About TWI
TWI
What is the Training Within Industry – TWI program and how was it set up?
The Training Within Industry (TWI) program is a program which supports the development of management skills of experienced operational employees and low and middle management superiors.
The origin of the program dates back to the early 40s of the last century, when after the Nazi invasion of France in June 1940, the US realized that a world war was inevitable. A report prepared on the request of the US Army showed that there were 8 million unemployed people in the United States in 1940. A big danger was that the involvement of US troops in the war meant that the majority of American men of working age, and working mainly in industry, would be recruited into the army. The activities of the program aimed to include people, who had never before worked in production, to work in industry. They were mainly women, men who were too young to be recruited into the army and administrative staff.
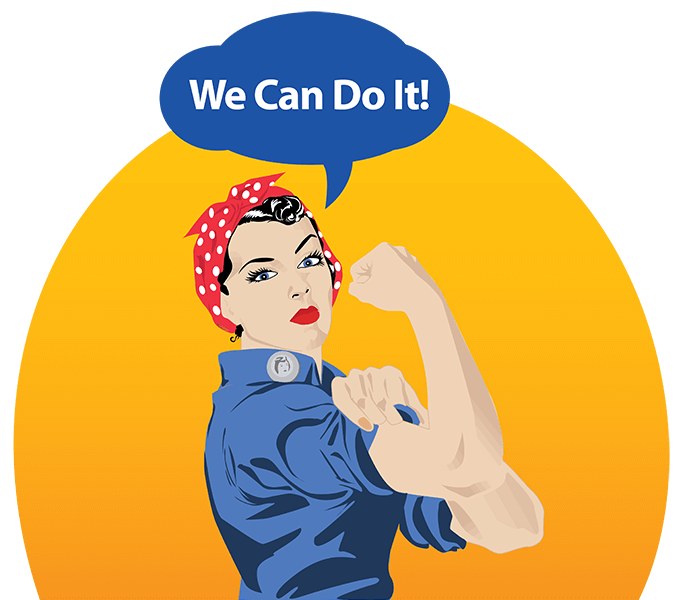
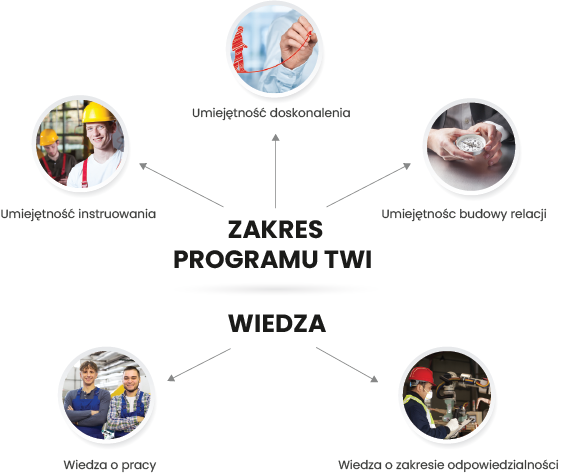
Why was the TWI program created?
The objective of the TWI program was the rapid development of new talented staff in order to achieve an increase in productivity, quality and occupational safety. This program includes the development of three managerial skills, which are necessary in the work of leaders and experienced employees:
- the ability to instruct employees and writing SOPs,
- the ability to improve working methods (kaizen),
- the ability to build good relations with employees (sometimes described as the ability of leadership.
The TWI program was designed for experienced employees, and not to new employees. The assumption of the program was that every experienced employee (leader, manager) possesses knowledge about the work and scope of responsibilities, which is gained through practice for years. In contrast, the three key management skills must be developed. This program provides ready-made tools which support the management of employees by their superiors.
What benefits did the TWI program bring?
The implementation of the TWI program in American industry brought tremendous benefits and contributed to the victory over Hitler’s armies. Out of the 600 manufacturing companies who participated in this program during World War II:
- 100% of companies shortened the time of training new employees by 25% or more,
- 86% of companies increased their efficiency by 25% or more,
- 88% of companies reduced the workload on a product by 25% or more,
- 55% of companies reduced deficiencies by more than 25%,
- 100% of companies reduced complaints by more than 25%.
Success of the Training Within Industry program resulted from the fact that each of its methods was built based on a cycle of Plan-Do-Check-Act (PDCA), which was developed by William Edwards Deming.
