TWI in Cooper Standard is known as a BTO. Cooper Standard is a leading global supplier of systems and components for the automotive industry. Products include rubber and plastic sealing, fuel and brake lines, fluid transfer hoses and anti-vibration systems. Cooper Standard employs more than 30,000 people globally and operates in 20 countries around the world (Figure 1).
Fig. 1. Global locations of plants
Source: Web site: http://www.cooperstandard.com/
Cooper Standard is accelerating game-changing advancements in material science to produce environmentally conscious solutions and automotive components that reduce weight, lower emissions, enhance design and improve vehicle performance for our customers.
As a leading global supplier of systems and components for the automotive industry, Cooper Standard is ranked as:
- The leading global supplier of sealing systems;
- The second largest global automotive supplier of fuel and brake delivery systems;
- The third largest provider of fluid transfer systems; and
- The North American leader of anti-vibration systems.
Cooper Standard established its Profitable Growth Strategy in 2013 to provide a clear vision, set of values, and strategy to achieve its mission to become one of the Top 30 global automotive suppliers in terms of sales and Top 5 in ROIC (return on invested capital). Since that time, the Global Leadership Team has evolved and refined the strategy to more closely represent the Company’s culture and provide a path for continued growth by driving value through the Company’s culture, innovation and results (Figure 2).
Fig. 2. Cooper Standard Automotive Vision
Source: Web site: http://www.cooperstandard.com/
Strategy of the implementation ofContinuous Improvement philosophy in Cooper Standard Automotive Europe
Organizations that use Lean Tools or Lean Manufacturing systems often start from the implementation of individual solutions and forget about one very important element -planning an effective strategy. A strategy expresses the long-term goals of an organization that are coherent with its main business directions and also allows efficient allocation of the resources that are needed to achieve desired effects. A well-planned strategy can significantly improve the effectiveness and speed of any organizational changes that are being implemented within Lean Management, which enables the effect of synergies between selected components to be fully used. This is only provided when the strategy is properly planned and carried out. The very important step in the effective implementation of Continuous Improvement strategy is to prepare KPIs (Key Performance Indicators). It’s important to understand that KPIs are not only company-wide metrics, but may focus on the operating efficiency of individual parts of the company which can then be related back to how those parts affect the whole. Tracking KPIs not only shows how departments work together to achieve the goals, but how individuals within each department can contribute to the organization success. The purpose of KPIs is to tie everyone in the organization to the one common goal. This is a very important for our organization.
However, before the start of any action, the present state of an organization should be well defined by answering the following two questions:
- Who constitutes a team in a department, factory, division or even whole corporation?
- What level of Lean Management is an organization presently at?
The first question of who constitutes a team in an organization is particularly important in the case of companies that are at the beginning of their adventure with the philosophy of Continuous Improvement. However, this does not meanthat it does not apply for companies that are more advanced in Lean. In general, each team is divided into change leaders (about 10%), those who will adapt to changes (about 80%) and also opponents of changes (the remaining 10%)whose basic argument is that theyhave always worked in such a wayand thereforedo not feel the need to change anything (Figure 3)[Prasał 2016]. For each organizational structure, two groups are fundamentally important. These are the change coordinators, and above all, the management staff of a particular structure.This is because the success of Lean Management and the effectiveness of each undertaken step, including the active promotion of Continuous Improvement culture, depend on their active attitude.
Fig. 3.Structure of a team
Three levels of Lean Management (Figure 4) should be distinguished when answering the second question. The first level, the so-called tool level,mainly characterizes organizations that are just starting their adventure with process optimization. These can sometimes be the organizationsthat treat Continuous Improvement as a savings program. Such an approach uses, to a very limited extent, the possibility of lean management.However,afteran initial success, it is usually difficult to stabilize and maintain implementation of Continuous Improvement approach for a longer period of time.
The second level can be observed in companies that systematically deal with the issue of Lean and are aware that due to such an approach, synergy, which is a result of the comprehensive implementation of many Lean Manufacturing tools, can be achieved. The highest level in the Kaizen area is reached by organizations for which Lean Management has become a way of doing business. Employees of these companies treat individual tools and continuous development as their natural way of working. There are a number of solutions available on the market that enable the level of organization to be determined. Some companies have an internal audit that is very helpful and ispart of the system itself. Understanding the goal is not as important as understanding the starting point, because this is where you are and this is where the journey begins.”
Fig. 4.Three levels of Lean Management
Source: Prasał 2016
Cooper Standard Corporation has been developing tools and Continuous Improvement systems in specific locations for many years. Based on these practices and seeing the potential intheirexchange between plants, one World Class Operation (WCO) system was developedthat is common for all locations. It has become an integral part of the culture and vision of a company that is constantly striving for perfection.
