The Rolls-Royce Poland factory is located in Gniew. As part of its activities, Lean, TWI, and HR training sessions have been conducted there.
“Perfection is made up of small things, but perfection itself is a big thing.” – Sir Henry Rose.
In many companies, there is a growing awareness of the importance of achieving higher standards to provide better opportunities for a changing world. As a result, managing companies based on Lean Management principles is becoming increasingly common. This is nothing more than creating a culture of continuous improvement.
Between 2009 and 2010, our Rolls-Royce Poland factory underwent a major modernization. From that moment on, we can speak about the beginning of our journey toward continuous process excellence. It is a never-ending journey, through which our ingenuity and pursuit of perfection enable us to deliver better opportunities.
Rolls-Royce Poland – A New Vision
Our factory began this journey with many changes in the organization. We can identify several key elements that contributed to its success: the company’s development vision, the determination of the leaders, a consistent system based on metrics, skillful use of Lean and Six Sigma tools, and employee engagement. Therefore, the first step was a new approach to change management. To this end, our factory introduced the Gniew Improvement Journey (GIJ). The goal of this project was to define at least one improvement project in every business area. Additionally, the main criterion for defining the project was business needs, which helped us eliminate unnecessary changes. Each approved project included a goal, deliverables, scope, timeline, team composition, team leader, and success metrics (so-called KPIs). All projects were documented using project cards, monthly ABCD reports (Achievements, Benefits, Concerns, Action Plans), and KPI results.
The Role of Leaders in GIJ
Project leaders were supported by Business Improvement Black Belts (BIBBs) and Sponsors. Once a month, all project leaders met at the GIJ Meeting to review the progress of process improvement projects with the Plant Director, Sponsors, and BIBBs. This review was based on a tool that assessed the foundational process area, its capabilities, value stream flow, and control. It is also worth noting that all projects and their current statuses were made available to all employees on two boards: one in the production workshop and the other in the main office lobby. Thanks to this project visualization, anyone interested could attend the monthly meeting. Furthermore, the projects were discussed during monthly meetings between the Plant Director and employees, where the Project Leader presented the project scope, explained why it was being addressed, and outlined the expected benefits. These presentations helped engage an increasing number of employees.
GIJ in Rolls-Royce Poland
This GIJ tool has enabled us to complete numerous projects over the past five years. The ingenuity of the employees is enormous, which is reflected in the fact that we continue to hold our regular GIJ meetings. Year after year, “we go one level lower in project management” – the first projects were led by directors, followed by managers, then supervisors or senior specialists. Today, specialists, technicians, engineers, and independent employees lead projects.
The Role of HR in Implementing GIJ
In this entire process, we cannot forget the role of the HR department. Based on business needs and the development vision, HR had to introduce or improve several aspects.
Employee Competencies
One of the key areas was employee competencies, helping them answer questions like: How to lead projects? What tools to use? Many questions arose regarding the managerial staff’s capabilities and the successful implementation of the Lean Management philosophy. To address this, we created competency matrices in every business area. These matrices included all the critical skills and necessary knowledge required not only for project tasks but also for daily work. A special Lean training program was prepared, ranging from Lean factory simulations to TWI (Training Within Industry) training for production workers and APICS (American Production and Inventory Control Society) methodology for planning-related employees.
The competency matrices are one of the main tools defining not only the basic competencies of employees but also introduced multi-skills for production workers, which enabled employees to develop in several areas.
It is also worth mentioning the training for Green Belts – individuals leading projects using the Lean Six Sigma methodology. Additionally, the factory introduced Yellow Belt training as a fundamental course for every employee, meaning that each worker contributes to improvements in their daily work.
5S as a Foundation
A crucial element in creating a culture of continuous improvement was the implementation of 5S, which we began on the production floor. This helped engage the entire workforce in our journey. To keep this process “alive,” we run a 5S competition, where departments compete for the top spot.
The “I Have an Idea” Program
In our pursuit of continuous excellence, the factory introduced the “I Have an Idea” program, aligned with Lean philosophy. This program is targeted specifically at workshop employees who know the most about their work. “I Have an Idea” supports continuous improvement through small steps and minimal costs. Even seemingly small improvements can significantly impact our work’s efficiency. The best ideas are rewarded during all-employee meetings, and project statuses are displayed on the information board. This program has contributed to many improvements, such as a tool for rotating parts in the welding process, reorganizing workspaces, and standardizing work areas.