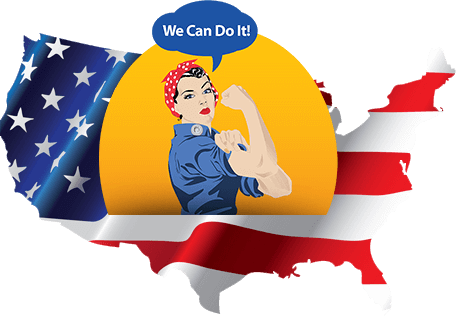
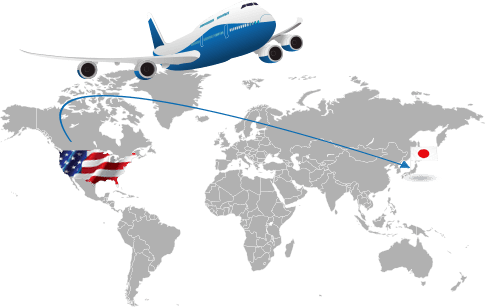
What was the fate of the TWI program after World War II?
After World War II the TWI program was submitted, inter alia, to Japan, where companies such as Toyota and Sanyo used it to build the foundations to develop their efficient production methods.
It was absorbed by Toyota and became an integral part of the Toyota Production System (TPS). It was also the basis of the creation of a management culture at Toyota, which was based on continuous improvement and a process of constant learning. Training Within Industry is the starting point in the implementation of Lean Management philosophy.
Why did the TWI program play such an important role in the Toyota Production System (TPS)?
In the TWI program the biggest emphasis was put on the development of its employees, especially foremen, masters and managers. Their professionally conducted on-the-job training and involvement in the process of continuous improvement (kaizen) was an expression of respect for their subordinates. It was soon noticed in Toyota that the development of employees and training of genuine leaders is essential for the success of the implementation of methods and tools of Lean Management. Without the awareness of employees, the implementation of Lean Management is a difficult and, in practice, an impossible challenge. Based on the fundamental principles of the TWI program, Toyota formulated the concept of employee development management, which is now called Lean HR. Its main objective is to eliminate the eighth type of waste: the lost creativity of employees. This type of waste is considered to be the worst because it indirectly affects the presence of the remaining 7 types of waste. Lean HR helps to manage the competences of employees with the use of tools such as, among other things, the Skill Matrix. The TWI program provides leaders with methods on how to extract the best features from people. Lean HR and the TWI program are both focused on the stimulation of employee creativity – eliminating the eighth type of waste.
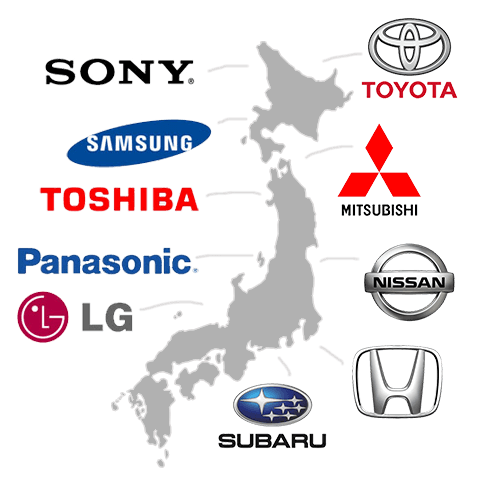
What is the current role of the TWI program?
Currently, the TWI program is identified with the philosophy of Lean Management. It should be treated as one fully complementary philosophy oriented towards the improvement of the efficiency of company processes.
Without the Training Within Industry program there would not be the Toyota Production System (TPS), and thus Lean Management. This program should be the foundation of every management system in any enterprise!
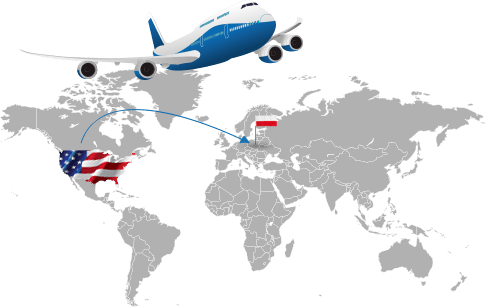
In what type of companies can the TWI program be implemented?
The TWI program is universal. It can be used in any company where there are people and processes. The program was originally created for the production industry.
However, its versatility means that it works well in other industries, such as:
- administration,
- services,
- the health service.
What connects the TWI program with standardization of work?
The TWI program was the basis of creating a management culture at Toyota, which was based on continuous improvement and the constant process of training employees.
This program became the foundation of Toyota, who took responsibility for the stabilizing and standardizing of processes such as:
- shortening of retooling time – SMED,
- activities within autonomous maintenance – TPM,
- maintenance of high-quality job posts – 5S,
- responding to problems.