An assessment of WCO has become a tool that supports the development of the system and also allows the progress of each location to be measured. It is a form of a Lean Management audit, which is divided into 10 chapters, each of which allows one tool to be measured (Figure 5). The whole WCO assessment consists of 150 questions – 15 for each chapter (an answer of “Yes” or “No” is required for each question).
Fig. 5.World Class Operation Assessment
Based on the results of an audit from 2016 (Figure 6) and taking into account feedback from all European locations, the Continuous Improvement team presented a short-term and long-term strategy.
Fig. 6. WCOassessment from 2016
The four following areas that CSA Europe would like to deal with first were determined:
- Further development of the WCO assessment (the so-called WCO assessment 2.0),
- The Value Stream Map,
- Total Productive Maintenance,
- Standardization based on the exchange of best practices.
Re1) Seeing the benefits and potential of Lean Management’s comprehensive approach, CSA Europe has decided to further describe the requirements and criteria of each Lean tool.The aim is to create/update the WCO assessment, which will also strengthen and accelerate the implementation of Lean culture within an organization. The next stage will be the introduction of an independent (not from the factory) group of auditors who will provide an objective assessment, which will in turn further improve the possibilityof comparing tools in individual plants and thereby improve the identification and exchangeof best practices.
Re2) CSA Europe also considered improvements in Value Stream Mapping as fundamental. The benefits, which give the correct use of this tool, are as follows:
- Visualization of the flow of information, a process and material on one sheet
- Support in defining the priorities of Continuous Improvement
- Designing the future state
- Reduction of inventory (cash release)
- Reduction of Lead Time
- Elimination of waste (8 Losses)
- Reduction of costs
- Achievement of the requirements of the CSA system – World Class Operation
Re3) Total Productive Maintenance is another area chosen as a priority in the field of Continuous Improvement. Great potential is seen in the development of Autonomous Maintenance approach. The main goals of the development of this program are:
- Formation of the best global standard, which is based on best practices from individual plants,
- Improvement of performance indicators (KPI’s)
- Increaseof the involvement of direct production staff
- Achievement of the requirements of the CSA system – World Class Operation
Re4) The standardization (global) of Lean Management tools is carried out in the case of the three above-mentioned tools. An additional element that supports this process is the creation of global training materials – the WCO Academy. As is the case in a single plant, the first step of further improvement in a whole corporation is the creation and determination of one common standard that is based on the knowledge and experience of each employee.
The BTO system –World-Class Operations (WCO) part
The Building a Talented Organization (BTO) system is an initiative that develops the skills of experienced employees in the field of effective knowledge transfer (instruction of staff). The basis of the BTO system is the Training Within Industry (TWI) program and more specifically, one of its methods – TWI JI – Job Instruction (Figure 8).
Fig. 8. The BTO system and the TWI program
The TWI program is essential for the implementation of work standardization, which not only comes down to creating work instructions but, above all, the ability to use them when teaching employees and improving Kaizen work methods. The BTO system is now the 11th pillar of the WCO system in the European division of our organization.
TWI in Cooper Standard – The TWI JI method is a key part of the BTO system
The TWI JI method is orientated towards an effective way of introducing employees to a job. One of the stereotypes about this method is that it shortens instructional time. This is not true. The TWI JI method reduces the time of introducing an employee to a job – the time it takes for him to be fully effective at work. This is not coherent with instructing itself. The TWI JI method is also orientated towards educating employees in conscious work performance. This is why so much emphasis in this method is placed on explaining the reasons of key work points.
The main goal of the TWI JI method is to teach experienced employees how to transfer their knowledge and experience to less qualified operators. However, the essential element of training – the starting point, is to prepare correct documentation. In our organization, in areas covered by the BTO, documentation is prepared by engineers in collaboration with experienced operators and leaders. Only then is there an assurance that work instructions contain tricks and facilitations that shorten the implementation time of employees to full work efficiency. There are two types of documentation describing the work of operators within the BTO system:
- Job Breakdown Sheets (JBSs)
- Standard Work Instructions (WIs)
A JBS is a tool for an instructor who is carrying out training. It contains the major steps, key points and reasons for key points (Figure 9).
Fig. 9. The creation of a Job Breakdown Sheet in the TWI JI method
Source: Misiurek 2016
WI is a document for a learner after being trained.WI, when compared to a JBS, is enriched with photos, symbols, and explanations such as special characteristics. WI is prepared for each reference. A JBS is the main document that guides an instructor through training. The key points from a JBS refer to specific references in WI. Using an example from the home – there is one main JBS for the laundry washing process, in which there is no detailed data such as the selected temperature or rotation speed of the washing machine. Every type of laundry (e.g. white delicate fabrics, workwear, etc.) has its own WI, for example, with the optimal washing temperature. When carrying out training according to the TWI JI method, an instructor uses the main JBS and WI for a specific reference. Thanks to this approach, documents describing work have become the basis of on-the-job training and also help for learners after training.
