Imagine a windmill, old and heavily worn, with its rotating parts rusty and its blades full of holes. However, this windmill still serves its purpose because it stands in a location where strong winds blow. However, here comes the question: what happens when these winds weaken? Will the friction caused by the enormous resistance allow our windmill to move? The windmill represents our company, and the wind symbolizes changing market conditions. The example of TWI in this article describes the process of repairing the blades that drive the organization, i.e., the training system and employee competence development.
TWI Program at Danone – Example of TWI in Practice
Challenges and Goals – Example of TWI in Action
Any organization can divide the challenges it faces into two categories. The first category is external challenges, examples of which include cost increases, product customization, seasonality, the labor market, and many others. Meanwhile, the second category is internal challenges, which are those over which we have direct control as managers within the organization. Examples of such challenges include lengthy onboarding and ineffective monitoring. Additional issues are tribal knowledge and a lack of structured employee development.
As highlighted earlier, the example of TWI at Danone shows how a systematic approach to competence development helps the organization meet both internal and external challenges. Considering both internal and external challenges, the team developed a vision based on Danone’s pillars of development: multiskilling, digitalization, and automation. Consequently, the vision for the TWI project was: an organization flexibly adapting to market requirements through a systematic approach to building competencies.
TWI Goals at Danone – Example of TWI in Action
- REDUCING EMPLOYEE ONBOARDING TIME – quick and efficient onboarding of new employees and those changing roles within the organization, without sacrificing quality and productivity.
- INCREASING EMPLOYEE POLIVALENCY – increasing workforce replaceability, which allows protection against unforeseen situations (e.g., sick leave during a pandemic).
- DOCUMENTING EXPERT KNOWLEDGE – in the case of retirement, employees’ knowledge remains within the organization.
- STANDARDIZING THE DEVELOPMENT PROCESS – this allows monitoring progress and highlighting employees with the highest skills.
Location of Activities
The production processes in the food industry are characterized by high automation, and Danone’s case is no different. Therefore, this results in a substantial amount of knowledge regarding machinery and equipment on the production lines, which takes time for employees to grasp, but more importantly, to translate into practice. Four Żywiec Zdrój water bottling plants were chosen as pilot areas. In the first phase, TWI focused on warehouse processes and the end of the bottling lines, where the finished products are packed.
Timeline and Duration
The transformation process at Danone was divided into 5 phases, starting at the end of 2020. A decision was made to move towards TWI, and the change preparation phase began.
Phase 1: Preparing the Change
The first phase of transformation is crucial – it often determines the success of the project. A key element of preparing for change is analyzing the current state, which allows determining what is working well and what needs improvement. As a consequence, this lays the groundwork for creating a detailed work schedule. At this stage, the team also formulates the vision and goals related to the TWI program. The establishment of the implementation team, which manages TWI activities, is crucial for the transformation. Before moving forward, the team recruits candidates for instructors, following prior communication about the benefits of the TWI program.
Phase 2: TWI Workshops for Pilot Areas
The second phase of the transformation involves conducting workshops in the pilot areas. These workshops focus on practically acquiring skills in creating work instructions and instructing employees. Despite the pandemic period, the team fully carried out these tasks remotely. As part of this phase, they trained management staff. Additionally, they also consulted trainers about the developed instructions and conducted job training.
Phase 3: Practicing
After the workshop phase, there was a six-month practice phase, during which candidates for TWI instructors practiced the method and consulted challenges with trainers. Importantly, the final element of this phase was the certification of instructors, which is confirmation of their skills in creating standards and instructing according to the TWI method.
Phase 4: Monitoring and Adjustment
The team dedicated the fourth phase to analyzing the completed actions, evaluating them, and implementing improvements in the TWI implementation process in the respective areas. Based on earlier practice, the organization extracted many important insights that allowed for adjusting the course that TWI was following. Employee development became a permanent part of daily meetings, discussed alongside key issues such as safety, quality, and productivity. Moreover, many of the instructions developed during the practice phase became the foundation for process improvements, which generated numerous optimization ideas. To achieve this, the team used audits such as 20Q, 10Q, and 5Q to analyze the actions, ensuring that the adaptation of TWI to the organization was based on facts.
Phase 5: Continuous Development of the TWI Program
The final phase of the TWI transformation at Danone focuses on continuously developing the program for new machines and positions. This ongoing process is made possible by the certification of TWI trainers, ensuring continuous improvement. In particular, a TWI trainer is someone who can independently conduct workshops and oversee the TWI program within the organization. Additionally, this person supports the development of instructors and certifies them within the organization.
Key People Involved
People mainly determine the success of projects, as the composition of the team influences the effectiveness of the actions taken. In this case, the HR Business Partner for 4 Żywiec Zdrój plants was responsible for the entire project. Key people in the steering team also included area managers and shift managers. The sponsor of the change was the director at each respective location. One of the biggest challenges faced by the implementation team was the issue of engaging people directly involved in production. This especially concerns the leaders, who bear the responsibility for most of the operational activities. Without their support, the transformation would have little chance of success. Leaders analyzed the current state, designed the target state, and influenced the selection of tools to be used. The TWI program touches many areas of the organization. For example, when creating work instructions, support from the quality and occupational health and safety departments is necessary. In terms of human resources, direct supervisors who lead the training and create instructions play a significant role. Those managing the transformation need both interpersonal and project management skills.
How the team uses the methods in automated production
The nature of water bottling production makes it hard to apply the standard method.Specifically, it requires mastering tasks like machine changeovers, component additions, problem-solving, and TPM. All of this means that the variability of work during a production shift is much greater than in assembly-based production. In managing the bottling line, employees focus more on maintaining continuity rather than producing parts manually. This increases the time required for onboarding, as it demands a broader knowledge base. Additionally, processes like changeovers take longer, making it harder to apply the standard TWI method. For certain trainings, the approach was slightly modified to accommodate long and infrequent processes. This modification reduces task repetition during training but requires the trainer to provide more oversight of the trainee after completing the training.
Obstacles and Results
The TWI program transformation at Danone lasted 1.5 years. It involved around 250 employees from production and warehouse teams. During the process, many obstacles were encountered, and solving them significantly facilitated actions in subsequent areas. The biggest obstacles included:
- Lack of easily accessible indicators to assess the current state,
- Low engagement of shift managers,
- Time management for training,
- Time-consuming process of creating and managing documentation.
Key Benefits of the TWI Program Implementation:
- Inreased training efficiency reduced onboarding time by 37% in warehouse areas and 50% in production areas,
- Increased ability to work across various positions/machines – from an average of 2 positions to an average of 3 positions,
- Monitoring training progress and trainee independence aids decisions on contract extensions or transfers using objective criteria.
- Reduced employee hiring costs due to the ability to recruit before the season,
- Improved opinions about the employee onboarding process, which makes it easier to recruit new employees (through referrals from current ones).
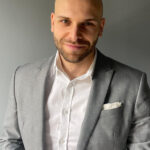
Training Within Industry and Lean Management Practitioner.
He is a lecturer at the WSB University in Wrocław. He is the author and co-author of several pieces of literature on the TWI program.
He is a managing partner in the LeanTrix company and a master Trainer for Europe. Additionally, he is involved in projects such as eTWI System and Lean Community
He has run projects for: Lotte Wedel, Danone, Kompania Piwowarska, eobuwie.pl, Arvato, Whirlpool, B / S / H, Geberit, RECARO, Tenneco, Sumitomo Electric, Stadler, Vesuvius Poland