This material is based on the authors’ experience in implementing Lean Management philosophy in a production environment (Nidec Motors & Actuators and LeanTrix consultant). The solutions presented in this article aim to show how to engage operators in tasks related to Total Productive Maintenance (TPM). The examples can also serve as a guide for implementing other Lean Management methods and tools, such as the TWI program, 5S system, SMED, etc.
Introduction to Nidec Motors & Actuators
Nidec Motors & Actuators (Poland), based in Niepołomice, is part of the Japanese Nidec Corporation, founded in 1973. It is one of the world’s largest producers of precision drives and systems used in various industries, including IT, automotive, aerospace, and machinery.
Nidec’s main product groups include:
- Small precision motors (e.g., motors for hard drives, laser printers, mobile phones, DVD recorders, CD players)
- General-purpose motors (e.g., automotive motors for steering assist, engine cooling systems, seat regulators, door closure systems, traction systems, household appliances, and industrial applications)
- Machines (e.g., robots, card readers)
- Electronic and optical components
Nidec Corporation operates across:
- 14 business sectors
- 169 subsidiaries in 25 countries
- 107,500 employees, with 90% based outside Japan
Nidec Motors & Actuators (NMA) is one of Nidec’s 14 business sectors, designing and producing electric motors and drives for automotive and industrial applications. The company’s plants are located in Germany, Spain, China, and Poland (Niepołomice). Nidec Motors & Actuators offers six product lines: Braking, Automotive Closures, Airflow, Automotive Seat Adjusters, Custom Actuators, and Industrial Drives.
Employee Involvement in Lean Management and TPM
In many companies, there is a belief that employee engagement in Lean Management can only be achieved through financial compensation. Often, companies that implement employee suggestion systems (commonly known as Kaizen systems) offer financial rewards for submitted or implemented ideas. However, our experience shows that company culture plays a far more significant role than monetary rewards in fostering continuous improvement. Building a Lean culture requires daily engagement, not just financial incentives.
In this case study, we present how to build a Lean culture in areas where operator engagement is required but not rewarded financially. This approach ensures that engagement becomes part of daily work, not just tied to Kaizen. If a company builds a Lean culture, the Kaizen system will naturally function well, with financial incentives serving as additional motivation but not the sole reason for engagement.
Engaging Employees in TPM at Nidec Motors & Actuators
Successfully implementing and applying TPM tools depends on the engagement and motivation of employees, particularly production operators. From the start, Nidec aimed to create a strong, stable organization that supports professional and personal growth. Production operators possess extensive knowledge about the functioning of machines and the issues encountered during their operation, which is critical to the success of the TPM system.
Our main goals were:
- Maximizing equipment efficiency by eliminating major losses
- Establishing an autonomous maintenance system conducted by operators
- Setting up a planned maintenance system carried out by the maintenance department
- Gaining support from management and all employees
To achieve these goals, we completed a series of tasks.
Autonomous Maintenance Instructions
We started by creating clear instructions for the basic inspection of machine mechanisms. These instructions were developed for machine operators with their involvement, covering two levels of maintenance. At the first level, operators check the correct operation of safety systems and perform basic cleaning. The second level involves regular stops of the entire production line, during which maintenance technicians and operators clean and inspect the technical condition of each machine. Identified issues are addressed either immediately or documented for future resolution.
The instructions are continuously improved as new problems are discovered. This ensures that standards are developed with the involvement of those responsible for their execution, a critical point in engaging operators.
Reporting Machine Problems
A key part of TPM implementation is encouraging operators to report problems observed during production. We created a system that allows for problem reporting and tracking their resolution. Issues regarding machine operation, product quality, or safety are reported on “red cards,” which are entered into a TPM database and assigned to the appropriate personnel for resolution. Simple visualization through TPM boards near production lines helps operators see the progress of their reports, which has significantly increased engagement.
Employee Recognition in TPM Activities
To encourage TPM involvement, we reward the most active operator each month with a surprise recognition (non-monetary). This simple recognition motivates employees and highlights those with potential for promotion to maintenance technician roles. Around 50% of Nidec’s current maintenance team started as production operators, and TPM activities provide a pathway for career growth.
Summary
Based on our practical experience, we know that TPM and all Lean Management methods are “soft” tools, meaning they rely on human factors and communication. Building a Lean culture is rooted in employees’ engagement and understanding of the importance of standards. While TPM starts with improving machine performance, its success depends on effective communication and shared responsibility from the outset. Engaging employees in Lean activities leads to both operational improvements and personal development for employees.
Benefits for the Company:
- Increased employee ownership and care for equipment
- Reduction of machine breakdowns and defects, with more confident operators
- Improved plant efficiency and workplace aesthetics
- Enhanced company image through a well-maintained production floor
- Unleashed creative potential among employees
Benefits for Employees:
- Opportunities for skill development and career advancement
- A platform to present ideas to management
- A cleaner, more organized work environment
Authors: Mateusz Danek, Dr. Eng. Bartosz Misiurek
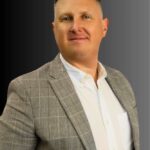
I am a promoter of Lean Management and the Training Within Industry program. I am a practitioner. I co-create many startups. Since 2015, I have been the CEO of Leantrix - a leading Lean consulting company in Poland, which, starting from 2024, organizes one of the largest conferences dedicated to lean management in Poland - the Lean TWI Summit. Since 2019, I have been the CEO of Do Lean IT OU, a company registered in Estonia that creates the software etwi.io, used by dozens of manufacturing and service companies in Europe and the USA.