This article provides a case study description of the Training Within Industry (TWI program) implementation at Autoliv Poland sp. z o.o., located in Jelcz-Laskowice. The article presents insights from both Autoliv employees and a consultant from LeanTrix sp. z o.o., who supported the implementation process.
Autoliv Corporation
Autoliv Corporation was founded in Vårgårda, Sweden, in 1953. Since its inception, Autoliv has been involved in the production of complete safety systems for automobiles (fig. 1). The company’s vision is to significantly reduce traffic accidents, injuries, and fatalities on the roads. To fulfill this vision, Autoliv designs, manufactures, and sells state-of-the-art vehicle safety systems. In brief, Autoliv is:
- A leader in technology and sales of safety systems, with a total sales revenue of $9 billion.
- A supplier to all leading car manufacturers.
- Operating 80 manufacturing plants in 29 countries, with 10 technical centers in 9 countries and 21 crash test tracks.
- An employer of over 64,000 people, including 4,000 employees in the R,D&E sector.
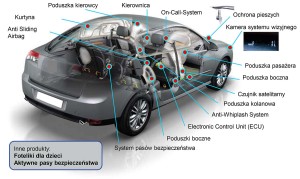
Autoliv
Fig. 1. Product portfolio manufactured by Autoliv Corporation
In Poland, Autoliv Corporation operates four production plants: two in Oława (AEP and APT) and two in Jelcz-Laskowice (APR and APA). In the Jelcz-Laskowice factories, seat belts have been manufactured since 2002, and airbag modules since 2010. In total, over 1,500 employees are employed at the Jelcz-Laskowice plants.
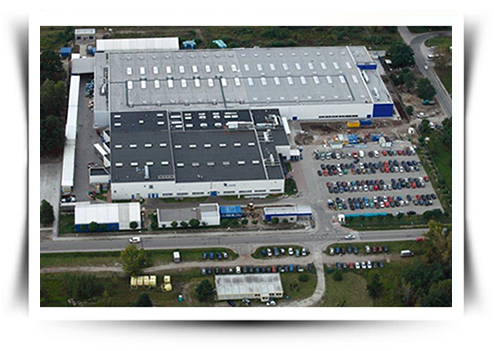
Autoliv w Jelczu Laskowice
Fig. 2. Autoliv Poland sp. z o.o. in Jelcz-Laskowice
The implementation of the TWI program, which is part of the case study described in the article, was initiated on selected production lines for airbag modules at the APA production plant in Jelcz-Laskowice.
Why the TWI Program?
The Training Within Industry program (TWI) is a comprehensive development program for supervisors, team leaders, foremen, and managers, focusing on Job Instruction (TWI JI), building good Employee Relations (TWI ER), and improving Job Methods (TWI JM). The TWI program was developed in the United States during World War II to help leaders efficiently integrate individuals who had never worked in industry—mainly women and youth—into the workforce. The implementation of the TWI program in American industry yielded tremendous benefits and significantly contributed to the defeat of Hitler’s forces. The success of this program was based on each method being built around the PDCA cycle, developed shortly before TWI by William Edwards Deming. After World War II, the TWI program was introduced as a key assistance program for Japanese companies, and shortly after, it gained such recognition that it became not only a productivity improvement method but also a culture of action in Japanese firms. To this day, TWI is considered a foundational element in the creation of the Toyota Production System, which later evolved into Lean Manufacturing.
Implementing the TWI program in manufacturing companies translates into improvements in their key performance indicators (KPIs), such as productivity, downtime, on-time delivery, quality, and safety. Losses in these areas are most often directly caused by human errors. According to Lean Management philosophy, effective problem elimination occurs when the root cause is addressed. In the case of human errors, root causes can include:
- Lack of or poorly conducted job instruction.
- Employees not adhering to work standards due to poorly developed standards.
- Lack of a process for auditing employees.
The TWI program is aimed at eliminating the root causes of human errors by providing effective methods for job instruction, auditing, and improving work methods (Kaizen).