Training Within Industry (TWI) in Rolls-Royce Poland
The journey to implementing the Lean philosophy never ends, as it is a continuous improvement process. This is where I should mention the implementation of TWI (Training Within Industry) at the factory. It was the beginning of a path the factory took to implement a consistent, effective, and simple system of internal job training. The condition for building an organization with agile production capabilities is having a highly skilled and flexible workforce, requiring the standardization of training processes, selecting appropriate trainers, reducing training time, and systematically developing employees. Thus, we decided to implement TWI. Training Within Industry is a program that develops the skills of supervisors, managers, and workers in Job Instruction (JI), Employee Relations (ER), Work Methods (WM), and Safety (JS). TWI has become the foundation of the Lean Management philosophy. The TWI program was created in the U.S. in the early 1940s and was used to train new and inexperienced supervisors and managers.
The Goal of Implementing TWI in Rolls-Royce Poland
The goal of implementing the TWI job training system was to ensure efficient training for production workers. Naturally, this involved tangible benefits that the factory achieved, such as:
- Reduced employee training time
- Standardized knowledge shared by trainers using Job Breakdown Sheets (JBS), regardless of who delivered the training
- Continuous improvement of existing employees’ skills to ensure they perform their work effectively and without errors
- Elimination of rework, resulting in increased productivity
- Enhanced employee flexibility, shortening lead times for production orders
All supervisors, managers, production workers, and HR employees underwent training in Job Instruction. This enabled them to create Job Breakdown Sheets (JBS). The next stage included Work Methods TWI training, aimed at showing how to improve current work methods to produce more quality products in less time with the same team, machines, and materials. This module was based on the Kaizen Event philosophy. This means that the training was conducted on the production floor, where we learned how to improve existing work methods. The final two modules focused on improving workplace safety and enhancing employee relations, leading to better problem-solving between supervisors and subordinates. This eliminated issues related to implementing changes and productivity losses caused by unresolved interpersonal conflicts. TWI allowed us to integrate regular Kaizen workshops into the factory’s culture and ensure effective training for inexperienced workers.
Summary of Implementation at Rolls-Royce Poland
We can confidently say that introducing simple Lean Management tools has successfully engaged employees in a way that makes thinking about continuous improvement a normal part of their daily work. Undoubtedly, simple tools like PDCA culture, 3C sheets, and brainstorming contributed to this success.
The Lean philosophy is nothing new for factory workers. Lean is our way of thinking. Many of us use Lean tools to be better, reduce waste, or increase efficiency. This mindset makes us focus on value-added, problem-solving, and continuously improving our business. All of this is naturally supported by management and coaching.
We are a company where identifying and eliminating waste in all forms is our way of life. Every person can learn through their role in the organization and their individual development plan. Such Lean thinking is expected from all of us. Leaders create an environment where continuous improvement is the norm. Lean Sigma experts (Green Belts, Business Improvement Black Belts) play a key role in supporting the business by setting priorities, selecting the most effective improvement methods, and delivering results on time.
The true Lean philosophy is about daily thinking, adjusting our behaviors, and working to improve how we do our jobs. As Sir Henry Rose said: “Perfection is made up of small things, but perfection itself is a big thing.” Supporting continuous improvement, through small steps and minimal costs, means that seemingly small enhancements can significantly impact our work’s efficiency. Therefore, from an HR perspective, it is essential to do the right things in the right place in daily work. We set standards and ensure that all employees understand and know what we expect from them. We create a work environment where proper leadership ensures that each of us participates in the journey toward continuous improvement to deliver better opportunities for a changing world.
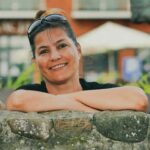
Partnering with business leadership to develop people in order to deliver the right talent, organisation and culture. Developing process and policies to drive standard, consistent services and solutions across HR.
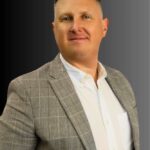
I am a promoter of Lean Management and the Training Within Industry program. I am a practitioner. I co-create many startups. Since 2015, I have been the CEO of Leantrix - a leading Lean consulting company in Poland, which, starting from 2024, organizes one of the largest conferences dedicated to lean management in Poland - the Lean TWI Summit. Since 2019, I have been the CEO of Do Lean IT OU, a company registered in Estonia that creates the software etwi.io, used by dozens of manufacturing and service companies in Europe and the USA.