entire process was based on the PDCA cycle (Plan – Do – Check – Act). This approach guaranteed the effectiveness and efficiency of the knowledge and skills acquisition process.
The first wave of the Training Within Industry program implementation concluded with our organization having trained:
- 8 certified TWI Instructors, who acquired practical skills in creating work standards and conducting job instruction,
- 6 certified TWI Trainers, who are capable of training other employees within our organization without external support.
The candidates for TWI Trainers were selected from three production plants. After completing their certification, they received training materials that enable them to independently conduct practical TWI workshops. This will allow for the gradual rollout of the TWI program across all areas of our three production plants.
Sustaining the Implementation of the Training Within Industry Program
The Training Within Industry program, especially the TWI Job Instruction method, primarily focuses on creating clear work standards (Standardized Work Instructions) and then using them for job instruction. Instructions in the TWI program are not solely aimed at describing the work (what you do). The main emphasis is placed on guidelines (how you should do it) and, most importantly, on the reasons that help employees understand why a particular guideline should be followed in a specific way (why you should do it this way). The key aspect of the Training Within Industry program is developing the ability of experienced employees to methodically transfer the knowledge documented in the standards.
A major challenge in our organization was the need to create TWI documentation and then keep it updated. Typically, MS Office programs are used for this purpose, but they often cause various issues, such as difficulties in adding photos, formatting cells, or managing current versions. A helpful tool that we started using is the LeanTrix system, which has a dedicated module for creating Standardized Work Instructions (Figure 3). Additionally, the system contains dozens of instructional videos, which are helpful for our TWI Instructors and Trainers in preparing for job instruction or conducting practical workshops.
Fig 3. TWI Work Instruction (Polish)
Another challenge we faced during the sustainment phase of the TWI program implementation was allocating time for TWI Instructors to carry out practical activities on the production floor (creating standards and instructing employees) and for TWI Trainers to conduct practical TWI workshops. However, we treated the entire project as an investment that initially requires resource commitment but will undoubtedly yield measurable results in the future in terms of reducing production-related issues. Our organization has become aware that we understand that quality defects, breakdowns, or accidents caused directly by human error are merely symptoms of a poor management system. The root causes of human errors should be sought in:
- A lack of or poorly conducted operator training processes.
- Non-adherence to work standards by operators due to poorly developed work standards.
- A lack of systems for monitoring and auditing operators after training.
The TWI program addresses these root causes by engaging production leaders in effective job instruction and improving work methods. The time dedicated to practical TWI activities will lead to the elimination of human errors, thereby improving all key performance indicators (KPIs) in our company.
Summary and Benefits of Implementing the Training Within Industry Program
The implementation and continuous work based on the Training Within Industry program bring many benefits to the Tarczyński S.A. Group. The main metric used at the start of the implementation is the time it takes for an employee to independently perform operations without additional assistance and supervision. Thanks to the efficient efforts of TWI Instructors and Trainers, the learning time has been reduced by 25-30%. It is also worth mentioning the reduction in quality errors, which has resulted from clear and structured onboarding for individual line workers and machine operators.
The Training Within Industry program has also significantly contributed to a shift in organizational culture concerning learning and employee training. Middle management has realized the importance of conducting job instruction using a method that has been proven across many industries for several decades. Additionally, employees trained using the TWI Job Instruction method (TWI JI) are far more willing to share their knowledge with other employees. Moreover, the entire Training Within Industry program has contributed to building employee and operator awareness, which directly impacts performance indicators and machine downtime caused by improper operation or lack of knowledge.
Authors
Dawid Tarczyński, Director of Continuous Improvement at Tarczyński S.A.
A graduate of the University of Economics in Wrocław, Faculty of Management and IT. He has been with the Tarczyński S.A. Group for over 5 years. He has more than 3 years of experience in implementing process optimization solutions for the manufacturing industry. Additionally, he is responsible for the development of management systems and fostering a Lean Manufacturing culture within the Tarczyński S.A. Group.
Krzysztof Kaczmarek, Continuous Improvement Manager at Tarczyński S.A.
A graduate of the University of Economics in Wrocław, Faculty of Management and Production Engineering—certified TWI Trainer. He has more than 4 years of experience in implementing process optimization solutions for the manufacturing and pharmaceutical industries, as well as in designing and implementing Continuous Improvement systems and management tools based on Lean Manufacturing (5S, SMED, TQM). Additionally, he is responsible for the development of MES systems and the implementation of production indicators at Tarczyński S.A.
Bartosz Misiurek, Ph.D. Eng. – Consultant at LeanTrix sp. z o.o.
CEO of LeanTrix sp. z o.o., which provides IT systems supporting Lean Management implementation. Currently, he supports Cooper Standard (Automotive) as TWI Lead Coach Europe, responsible for implementing the TWI program in several dozen factories across Europe. From 2007 to 2015, he was responsible at Lean Enterprise Institute Poland for transferring the TWI program from the USA and its subsequent development in Poland. He has worked as a Lean Management, TPM, and TWI consultant for over 150 manufacturing and service companies in Europe.
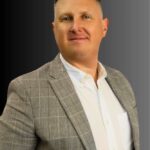
I am a promoter of Lean Management and the Training Within Industry program. I am a practitioner. I co-create many startups. Since 2015, I have been the CEO of Leantrix - a leading Lean consulting company in Poland, which, starting from 2024, organizes one of the largest conferences dedicated to lean management in Poland - the Lean TWI Summit. Since 2019, I have been the CEO of Do Lean IT OU, a company registered in Estonia that creates the software etwi.io, used by dozens of manufacturing and service companies in Europe and the USA.