The implementation of the TWI program at Autoliv’s production plant in Jelcz-Laskowice aimed to address specific production issues related to:
- Increasing employee headcount (over 300 new employees planned for 2016),
- Frequent employment of temporary workers,
- High employee turnover between production lines,
- Long onboarding time for new employees,
- Lack of skills transfer from experienced workers (tips, shortcuts) that extended the onboarding period for new employees,
- Failure to explain to new employees the precise reasons why they should work according to the established standard (lack of awareness among employees),
- Lack of willingness by experienced workers to use instructions (instructions often did not reflect actual production practices).
Competence Development in the TWI Program
In the implementation of the TWI program, the development of competencies among the employees involved in the program is crucial. Competencies should be viewed as a combination of three main components: knowledge, skills, and responsibility. At Autoliv, employee competence development was based on the PDCA cycle. Employee training (Plan phase) primarily aimed to build knowledge about the TWI program. Through practicing this knowledge (Do phase), employees began to develop skills. Once they were certified and began to use TWI methods independently, they assumed responsibility (Check phase). The final stage was training internal experts who not only had practical experience with the TWI program but were also able to teach others (Act phase). This process is illustrated in Fig. 3.
Fig. 3. Employee development levels involved in the TWI program
Between the training phase (1) and certification (3), there is the area of practicing methods (2). Often, when training companies are asked to conduct training (1), they are given a goal from top management: to build employee awareness and engagement. This goal is impossible to achieve! Awareness begins to develop only from the point of licensing (3). After training (1), people may experience euphoria and enthusiasm for applying Lean methods and tools. However, awareness comes from practice. The TWI program often fails in companies due to the lack of a practicing phase (2). This typically happens because people do not have set goals before training and do not have scheduled time slots to achieve those goals. Therefore, the role of top management in planning the implementation of the TWI program is crucial, as the most challenging moment in engaging employees is the practice phase (2). This process is best explained by using the example of teaching new drivers to drive on Polish roads. A person who undergoes theoretical training in a classroom reaches level (1). When this person starts learning to drive under the supervision of a Sensei (Japanese for teacher), they move to level (2). The practice process can take dozens of lessons, lasting several months! At this point, the person cannot drive a car independently—in a 0/1 scale, their rating is “0.” They obtain a license (certificate) when they pass the practical exam and move to level (3). In the future, if they decide to become a Trainer (in this case, a driving instructor), they must pass another exam and receive a diploma, moving to level (4).
Implementation Strategy of Training Within Industry (TWI program) at Autoliv’s Production Plant in Jelcz-Laskowice
The process of implementing the Training Within Industry (TWI program) at Autoliv’s production plant in Jelcz-Laskowice followed the PDCA cycle precisely. Table 1 provides a detailed scenario of this process, along with guidelines, rationale, and a specific description of the activities in Autoliv.
Table 1. Implementation framework of the TWI program at Autoliv’s production plant in Jelcz-Laskowice
Implementation Stage | Guidelines | Reasons | Description of Actions at Autoliv |
---|---|---|---|
1. Planning the implementation (PLAN) | 1. Selection of a pilot line | 1. Gaining practical experience and learning on a dedicated process so that subsequent full-factory implementation is more efficient. | Several production lines for airbag modules, critical in terms of quality and impact on the end customer, were selected for the project. |
2. Selection of the implementation group | 2. To implement the TWI program, individuals with extensive work knowledge (experienced operators and leaders) should be selected. Only then will the standards they create reflect the actual way of working. | The most experienced group for the selected production lines was defined. | |
3. Setting goals | 3. It is important to set measurable goals before the practical workshop. This allows people to participate more consciously in the workshop. | Selected individuals from the implementation group were given a clear goal in the practicing phase (Do) before the workshop. The goal was to create standardized work instructions for specific operations. | |
4. Conducting the practical workshop | 4. During the workshop, theoretical and practical knowledge is shared. Additionally, standardized work instructions are created under the supervision of a TWI expert. | The practical workshop lasted two days. During the workshop, 5 standardized work instructions were developed. Each participant had the opportunity to act as a TWI Instructor. The entire process was overseen by a consultant from LeanTrix. | |