Internal training is an indispensable stage when implementing the TWI JI method. This is where employees are taught how to make correct documentation. It is a real challenge because the creation of standards according to TWI is not a straightforward process. It requires adapting to many rules and principles that are unintuitive for people who make instructions every day. Filling out a WI form and writing the correct WI are two different things that our instructors and engineers have already experienced.
TWI in Cooper Standard – Implementation of the BTO
The implementation of the BTO system in the European division of our organization has been divided into three phases (Table 1). Currently, there is the so-called second wave of implementation, which includes:
- New projects;
- Critical projects (e.g. important in terms of quality, safety);
- Diamond Cells.
Tab. 1. Three phases of implementing the BTO system in Cooper Standard (European Division)
Implementation phase | Time of execution | Phase description |
Pilot implementation in 4 plants | March 2016 – June 2016 | The pilot project was undertaken by four plants – from Poland, Germany, France and Italy. Each plant had one pilot area selected. All managers and people working in the pilot area were trained in the TWI JI method. After the training, each plant went through an audit and a Follow Up session conducted by TWI Lead Coach Europe. The purpose of this session was to verify the documentation and skills of instructorsin the area of using the TWI JI method. On-the-job trainings were then carried out and the effects (outcomes) were measured. The whole phase ended with a joint meeting of representatives of the four plants, exchange of experiences and the writing down of recommendations for other plants on how to introduce the BTO system in the first wave of implementation. In addition, 6 people from the four countries were selected to undergo training to become internal TWI trainers. |
The first wave of implementation in all plants | July 2016 – December 2016 | The first wave of implementation was based on the recommendations of the plants taking part in the pilot implementation. Each Cooper Standard European division had the task to select a pilot area where the TWI JI method would be implemented. The TWI training and Follow Up sessions were mainly conducted by internal trainers. |
The second wave of implementation in all plants | January 2017 – up to now | The second implementation wave is focused on all new projects launched in the European Cooper Standard division. In addition, the BTO system and the TWI program will cover all Diamond Cells. |
Implementation of the BTO system in the European Cooper Standard division is proceeding methodically. We know that changing the way of teaching employees and how to create documentation in a company is not an easy challenge. It takes time and understanding. Thanks to such an approach, very good results have been achieved. All the plants thattook part in the implementation of the TWI program in the so-called first wave managed to:
- increase work productivity by an average of 17.55%,
- reduce the level of deficiencies by an average of 35.83%.
A very important part of the BTO implementation system is reporting. European divisions are required to submit a BTO implementation report each week. The report defines the status of the implementation and records all the Lessons Learned from a particular week.
We are currently in the process of training our internal BTO Trainers. Each plant has at least one person that hasthe role of a Plant BTO Trainer. Ultimately, these Trainers will take responsibility for maintaining the BTO system at plant level.
Summary – TWI in Cooper Standard
CSA Europe identified detailed actions in the area of Continuous Improvement for subsequent years (Figure 10) in order to be able to function long-term.
Fig. 10 Strategy for the years 2016 – 2019
The organization believes that action in a systematic and orderly manner brings long lasting results and allows effective interaction with competitors on the market.
Literature
Web site: http://cooperstandard.com/ [8th of April, 2017]
Misiurek B., 2016, Standardized Work with TWI: Eliminating Human Errors in Production and Service Processes, Productivity Press, New York
Prasał M., 2016, Masa krytyczna, Czasopismo Kaizen, 3/2016
1 Vice President Quality and Continuous Improvement Europe, Cooper-Standard Automotive Inc.
2 Director Continuous Improvement Europe, Cooper-Standard Automotive Inc.
3 TWI Lead Coach Europe, Cooper-Standard Automotive Inc.
4 Senior Continuous Improvement Manager, Cooper-Standard Automotive Inc.
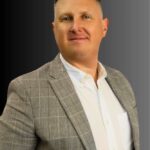
I am a promoter of Lean Management and the Training Within Industry program. I am a practitioner. I co-create many startups. Since 2015, I have been the CEO of Leantrix - a leading Lean consulting company in Poland, which, starting from 2024, organizes one of the largest conferences dedicated to lean management in Poland - the Lean TWI Summit. Since 2019, I have been the CEO of Do Lean IT OU, a company registered in Estonia that creates the software etwi.io, used by dozens of manufacturing and service companies in Europe and the USA.