Lean AI. Let’s start with a fundamental question: Who in your organization is responsible for continuous improvement? The answer seems obvious – everyone. A similar response applies to workplace safety – theoretically, every employee should care about health and safety. However, in reality, there is always a dedicated safety specialist responsible for formal procedures, audits, and corrective actions. Responsibility shifts from “everyone” to a single role. The same happens with continuous improvement. Many companies have a Lean specialist, whose job is to optimize processes, organize KAIZEN workshops, monitor 5S standards, and report cost savings.
In theory, continuous improvement should be part of everyone’s job.
In practice, when improvement-related tasks arise, people often say:
- “That’s not my responsibility, we have a Lean specialist for that.”
- “You need to talk to the Lean department.”
- “Submit this issue to the Lean Manager – it’s their job.”
Eventually, Lean responsibility falls solely on one person or a small team of specialists, rather than being an integral part of leadership and frontline operations.
A typical production plant structure
Let’s look at a standard production facility’s organizational structure to understand how Lean roles function in practice.
At the top, we have Tomek Dydlajnowski, the plant manager, responsible for the entire facility.
Below him are three key managers:
- Monika Kadrowa – HR Director, responsible for talent development and workforce management.
- Marek Dowieźto – Production Manager, focusing on meeting production targets.
- Wojtek Daszradę – Lean Specialist, tasked with driving process improvements.
HR and production have their teams. HR includes talent managers and recruitment specialists, while production managers oversee coordinators, who, in turn, manage team leaders on the shop floor.
And what about the Lean Specialist?
Unlike HR and production managers, the Lean Specialist operates alone. He has no direct reports and is expected to “deliver Lean” to the organization.
The goals of a Lean Specialist
In theory, a Lean Specialist should support the organization in continuous improvement.
In reality, their goals are very specific and measurable. Wojtek Daszradę is expected to:
- Conduct three KAIZEN workshops per month,
- Report the results of 5S audits,
- Monitor and report employee activity in KAIZEN initiatives,
- Report the status of Lean savings to CORTIM and achieve yearly cost-saving targets.
However, things get complicated when Wojtek tries to execute these tasks.
Where do silos come from?
When Wojtek attempts to organize a KAIZEN workshop, he faces resistance:
- Marek Dowieźto, the Production Manager, says:
“I don’t have time. Production has priority, and orders are more urgent than workshops.” - Rafał Wrabialski, Production Coordinator, responds:
“If you want to implement 5S improvements, do it yourself. I have other priorities.” - Monika Kadrowa, the HR Director, asks for a report on KAIZEN implementation but adds:
“Operators complain that they submit a lot of ideas, but only a few are implemented, so they don’t get their bonuses.” - Tomek Dydlajnowski, the Plant Manager, says:
“We are 20% below our Lean savings target. Speed up KAIZEN activities and collect more ideas from operators.”
As a result, Wojtek is left to deal with these challenges alone.
Everyone expects results, but no one wants to actively participate.
The creation of silos
This situation leads to the formation of two silos:
- The Lean silo, where Wojtek is responsible for optimizing processes.
- The Production silo, where Marek focuses on meeting production targets.
Each department works toward its own priorities.
Production does not engage in Lean because their focus is on output.
Meanwhile, Lean cannot function effectively without production’s engagement.
A historical perspective – a time when leaders owned Lean
But has it always been this way?
No.
In the 1940s in the United States, as industrial production expanded, leaders were naturally responsible for process improvement.
This was the foundation of the Training Within Industry (TWI) program, which developed leaders in four key areas:
- Job Instruction (TWI JI) – Teaching employees how to perform their jobs correctly.
- Job Methods (TWI JM) – Improving work methods for efficiency.
- Job Relations (TWI JR) – Building strong relationships within teams.
- Job Safety (TWI JS) – Ensuring workplace safety.
At that time, leaders were not just supervisors – they were responsible for:
- Training and instructing employees,
- Optimizing work processes,
- Resolving team conflicts,
- Ensuring workplace safety.
However, organizations later centralized these responsibilities, creating dedicated roles such as:
- One Lean Specialist instead of developing all leaders in Lean,
- One Safety Specialist instead of engaging team leaders in risk assessment.
Why? Because training one expert was easier than developing fifteen leaders to be proficient in Lean methodologies. But was this more effective?
Reversing the model – giving ownership back to leaders
What if Lean became a natural part of leadership again, and the Lean Specialist played a mentorship role rather than being the “deliverer” of Lean?
Imagine if leaders had weekly improvement goals, such as:
- Analyzing a process using TWI Job Methods and implementing quick wins,
- Investigating a drop in machine efficiency using an A3 report,
- Supporting operators in submitting KAIZEN ideas,
- Creating a standardized work instruction using TWI JI,
- Implementing corrective actions from a 5S audit,
- Addressing safety compliance issues with personal protective equipment (PPE).
In this model, the leader would approach the Lean Specialist for guidance:
“I need to prepare an A3 report. Can you help me structure it?”
“I want to create a TWI instruction – can you review my approach?”
This shifts the dynamic.
Instead of Lean requesting production’s involvement, production requests Lean’s support.
How can AI accelerate this transformation?
A few years ago, this shift would have been difficult.
But today, we have Artificial Intelligence (AI).
The biggest challenge in implementing Lean at the leadership level is time and expertise.
AI can address these gaps by supporting leaders in:
- Process Improvement – AI can analyze current work methods and suggest optimizations, allowing leaders to focus on execution.
- Problem-Solving – AI can generate an A3 report based on data provided by the leader.
- Standardized Work Instructions – AI can draft TWI job instructions, requiring only voice recordings from the leader.
- Team Management – AI can provide recommendations for resolving workplace conflicts based on gathered data.
The leader’s role? Capture the current state.
AI’s role? Analyze it and generate improvement ideas.
With AI, we eliminate the most time-consuming part of continuous improvement – finding improvement opportunities.
And Lean Specialists transition from executors to mentors.
At Leantrix, we are developing a dedicated AI tool to support this transformation.
You can see how it works in the video below, where AI generates improvement ideas for real production processes.
Conclusion – Lean AI
- Should Lean be the responsibility of just one person? No.
- Should leaders regain ownership of continuous improvement? Yes.
- Can AI help leaders become Lean experts? It already is.
If you want to see this in action, join our conference on June 10-11 in Wrocław, where we’ll showcase how AI and Lean can work together to empower leaders and eliminate silos in manufacturing. Visit KaizenUp.ai.
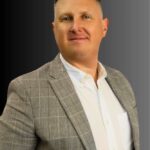
I am a promoter of Lean Management and the Training Within Industry program. I am a practitioner. I co-create many startups. Since 2015, I have been the CEO of Leantrix - a leading Lean consulting company in Poland, which, starting from 2024, organizes one of the largest conferences dedicated to lean management in Poland - the Lean TWI Summit. Since 2019, I have been the CEO of Do Lean IT OU, a company registered in Estonia that creates the software etwi.io, used by dozens of manufacturing and service companies in Europe and the USA.