2. Practicing knowledge by the implementation group (DO) | 1. Scheduling time slots | 1. Individuals involved in implementing the TWI program should have time to practice their skills (including creating standardized work instructions). | A selected group of 4 experienced leaders were provided with computer stations and the necessary time to develop all instructions for the selected production lines in the project. |
2. Consultations with a TWI expert | 2. Questions and ambiguities often arise during practice. It is important for a TWI expert to support practitioners in this process. | The LeanTrix consultant was available for the implementation group. Numerous phone calls were made to precisely clarify any doubts regarding the creation of standardized work instructions. | |
3. Licensing individuals from the implementation group (CHECK) | 1. Checking the developed instructions by the TWI expert | 1. A correct standardized work instruction is essential for conducting effective job instruction following the TWI JI method. | The LeanTrix consultant audited the standardized work instructions with the implementation group before the job instruction process. |
2. Checking the job instruction process conducted by the implementation group | 2. The TWI JI method is theoretically easy but poses many challenges in practice, as it often contradicts habits of most trainers. Therefore, it is important to check multiple times whether leaders are correctly applying the TWI JI method in practice. | Each of the 4 selected individuals from the implementation group underwent a practical audit conducted by the LeanTrix consultant on real production processes. In all cases, two audits were sufficient to certify the practitioners as TWI Instructors. | |
3. Certification as a TWI Instructor | 3. This is a formal process confirming that a person can create standardized work instructions and conduct job instruction in line with the TWI JI method. | After the audit, the LeanTrix consultant awarded the selected group of 4 individuals from the implementation group with TWI Instructor certification. | |
4. Expert development – Train the Trainer program (ACT) | 1. Selecting a candidate for TWI Trainer | 1. A TWI Trainer is a person who not only practices the TWI JI method but can also teach other employees (Sensei in Japanese). | One person from the certified TWI Instructors was selected to undergo training to become a TWI Trainer. |
Benefits of Implementing the TWI Program at Autoliv
The TWI program has been implemented at the APA production plant in Jelcz-Laskowice since July 2015. Currently, the program covers nearly 20% of the airbag module production lines. Ultimately, this program is expected to be fully implemented across both factories in Jelcz-Laskowice. Initial actions to implement the TWI program have also been undertaken at Autoliv’s factories in Oława.
The first benefits of the TWI program can already be seen in the behavior and attitude of employees working on the pilot lines. The TWI program places significant emphasis on explaining job instructions (including tips and shortcuts) and the reasons behind these instructions, helping employees understand the essence of their work. Employee awareness is crucial, as it has a major impact on eliminating human errors, which are mainly caused by lack of knowledge. Currently, on the pilot production lines, it is difficult to find an operator who, when asked, “Why do you perform this operation in this way rather than another?” would answer, “Because my supervisor told me to.” Every employee fully understands why they must perform the work in a specific way and how it impacts the process and the end customer. If an employee forgets something, they can always refer to the standardized work instruction, using which the TWI Instructor trained them. We believe that this approach to training employees will translate, in the long term, into improved KPIs for the company.
At Autoliv, we believe that employees should not be blamed for human errors—only the processes should be. Designing and defining processes is the responsibility of the supervisors. Supervisors must take responsibility for potential human errors. The motto of the TWI Job Instruction method is: “If the employee hasn’t learned, it means the teacher hasn’t taught them.” This motto forms the foundation of employee competency development at Autoliv. Respect for employees, expressed through effective training, is one of the company’s most important values.
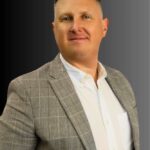
I am a promoter of Lean Management and the Training Within Industry program. I am a practitioner. I co-create many startups. Since 2015, I have been the CEO of Leantrix - a leading Lean consulting company in Poland, which, starting from 2024, organizes one of the largest conferences dedicated to lean management in Poland - the Lean TWI Summit. Since 2019, I have been the CEO of Do Lean IT OU, a company registered in Estonia that creates the software etwi.io, used by dozens of manufacturing and service companies in Europe and the USA.