The TWI program was the main tool in the process of standardization of work. Methods of this program are used in Toyota to this day in exactly the same form as when they were formulated during World War II.
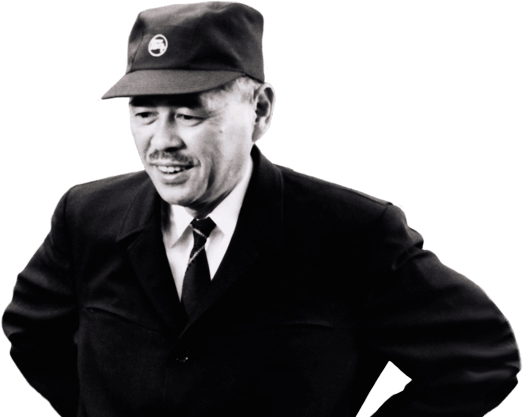
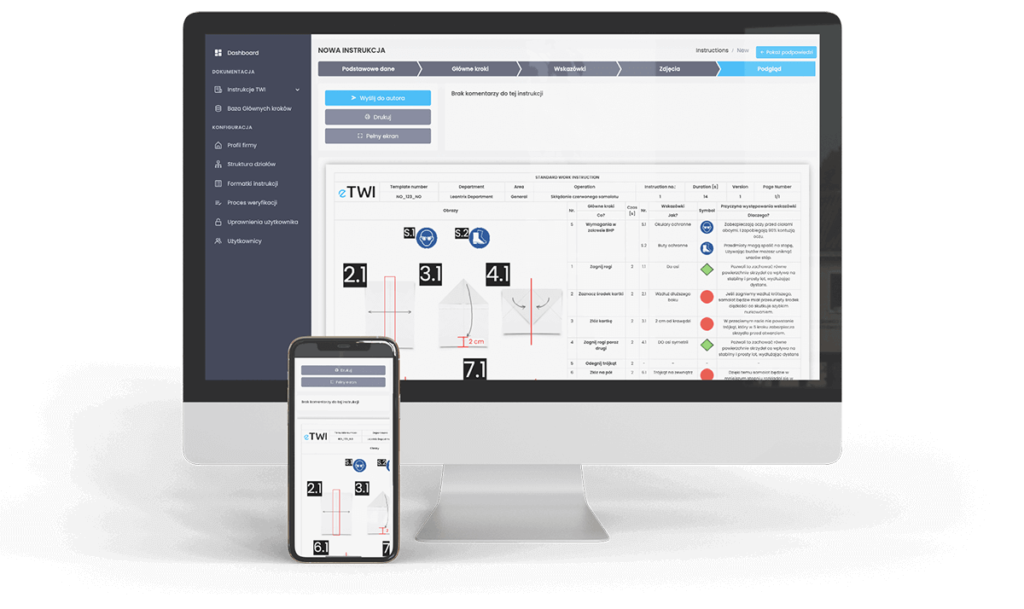
What is standardization of work?
Standardization of work is a process in which the current best ways of performing operations must be written down and improved. Operators should then be trained from them.
Standardization of work is not only a description of working methods on instructions. Instructions are of course important for standardization of work, however, they are only used to effectively lead on-the-job training or undergo the operation of the process of improvement.
Therefore, instructions are only an indirect measure to achieve the objective, which is the standardization of a process. Instructions themselves are not an aim.
At the current time, work instructions can be prepared in SOP Software.
How does the TWI program support standardization of work?
The TWI program provides the most effective tools for standardization of work:
- Documentation of the best practices of executing work on Standardized Work Instructions
- The involvement of employees in the improvement of working methods thanks to the Kaizen approach and 5W1H
- The most effective way of conducting on-the-job training with regards to the TWI method of Instructing Employees
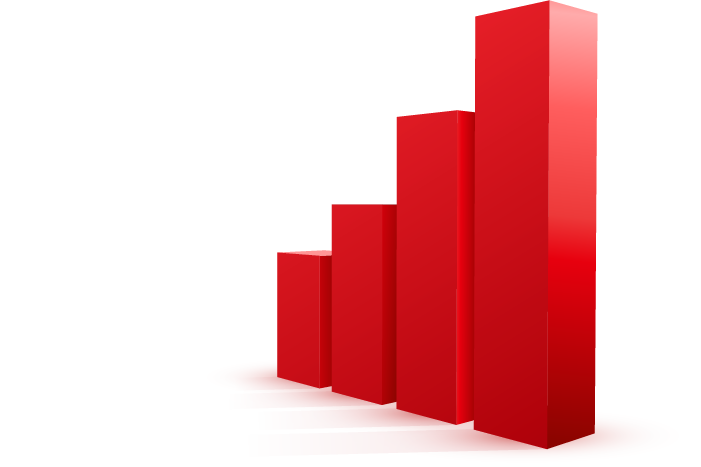
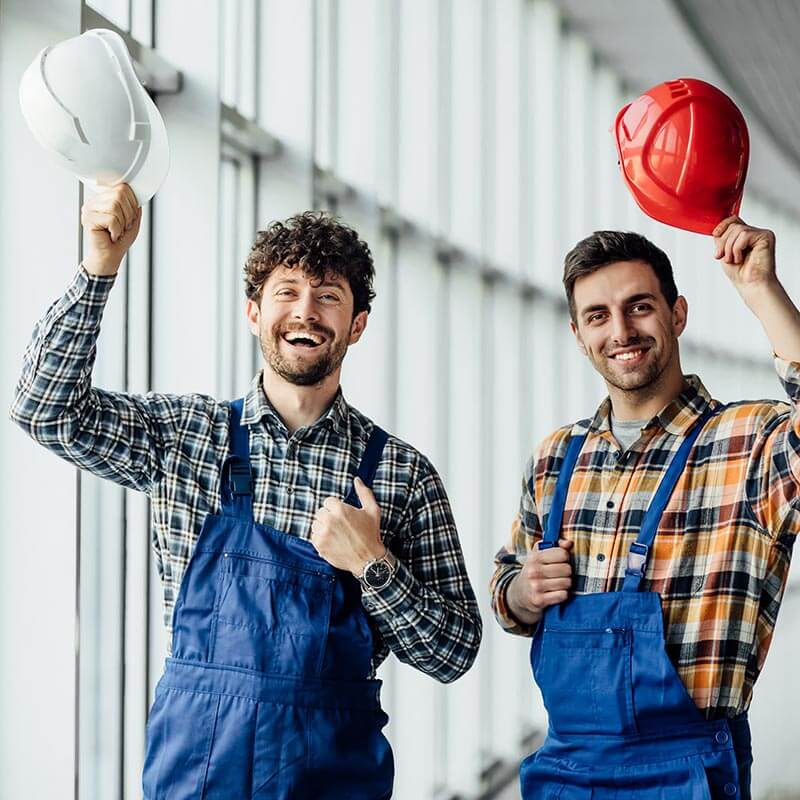
What benefits come from standardization of work?
Standardization of work effectively influences the reduction of human errors in processes as it is closely connected with the elimination of their root causes:
- The lack of or poor process of training operators.
- Failure to comply with a work standard by operators, due to the fact that the work standard was poorly developed.
- The lack of monitoring and auditing of an operator after training.
Human errors are indeed the direct cause of: accidents, quality deficiencies or reduced work efficiency. The TWI program eliminates the root causes of human errors which are associated with the way of managing an organization.
The role of a leader in standardization of work
In the TWI program a leader is a person who formally manages a group of people and he is also an experienced operator who e.g. takes responsibility for a trained employee during training.
Our experience shows that leaders in the best production companies are responsible for:
- Work in accordance with an established standard while working on a production line.
- Providing operators with the conditions which enable work according to the standard (appropriate tools, responding to problems, etc.).
- Training operators to perform work in accordance with the standard.
- Auditing of executed work in accordance with the standard.
- Analysing improvements in the method of performing work which are notified by operators and also reporting their own improvements.
- Documentation of work in cooperation with production support services.
- Caring for up to date documentation on a job post.
The TWI program supports leaders in these tasks.
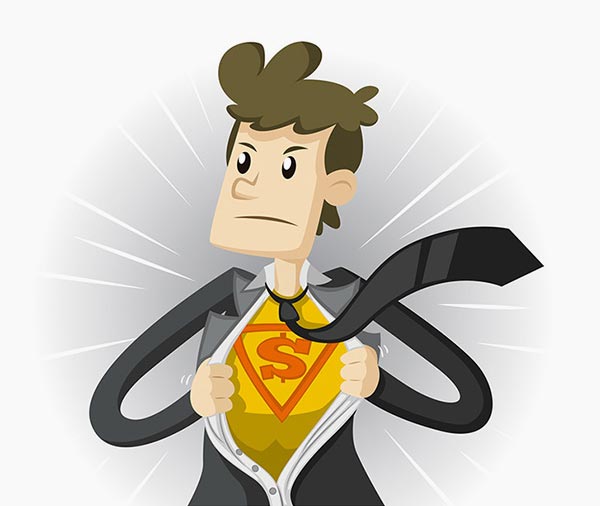